The Evolution of PCBs
PCBs have come a long way since their inception in the early 20th century. The first PCBs were made using a process called “through-hole” technology, where components were inserted into holes drilled in the board and soldered in place. This method was time-consuming and required a lot of manual labor.
In the 1950s, the introduction of “surface-mount” technology revolutionized the PCB industry. This method involved placing components directly on the surface of the board and soldering them in place. Surface-mount technology allowed for smaller, more compact PCBs and faster production times.
Today, PCBs are manufactured using a variety of advanced technologies, including:
- High Density Interconnect (HDI)
- Flexible PCBs
- Rigid-Flex PCBs
- 3D Printing
- Embedded Components
These technologies have enabled the creation of smaller, more complex, and more reliable PCBs than ever before.
High Density Interconnect (HDI)
HDI is a type of PCB technology that allows for a higher density of interconnects than traditional PCBs. This is achieved by using smaller vias (holes) and finer trace widths. HDI PCBs can have up to 8 layers, with each layer containing a high density of interconnects.
The benefits of HDI technology include:
- Reduced size and weight
- Improved signal integrity
- Higher reliability
- Faster data transmission speeds
HDI technology is commonly used in smartphones, tablets, and other portable electronics where space is at a premium.
Flexible PCBs
Flexible PCBs, also known as flex circuits, are PCBs that can bend and flex without breaking. They are made using a flexible substrate material, such as polyimide or polyester, and can be designed to fit into tight spaces or conform to curved surfaces.
Flexible PCBs are commonly used in:
- Wearable electronics
- Medical devices
- Aerospace systems
- Automotive electronics
The benefits of flexible PCBs include:
- Reduced weight and size
- Improved durability
- Increased design flexibility
- Reduced assembly costs
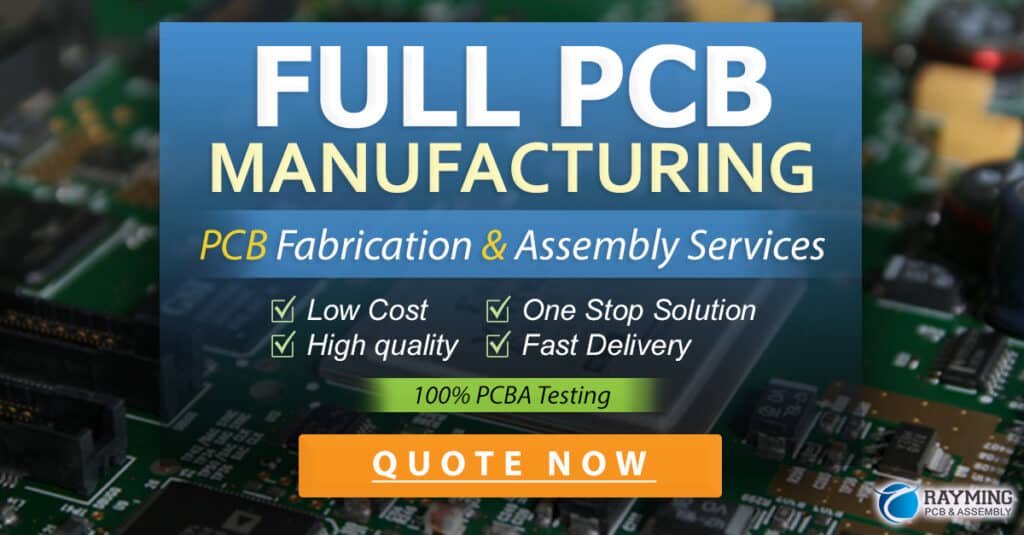
Rigid-Flex PCBs
Rigid-flex PCBs are a combination of traditional rigid PCBs and flexible PCBs. They consist of one or more rigid PCBs connected by flexible circuits. This allows for the benefits of both technologies in a single package.
Rigid-flex PCBs are commonly used in:
- Aerospace systems
- Military equipment
- Medical devices
- Industrial automation
The benefits of rigid-flex PCBs include:
- Reduced size and weight
- Improved reliability
- Increased design flexibility
- Reduced assembly costs
3D Printing
3D printing is a relatively new technology that is starting to make its way into the PCB industry. With 3D printing, PCBs can be manufactured using a layer-by-layer process, allowing for more complex designs and faster prototyping.
