What are Flexible PCBs?
Flexible PCBs, also known as flex circuits, are thin, lightweight, and bendable printed circuit boards that offer numerous advantages over traditional rigid PCBs. They consist of a flexible substrate, typically made of polyimide or other flexible materials, with conductive traces and components mounted on the surface. Flexible PCBs can be single-sided, double-sided, or multi-layered, depending on the complexity of the design and the required functionality.
Advantages of Flexible PCBs
- Compact design: Flexible PCBs allow for more compact and space-saving designs compared to rigid PCBs, as they can be bent, folded, or twisted to fit into tight spaces.
- Lightweight: The thin and lightweight nature of flexible PCBs makes them ideal for portable and weight-sensitive applications, such as wearable devices and aerospace systems.
- Improved reliability: Flexible PCBs offer better resistance to vibration, shock, and thermal stress, resulting in improved reliability and longer product life.
- Enhanced signal integrity: The reduced distance between components and the ability to control impedance in flexible PCBs lead to improved signal integrity and reduced electromagnetic interference (EMI).
- Cost-effective: Flexible PCBs can simplify assembly processes and reduce the need for connectors and wiring, leading to cost savings in manufacturing and assembly.
Factors to Consider When Choosing Flexible PCB Materials
When selecting the appropriate flexible PCB material for your application, several key factors should be considered to ensure optimal performance and cost-effectiveness.
1. Electrical Properties
The electrical properties of the flexible PCB material are crucial for ensuring proper functionality and signal integrity. Consider the following aspects:
- Dielectric constant (Dk): The dielectric constant determines the material’s ability to store electrical energy. A lower Dk value is desirable for high-frequency applications to minimize signal loss and distortion.
- Dissipation factor (Df): The dissipation factor measures the material’s tendency to absorb electrical energy and convert it into heat. A lower Df value is preferred to minimize signal loss and maintain signal integrity.
- Insulation resistance: The insulation resistance indicates the material’s ability to resist electrical current flow between conductors. Higher insulation resistance is essential to prevent short circuits and maintain signal integrity.
2. Mechanical Properties
The mechanical properties of the flexible PCB material determine its ability to withstand physical stress and maintain its structural integrity. Consider the following factors:
- Flexural endurance: Flexural endurance refers to the material’s ability to withstand repeated bending and folding without cracking or breaking. Higher flexural endurance is essential for applications that require frequent flexing or dynamic motion.
- Tensile strength: Tensile strength measures the material’s ability to resist stretching and breaking under tension. Higher tensile strength is desirable for applications that involve stretching or pulling forces.
- Dimensional stability: Dimensional stability refers to the material’s ability to maintain its size and shape under varying environmental conditions, such as temperature and humidity changes. Good dimensional stability is crucial for maintaining the accuracy of the circuit layout and preventing warping or deformation.
3. Thermal Properties
The thermal properties of the flexible PCB material are essential for ensuring reliable performance in various temperature conditions. Consider the following aspects:
- Glass transition temperature (Tg): The glass transition temperature is the point at which the material transitions from a rigid, glassy state to a softer, rubbery state. A higher Tg value is desirable for applications that require high-temperature stability and resistance to thermal deformation.
- Coefficient of thermal expansion (CTE): The CTE measures the material’s tendency to expand or contract with changes in temperature. A lower CTE value is preferred to minimize stress on components and solder joints caused by thermal expansion mismatches.
- Thermal conductivity: Thermal conductivity refers to the material’s ability to conduct heat away from components and distribute it evenly across the PCB. Higher thermal conductivity is beneficial for applications that generate significant heat, as it helps prevent hot spots and improves overall thermal management.
4. Chemical Resistance
The chemical resistance of the flexible PCB material is crucial for ensuring the long-term reliability of the circuit in environments where it may be exposed to various chemicals, solvents, or moisture. Consider the following factors:
- Resistance to solvents and cleaning agents: The material should be resistant to the solvents and cleaning agents used during the manufacturing process and in the end-use environment to prevent degradation or delamination of the PCB.
- Moisture resistance: The material should have good moisture resistance to prevent water absorption, which can lead to swelling, delamination, or changes in electrical properties.
- Resistance to environmental pollutants: The material should be resistant to common environmental pollutants, such as salt spray, sulfur dioxide, and nitrogen oxides, to ensure reliable performance in harsh environments.
5. Cost and Availability
The cost and availability of the flexible PCB material are essential considerations for ensuring the feasibility and cost-effectiveness of your project. Consider the following aspects:
- Material cost: The cost of the flexible PCB material should be evaluated in relation to the project budget and the required performance characteristics. Some high-performance materials may have a higher initial cost but can offer long-term cost savings through improved reliability and durability.
- Availability and lead times: The availability and lead times of the flexible PCB material should be considered to ensure timely procurement and avoid potential project delays. Some specialized materials may have longer lead times or limited availability, which can impact project schedules and costs.
- Minimum order quantities (MOQs): The MOQs for the flexible PCB material should be considered in relation to your project’s production volume. Some materials may have higher MOQs, which can increase inventory costs and impact cash flow for low-volume projects.
