Introduction to PCB Bonding
PCB bonding is a critical process in the manufacturing of printed circuit boards (PCBs), especially for high-frequency applications such as microwave and RF circuits. The bonding process involves joining multiple layers of PCBs together to create a single, cohesive board that can withstand the rigors of manufacturing and operation. In this article, we will explore the various PCB bonding methods used in column Microwave PCBs and what designers need to know to ensure optimal performance and reliability.
Why is PCB Bonding Important for Microwave Applications?
Microwave PCBs operate at high frequencies, typically above 1 GHz, and require special considerations in terms of material selection, layout, and manufacturing processes. One of the most critical aspects of microwave PCB design is the bonding process, which directly impacts the board’s electrical performance, mechanical stability, and thermal management.
Proper PCB bonding ensures:
- Minimized signal loss and distortion
- Reduced electromagnetic interference (EMI)
- Improved heat dissipation
- Enhanced mechanical strength and durability
Types of PCB Bonding Methods
There are several PCB bonding methods used in the industry, each with its advantages and disadvantages. The choice of bonding method depends on factors such as the materials used, the application requirements, and the manufacturing constraints. The most common PCB bonding methods for column microwave PCBs include:
- Adhesive Bonding
- Fusion Bonding
- Mechanical Bonding
Adhesive Bonding
Adhesive bonding is a widely used method for joining PCB layers together. It involves applying an adhesive material between the layers and curing it under pressure and heat. The adhesive material can be either conductive or non-conductive, depending on the application requirements.
Advantages of Adhesive Bonding
- Relatively low cost
- Easy to apply and process
- Provides good mechanical strength
- Can accommodate irregular surfaces
Disadvantages of Adhesive Bonding
- Potential for voids and air gaps
- Limited temperature resistance
- Possible outgassing during curing
- May require additional surface treatment
Fusion Bonding
Fusion bonding, also known as direct bonding, involves joining PCB layers together by applying heat and pressure directly to the materials. This method relies on the molecular attraction between the surfaces to create a strong, seamless bond without the need for additional adhesives.
Advantages of Fusion Bonding
- Creates a homogeneous, void-free bond
- Provides excellent electrical and thermal conductivity
- High temperature resistance
- No additional materials required
Disadvantages of Fusion Bonding
- Requires precise surface preparation and cleanliness
- Limited to compatible materials (e.g., PTFE, ceramic)
- High processing temperatures may damage sensitive components
- Specialized equipment and expertise needed
Mechanical Bonding
Mechanical bonding involves using physical means, such as screws, rivets, or clamps, to join PCB layers together. This method is often used in conjunction with adhesive or fusion bonding to provide additional mechanical support and stability.
Advantages of Mechanical Bonding
- Provides excellent mechanical strength and durability
- Allows for easy disassembly and repair
- Can accommodate a wide range of materials
- Suitable for large or complex assemblies
Disadvantages of Mechanical Bonding
- Adds weight and bulk to the assembly
- May introduce signal integrity issues (e.g., impedance mismatch)
- Requires additional manufacturing steps and components
- Potential for mechanical stress and damage during assembly
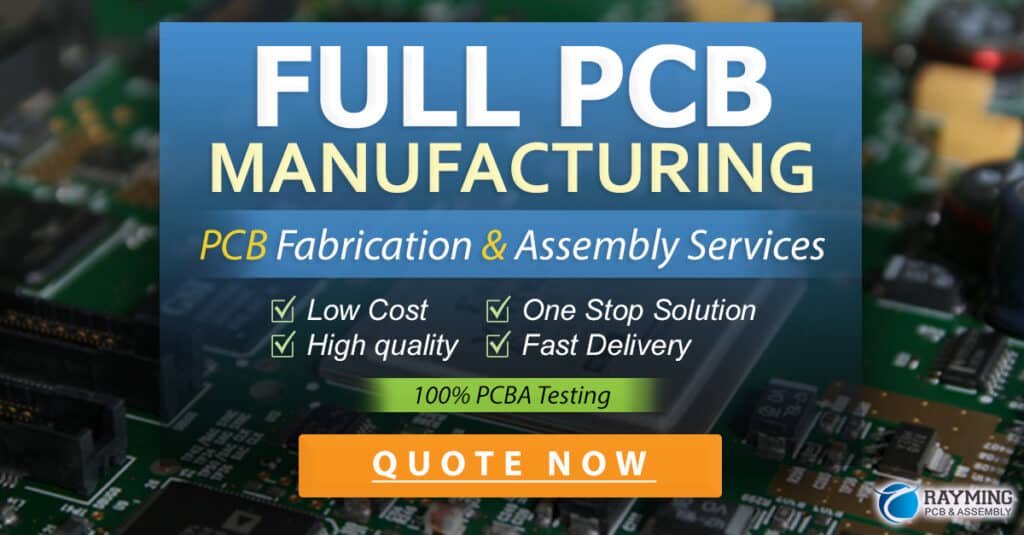
Factors to Consider When Choosing a PCB Bonding Method
When selecting a PCB bonding method for a column microwave application, designers must consider several key factors to ensure optimal performance and reliability:
-
Material Compatibility: The bonding method must be compatible with the PCB materials used, such as PTFE, Rogers, or ceramic substrates. Incompatible materials may result in poor adhesion, delamination, or other defects.
