Introduction to PCB and PCBA
Printed Circuit Boards (PCBs) and Printed Circuit Board Assemblies (PCBAs) are essential components in modern electronic devices. They provide the foundation for connecting and integrating various electronic components, allowing for complex functionality and miniaturization. In this article, we will explore the various devices in which PCB and PCBA are applied, their manufacturing process, and the benefits they offer.
What is a PCB?
A PCB is a flat board made of insulating materials, such as fiberglass or plastic, with conductive copper tracks printed on its surface. These tracks form the electrical connections between components, replacing the need for individual wires. PCBs come in different types, including:
- Single-sided PCBs: Copper tracks are printed on one side of the board.
- Double-sided PCBs: Copper tracks are printed on both sides of the board, allowing for more complex circuits and higher component density.
- Multi-layer PCBs: Multiple layers of insulating material and copper tracks are stacked together, enabling even more complex designs and higher component density.
What is a PCBA?
A PCBA is a PCB that has been populated with electronic components, such as resistors, capacitors, integrated circuits (ICs), and connectors. The components are soldered onto the PCB, either through traditional through-hole mounting or surface mount technology (SMT). The PCBA Manufacturing process involves several steps:
- Solder paste application: A precise amount of solder paste is applied to the PCB’s contact pads using a stencil or screen printing process.
- Component placement: Electronic components are placed on the PCB using automated pick-and-place machines or manual assembly for smaller batches.
- Reflow soldering: The PCB with components is passed through a reflow oven, which melts the solder paste and creates a permanent electrical and mechanical connection between the components and the PCB.
- Inspection and testing: The assembled PCBA undergoes visual inspection and electrical testing to ensure proper functionality and quality control.
Devices that Utilize PCB and PCBA
PCBs and PCBAs are found in a wide range of electronic devices, from consumer electronics to industrial equipment and medical devices. Here are some common applications:
1. Smartphones and Tablets
Modern smartphones and tablets rely heavily on PCBs and PCBAs to accommodate their numerous features and functions within a compact form factor. These devices typically utilize multi-layer PCBs to integrate various components, such as:
- System-on-Chip (SoC) processors
- Memory modules (RAM and storage)
- Wireless communication modules (Wi-Fi, Bluetooth, cellular)
- Sensors (accelerometer, gyroscope, proximity)
- Power management ICs
- Display and touch controllers
The use of PCBs and PCBAs allows for efficient space utilization, enabling manufacturers to create slim and lightweight devices with high performance and functionality.
2. Computers and Laptops
PCBs and PCBAs form the backbone of modern computers and laptops. The main PCB in a computer is the motherboard, which connects and integrates various components, such as:
- Central Processing Unit (CPU)
- Graphics Processing Unit (GPU)
- Memory modules (RAM and ROM)
- Storage devices (HDD, SSD)
- Input/Output (I/O) connectors
- Power supply unit (PSU)
In addition to the motherboard, PCBs and PCBAs are used in other computer components, such as:
- Expansion cards (graphics cards, sound cards, network adapters)
- Solid-state drives (SSDs)
- Power supply units (PSUs)
- Keyboard and mouse controllers
The use of PCBs and PCBAs in computers and laptops ensures reliable and efficient data transfer, power distribution, and overall system performance.
3. Consumer Electronics
PCBs and PCBAs are ubiquitous in consumer electronics, enabling the development of feature-rich and user-friendly devices. Some examples include:
- Televisions and smart displays
- Home appliances (refrigerators, washing machines, air conditioners)
- Audio equipment (speakers, headphones, amplifiers)
- Gaming consoles and controllers
- Wearable devices (smartwatches, fitness trackers)
- Smart home devices (thermostats, security cameras, smart locks)
The application of PCBs and PCBAs in consumer electronics allows for the integration of advanced features, such as wireless connectivity, voice control, and energy efficiency, while maintaining a compact and aesthetically pleasing design.
4. Automotive Electronics
The automotive industry has increasingly adopted PCBs and PCBAs to enhance vehicle performance, safety, and user experience. Some automotive applications include:
- Engine control units (ECUs)
- Transmission control modules (TCMs)
- Infotainment systems
- Advanced driver assistance systems (ADAS)
- Body control modules (BCMs)
- Lighting control modules
- Battery management systems (BMSs) for electric vehicles
PCBs and PCBAs used in automotive applications must be designed and manufactured to withstand harsh environmental conditions, such as extreme temperatures, vibrations, and moisture. Automotive-grade PCBs and PCBAs often require additional certifications and testing to ensure reliability and safety.
