Introduction
Printed Circuit Boards (PCBs) are essential components in modern electronics, providing the foundation for interconnecting electronic components. The manufacturing process of PCBs involves several critical steps, one of which is drilling. Drilling is the process of creating holes in the PCB Substrate to allow for the insertion of components and the creation of vias for electrical connections between layers. However, drilling defects can occur during the manufacturing process, leading to issues with the functionality and reliability of the final product. In this article, we will explore the various causes of PCB Drilling defects and discuss methods for their elimination.
Types of PCB Drilling Defects
There are several types of drilling defects that can occur during the PCB manufacturing process. Some of the most common include:
Misaligned Holes
Misaligned holes occur when the drilled holes do not align with the intended locations on the PCB design. This can be caused by issues with the drilling machine’s calibration or positioning accuracy.
Oversized or Undersized Holes
Oversized or undersized holes occur when the diameter of the drilled holes is larger or smaller than the specified size in the PCB design. This can be caused by worn or damaged drill bits, incorrect drill bit selection, or improper machine settings.
Incomplete or Missing Holes
Incomplete or missing holes occur when the drilling process fails to create a hole entirely or only partially drills through the PCB substrate. This can be caused by dull or broken drill bits, incorrect drilling parameters, or machine malfunctions.
Burrs and Rough Hole Walls
Burrs and rough hole walls occur when the edges of the drilled holes are not smooth or have excess material protruding from the surface. This can be caused by worn or damaged drill bits, incorrect drilling speeds and feeds, or inadequate cleaning and deburring processes.
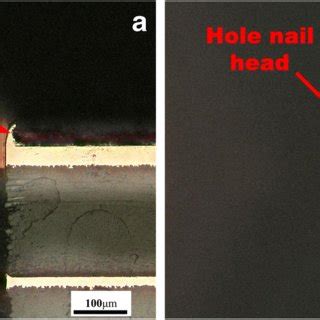
Causes of PCB Drilling Defects
There are several factors that can contribute to the occurrence of drilling defects in PCB manufacturing. These include:
Drill Bit Wear and Damage
Drill bits are subject to wear and damage over time, which can lead to inaccuracies in hole size and position. Factors that contribute to drill bit wear include:
- Abrasive nature of the PCB substrate material
- High drilling speeds and feeds
- Inadequate cooling or lubrication during drilling
- Improper storage and handling of drill bits
Incorrect Drilling Parameters
Incorrect drilling parameters, such as spindle speed, feed rate, and depth of cut, can lead to drilling defects. These parameters must be carefully selected based on the specific requirements of the PCB design and the capabilities of the drilling machine.
Machine Calibration and Maintenance
Proper calibration and maintenance of the drilling machine are essential for ensuring accurate and consistent drilling results. Factors that can affect machine performance include:
- Wear and tear on machine components
- Incorrect or outdated calibration settings
- Inadequate cleaning and lubrication of machine parts
- Improper machine setup and operation
Material Handling and Storage
Improper handling and storage of the PCB substrate material can also contribute to drilling defects. Factors to consider include:
- Moisture content of the substrate material
- Temperature and humidity conditions during storage
- Physical damage to the substrate during handling and transport
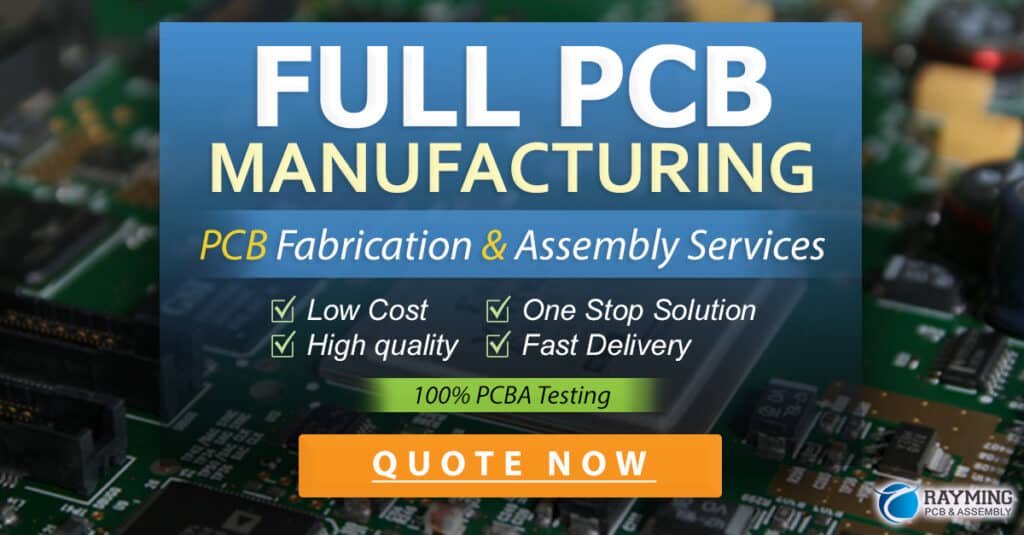
Elimination Methods for PCB Drilling Defects
To minimize the occurrence of drilling defects in PCB manufacturing, several methods can be employed:
Proper Drill Bit Selection and Maintenance