-
Electrical Performance: The bonding method should minimize signal loss, distortion, and EMI while providing adequate electrical conductivity between layers. Designers must also consider the impact of the bonding process on the board’s impedance and propagation characteristics.
-
Thermal Management: Microwave PCBs often generate significant amounts of heat, which must be efficiently dissipated to prevent component damage and ensure reliable operation. The bonding method should provide good thermal conductivity and help distribute heat evenly across the board.
-
Mechanical Strength: The bonded PCB must withstand the mechanical stresses encountered during manufacturing, assembly, and operation. The bonding method should provide sufficient strength and durability to prevent delamination, warping, or other mechanical failures.
-
Manufacturing Feasibility: The chosen bonding method must be compatible with the available manufacturing processes and equipment. Designers should consider factors such as processing time, temperature, pressure, and cost when selecting a bonding method.
Best Practices for Designing Column Microwave PCBs with Bonding in Mind
To ensure successful PCB bonding and optimal performance in column microwave applications, designers should follow these best practices:
-
Choose materials with similar thermal expansion coefficients to minimize stress and warping during bonding and operation.
-
Design the PCB layout to minimize the number of layers and the distance between bonded surfaces to reduce signal loss and improve mechanical stability.
-
Incorporate vias and other conductive structures to improve electrical and thermal conductivity between bonded layers.
-
Use symmetrical designs and balanced copper distribution to prevent warping and ensure even pressure distribution during bonding.
-
Specify appropriate surface finishes and treatments to improve adhesion and prevent contamination during bonding.
-
Collaborate closely with the PCB manufacturer to ensure compatibility between the design and the chosen bonding process.
Conclusion
PCB bonding is a critical aspect of column microwave PCB design, directly impacting the board’s electrical performance, mechanical stability, and thermal management. By understanding the various bonding methods available and their advantages and disadvantages, designers can make informed decisions to ensure optimal performance and reliability in their microwave applications. By following best practices and collaborating with PCB manufacturers, designers can successfully navigate the challenges of PCB bonding and create high-quality, reliable column microwave PCBs.
Frequently Asked Questions (FAQ)
- What is the most common PCB bonding method for column microwave applications?
-
Adhesive bonding is the most widely used method due to its relatively low cost, ease of application, and good mechanical strength. However, fusion bonding and mechanical bonding are also used depending on the specific application requirements.
-
Can different bonding methods be used together in a single PCB?
-
Yes, it is common to use a combination of bonding methods in a single PCB to achieve the desired performance and reliability. For example, adhesive bonding may be used in conjunction with mechanical bonding to provide additional support and stability.
-
How does the choice of PCB material affect the bonding process?
-
The choice of PCB material directly impacts the bonding process, as the bonding method must be compatible with the material properties. For example, PTFE and ceramic substrates are well-suited for fusion bonding, while adhesive bonding can accommodate a wider range of materials.
-
What are the main challenges in bonding column microwave PCBs?
-
The main challenges in bonding column microwave PCBs include achieving good electrical and thermal conductivity, minimizing signal loss and distortion, ensuring mechanical strength and stability, and maintaining compatibility with the manufacturing processes and equipment.
-
How can designers ensure successful PCB bonding in their column microwave applications?
- Designers can ensure successful PCB bonding by choosing compatible materials, designing the PCB layout with bonding in mind, specifying appropriate surface treatments, and collaborating closely with the PCB manufacturer to ensure compatibility between the design and the chosen bonding process. Following best practices and considering the key factors that affect bonding performance can help designers create high-quality, reliable column microwave PCBs.
No responses yet