Types of PCB Manufacturing Equipment
1. PCB Design Software
PCB design software is the first step in the manufacturing process. It allows engineers to create detailed layouts and schematics for the circuit board. Some popular PCB design software include:
- Altium Designer
- KiCad
- Eagle
- OrCAD
These software tools help designers create complex designs, simulate circuits, and generate files for manufacturing.
2. PCB Printing Equipment
After the design is complete, the next step is to print the circuit pattern onto the copper-clad board. There are several methods for PCB printing, including:
Screen Printing
Screen printing is a traditional method that uses a stencil to apply ink onto the board. The process involves:
- Creating a screen with the desired pattern
- Placing the screen on top of the board
- Applying ink through the screen onto the board
Inkjet Printing
Inkjet printing is a newer technology that uses a printer to deposit ink directly onto the board. This method is faster and more precise than screen printing, making it ideal for high-volume production.
3. Etching Equipment
Once the circuit pattern is printed onto the board, the next step is to remove the unwanted copper. This process is called etching. There are two main types of etching equipment:
Chemical Etching
Chemical etching involves submerging the board in a chemical solution that dissolves the unwanted copper. The most common etchant is ferric chloride. The process involves:
- Placing the board in a tank filled with the etchant
- Agitating the solution to ensure even etching
- Removing the board once the etching is complete
Plasma Etching
Plasma etching uses a high-energy plasma to remove the unwanted copper. This method is faster and more environmentally friendly than chemical etching. The process involves:
- Placing the board in a vacuum chamber
- Generating a plasma using radio frequency (RF) power
- Directing the plasma towards the board to remove the copper
4. Drilling Equipment
After etching, the next step is to drill holes in the board for component placement. There are several types of drilling equipment, including:
CNC Drilling Machines
CNC (Computer Numerical Control) drilling machines are automated tools that use a drill bit to create holes in the board. These machines are programmed with the desired drill patterns and can produce high-quality holes with minimal human intervention.
Laser Drilling Machines
Laser drilling machines use a high-powered laser to create holes in the board. This method is faster and more precise than traditional drilling, making it ideal for high-density boards.
5. Solder Mask Application Equipment
Solder mask is a protective layer that is applied to the board to prevent short circuits and improve the board’s durability. There are several methods for applying solder mask, including:
Liquid Photoimageable (LPI) Solder Mask
LPI solder mask is a liquid material that is applied to the board using a screen printing process. The material is then exposed to UV light, which cures the solder mask in the desired pattern.
Dry Film Solder Mask
Dry film solder mask is a solid material that is laminated onto the board using heat and pressure. The material is then exposed to UV light, which cures the solder mask in the desired pattern.
6. Surface Finish Equipment
Surface finish is the final layer applied to the board to improve its solderability and protect the copper from oxidation. There are several types of surface finish, including:
Hot Air Solder Leveling (HASL)
HASL involves dipping the board in molten solder and then using hot air to level the solder on the surface. This method is simple and cost-effective, making it a popular choice for many manufacturers.
Electroless Nickel Immersion Gold (ENIG)
ENIG involves plating the board with a layer of nickel and then a thin layer of gold. This method provides excellent solderability and durability, making it ideal for high-reliability applications.
Immersion Silver (IAg)
IAg involves plating the board with a thin layer of silver. This method provides good solderability and is a cost-effective alternative to ENIG.
Importance of PCB Manufacturing Equipment
PCB manufacturing equipment is essential for producing high-quality circuit boards consistently and efficiently. Here are some reasons why these machines are so important:
1. Improved Accuracy
PCB manufacturing equipment is designed to produce circuit boards with high precision and accuracy. These machines use advanced technologies such as computer numerical control (CNC) and laser technology to ensure that the boards are manufactured to the exact specifications required.
2. Increased Efficiency
PCB manufacturing equipment helps to streamline the production process, reducing the time and labor required to produce circuit boards. Automated machines can work 24/7, allowing manufacturers to produce boards faster and more efficiently than manual methods.
3. Consistent Quality
PCB manufacturing equipment helps to ensure consistent quality across all boards produced. These machines are programmed to follow specific parameters and tolerances, reducing the risk of errors and defects.
4. Cost Savings
Investing in PCB manufacturing equipment can help manufacturers reduce costs in the long run. Automated machines require less labor and can produce boards faster, reducing the overall cost per board.
Value of PCB Manufacturing Equipment
PCB manufacturing equipment is a valuable asset for any electronics manufacturer. These machines are essential for producing high-quality circuit boards that meet the demanding requirements of today’s electronics industry. Here are some ways in which PCB manufacturing equipment adds value:
1. Competitive Advantage
Investing in advanced PCB manufacturing equipment can give manufacturers a competitive advantage in the market. These machines allow manufacturers to produce high-quality boards faster and more efficiently than their competitors, helping them to win more business.
