What is a PCB?
A Printed Circuit Board (PCB) is a fundamental component in modern electronics. It is a flat board made of insulating materials, such as fiberglass or composite epoxy, with conductive pathways etched or printed onto its surface. These pathways, also known as traces, connect various electronic components, such as resistors, capacitors, and integrated circuits, to create a functional electronic device.
PCBs have revolutionized the electronics industry by providing a reliable and efficient means of connecting electronic components. They have replaced the old method of point-to-point wiring, which was time-consuming, error-prone, and resulted in bulky devices. With PCBs, electronic devices have become more compact, reliable, and easier to mass-produce.
Types of PCBs
There are several types of PCBs, each designed to meet specific requirements and applications. The most common types include:
1. Single-sided PCBs
Single-sided PCBs have conductive traces on only one side of the board. They are the simplest and most cost-effective type of PCB, suitable for basic electronic projects and low-density designs.
2. Double-sided PCBs
Double-sided PCBs have conductive traces on both sides of the board, allowing for more complex designs and higher component density. The two sides are connected using through-hole technology, where holes are drilled through the board and plated with conductive material.
3. Multi-layer PCBs
Multi-layer PCBs consist of three or more conductive layers separated by insulating layers. They offer the highest component density and are used in complex electronic devices, such as smartphones, computers, and medical equipment. The layers are connected using vias, which are small holes drilled through the board and plated with conductive material.
4. Flexible PCBs
Flexible PCBs are made of thin, flexible materials, such as polyimide or PEEK. They can bend and twist without damaging the conductive traces, making them ideal for applications that require flexibility, such as wearable electronics and automotive systems.
5. Rigid-Flex PCBs
Rigid-Flex PCBs combine the benefits of rigid and flexible PCBs. They consist of rigid sections connected by flexible sections, allowing for three-dimensional designs and improved reliability in applications that require both stability and flexibility.
PCB Type | Layers | Density | Flexibility | Typical Applications |
---|---|---|---|---|
Single-sided | 1 | Low | No | Basic electronic projects |
Double-sided | 2 | Medium | No | More complex designs |
Multi-layer | 3+ | High | No | Complex electronic devices |
Flexible | 1-2 | Low-Medium | Yes | Wearable electronics, automotive systems |
Rigid-Flex | 3+ | High | Partial | 3D designs, high-reliability applications |
PCB Manufacturing Process
The PCB manufacturing process involves several steps, each critical to ensuring the quality and functionality of the final product. The main steps include:
1. Design
The PCB design process begins with creating a schematic diagram that shows the interconnections between electronic components. This schematic is then translated into a physical layout using PCB design software, such as Altium Designer or KiCad. The layout specifies the position of components, the routing of traces, and the placement of vias.
2. Printing
Once the design is finalized, the PCB layout is printed onto a photosensitive film or directly onto the PCB substrate using a plotter or laser printer. This process creates a photomask that will be used in the next step.
3. Etching
The printed PCB substrate is then coated with a layer of photoresist, a light-sensitive material that hardens when exposed to UV light. The photomask is placed on top of the photoresist, and the board is exposed to UV light. The areas of the photoresist not covered by the photomask harden, while the exposed areas remain soluble.
The board is then placed in a chemical bath that removes the soluble photoresist, exposing the unwanted copper. The exposed copper is etched away using an acidic solution, leaving only the desired conductive traces.
4. Drilling
After etching, holes are drilled through the board to accommodate through-hole components and vias. The drilling process is typically done using computer-controlled drill machines to ensure precision and accuracy.
5. Plating
The drilled holes are then plated with a conductive material, usually copper, to create electrical connections between layers. This process is called through-hole plating or via plating.
6. Solder Mask and Silkscreen
A solder mask, a thin layer of polymer, is applied to the PCB surface to protect the conductive traces from oxidation and prevent solder bridging. The solder mask also provides electrical insulation between adjacent traces.
A silkscreen layer is then added to the PCB surface to label components, provide assembly instructions, and display the company logo or other information. The silkscreen is typically printed using white ink.
7. Surface Finish
The exposed copper on the PCB surface is coated with a protective layer to prevent oxidation and improve solderability. Common surface finishes include:
- HASL (Hot Air Solder Leveling): A thin layer of solder is applied to the copper surface.
- ENIG (Electroless Nickel Immersion Gold): A layer of nickel is deposited on the copper, followed by a thin layer of gold.
- OSP (Organic Solderability Preservative): A thin, organic coating is applied to the copper surface.
8. Testing and Inspection
Finally, the manufactured PCBs undergo rigorous testing and inspection to ensure they meet the required quality standards. This includes visual inspection, electrical testing, and functional testing.
