Introduction to Multilayer PCB Bonding
Multilayer PCBs (Printed Circuit Boards) are essential components in modern electronics, enabling the creation of complex and compact designs. The fabrication of these boards involves several critical steps, with lay-up and bonding being among the most important. In this article, we will delve into the intricacies of multilayer PCB Bonding, exploring the various techniques, materials, and best practices involved in creating reliable and high-quality boards.
What is Multilayer PCB Bonding?
Multilayer PCB bonding is the process of stacking and joining multiple layers of PCB material to create a single, cohesive board. This process allows for increased circuit density, improved signal integrity, and better Thermal Management compared to single-layer boards. The bonding process typically involves applying pressure and heat to the stacked layers, causing the bonding material to melt and fuse the layers together.
Why is Multilayer PCB Bonding Important?
Multilayer PCB bonding is crucial for several reasons:
-
Increased Circuit Density: By stacking multiple layers, designers can fit more components and traces into a smaller space, enabling the creation of more compact and sophisticated devices.
-
Improved Signal Integrity: Properly bonded layers minimize signal interference and crosstalk, ensuring that signals travel through the board with minimal distortion.
-
Enhanced Thermal Management: Multilayer boards can dissipate heat more efficiently than single-layer boards, helping to prevent component failure due to overheating.
-
Greater Reliability: A well-bonded multilayer PCB is more durable and less prone to delamination and other failures, resulting in a more reliable end product.
Multilayer PCB Bonding Techniques
There are several techniques used for multilayer PCB bonding, each with its own advantages and disadvantages. The choice of bonding technique depends on factors such as the number of layers, the materials used, and the intended application of the board.
Thermal Compression Bonding
Thermal compression bonding is a widely used technique for multilayer PCB bonding. In this method, the stacked layers are subjected to high pressure and temperature, causing the bonding material (typically a prepreg or adhesive) to melt and fuse the layers together. The process involves the following steps:
- Stacking the layers in the desired order, with prepreg or adhesive sheets between each layer.
- Placing the stack in a press and applying pressure and heat according to the manufacturer’s specifications.
- Cooling the bonded stack under pressure to ensure a strong and uniform bond.
Thermal compression bonding offers several advantages, including:
- High bond strength
- Compatibility with a wide range of materials
- Suitability for high-volume production
However, this technique also has some drawbacks:
- Requires specialized equipment
- Can be time-consuming
- May cause dimensional changes due to the high temperature and pressure
Vacuum Lamination
Vacuum lamination is another common method for multilayer PCB bonding. In this technique, the stacked layers are placed in a vacuum chamber and subjected to pressure and heat. The vacuum helps to remove any air trapped between the layers, ensuring a more uniform and void-free bond. The process involves the following steps:
- Stacking the layers in the desired order, with prepreg or adhesive sheets between each layer.
- Placing the stack in a vacuum chamber and applying a vacuum to remove any trapped air.
- Applying pressure and heat according to the manufacturer’s specifications.
- Cooling the bonded stack under pressure to ensure a strong and uniform bond.
Vacuum lamination offers several benefits, such as:
- Reduced void formation
- Improved bond uniformity
- Compatibility with a wide range of materials
However, this method also has some limitations:
- Requires specialized vacuum equipment
- Can be more time-consuming than thermal compression bonding
- May not be suitable for very high-volume production
Plasma Bonding
Plasma bonding is a more advanced technique that uses a plasma treatment to activate the surfaces of the PCB Layers before bonding. This activation process improves the adhesion between the layers, resulting in a stronger and more reliable bond. The process involves the following steps:
- Stacking the layers in the desired order, with prepreg or adhesive sheets between each layer.
- Exposing the surfaces of the layers to a plasma treatment to activate them.
- Applying pressure and heat according to the manufacturer’s specifications.
- Cooling the bonded stack under pressure to ensure a strong and uniform bond.
Plasma bonding offers several advantages, such as:
- Improved bond strength
- Better adhesion between layers
- Reduced void formation
However, this technique also has some drawbacks:
- Requires specialized plasma equipment
- Can be more expensive than other bonding methods
- May not be suitable for all materials
Materials Used in Multilayer PCB Bonding
The materials used in multilayer PCB bonding play a critical role in determining the quality and reliability of the final board. The two main types of materials used are prepregs and adhesives.
Prepregs
Prepregs are sheets of reinforcing fabric (typically glass or aramid) that are pre-impregnated with a partially cured resin. When subjected to heat and pressure during the bonding process, the resin melts and flows, bonding the layers together. Prepregs are available in a variety of materials, thicknesses, and resin compositions to suit different applications.
Some common prepreg materials include:
- FR-4: A glass-reinforced epoxy laminate, widely used for general-purpose PCBs.
- Polyimide: A high-performance material with excellent thermal and electrical properties, suitable for demanding applications.
- PTFE: A low-dielectric-constant material with good high-frequency performance, often used in RF and microwave applications.
Adhesives
Adhesives are another option for bonding multilayer PCBs. These materials are applied between the layers and cure to form a strong bond when subjected to heat and pressure. Adhesives offer some advantages over prepregs, such as lower bonding temperatures and the ability to bond dissimilar materials.