The benefits of 3D printing for PCBs include:
- Faster prototyping
- Reduced waste
- Increased design flexibility
- Lower costs for small production runs
While 3D printing is not yet widely used for mass production of PCBs, it is expected to become more common in the coming years as the technology improves and becomes more affordable.
Embedded Components
Embedded components are electronic components that are embedded directly into the PCB substrate. This allows for smaller, more compact designs and improved reliability.
Embedded components are commonly used in:
- Automotive electronics
- Medical devices
- Aerospace systems
- Military equipment
The benefits of embedded components include:
- Reduced size and weight
- Improved reliability
- Increased design flexibility
- Reduced assembly costs
The Future of PCBs
As technology continues to advance, so will the requirements for PCBs. Some of the trends we can expect to see in the coming years include:
Increased Miniaturization
As electronic devices continue to get smaller and more portable, the demand for smaller PCBs will only increase. HDI technology and embedded components will play a key role in enabling further miniaturization of PCBs.
Higher Speeds and Bandwidth
With the rise of 5G networks and the Internet of Things (IoT), there will be a growing demand for PCBs that can handle higher speeds and bandwidth. Advanced materials and manufacturing techniques will be needed to meet these requirements.
Greater Integration
As PCBs become more complex, there will be a need for greater integration of components and functionalities. This will require advanced design tools and manufacturing processes to ensure reliability and performance.
Sustainable Manufacturing
As environmental concerns continue to grow, there will be increasing pressure on PCB manufacturers to adopt sustainable practices. This may include the use of eco-friendly materials, reduced waste, and more efficient manufacturing processes.
FAQs
- What is the difference between through-hole and surface-mount technology?
Through-hole technology involves inserting components into holes drilled in the PCB and soldering them in place. Surface-mount technology involves placing components directly on the surface of the PCB and soldering them in place. Surface-mount technology allows for smaller, more compact PCBs and faster production times.
- What are the benefits of HDI technology?
The benefits of HDI technology include reduced size and weight, improved signal integrity, higher reliability, and faster data transmission speeds. HDI PCBs can have up to 8 layers, with each layer containing a high density of interconnects.
- What are flexible PCBs used for?
Flexible PCBs are commonly used in wearable electronics, medical devices, aerospace systems, and automotive electronics. They are made using a flexible substrate material and can bend and flex without breaking, allowing for increased design flexibility and reduced weight and size.
- What is 3D printing and how is it used in PCB manufacturing?
3D printing is a process where PCBs are manufactured using a layer-by-layer process. This allows for more complex designs and faster prototyping. While 3D printing is not yet widely used for mass production of PCBs, it is expected to become more common in the coming years as the technology improves and becomes more affordable.
- What are the benefits of embedded components?
The benefits of embedded components include reduced size and weight, improved reliability, increased design flexibility, and reduced assembly costs. Embedded components are electronic components that are embedded directly into the PCB substrate, allowing for smaller, more compact designs.
Conclusion
PCB technology has come a long way in recent years, and the future looks bright for this essential component of the electronics industry. With advancements in HDI technology, flexible and rigid-flex PCBs, 3D printing, and embedded components, PCBs are becoming smaller, more complex, and more reliable than ever before.
As technology continues to evolve, so will the requirements for PCBs. Manufacturers will need to stay ahead of the curve by investing in advanced materials, design tools, and manufacturing processes to meet the demands of the market.
Despite the challenges ahead, the future of PCBs looks promising. With the right investments and innovations, PCBs will continue to play a critical role in enabling the next generation of electronic devices and systems.
Technology | Benefits | Applications |
---|---|---|
HDI | Reduced size and weight, improved signal integrity | Smartphones, tablets, portable electronics |
Flexible PCBs | Reduced weight and size, improved durability | Wearables, medical devices, aerospace, automotive |
Rigid-Flex PCBs | Reduced size and weight, improved reliability | Aerospace, military, medical, industrial |
3D Printing | Faster prototyping, reduced waste, increased flexibility | Prototyping, small production runs |
Embedded Components | Reduced size and weight, improved reliability | Automotive, medical, aerospace, military |
No responses yet