Why is PCB Insulation Important?
PCB insulation serves several critical functions in the design and operation of electronic circuits:
-
Electrical Isolation: Insulation prevents unwanted electrical contact between conductive layers, traces, and components, ensuring proper circuit functionality and preventing short circuits.
-
Signal Integrity: Proper insulation helps maintain signal integrity by reducing crosstalk, electromagnetic interference (EMI), and other forms of signal distortion that can degrade device performance.
-
Heat Dissipation: Some insulation materials, such as thermally conductive dielectrics, help dissipate heat generated by components, preventing thermal damage and improving overall device reliability.
-
Mechanical Support: Insulation materials provide mechanical support to the PCB Structure, enhancing its durability and resistance to physical stress and vibration.
Types of PCB Insulation Materials
Several materials are commonly used for PCB insulation, each with its own unique properties and advantages:
FR-4
FR-4 (Flame Retardant 4) is the most widely used PCB insulation material. It is a composite material made of woven fiberglass cloth impregnated with an epoxy resin binder. FR-4 offers excellent electrical insulation, mechanical strength, and thermal stability, making it suitable for a wide range of applications.
Property | Value |
---|---|
Dielectric Constant (1 MHz) | 4.5 – 4.7 |
Dielectric Strength | 55 – 65 kV/mm |
Thermal Conductivity | 0.3 – 0.4 W/m·K |
Glass Transition Temperature | 135 – 145 °C |
Flexural Strength | 415 – 450 MPa |
Polyimide
Polyimide is a high-performance polymer known for its exceptional thermal stability, chemical resistance, and mechanical strength. It is often used in applications that require operation at high temperatures or exposure to harsh environments, such as aerospace and military electronics.
Property | Value |
---|---|
Dielectric Constant (1 MHz) | 3.5 – 3.8 |
Dielectric Strength | 200 – 300 kV/mm |
Thermal Conductivity | 0.2 – 0.3 W/m·K |
Glass Transition Temperature | 360 – 410 °C |
Tensile Strength | 150 – 250 MPa |
PTFE (Teflon)
PTFE (Polytetrafluoroethylene), also known as Teflon, is a fluoropolymer with excellent dielectric properties, low dielectric loss, and high thermal stability. It is often used in high-frequency applications, such as RF and microwave circuits, due to its low dissipation factor and stable dielectric constant.
Property | Value |
---|---|
Dielectric Constant (1 MHz) | 2.0 – 2.1 |
Dielectric Strength | 60 – 170 kV/mm |
Thermal Conductivity | 0.2 – 0.3 W/m·K |
Melting Point | 327 °C |
Tensile Strength | 20 – 35 MPa |
PCB Insulation Techniques
Several techniques are employed to achieve proper insulation in PCB manufacturing:
Lamination
Lamination is the process of bonding the insulation material to the conductive layers of the PCB using heat and pressure. This creates a solid, multilayer structure with insulation between the conductive layers. The choice of lamination parameters, such as temperature, pressure, and duration, depends on the specific insulation material and PCB design requirements.
Solder Mask
Solder mask is a thin, protective coating applied to the PCB surface to insulate the copper traces and pads from accidental contact with other components or conductive materials. It also helps prevent solder bridging during the assembly process. Solder mask is typically applied using screen printing or photoimaging techniques and can be found in various colors, with green being the most common.
Conformal Coating
Conformal coating is a protective layer applied to the assembled PCB to provide additional insulation, moisture resistance, and environmental protection. Common conformal coating materials include acrylic, silicone, urethane, and parylene. The choice of material depends on the specific application requirements, such as temperature range, chemical exposure, and mechanical stress.