Some common adhesive types used in multilayer PCB bonding include:
- Epoxy: A versatile and widely used adhesive with good strength and chemical resistance.
- Acrylic: A fast-curing adhesive with good environmental resistance and flexibility.
- Silicone: A high-temperature adhesive with excellent thermal stability and flexibility.
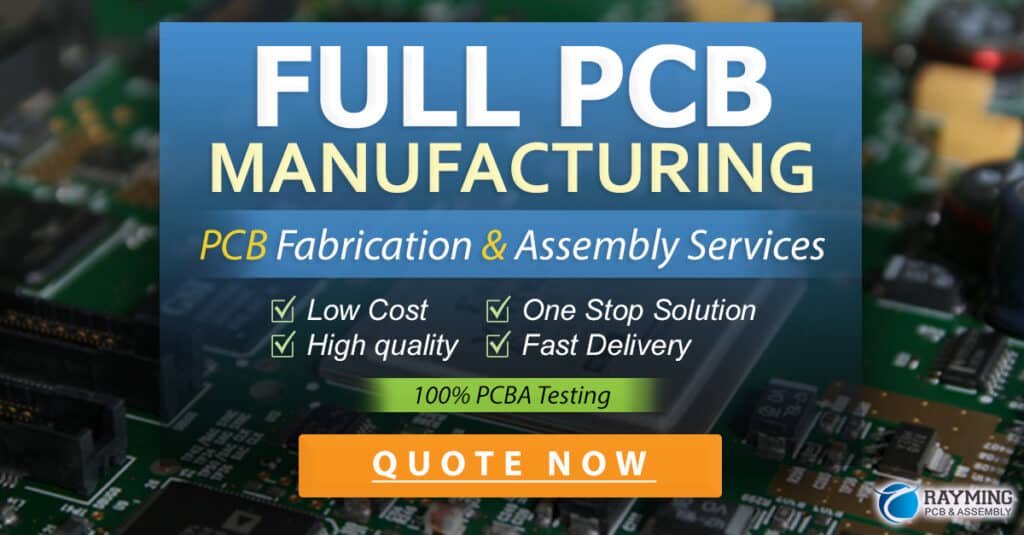
Best Practices for Multilayer PCB Bonding
To ensure the best results when bonding multilayer PCBs, consider the following best practices:
-
Material Selection: Choose materials that are compatible with your specific application and manufacturing process. Consider factors such as the number of layers, the required electrical and thermal properties, and the intended operating environment.
-
Surface Preparation: Ensure that the surfaces of the layers are clean, dry, and free from contaminants before bonding. Any dirt, grease, or oxidation can weaken the bond and lead to delamination.
-
Pressure and Temperature Control: Follow the manufacturer’s recommended settings for pressure and temperature during the bonding process. Insufficient pressure or temperature can result in weak bonds, while excessive pressure or temperature can cause damage to the layers or components.
-
Cooling and Curing: Allow the bonded stack to cool and cure under pressure to ensure a strong and uniform bond. Rapid cooling or insufficient curing time can lead to stress and delamination.
-
Quality Control: Implement a robust quality control process to inspect the bonded boards for any defects, such as voids, delamination, or misalignment. Catching these issues early can help prevent costly failures down the line.
Frequently Asked Questions (FAQ)
-
What is the difference between prepregs and adhesives in multilayer PCB bonding?
Prepregs are sheets of reinforcing fabric pre-impregnated with a partially cured resin, while adhesives are applied separately between the layers. Prepregs offer better control over the bonding process and are more widely used, while adhesives can offer lower bonding temperatures and the ability to bond dissimilar materials. -
How many layers can be bonded in a multilayer PCB?
The number of layers that can be bonded depends on several factors, such as the materials used, the bonding technique, and the manufacturing capabilities. In general, multilayer PCBs can have anywhere from 4 to over 50 layers, with some high-end boards having even more. -
What causes delamination in multilayer PCBs?
Delamination can be caused by several factors, including poor surface preparation, insufficient pressure or temperature during bonding, rapid cooling, or incompatible materials. Ensuring proper material selection, surface preparation, and process control can help minimize the risk of delamination. -
Can multilayer PCBs be reworked or repaired after bonding?
Reworking or repairing multilayer PCBs after bonding can be challenging, as the layers are permanently fused together. In some cases, minor repairs may be possible, but extensive rework often requires scrapping the board and starting over. This underscores the importance of proper design, manufacturing, and quality control to minimize the need for rework. -
What is the role of plasma treatment in multilayer PCB bonding?
Plasma treatment is used to activate the surfaces of the PCB layers before bonding, improving adhesion and resulting in a stronger bond. This technique is particularly useful for bonding dissimilar materials or when using adhesives that require surface activation for optimal performance.
Conclusion
Multilayer PCB bonding is a critical process in the fabrication of complex and high-performance electronic devices. By understanding the various bonding techniques, materials, and best practices involved, manufacturers can create reliable and high-quality boards that meet the demands of modern applications. As technology continues to advance, the importance of effective multilayer PCB bonding will only continue to grow, making it an essential skill for anyone involved in electronics manufacturing.
No responses yet