5. Industrial Equipment and Automation
PCBs and PCBAs play a crucial role in industrial equipment and automation systems, enabling precise control, monitoring, and communication. Some industrial applications include:
- Programmable logic controllers (PLCs)
- Human-machine interfaces (HMIs)
- Industrial robots and manipulators
- Motor drives and controllers
- Sensor and data acquisition systems
- Networking and communication devices
- Power distribution and management systems
Industrial-grade PCBs and PCBAs are designed to operate in demanding environments, withstanding factors such as dust, moisture, and electromagnetic interference (EMI). They often require ruggedized construction and additional protection, such as conformal coating or potting.
6. Medical Devices
PCBs and PCBAs are essential components in medical devices, enabling accurate diagnosis, treatment, and monitoring of patients. Some medical applications include:
- Diagnostic imaging equipment (X-ray, MRI, CT scanners)
- Patient monitoring systems (ECG, EEG, pulse oximeters)
- Surgical instruments and devices
- Laboratory analysis equipment
- Implantable devices (pacemakers, insulin pumps)
- Wearable medical devices (glucose monitors, blood pressure monitors)
Medical-grade PCBs and PCBAs must adhere to strict quality control and regulatory standards, such as ISO 13485 and IEC 60601, to ensure patient safety and device reliability.
7. Aerospace and Defense
PCBs and PCBAs used in aerospace and defense applications must meet stringent requirements for reliability, performance, and security. Some applications include:
- Avionics systems (flight control, navigation, communication)
- Radar and surveillance systems
- Satellite and spacecraft electronics
- Military communication and networking devices
- Guidance and control systems for missiles and drones
- Ruggedized computers and displays
Aerospace and defense PCBs and PCBAs often require specialized materials, such as high-temperature laminates, and advanced manufacturing techniques, such as high-density interconnect (HDI) and rigid-flex PCBs, to meet the demanding performance and environmental requirements.
Benefits of PCBs and PCBAs
The widespread use of PCBs and PCBAs in various devices and industries can be attributed to the numerous benefits they offer:
-
Miniaturization: PCBs and PCBAs allow for the integration of many components in a compact space, enabling the development of smaller and more portable devices.
-
Reliability: Well-designed and manufactured PCBs and PCBAs provide reliable electrical connections and stable performance, reducing the risk of device failure.
-
Cost-effectiveness: Mass production of PCBs and PCBAs using automated processes reduces manufacturing costs, making electronic devices more affordable.
-
Efficiency: PCBs and PCBAs streamline the assembly process, reducing the time and labor required to manufacture electronic devices.
-
Design flexibility: PCBs and PCBAs can be customized to meet specific device requirements, enabling the development of innovative and unique products.
-
Scalability: PCB and PCBA manufacturing processes can be easily scaled up to meet increasing demand, allowing for the production of large quantities of electronic devices.
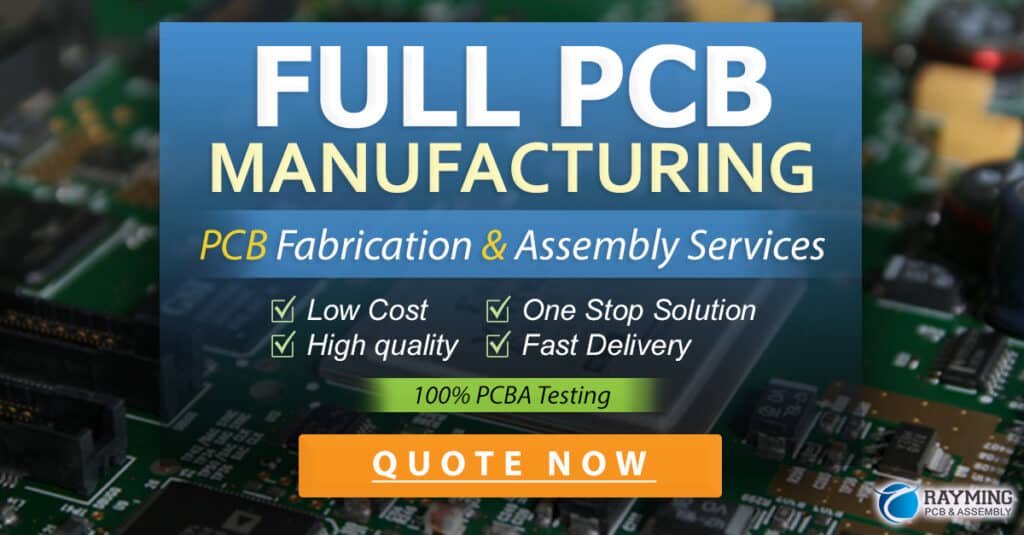
PCB and PCBA Manufacturing Process
The manufacturing process for PCBs and PCBAs involves several steps, each requiring precision and quality control:
PCB Manufacturing
-
Design: The PCB design is created using computer-aided design (CAD) software, specifying the layout, component placement, and electrical connections.
