Introduction to PCBA Manufacturing
Printed Circuit Board Assembly (PCBA) manufacturing is a complex process that involves several steps to create a functional electronic device. PCBA is a crucial component in various industries, including consumer electronics, automotive, aerospace, and medical devices. In this comprehensive guide, we will walk you through the step-by-step process of PCBA manufacturing, from design to final assembly.
Key Components of a PCBA
Before diving into the manufacturing process, it’s essential to understand the key components that make up a PCBA:
1. PCB (Printed Circuit Board)
The PCB is the foundation of the PCBA. It is a thin board made of insulating materials, such as fiberglass or plastic, with conductive copper traces printed on its surface. The PCB provides mechanical support and electrical connectivity for the electronic components.
2. Electronic Components
Electronic components, such as resistors, capacitors, integrated circuits (ICs), and connectors, are the building blocks of a PCBA. These components are mounted on the PCB and connected through the copper traces.
3. Solder
Solder is a metal alloy used to create electrical and mechanical connections between the electronic components and the PCB. It is typically composed of tin, lead, and other metals, although lead-free solder is becoming more common due to environmental concerns.
The PCBA Manufacturing Process
The PCBA manufacturing process consists of several steps, each requiring precision and attention to detail. The main stages of PCBA manufacturing are:
Step 1: PCB Design and Fabrication
The first step in PCBA manufacturing is designing the PCB. This involves creating a schematic diagram and a layout using specialized software, such as Altium Designer or Eagle. The schematic diagram represents the electrical connections between the components, while the layout determines the physical placement of the components on the PCB.
Once the design is finalized, the PCB is fabricated. This process involves the following sub-steps:
-
Substrate Preparation: The PCB substrate, typically made of fiberglass or plastic, is cut to the desired size and shape.
-
Copper Lamination: A thin layer of copper foil is laminated onto the substrate using heat and pressure.
-
Photoresist Application: A light-sensitive photoresist is applied to the copper layer.
-
Exposure and Development: The photoresist is exposed to UV light through a photomask, which contains the PCB layout. The exposed areas of the photoresist are then removed using a developer solution.
-
Etching: The exposed copper is etched away using a chemical solution, leaving behind the desired copper traces.
-
Drill Holes: Holes are drilled in the PCB to accommodate through-hole components and vias, which connect different layers of the PCB.
-
Solder Mask Application: A solder mask, typically green in color, is applied to the PCB to protect the copper traces from oxidation and prevent solder bridges during the assembly process.
-
Silkscreen Printing: A silkscreen layer is printed on the PCB to add text, logos, and component identifiers.
Step 2: PCB Assembly
Once the PCB is fabricated, the next step is to assemble the electronic components onto the board. There are two primary methods for PCB assembly: through-hole and surface mount.
Through-Hole Assembly (THA)
In through-hole assembly, the components have long leads that are inserted into the drilled holes on the PCB. The leads are then soldered to the copper pads on the opposite side of the board. THA is generally used for larger components and is more robust than surface mount assembly.
Surface Mount Assembly (SMT)
Surface mount assembly involves placing components directly onto the surface of the PCB. The components have small metal pads or leads that are soldered to the copper pads on the PCB. SMT allows for smaller components and higher component density compared to THA.
The PCB assembly process typically involves the following sub-steps:
-
Solder Paste Application: A solder paste, consisting of tiny solder particles suspended in a flux medium, is applied to the copper pads on the PCB using a stencil or syringe.
-
Component Placement: The electronic components are placed onto the solder paste using a pick-and-place machine or by hand.
-
Reflow Soldering: The PCB is passed through a reflow oven, which heats the solder paste to its melting point. As the solder cools, it forms a strong electrical and mechanical bond between the components and the PCB.
-
Inspection and Testing: The assembled PCB is inspected visually and tested using automated optical inspection (AOI) or x-ray inspection to ensure proper component placement and soldering.
Step 3: Final Assembly and Packaging
After the PCB is assembled, the final steps involve integrating the PCBA into the end product and packaging it for shipment.
-
Mechanical Assembly: The PCBA is mounted into the device enclosure along with other mechanical components, such as buttons, displays, and connectors.
-
Functional Testing: The assembled device is tested to ensure proper functionality and performance.
-
Packaging: The finished product is packaged in protective materials and labeled for shipment.
