What is a PCB Prototype?
A PCB prototype is an early version of a printed circuit board that is designed and fabricated to test and validate the functionality, performance, and layout of the board before mass production. It is a physical representation of the PCB design that allows engineers to conduct real-world testing and make necessary adjustments to ensure the final product meets the desired specifications.
Types of PCB Prototypes
There are several types of PCB prototypes, each serving a specific purpose in the development process:
-
Visual Prototype: A visual prototype is a non-functional representation of the PCB layout. It is used to assess the visual aspects of the design, such as component placement, routing, and overall aesthetics.
-
Proof-of-Concept (POC) Prototype: A POC prototype is a simplified version of the PCB that is used to validate the basic functionality of the design. It may not include all the features of the final product but focuses on testing the core concepts.
-
Functional Prototype: A functional prototype is a fully working version of the PCB that includes all the components and features of the final product. It is used to test and validate the complete functionality of the board.
-
Pre-Production Prototype: A pre-production prototype is a near-final version of the PCB that is used to validate the manufacturing process and ensure that the board can be mass-produced without any issues.
Prototype Type | Purpose |
---|---|
Visual Prototype | Assess visual aspects of the design |
POC Prototype | Validate basic functionality |
Functional Prototype | Test and validate complete functionality |
Pre-Production Prototype | Validate manufacturing process |
Why You Need a PCB Prototype
Creating a PCB prototype is a crucial step in the electronic product development process. Here are some key reasons why you need a PCB prototype:
1. Test and Validate Functionality
A PCB prototype allows you to test and validate the functionality of your design in a real-world environment. By testing the prototype, you can identify any issues or bugs in the design and make necessary modifications before moving to mass production. This helps ensure that the final product functions as intended and meets the desired specifications.
2. Identify Design Flaws
Creating a PCB prototype helps identify design flaws early in the development process. By physically assembling the components and testing the board, you can uncover any layout or routing issues, component incompatibilities, or other design problems. Identifying and addressing these flaws at the prototype stage saves time and money compared to discovering them during mass production.
3. Optimize Performance
A PCB prototype provides an opportunity to optimize the performance of your design. By conducting thorough testing and measurements, you can assess factors such as signal integrity, power consumption, and thermal management. Based on the results, you can make necessary adjustments to improve the overall performance of the PCB.
4. Verify Manufacturing Feasibility
Creating a pre-production prototype helps verify the manufacturing feasibility of your PCB design. It allows you to test the assembly process, identify any potential manufacturing challenges, and ensure that the board can be efficiently and reliably produced in large quantities. This step is crucial to avoid costly manufacturing issues and delays during mass production.
5. Obtain User Feedback
A functional PCB prototype allows you to obtain valuable user feedback before finalizing the design. By providing prototypes to potential users or customers, you can gather insights on the usability, functionality, and overall user experience of your product. This feedback can help you make informed decisions and improvements to enhance the final product.
PCB Prototype Development Process
The PCB prototype development process typically involves the following steps:
-
Schematic Design: The first step is to create a schematic diagram of the PCB, which represents the electrical connections and components of the board. This is done using electronic design automation (EDA) software.
-
PCB Layout: Once the schematic is finalized, the next step is to create the PCB layout. This involves placing the components on the board and routing the traces to establish the electrical connections. The layout is optimized for manufacturability, signal integrity, and thermal management.
-
Prototype Fabrication: After the PCB layout is complete, the prototype is fabricated using specialized PCB manufacturing techniques. This typically involves printing the circuit pattern onto a substrate material, such as FR-4, and then etching away the unwanted copper to create the traces.
-
Component Assembly: Once the PCB prototype is fabricated, the components are assembled onto the board. This can be done manually or using automated assembly processes, depending on the complexity of the design and the quantity of prototypes required.
-
Testing and Validation: The assembled PCB prototype undergoes rigorous testing and validation to ensure it functions as intended. This includes functional testing, signal integrity analysis, power consumption measurements, and environmental testing (if required).
-
Design Iterations: Based on the testing results and user feedback, the PCB design may go through multiple iterations to address any issues or make improvements. This process continues until the prototype meets the desired specifications and performance criteria.