Common Flexible PCB Materials
There are several common flexible PCB materials available, each with its own unique properties and advantages. The following table summarizes the key characteristics of some widely used flexible PCB materials:
Material | Dielectric Constant (Dk) | Dissipation Factor (Df) | Glass Transition Temperature (Tg) | Flexural Endurance | Typical Applications |
---|---|---|---|---|---|
Polyimide (PI) | 3.2 – 3.5 | 0.002 – 0.008 | 360°C – 400°C | High | High-temperature, aerospace, military |
Polyester (PET) | 2.8 – 3.2 | 0.002 – 0.005 | 70°C – 150°C | Moderate | Consumer electronics, displays |
Liquid Crystal Polymer (LCP) | 2.9 – 3.1 | 0.002 – 0.004 | 280°C – 320°C | High | High-frequency, automotive, medical |
Flex-Rigid | 3.2 – 4.5 | 0.01 – 0.03 | 130°C – 170°C | Moderate | Complex designs, mixed rigid and flexible |
Polyimide (PI)
Polyimide is one of the most widely used materials for flexible PCBs due to its excellent thermal stability, chemical resistance, and mechanical properties. It offers high flexural endurance and can withstand temperatures up to 400°C, making it suitable for high-temperature applications in aerospace, military, and automotive industries.
Polyester (PET)
Polyester is a cost-effective material for flexible PCBs, offering good electrical properties and moderate flexural endurance. It is commonly used in consumer electronics, displays, and applications that require a balance between cost and performance.
Liquid Crystal Polymer (LCP)
Liquid Crystal Polymer is a high-performance material that offers excellent electrical properties, including low dielectric constant and dissipation factor, making it suitable for high-frequency applications. LCP also exhibits high thermal stability and chemical resistance, making it ideal for automotive, medical, and telecommunications industries.
Flex-Rigid
Flex-Rigid materials combine the benefits of both flexible and rigid PCBs, allowing for the creation of complex designs that require both flexibility and structural support. These materials typically consist of a flexible substrate, such as polyimide, bonded to a rigid substrate, such as FR-4. Flex-Rigid PCBs are commonly used in applications that require high density and reliability, such as medical devices, industrial controls, and automotive electronics.
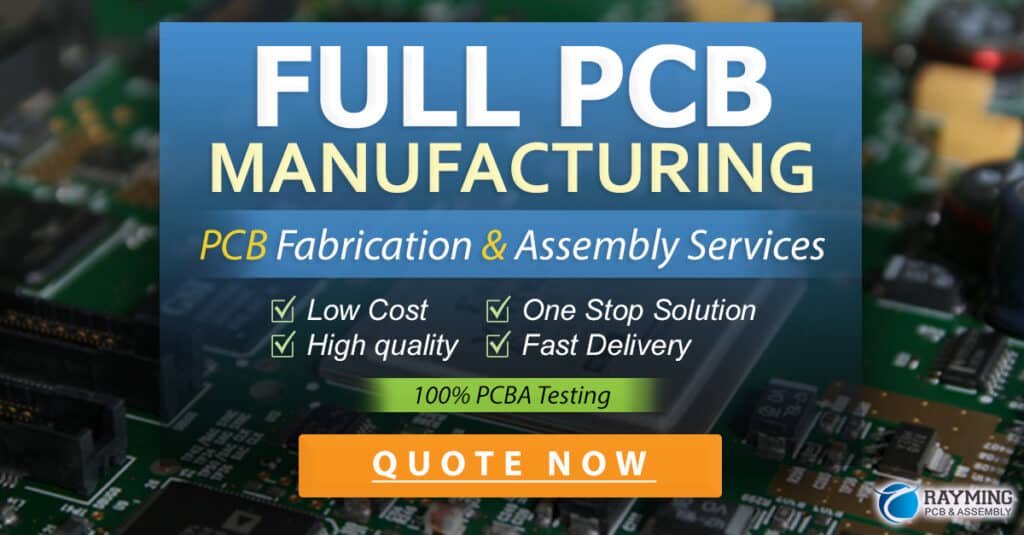
Frequently Asked Questions (FAQ)
-
Q: What is the most important factor to consider when choosing a flexible PCB material?
A: The most important factor to consider when choosing a flexible PCB material depends on your specific application requirements. However, in general, the electrical properties, such as dielectric constant and dissipation factor, are crucial for ensuring proper functionality and signal integrity. -
Q: Can flexible PCBs be used in high-temperature applications?
A: Yes, certain flexible PCB materials, such as polyimide (PI), can withstand high temperatures up to 400°C, making them suitable for high-temperature applications in aerospace, military, and automotive industries. -
Q: Are flexible PCBs more expensive than rigid PCBs?
A: The cost of flexible PCBs can be higher than rigid PCBs due to the specialized materials and manufacturing processes involved. However, the use of flexible PCBs can lead to cost savings in the long run through simplified assembly, reduced wiring and connectors, and improved reliability. -
Q: How do I determine the appropriate thickness for my flexible PCB?
A: The appropriate thickness for your flexible PCB depends on factors such as the required flexibility, mechanical strength, and the number of layers in the design. Thinner materials offer greater flexibility but may have reduced mechanical strength. It is essential to consult with your PCB manufacturer to determine the optimal thickness for your specific application. -
Q: Can flexible PCBs be used in high-frequency applications?
A: Yes, certain flexible PCB materials, such as Liquid Crystal Polymer (LCP), offer excellent electrical properties, including low dielectric constant and dissipation factor, making them suitable for high-frequency applications in telecommunications, automotive, and medical industries.
Conclusion
Choosing the right flexible PCB material is crucial for ensuring optimal performance, reliability, and cost-effectiveness in your electronic devices. By considering factors such as electrical properties, mechanical properties, thermal properties, chemical resistance, and cost, you can select the most appropriate material for your specific application needs.
Whether you require high-temperature stability, high-frequency performance, or a balance between cost and performance, there is a flexible PCB material available to meet your requirements. By working closely with your PCB manufacturer and leveraging their expertise, you can design and produce flexible PCBs that deliver exceptional functionality and durability in your target applications.
As technology continues to advance and the demand for compact, lightweight, and reliable electronic devices grows, the importance of selecting the right flexible PCB material will only increase. By staying informed about the latest material options and their properties, you can make informed decisions that drive innovation and success in your projects.
No responses yet