-
Printing: The PCB design is printed onto a copper-clad laminate board using a photoresist process, which transfers the circuit pattern onto the board.
-
Etching: The unwanted copper is removed from the board using a chemical etching process, leaving only the desired circuit pattern.
-
Drilling: Holes are drilled into the board to accommodate through-hole components and provide electrical connections between layers in multi-layer PCBs.
-
Plating: The holes are plated with copper to ensure proper electrical conductivity and mechanical strength.
-
Solder mask application: A protective solder mask is applied to the board, exposing only the areas where components will be soldered.
-
Silkscreen printing: Text and symbols are printed onto the board using a silkscreen process, providing information for assembly and identification.
PCBA Manufacturing
-
Solder paste application: Solder paste is applied to the PCB’s contact pads using a stencil or screen printing process.
-
Component placement: Electronic components are placed onto the PCB using automated pick-and-place machines or manual assembly for smaller batches.
-
Reflow soldering: The PCB with components is passed through a reflow oven, which melts the solder paste and creates a permanent electrical and mechanical connection between the components and the PCB.
-
Inspection and testing: The assembled PCBA undergoes visual inspection and electrical testing to ensure proper functionality and quality control.
-
Conformal coating (optional): A protective coating is applied to the PCBA to shield it from environmental factors such as moisture, dust, and chemicals.
-
Final assembly: The PCBA is integrated into the final device housing or enclosure, along with other components such as displays, batteries, and connectors.
Frequently Asked Questions (FAQ)
1. What is the difference between a PCB and a PCBA?
A PCB is a bare board with copper tracks and pads, while a PCBA is a PCB that has been populated with electronic components and soldered together.
2. What are the different types of PCBs?
The main types of PCBs are single-sided, double-sided, and multi-layer. Single-sided PCBs have copper tracks on one side, double-sided PCBs have tracks on both sides, and multi-layer PCBs have multiple layers of insulating material and copper tracks stacked together.
3. What are the advantages of using PCBs and PCBAs in electronic devices?
PCBs and PCBAs offer several advantages, including miniaturization, reliability, cost-effectiveness, efficiency, design flexibility, and scalability.
4. What are some common applications of PCBs and PCBAs?
PCBs and PCBAs are used in a wide range of devices, including smartphones, computers, consumer electronics, automotive electronics, industrial equipment, medical devices, and aerospace and defense systems.
5. What are the key steps in the PCB and PCBA manufacturing process?
The PCB manufacturing process involves design, printing, etching, drilling, plating, solder mask application, and silkscreen printing. The PCBA manufacturing process includes solder paste application, component placement, reflow soldering, inspection and testing, conformal coating (optional), and final assembly.
Conclusion
PCBs and PCBAs are essential components in modern electronic devices, enabling the development of compact, reliable, and feature-rich products across various industries. From smartphones and computers to automotive electronics and medical devices, PCBs and PCBAs provide the foundation for connecting and integrating electronic components, allowing for complex functionality and miniaturization.
The manufacturing process for PCBs and PCBAs involves several precision steps, ensuring the quality and reliability of the final product. As technology continues to advance, the demand for more sophisticated and efficient PCBs and PCBAs will only increase, driving innovation and shaping the future of electronic devices.
By understanding the various applications and benefits of PCBs and PCBAs, manufacturers can make informed decisions when designing and producing electronic devices, ultimately delivering products that meet the evolving needs of consumers and industries alike.
Application | Examples |
---|---|
Smartphones and Tablets | System-on-Chip (SoC) processors, Memory modules, Wireless communication modules, Sensors, Power management ICs, Display and touch controllers |
Computers and Laptops | Motherboard, Expansion cards, Solid-state drives (SSDs), Power supply units (PSUs), Keyboard and mouse controllers |
Consumer Electronics | Televisions and smart displays, Home appliances, Audio equipment, Gaming consoles and controllers, Wearable devices, Smart home devices |
Automotive Electronics | Engine control units (ECUs), Transmission control modules (TCMs), Infotainment systems, Advanced driver assistance systems (ADAS), Body control modules (BCMs), Lighting control modules, Battery management systems (BMSs) |
Industrial Equipment and Automation | Programmable logic controllers (PLCs), Human-machine interfaces (HMIs), Industrial robots and manipulators, Motor drives and controllers, Sensor and data acquisition systems, Networking and communication devices, Power distribution and management systems |
Medical Devices | Diagnostic imaging equipment, Patient monitoring systems, Surgical instruments and devices, Laboratory analysis equipment, Implantable devices, Wearable medical devices |
Aerospace and Defense | Avionics systems, Radar and surveillance systems, Satellite and spacecraft electronics, Military communication and networking devices, Guidance and control systems for missiles and drones, Ruggedized computers and displays |
No responses yet