Selecting the appropriate drill bit for the specific PCB design and material is crucial for achieving accurate and consistent drilling results. Factors to consider when selecting drill bits include:
- Material composition and hardness of the PCB substrate
- Required hole size and tolerance
- Drilling depth and aspect ratio
Regular maintenance and replacement of drill bits are also essential for maintaining drilling accuracy and minimizing defects. This includes:
- Inspecting drill bits for wear and damage before each use
- Regularly sharpening or replacing worn drill bits
- Proper storage and handling of drill bits to prevent damage
Optimizing Drilling Parameters
Optimizing drilling parameters, such as spindle speed, feed rate, and depth of cut, can help to minimize drilling defects and improve hole quality. This requires careful consideration of the specific requirements of the PCB design and the capabilities of the drilling machine. Some key factors to consider include:
- Material properties of the PCB substrate
- Required hole size and tolerance
- Drilling depth and aspect ratio
- Capabilities and limitations of the drilling machine
Parameter | Description | Optimization Considerations |
---|---|---|
Spindle Speed | The rotational speed of the drill bit, measured in revolutions per minute (RPM) | – Material hardness and composition – Drill bit diameter and geometry – Required hole quality and surface finish |
Feed Rate | The speed at which the drill bit advances into the PCB substrate, measured in inches per minute (IPM) or millimeters per minute (mm/min) | – Material thickness and composition – Drill bit diameter and geometry – Required hole quality and throughput |
Depth of Cut | The distance the drill bit advances into the PCB substrate with each revolution, measured in inches per revolution (IPR) or millimeters per revolution (mm/rev) | – Material thickness and composition – Drill bit diameter and geometry – Required hole quality and aspect ratio |
Implementing Proper Machine Calibration and Maintenance
Regular calibration and maintenance of the drilling machine are essential for ensuring accurate and consistent drilling results. This includes:
- Regularly inspecting and adjusting machine components for wear and alignment
- Updating and verifying machine calibration settings
- Implementing a preventive maintenance schedule for cleaning, lubrication, and repair of machine parts
- Providing proper training and supervision for machine operators
Ensuring Proper Material Handling and Storage
Proper handling and storage of the PCB substrate material can help to minimize drilling defects by ensuring consistent material properties and preventing physical damage. This includes:
- Storing PCB substrates in a controlled environment with appropriate temperature and humidity levels
- Handling PCB substrates with care to prevent physical damage, such as bending or scratching
- Verifying the moisture content of the PCB substrate before drilling to ensure compatibility with the drilling process
Implementing Quality Control Measures
Implementing quality control measures throughout the PCB manufacturing process can help to identify and address drilling defects early in the production cycle. This includes:
- Conducting regular visual inspections of drilled holes for size, position, and quality
- Utilizing automated optical inspection (AOI) systems to detect and measure drilling defects
- Implementing statistical process control (SPC) techniques to monitor and adjust the drilling process in real-time
- Conducting destructive testing on a sample of finished PCBs to verify internal hole quality and integrity
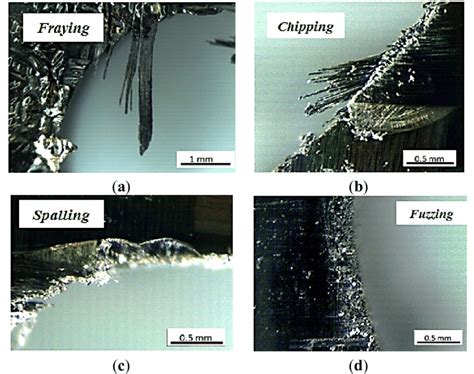
FAQ
What is the most common cause of PCB drilling defects?
