Introduction to PCB Proto Service Defaults
When it comes to PCB (Printed Circuit Board) prototyping services, understanding the default values and settings can greatly streamline the design and manufacturing process. PCB proto defaults encompass a wide range of parameters, including material selection, layer stackup, trace width and spacing, via sizes, soldermask and silkscreen options, and more. By familiarizing yourself with these default values, you can optimize your PCB design, ensure compatibility with manufacturing processes, and avoid potential issues during fabrication and assembly.
In this comprehensive article, we will dive deep into the world of PCB proto service defaults, exploring the various aspects that designers and engineers should consider when creating PCBs for prototyping and low-volume production. We’ll discuss the importance of adhering to these defaults, the flexibility they offer, and how they can impact the overall quality, reliability, and cost of your PCB project.
Understanding the Significance of PCB Proto Defaults
Why PCB Proto Defaults Matter
PCB proto defaults serve as a starting point for designers and engineers, providing a set of tried-and-tested parameters that have been proven to work well in most PCB Prototyping scenarios. By following these defaults, you can:
- Ensure compatibility with standard manufacturing processes
- Minimize the risk of design errors and manufacturing issues
- Reduce the time and effort required for design and setup
- Achieve consistent results across different PCB prototyping services
- Optimize the cost and turnaround time of your PCB project
Balancing Flexibility and Adherence to Defaults
While PCB proto defaults offer a solid foundation for your PCB design, it’s important to understand that they are not set in stone. Depending on your specific requirements, you may need to deviate from these defaults to achieve the desired functionality, performance, or form factor. However, it’s crucial to carefully consider the implications of deviating from the defaults, as it may impact the manufacturability, reliability, and cost of your PCB.
When deciding whether to adhere to or deviate from PCB proto defaults, consider the following factors:
- The complexity and uniqueness of your PCB design
- The intended application and operating environment of your PCB
- The manufacturing capabilities of your chosen PCB prototyping service
- The timeline and budget constraints of your project
By striking the right balance between flexibility and adherence to defaults, you can create PCBs that are both functionally optimized and manufacturable within your project’s constraints.
Key Aspects of PCB Proto Defaults
Material Selection
One of the most critical aspects of PCB proto defaults is the choice of material for the PCB substrate. The most common default material for PCB prototyping is FR-4, a glass-reinforced epoxy laminate that offers a good balance of mechanical, electrical, and thermal properties. FR-4 is suitable for a wide range of applications and is cost-effective for prototyping and low-volume production.
However, depending on your specific requirements, you may need to consider alternative materials, such as:
- High-frequency laminates (e.g., Rogers, Isola) for RF and microwave applications
- Metal-core PCBs (MCPCBs) for high-power and heat-dissipation applications
- Flexible or Rigid-Flex PCBs for wearable electronics and space-constrained designs
When selecting a material, consider factors such as dielectric constant, dissipation factor, thermal conductivity, and cost to ensure that it meets your design requirements and budget.
Layer Stackup and Thickness
The layer stackup and thickness of your PCB play a crucial role in determining its mechanical strength, signal integrity, and manufacturability. PCB proto defaults typically offer a range of standard layer stackups, such as:
Layers | Thickness (mm) | Typical Applications |
---|---|---|
1 | 0.4 – 0.8 | Simple, single-sided designs |
2 | 0.8 – 1.6 | Double-sided designs with minimal routing |
4 | 1.0 – 2.0 | Moderate complexity, mixed-signal designs |
6 | 1.2 – 2.4 | Complex, high-density designs |
8+ | 1.6 – 3.2 | High-end, multilayer designs with advanced features |
When choosing a layer stackup, consider the following factors:
- The number of signal layers required for your design
- The need for dedicated power and ground planes
- The required impedance control and signal integrity
- The overall thickness and weight constraints of your PCB
By selecting an appropriate layer stackup and thickness, you can ensure that your PCB meets your design requirements while remaining manufacturable and cost-effective.
Trace Width and Spacing
Trace width and spacing are critical parameters that determine the current-carrying capacity, signal integrity, and manufacturability of your PCB. PCB proto defaults typically provide a set of minimum trace width and spacing values based on the chosen copper weight and layer stackup.
For example, a typical set of minimum trace width and spacing values for a 1 oz. copper, 2-layer PCB might be:
Parameter | Minimum Value (mm) |
---|---|
Trace width | 0.15 |
Trace spacing | 0.15 |
When designing your PCB, consider the following factors:
- The current-carrying requirements of your traces
- The impedance control and signal integrity requirements
- The manufacturing capabilities of your chosen PCB prototyping service
- The cost implications of using narrower traces and smaller spacings
By adhering to the minimum trace width and spacing values provided by your PCB proto defaults, you can ensure that your PCB is manufacturable and reliable. However, if your design requires narrower traces or smaller spacings, consult with your PCB prototyping service to determine the feasibility and potential cost implications.
Via Sizes and Drilling
Vias are essential for connecting traces between layers in a Multilayer PCB. PCB proto defaults typically specify a range of standard via sizes and drilling options, such as:
Via Type | Diameter (mm) | Drill Size (mm) |
---|---|---|
Through hole | 0.8 – 1.0 | 0.3 – 0.5 |
Blind/buried | 0.5 – 0.8 | 0.2 – 0.4 |
Microvias | 0.2 – 0.5 | 0.1 – 0.3 |
When selecting via sizes and drilling options, consider the following factors:
- The number of layers in your PCB Stackup
- The density and routing requirements of your design
- The manufacturing capabilities and costs associated with different via types
- The reliability and signal integrity requirements of your PCB
By choosing appropriate via sizes and drilling options, you can ensure that your PCB is manufacturable, reliable, and cost-effective.