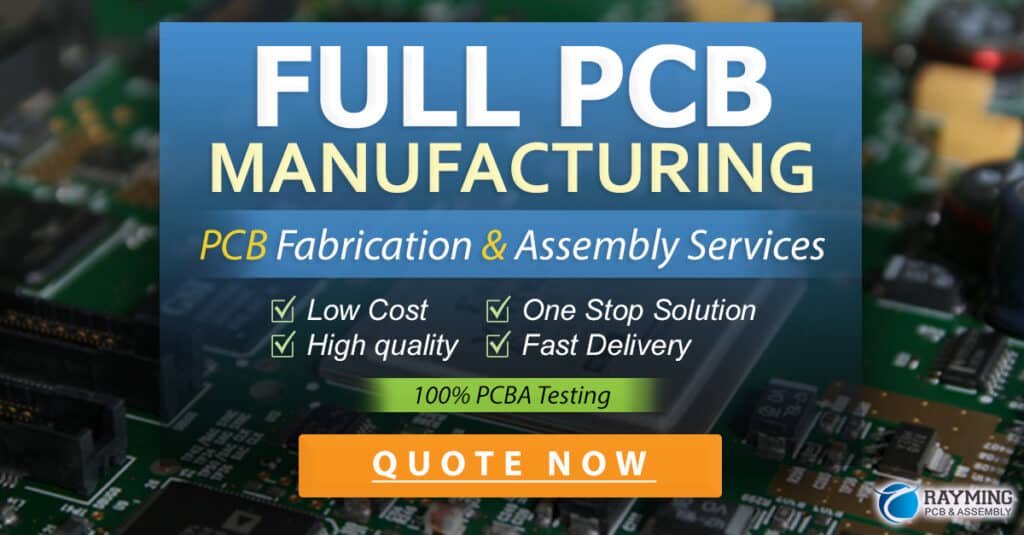
Advantages of Using PCBs
PCBs offer several advantages over traditional point-to-point wiring:
-
Reliability: PCBs provide a stable and reliable means of connecting electronic components, reducing the risk of loose connections and short circuits.
-
Consistency: PCBs ensure consistent performance across multiple devices, as the manufacturing process is highly automated and standardized.
-
Compact size: PCBs allow for the creation of compact and lightweight electronic devices, as components can be placed close together and routed efficiently.
-
Cost-effective: PCBs are cost-effective for mass production, as the manufacturing process can be automated and optimized for high volumes.
-
Design flexibility: PCBs offer design flexibility, allowing for the creation of complex circuits and three-dimensional structures.
Choosing a PCB Manufacturer
When selecting a PCB manufacturer, consider the following factors:
-
Quality: Choose a manufacturer that adheres to strict quality control standards and has a proven track record of producing high-quality PCBs.
-
Capabilities: Ensure the manufacturer has the necessary capabilities to produce your specific PCB design, including the required layer count, material, and surface finish.
-
Turnaround time: Consider the manufacturer’s turnaround time, especially if you have tight deadlines or require quick prototyping.
-
Customer support: Select a manufacturer that offers excellent customer support, including responsive communication and technical assistance.
-
Pricing: Compare pricing from multiple manufacturers, but don’t sacrifice quality for cost savings.
FAQ
1. What is the typical turnaround time for PCB manufacturing?
The turnaround time for PCB manufacturing varies depending on the complexity of the design, the volume of the order, and the manufacturer’s capabilities. Typical turnaround times range from 24 hours for quick-turn prototyping to several weeks for large-volume production.
2. What is the minimum order quantity for PCBs?
The minimum order quantity (MOQ) for PCBs varies between manufacturers. Some manufacturers offer low MOQs for prototyping, while others require higher volumes for production runs. It’s essential to discuss your specific requirements with the manufacturer to determine their MOQ.
3. What file formats are required for PCB manufacturing?
PCB manufacturers typically require Gerber files, which are standard file formats used in the PCB industry. Gerber files contain the necessary information for each layer of the PCB, including the conductive traces, solder mask, and silkscreen. Some manufacturers may also accept other file formats, such as ODB++ or IPC-2581.
4. How can I ensure the quality of my PCBs?
To ensure the quality of your PCBs, work with a reputable manufacturer that follows strict quality control standards. Provide clear and accurate design files, and communicate your requirements effectively. Consider requesting a design for manufacturability (DFM) analysis to identify potential issues before production begins.
5. What is the difference between PCB Prototyping and production?
PCB prototyping involves creating a small number of boards for testing and validation purposes. Prototyping allows you to verify your design and make necessary changes before committing to full-scale production. PCB production, on the other hand, involves manufacturing a larger volume of boards for commercial use. Production runs typically offer lower per-unit costs but require higher initial setup costs and longer lead times.
Conclusion
PCBs have become an essential component in modern electronics, offering reliability, consistency, and design flexibility. Understanding the different types of PCBs, the manufacturing process, and the factors to consider when choosing a PCB manufacturer is crucial for anyone involved in electronics design and production.
When selecting a PCB manufacturer, prioritize quality, capabilities, turnaround time, customer support, and pricing. By working with a reputable manufacturer and following best practices in PCB design, you can ensure the success of your electronic projects.
As technology continues to evolve, the demand for advanced PCBs will only grow. Staying informed about the latest developments in PCB manufacturing and design will help you stay competitive in the ever-changing world of electronics.
No responses yet