Introduction to PCB Manufacturing
Printed Circuit Board (PCB) manufacturing is a crucial process in the electronics industry. PCBs are the backbone of almost all electronic devices, from smartphones and computers to medical equipment and aerospace systems. PCB manufacturing services play a vital role in bringing these devices to life by providing high-quality, reliable, and cost-effective PCBs.
What is a PCB?
A PCB is a flat board made of insulating materials, such as fiberglass or composite epoxy, with conductive pathways etched or printed onto its surface. These pathways, known as traces, connect various electronic components, such as resistors, capacitors, and integrated circuits (ICs), to form a complete electronic circuit.
Types of PCBs
There are several types of PCBs, each with its own unique characteristics and applications:
-
Single-sided PCBs: These PCBs have conductive traces on only one side of the board. They are the simplest and most cost-effective type of PCB, suitable for low-complexity circuits.
-
Double-sided PCBs: These PCBs have conductive traces on both sides of the board, allowing for more complex circuits and higher component density. The two sides are connected through plated holes called vias.
-
Multi-layer PCBs: These PCBs consist of multiple layers of conductive traces separated by insulating layers. They offer the highest component density and are used in complex electronic devices, such as smartphones and computers.
-
Flexible PCBs: These PCBs are made of flexible materials, such as polyimide, allowing them to bend and conform to various shapes. They are used in applications where space is limited or where the PCB needs to fit into a specific form factor.
-
Rigid-Flex PCBs: These PCBs combine the benefits of both rigid and flexible PCBs. They consist of rigid sections connected by flexible sections, allowing for greater design freedom and improved reliability.
PCB Manufacturing Process
The PCB manufacturing process involves several steps, each requiring precision and adherence to strict quality standards. The main stages of PCB manufacturing are:
1. PCB Design and Layout
The first step in PCB manufacturing is designing the circuit and creating a layout. This is done using specialized software, such as Altium Designer or KiCad. The designer creates a schematic diagram of the circuit, which is then translated into a physical layout. The layout determines the placement of components, the routing of traces, and the overall dimensions of the PCB.
2. PCB Fabrication
Once the design is finalized, the PCB fabrication process begins. This involves several sub-steps:
-
Substrate preparation: The substrate material, usually fiberglass or composite epoxy, is cut to the required size and thickness.
-
Copper cladding: A thin layer of copper is laminated onto the substrate using heat and pressure.
-
Drilling: Holes are drilled into the substrate to accommodate through-hole components and vias.
-
Plating: The holes are plated with copper to create electrical connections between layers.
-
Etching: The unwanted copper is removed using a chemical etching process, leaving only the desired traces.
-
Solder mask application: A protective layer, called solder mask, is applied to the PCB to insulate the traces and prevent short circuits.
-
Silkscreen printing: Text and symbols are printed onto the PCB for component identification and assembly instructions.
3. PCB Assembly
After the PCB is fabricated, the electronic components are assembled onto the board. This can be done manually for low-volume production or using automated machines for high-volume production. The main steps in PCB assembly are:
-
Solder paste application: Solder paste, a mixture of tiny solder particles and flux, is applied to the pads on the PCB where components will be placed.
-
Component placement: The electronic components are placed onto the PCB, either manually or using pick-and-place machines.
-
Reflow soldering: The PCB is heated in a reflow oven, causing the solder paste to melt and form a permanent connection between the components and the PCB.
-
Inspection and testing: The assembled PCB is inspected visually and tested electrically to ensure proper functionality and adherence to quality standards.
Benefits of PCB Manufacturing Services
Outsourcing PCB manufacturing to a reliable service provider offers several benefits:
-
Cost savings: PCB manufacturing services have the expertise, equipment, and economies of scale to produce PCBs at a lower cost than in-house manufacturing.
-
Faster turnaround times: Professional PCB manufacturers have streamlined processes and dedicated resources, allowing them to deliver PCBs faster than in-house production.
-
Higher quality: PCB manufacturing service providers adhere to strict quality standards and have the necessary expertise to produce high-quality PCBs consistently.
-
Access to advanced technologies: PCB manufacturers invest in state-of-the-art equipment and technologies, enabling them to produce PCBs with advanced features and capabilities.
-
Scalability: PCB manufacturing services can easily scale production up or down based on demand, allowing companies to respond quickly to market changes.
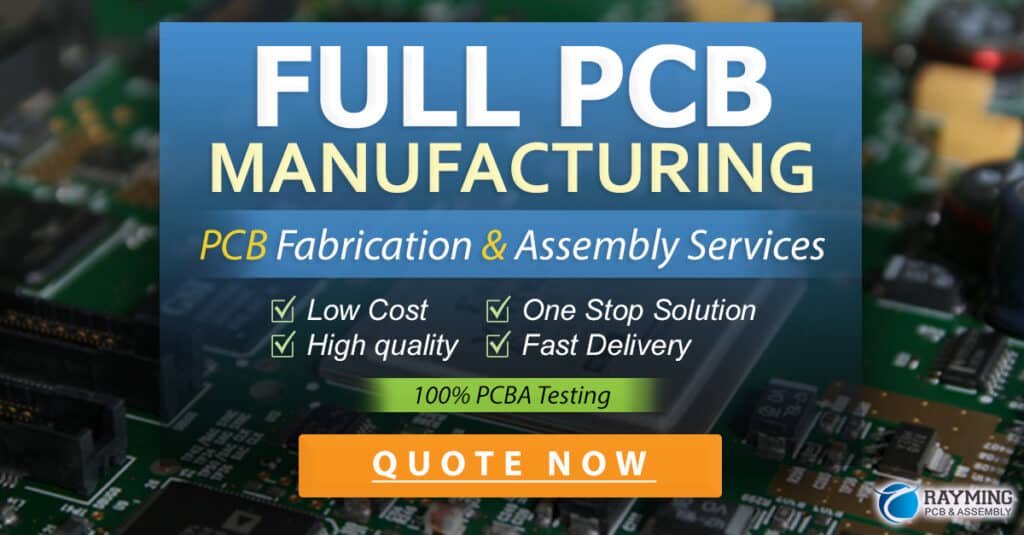
Choosing a PCB Manufacturing Service Provider
When selecting a PCB manufacturing service provider, consider the following factors:
-
Experience and expertise: Look for a manufacturer with a proven track record and experience in producing PCBs similar to your requirements.