2. Increased Profitability
PCB manufacturing equipment can help manufacturers increase their profitability by reducing costs and improving efficiency. Automated machines require less labor and can produce boards faster, allowing manufacturers to take on more orders and increase their revenue.
3. Improved Customer Satisfaction
Producing high-quality circuit boards consistently and efficiently helps to improve customer satisfaction. Customers expect their orders to be delivered on time and to the required specifications, and PCB manufacturing equipment helps manufacturers meet these expectations.
4. Future-Proofing
Investing in advanced PCB manufacturing equipment can help manufacturers future-proof their business. As technology continues to evolve, manufacturers need to be able to produce boards that meet the latest industry standards and requirements. Advanced manufacturing equipment helps manufacturers stay ahead of the curve and adapt to changing market demands.
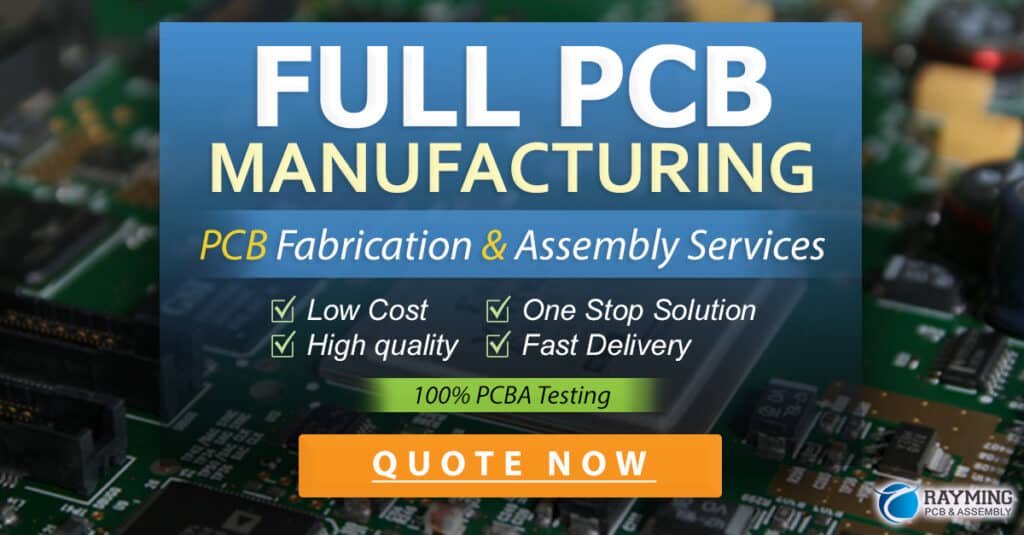
FAQ
1. What is the most important piece of equipment in PCB manufacturing?
There is no single most important piece of equipment in PCB manufacturing, as each machine plays a critical role in the production process. However, some of the most essential machines include PCB design software, etching equipment, and drilling machines.
2. How much does PCB manufacturing equipment cost?
The cost of PCB manufacturing equipment varies depending on the type of machine and its features. Some machines, such as PCB design software, can cost a few thousand dollars, while others, such as advanced CNC drilling machines, can cost hundreds of thousands of dollars.
3. Can PCB manufacturing be done manually?
While it is possible to manufacture PCBs manually, it is not practical or efficient for large-scale production. Manual methods are time-consuming and prone to errors, making them unsuitable for the demands of today’s electronics industry.
4. What is the difference between chemical etching and plasma etching?
Chemical etching involves using a chemical solution to dissolve unwanted copper from the board, while plasma etching uses a high-energy plasma to remove the copper. Plasma etching is faster and more environmentally friendly than chemical etching, but it requires specialized equipment.
5. What is the purpose of solder mask in PCB manufacturing?
Solder mask is a protective layer that is applied to the board to prevent short circuits and improve the board’s durability. It also helps to improve the board’s aesthetic appearance and makes it easier to solder components onto the board.
Conclusion
PCB manufacturing equipment is essential for producing high-quality circuit boards consistently and efficiently. These machines help to improve accuracy, increase efficiency, ensure consistent quality, and reduce costs. Investing in advanced PCB manufacturing equipment can give manufacturers a competitive advantage, increase profitability, improve customer satisfaction, and future-proof their business. As the electronics industry continues to evolve, PCB manufacturing equipment will remain a valuable asset for any manufacturer looking to stay ahead of the curve.
Equipment Type | Function | Examples |
---|---|---|
PCB Design Software | Create detailed layouts and schematics for the board | Altium Designer, KiCad, Eagle |
PCB Printing Equipment | Print the circuit pattern onto the copper-clad board | Screen printing, inkjet printing |
Etching Equipment | Remove unwanted copper from the board | Chemical etching, plasma etching |
Drilling Equipment | Create holes in the board for component placement | CNC drilling, laser drilling |
Solder Mask Application Equipment | Apply a protective layer to prevent short circuits | LPI solder mask, dry film solder mask |
Surface Finish Equipment | Apply a final layer to improve solderability and protection | HASL, ENIG, IAg |
No responses yet