Soldermask and Silkscreen
Soldermask and silkscreen are essential features that protect your PCB from environmental factors and provide clear labeling for assembly and debugging. PCB proto defaults typically offer a range of soldermask and silkscreen options, such as:
Feature | Options |
---|---|
Soldermask color | Green, red, blue, black, white, yellow |
Soldermask finish | Glossy, matte |
Silkscreen color | White, black |
When selecting soldermask and silkscreen options, consider the following factors:
- The aesthetic requirements of your PCB
- The legibility and contrast of the silkscreen markings
- The environmental protection and durability requirements of your PCB
- The cost implications of different soldermask and silkscreen options
By choosing appropriate soldermask and silkscreen options, you can enhance the appearance, protection, and usability of your PCB.
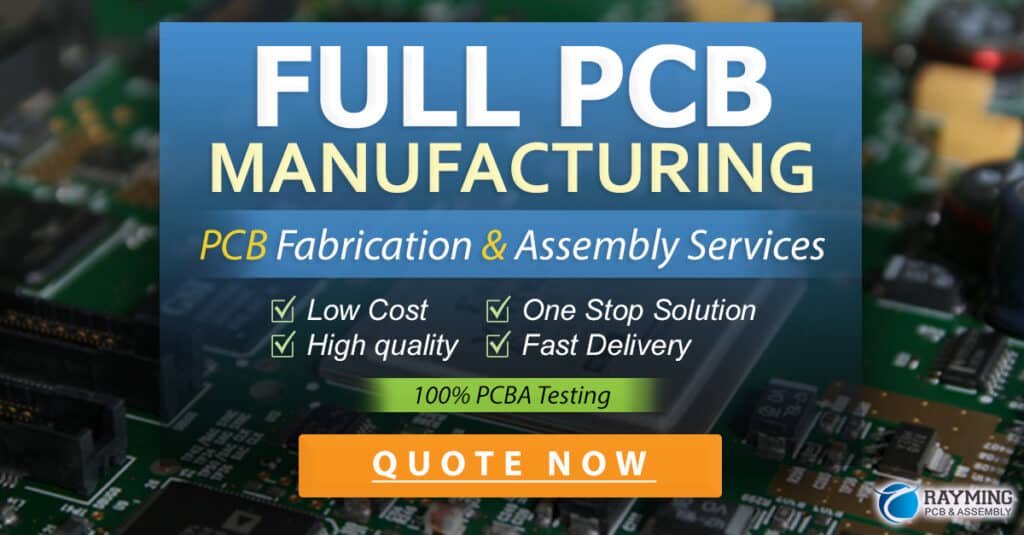
Frequently Asked Questions (FAQ)
-
Q: What happens if I deviate from the PCB proto defaults?
A: Deviating from PCB proto defaults may impact the manufacturability, reliability, and cost of your PCB. While some deviations may be necessary to achieve specific design requirements, it’s essential to consult with your PCB prototyping service to understand the implications and ensure that your design remains manufacturable. -
Q: Can I use different materials for different layers in my PCB stackup?
A: Yes, it’s possible to use different materials for different layers in your PCB stackup, such as using a high-frequency laminate for RF layers and FR-4 for digital layers. However, this may increase the complexity and cost of your PCB, so it’s essential to discuss the feasibility and implications with your PCB prototyping service. -
Q: What is the minimum feature size achievable with PCB proto defaults?
A: The minimum feature size achievable with PCB proto defaults depends on the capabilities of your chosen PCB prototyping service. Typically, minimum trace widths and spacings range from 0.1 mm to 0.15 mm, while minimum via diameters range from 0.2 mm to 0.3 mm. However, it’s always best to consult with your PCB prototyping service to determine their specific capabilities and limitations. -
Q: How do I ensure the manufacturability of my PCB design?
A: To ensure the manufacturability of your PCB design, follow these best practices: - Adhere to the PCB proto defaults whenever possible
- Use standard trace widths, spacings, and via sizes
- Avoid using complex structures or non-standard materials unless necessary
- Perform design rule checks (DRC) and manufacturability checks using PCB design software
-
Consult with your PCB prototyping service for design review and feedback
-
Q: Can I specify custom soldermask and silkscreen colors?
A: Most PCB prototyping services offer a range of standard soldermask and silkscreen colors, such as green, red, blue, black, white, and yellow for soldermask, and white and black for silkscreen. If you require custom colors, consult with your PCB prototyping service to determine the feasibility and potential cost implications.
Conclusion
PCB proto defaults provide a solid foundation for designing and manufacturing reliable, cost-effective, and manufacturable PCBs for prototyping and low-volume production. By understanding and adhering to these defaults, you can streamline your design process, minimize the risk of errors and issues, and ensure compatibility with standard manufacturing processes.
However, it’s essential to recognize that PCB proto defaults are not one-size-fits-all solutions. Depending on your specific design requirements, you may need to deviate from these defaults to achieve the desired functionality, performance, or form factor. When doing so, it’s crucial to carefully consider the implications on manufacturability, reliability, and cost, and to consult with your PCB prototyping service for guidance and feedback.
By striking the right balance between flexibility and adherence to PCB proto defaults, and by following best practices for design and manufacturability, you can create PCBs that meet your unique requirements while remaining cost-effective and reliable. With a solid understanding of PCB proto defaults and a collaborative approach with your PCB prototyping service, you can bring your innovative electronic products to life with confidence and success.
No responses yet