Introduction to PCB Materials
Printed Circuit Boards (PCBs) are the backbone of modern electronics. They provide a platform for interconnecting electronic components and form the foundation of countless devices we use every day. The choice of PCB materials plays a crucial role in determining the performance, reliability, and longevity of these electronic assemblies. In this comprehensive guide, we will dive deep into the world of PCB materials, exploring their properties, applications, and impact on the PCB manufacturing process.
Types of PCB Materials
FR-4
FR-4 is the most commonly used PCB material. It is a composite material made of woven fiberglass cloth impregnated with an epoxy resin. FR-4 offers good mechanical strength, electrical insulation, and thermal stability, making it suitable for a wide range of applications.
Property | Value |
---|---|
Dielectric Constant | 4.2 – 4.9 |
Dissipation Factor | 0.02 |
Thermal Conductivity | 0.3 W/mK |
Glass Transition Temperature (Tg) | 130°C – 140°C |
High-Frequency Materials
For high-frequency applications, such as RF and microwave circuits, specialized PCB materials are required. These materials have lower dielectric constants and dissipation factors to minimize signal loss and distortion at higher frequencies. Some common high-frequency PCB materials include:
- Rogers RO4000 Series
- Isola IS680
- PTFE (Polytetrafluoroethylene)
Flexible PCB Materials
Flexible PCBs are made using materials that can bend and flex without breaking. These materials include:
- Polyimide (PI)
- Polyester (PET)
- Flexible FR-4
Flexible PCB materials enable the creation of compact, lightweight, and conformable electronic assemblies.
PCB Material Properties
Dielectric Constant (Dk)
The dielectric constant, also known as relative permittivity, is a measure of a material’s ability to store electrical energy. A lower dielectric constant is desirable for high-frequency applications to minimize signal propagation delay and loss.
Dissipation Factor (Df)
The dissipation factor, or loss tangent, represents the amount of energy lost as heat when an alternating electric field is applied to the material. A lower dissipation factor is preferred to reduce signal attenuation and maintain signal integrity.
Thermal Conductivity
Thermal conductivity is a measure of a material’s ability to conduct heat. PCB materials with higher thermal conductivity help dissipate heat more effectively, preventing thermal damage to components and improving the overall reliability of the PCB.
Glass Transition Temperature (Tg)
The glass transition temperature is the temperature at which a material transitions from a rigid, glassy state to a softer, rubbery state. PCB materials with higher Tg values can withstand higher operating temperatures without deformation or degradation.
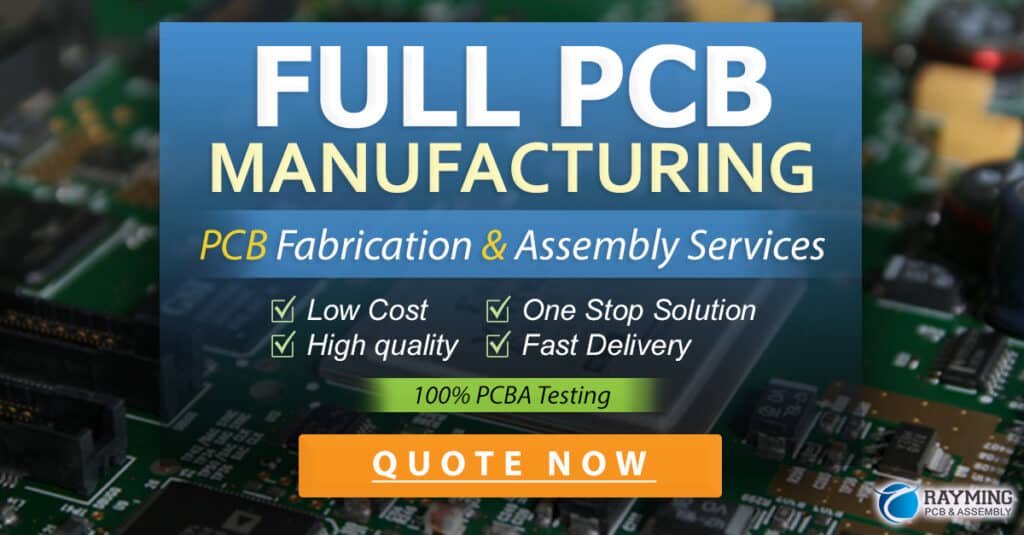
PCB Material Selection Considerations
When selecting PCB materials, several factors should be considered:
- Electrical Requirements
- Operating frequency
- Signal integrity
-
Impedance control
-
Thermal Requirements
- Operating temperature range
-
Heat dissipation
-
Mechanical Requirements
- Flexibility
- Strength and durability
-
Dimensional stability
-
Environmental Factors
- Humidity resistance
- Chemical resistance
-
UV exposure
-
Cost and Availability
- Material cost
- Minimum order quantities
- Lead times
PCB Material Impact on Manufacturing
The choice of PCB material can significantly impact the manufacturing process:
Drilling and Routing
Different PCB materials have varying hardness and machinability. Harder materials, such as ceramic-based substrates, may require specialized drilling and routing equipment and longer processing times.
Lamination
The lamination process involves bonding multiple layers of PCB material together under heat and pressure. The lamination parameters, such as temperature, pressure, and duration, must be carefully controlled to ensure proper bonding and avoid material degradation.
Etching
The etching process removes unwanted copper from the PCB surface to create the desired circuit pattern. The etchant compatibility and etch rate can vary depending on the PCB material, requiring adjustments to the etching process parameters.
Soldermask Application
Soldermask is a protective coating applied to the PCB surface to prevent short circuits and improve solderability. The adhesion and compatibility of the soldermask material with the underlying PCB substrate are important considerations.
FAQ
-
Q: What is the most common PCB material?
A: FR-4 is the most widely used PCB material due to its good balance of electrical, mechanical, and thermal properties. -
Q: What are high-frequency PCB materials?
A: High-frequency PCB materials, such as Rogers RO4000 series and Isola IS680, have lower dielectric constants and dissipation factors to minimize signal loss and distortion at higher frequencies. -
Q: What factors should be considered when selecting PCB materials?
A: When selecting PCB materials, consider electrical requirements (operating frequency, signal integrity), thermal requirements (operating temperature, heat dissipation), mechanical requirements (flexibility, strength), environmental factors (humidity, chemical resistance), and cost and availability. -
Q: How does the choice of PCB material impact the manufacturing process?
A: The choice of PCB material can affect drilling and routing (machinability), lamination (bonding parameters), etching (etchant compatibility, etch rate), and soldermask application (adhesion, compatibility). -
Q: What are flexible PCB materials?
A: Flexible PCB materials, such as polyimide (PI), polyester (PET), and flexible FR-4, enable the creation of bendable and conformable electronic assemblies for applications requiring flexibility and compact packaging.
Conclusion
PCB materials form the foundation of every electronic assembly. Understanding the properties, applications, and manufacturing implications of different PCB materials is crucial for designing and producing reliable, high-performance PCBs. By considering factors such as electrical requirements, thermal management, mechanical properties, and environmental conditions, engineers can select the most suitable PCB material for their specific application. With advancements in material science and manufacturing technologies, new PCB materials continue to emerge, offering improved performance and capabilities for the ever-evolving electronics industry.
No responses yet