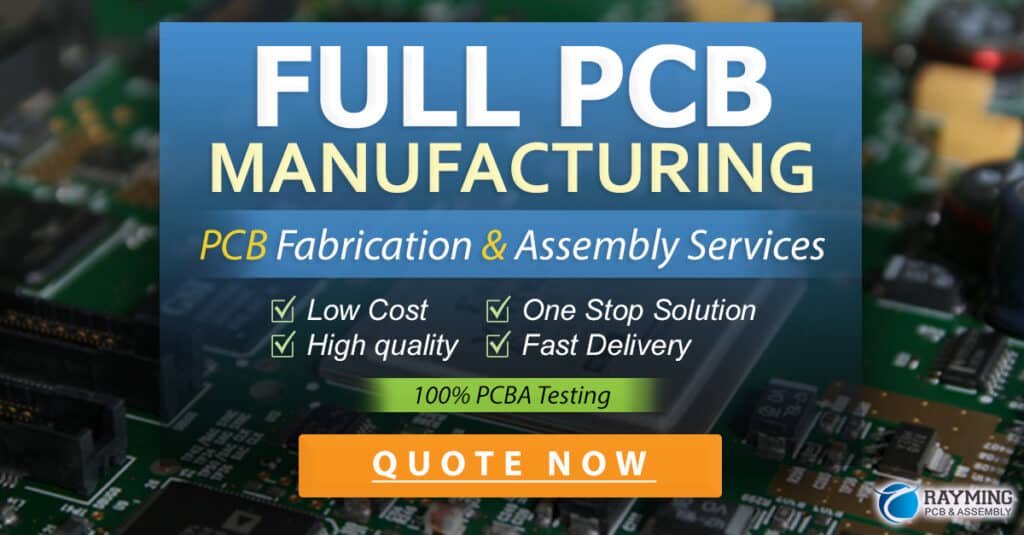
Best Practices for PCB Insulation
To ensure optimal insulation performance in PCB manufacturing, consider the following best practices:
-
Material Selection: Choose the appropriate insulation material based on the specific application requirements, such as temperature range, dielectric properties, and mechanical strength.
-
Design for Manufacturability: Incorporate design features that facilitate proper insulation, such as adequate spacing between conductive layers, proper trace width and spacing, and the use of vias for interlayer connections.
-
Process Control: Implement strict process controls during PCB manufacturing to ensure consistent insulation quality, such as monitoring lamination parameters, controlling solder mask application, and inspecting for defects.
-
Testing and Validation: Perform thorough testing and validation of the insulated PCB to verify its electrical, thermal, and mechanical properties meet the design specifications and industry standards.
-
Continuous Improvement: Regularly review and update PCB insulation processes and materials to incorporate new technologies, improve performance, and address evolving application requirements.
Frequently Asked Questions (FAQ)
- What is the most common PCB insulation material?
-
FR-4 is the most widely used PCB insulation material due to its excellent electrical, mechanical, and thermal properties, as well as its cost-effectiveness.
-
Can PCB insulation materials be mixed in a single board?
-
Yes, different insulation materials can be used in a single PCB, depending on the specific requirements of different sections of the board. For example, a high-frequency section may use PTFE for its superior dielectric properties, while the rest of the board uses FR-4.
-
How does PCB insulation affect signal integrity?
-
Proper PCB insulation helps maintain signal integrity by reducing crosstalk, EMI, and other forms of signal distortion. The choice of insulation material, thickness, and layout design all contribute to minimizing signal degradation.
-
What are the challenges in PCB insulation for high-temperature applications?
-
High-temperature applications require insulation materials with high thermal stability, such as polyimide or high-temperature FR-4 variants. The main challenges include maintaining dielectric properties, preventing thermal expansion mismatches, and ensuring reliable interlayer adhesion at elevated temperatures.
-
How can PCB designers ensure proper insulation in their designs?
- PCB designers can ensure proper insulation by following best practices such as selecting appropriate insulation materials, incorporating design features that facilitate insulation (e.g., adequate spacing, proper trace sizing), and adhering to industry standards and guidelines for PCB design and manufacturing.
In conclusion, PCB insulation is a critical aspect of PCB production that ensures proper electrical isolation, signal integrity, thermal management, and mechanical stability in electronic devices. By understanding the various insulation materials, techniques, and best practices, PCB manufacturers and designers can optimize insulation performance and create high-quality, reliable products that meet the evolving demands of modern electronics.
No responses yet