Drill bit wear and damage is one of the most common causes of PCB drilling defects. As drill bits are used repeatedly, they can become dull, chipped, or otherwise damaged, leading to inaccuracies in hole size, position, and quality.
How can I determine the optimal drilling parameters for my PCB design?
Determining the optimal drilling parameters for a specific PCB design requires careful consideration of several factors, including the material properties of the substrate, the required hole size and tolerance, and the capabilities of the drilling machine. It is recommended to consult with experienced PCB manufacturers or reference industry guidelines and standards, such as IPC-6012, for guidance on selecting appropriate drilling parameters.
How often should I replace my drill bits to prevent defects?
The frequency of drill bit replacement depends on several factors, including the material being drilled, the drilling parameters used, and the quality requirements for the finished holes. As a general guideline, it is recommended to inspect drill bits for wear and damage before each use and to replace them as soon as any signs of wear or damage are observed. Some manufacturers may also recommend replacing drill bits after a certain number of hits or drilling cycles, based on their specific experience and quality control standards.
Can PCB drilling defects be repaired after the fact?
In some cases, minor drilling defects, such as slightly oversized or undersized holes, can be repaired through secondary operations, such as reaming or plating. However, more severe defects, such as misaligned or missing holes, may require scrapping the affected PCBs and starting over with a new production run. The feasibility and cost-effectiveness of repairing drilling defects will depend on the specific nature and extent of the defects, as well as the quality requirements and production deadlines for the finished product.
What are some best practices for preventing PCB drilling defects in my manufacturing process?
To prevent PCB drilling defects in your manufacturing process, consider implementing the following best practices:
- Select appropriate drill bits for the specific PCB design and material, and maintain them regularly to ensure optimal performance.
- Optimize drilling parameters, such as spindle speed, feed rate, and depth of cut, based on the specific requirements of the PCB design and the capabilities of the drilling machine.
- Implement proper machine calibration and maintenance procedures, including regular inspections, adjustments, and preventive maintenance.
- Ensure proper handling and storage of PCB substrates to maintain consistent material properties and prevent physical damage.
- Implement quality control measures, such as visual inspections, automated optical inspection, and statistical process control, to identify and address drilling defects early in the production cycle.
By adhering to these best practices and continually monitoring and improving your PCB manufacturing process, you can minimize the occurrence of drilling defects and ensure the highest quality and reliability of your finished products.
Conclusion
PCB drilling defects can have significant impacts on the functionality, reliability, and cost of electronic products. By understanding the common types and causes of these defects, as well as implementing appropriate prevention and elimination methods, PCB manufacturers can minimize the occurrence of drilling defects and ensure the highest quality of their finished products.
Some key strategies for preventing and eliminating PCB drilling defects include:
- Proper selection and maintenance of drill bits
- Optimization of drilling parameters
- Regular calibration and maintenance of drilling machines
- Proper handling and storage of PCB substrates
- Implementation of quality control measures throughout the manufacturing process
By adopting these best practices and continually monitoring and improving their processes, PCB manufacturers can deliver high-quality, reliable products to their customers while minimizing waste, rework, and production delays.
As the electronics industry continues to evolve and demand ever-higher levels of performance and miniaturization, the importance of effective PCB drilling defect prevention and elimination will only continue to grow. By staying up-to-date with the latest technologies, standards, and best practices in PCB manufacturing, and by fostering a culture of continuous improvement and quality control, manufacturers can position themselves for success in this challenging and dynamic industry.
No responses yet