-
Quality standards: Ensure that the manufacturer adheres to industry-recognized quality standards, such as IPC (Association Connecting Electronics Industries) standards.
-
Capabilities: Choose a manufacturer that offers the specific capabilities you need, such as multi-layer PCBs, flexible PCBs, or high-density interconnect (HDI) PCBs.
-
Turnaround time: Consider the manufacturer’s typical turnaround times and their ability to meet your deadlines.
-
Customer support: Look for a manufacturer that provides excellent customer support, including responsive communication and technical assistance.
Future Trends in PCB Manufacturing
PCB manufacturing is continuously evolving to meet the demands of advancing technology. Some of the key trends shaping the future of PCB manufacturing include:
-
Miniaturization: As electronic devices become smaller and more compact, PCBs need to accommodate higher component density and smaller feature sizes.
-
High-speed and high-frequency applications: The increasing demand for high-speed data transmission and high-frequency applications, such as 5G networks and IoT devices, requires PCBs with advanced materials and design techniques.
-
Environmentally friendly materials: There is a growing emphasis on using eco-friendly materials in PCB manufacturing, such as halogen-free and lead-free materials, to reduce the environmental impact of electronic waste.
-
Additive manufacturing: 3D printing technologies are being explored for PCB manufacturing, potentially enabling faster prototyping and more complex PCB designs.
-
Intelligent PCBs: The integration of sensors, antennae, and other smart components into PCBs is becoming more common, enabling the development of intelligent and connected devices.
Conclusion
PCB manufacturing services play a critical role in the electronics industry, providing the foundation for the devices that shape our modern world. By understanding the PCB manufacturing process, its benefits, and the key factors to consider when choosing a service provider, companies can ensure they receive high-quality, reliable PCBs that meet their specific requirements. As technology continues to advance, PCB manufacturing will evolve to keep pace, driving innovation and enabling the development of ever-more sophisticated electronic devices.
FAQ
-
What is the typical turnaround time for PCB manufacturing?
The turnaround time for PCB manufacturing varies depending on the complexity of the design, the quantity ordered, and the manufacturer’s capacity. For simple, low-volume orders, turnaround times can be as short as 24-48 hours. For more complex, high-volume orders, turnaround times can range from several days to several weeks. -
What is the minimum order quantity (MOQ) for PCB manufacturing?
The MOQ for PCB manufacturing varies among service providers. Some manufacturers offer low MOQs, even as low as one piece, for prototyping and small-scale production. Others may require higher MOQs, such as 100 or 1,000 pieces, for larger-scale production runs. It’s essential to discuss your specific requirements with the manufacturer to determine their MOQ policies. -
How much does PCB Manufacturing Cost?
The cost of PCB manufacturing depends on several factors, including the size and complexity of the PCB, the number of layers, the materials used, the quantity ordered, and the turnaround time. Simple, low-volume orders can cost a few dollars per PCB, while complex, high-volume orders can cost several hundred or even thousands of dollars. It’s best to request a quote from the manufacturer based on your specific requirements to get an accurate cost estimate. -
What file formats are required for PCB manufacturing?
PCB manufacturers typically require a set of files known as Gerber files, which contain the necessary information for fabricating the PCB. Gerber files include data on the copper layers, solder mask, silkscreen, and drill holes. In addition to Gerber files, manufacturers may also require a drill file, a bill of materials (BOM), and assembly drawings. It’s essential to check with the manufacturer for their specific file format requirements. -
What quality standards do PCB manufacturing services adhere to?
Reputable PCB manufacturing services adhere to industry-recognized quality standards, such as those set by the IPC (Association Connecting Electronics Industries). These standards cover various aspects of PCB manufacturing, including design, fabrication, assembly, and testing. Some common IPC standards include IPC-A-600 for acceptability of printed boards, IPC-6012 for qualification and performance specification for rigid PCBs, and IPC-J-STD-001 for requirements for soldered electrical and electronic assemblies. When choosing a PCB manufacturing service provider, it’s essential to ensure they comply with relevant quality standards to guarantee the reliability and performance of your PCBs.
PCB Type | Layers | Typical Applications | Cost |
---|---|---|---|
Single-sided | 1 | Simple circuits, low-power devices | $ |
Double-sided | 2 | More complex circuits, higher component density | $$ |
Multi-layer | 4-12+ | High-density circuits, advanced devices | $$$ |
Flexible | 1-2 | Wearables, space-constrained devices | $$$ |
Rigid-Flex | Varies | Complex devices requiring both rigid and flexible sections | $$$$ |
No responses yet