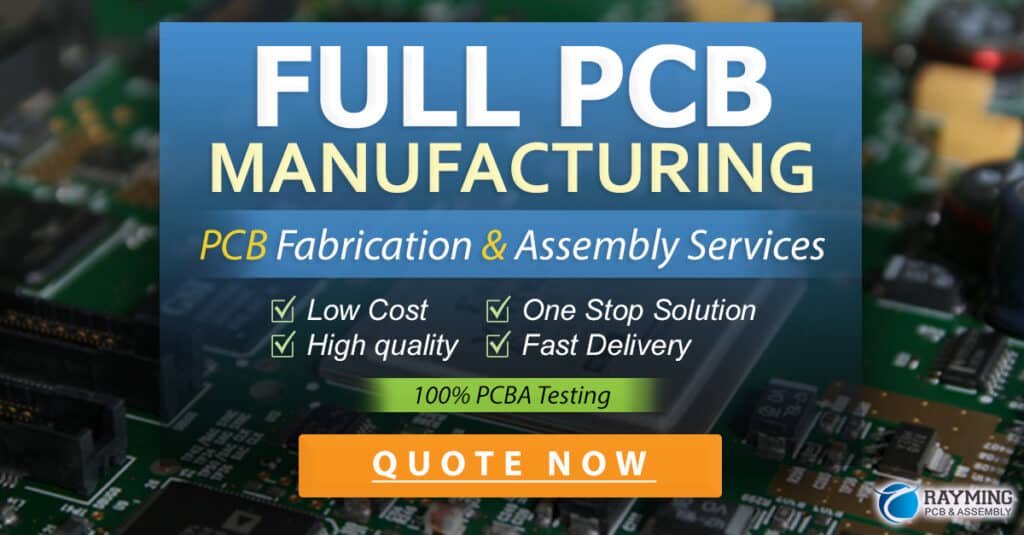
Choosing the Right PCB Prototype Manufacturer
Selecting the right PCB prototype manufacturer is crucial to ensure the success of your project. Here are some factors to consider when choosing a manufacturer:
-
Experience and Expertise: Look for a manufacturer with extensive experience in PCB prototyping and a proven track record of delivering high-quality prototypes. They should have expertise in various PCB technologies and be able to handle complex designs.
-
Manufacturing Capabilities: Ensure that the manufacturer has the necessary equipment and capabilities to fabricate your PCB prototype. This includes the ability to handle different PCB materials, layer stackups, and surface finishes.
-
Turnaround Time: PCB prototyping often requires quick turnaround times to meet project deadlines. Choose a manufacturer that offers fast prototyping services without compromising on quality.
-
Quality Control: A reliable PCB prototype manufacturer should have strict quality control measures in place to ensure the consistency and reliability of the prototypes. Look for certifications such as ISO 9001 and IPC standards.
-
Customer Support: Good customer support is essential throughout the prototyping process. The manufacturer should be responsive, communicate clearly, and provide technical assistance when needed.
Frequently Asked Questions (FAQ)
-
What is the difference between a PCB prototype and a final production PCB?
A PCB prototype is an early version of the PCB used for testing and validation, while a final production PCB is the finished product that has undergone all the necessary iterations and is ready for mass production. -
How long does it take to create a PCB prototype?
The turnaround time for PCB prototyping varies depending on the complexity of the design and the manufacturer’s capabilities. Typically, it can range from a few days to a couple of weeks. -
How much does a PCB prototype cost?
The cost of a PCB prototype depends on factors such as the size of the board, the number of layers, the components used, and the quantity of prototypes required. It can range from a few hundred to several thousand dollars. -
Can I test the functionality of my PCB design without a physical prototype?
While simulation tools can provide valuable insights into the behavior of a PCB design, a physical prototype is essential to test and validate the real-world functionality, performance, and reliability of the board. -
What should I do if my PCB prototype fails to function as intended?
If your PCB prototype fails to function as intended, the first step is to identify the root cause of the issue. This may involve conducting further testing, analyzing the design, or consulting with PCB experts. Based on the findings, you can make necessary modifications to the design and create a new prototype for validation.
Conclusion
A PCB prototype is a crucial step in the electronic product development process. It allows you to test and validate the functionality, performance, and reliability of your PCB design before moving to mass production. By identifying design flaws, optimizing performance, verifying manufacturing feasibility, and obtaining user feedback, a PCB prototype helps ensure the success of your final product.
When creating a PCB prototype, it’s essential to follow a structured development process and choose a reliable PCB prototype manufacturer with the necessary experience, capabilities, and quality control measures. By investing in a well-designed and thoroughly tested PCB prototype, you can save time, money, and resources in the long run and bring a high-quality electronic product to market.
No responses yet