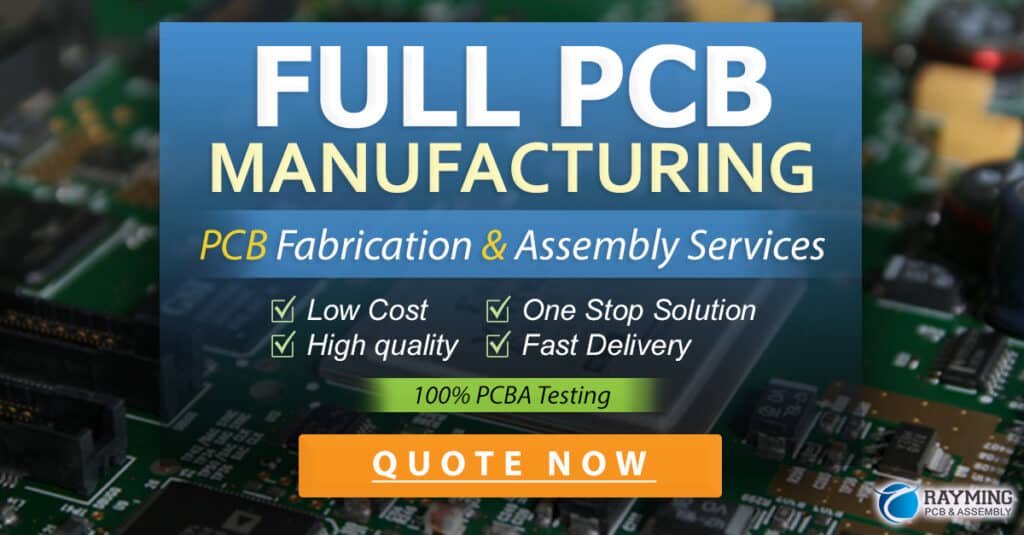
Quality Control in PCBA Manufacturing
Quality control is critical throughout the PCBA manufacturing process to ensure the reliability and performance of the final product. Some common quality control measures include:
- Visual inspection
- Automated optical inspection (AOI)
- X-ray inspection
- In-circuit testing (ICT)
- Functional testing
- Burn-in testing
These tests help identify defects, such as solder bridges, component misalignment, and electrical shorts, ensuring that only high-quality products reach the end-user.
Advantages of Outsourcing PCBA Manufacturing
Many companies choose to outsource their PCBA manufacturing to specialized providers. Outsourcing offers several advantages, including:
-
Cost Savings: Outsourcing can reduce labor, equipment, and facility costs associated with in-house manufacturing.
-
Expertise: PCBA manufacturers have specialized knowledge and experience in the manufacturing process, ensuring high-quality results.
-
Scalability: Outsourcing allows companies to scale their production up or down based on demand without investing in additional equipment or personnel.
-
Focus on Core Competencies: By outsourcing PCBA manufacturing, companies can focus on their core competencies, such as product design and marketing.
Choosing a PCBA Manufacturer
When selecting a PCBA manufacturer, consider the following factors:
- Experience and expertise in your industry
- Quality control processes and certifications (e.g., ISO 9001, IPC)
- Manufacturing capabilities and capacity
- Lead times and delivery reliability
- Communication and customer support
- Pricing and total cost of ownership
Future Trends in PCBA Manufacturing
As technology advances, PCBA manufacturing continues to evolve. Some future trends to watch include:
-
Miniaturization: The demand for smaller, more compact electronic devices is driving the development of advanced packaging techniques, such as system-in-package (SiP) and 3D packaging.
-
Flexible and Stretchable Electronics: The growth of wearable and IoT devices is fueling the development of flexible and stretchable PCBs that can conform to various shapes and withstand repeated bending and stretching.
-
Sustainable Manufacturing: There is a growing emphasis on environmentally friendly manufacturing practices, such as the use of lead-free solder and the adoption of green packaging materials.
-
Automation and Industry 4.0: The integration of automation, artificial intelligence, and the Internet of Things (IoT) in PCBA manufacturing is expected to improve efficiency, quality, and flexibility.
Frequently Asked Questions (FAQ)
-
What is the difference between PCB and PCBA?
A PCB is a bare board with copper traces and pads, while a PCBA is a PCB with electronic components mounted and soldered onto it. -
What are the main methods for PCB assembly?
The two main methods for PCB assembly are through-hole assembly (THA) and surface mount assembly (SMT). THA involves inserting component leads into drilled holes and soldering them, while SMT involves placing components directly onto the surface of the PCB and soldering them. -
How long does the PCBA manufacturing process typically take?
The lead time for PCBA manufacturing varies depending on factors such as the complexity of the design, the manufacturing capabilities of the provider, and the order volume. Typical lead times range from a few days to several weeks. -
What certifications should I look for in a PCBA manufacturer?
Some important certifications to look for in a PCBA manufacturer include ISO 9001 (quality management), IPC (industry standards for PCB design and manufacturing), and UL (safety certification). -
How can I ensure the quality of my PCBA?
To ensure the quality of your PCBA, work with a reputable manufacturer that follows strict quality control processes, such as automated optical inspection (AOI), x-ray inspection, and functional testing. Additionally, provide clear and detailed design files and specifications to minimize the risk of errors.
Conclusion
PCBA manufacturing is a complex process that requires precision, expertise, and attention to detail. By understanding the step-by-step process, from PCB design and fabrication to final assembly and packaging, you can make informed decisions when developing and manufacturing electronic products. As technology continues to advance, staying up-to-date with the latest trends and best practices in PCBA manufacturing will be essential for success in the competitive electronics industry.
No responses yet