What are PCB Adhesives?
PCB adhesives are specialized materials used to bond components to the surface of a printed circuit board. These adhesives provide mechanical stability, protect against vibration and shock, and help dissipate heat from components. PCB adhesives come in various formulations, each with unique properties suited for specific applications.
Key Applications of PCB Adhesives
Surface Mount Technology (SMT)
Surface Mount Technology (SMT) is a method of mounting components directly onto the surface of a PCB. SMT has largely replaced through-hole technology in modern electronics manufacturing due to its numerous advantages, such as:
- Increased component density
- Improved performance
- Reduced board size
- Faster assembly processes
PCB adhesives play a crucial role in SMT by securely bonding components to the board surface. The adhesive must be carefully selected based on the component type, board material, and environmental factors to ensure optimal performance and reliability.
Potting and Encapsulation
Potting and encapsulation involve filling a complete electronic assembly or specific components with a protective material, such as epoxy or silicone. This process offers several benefits:
- Protection against moisture, dust, and other environmental contaminants
- Improved mechanical stability
- Enhanced thermal dissipation
- Increased electrical insulation
PCB adhesives used for potting and encapsulation must have excellent flow properties to fill all voids and cavities, while also providing strong adhesion to the components and PCB surface.
Conformal Coating
Conformal coating is a thin protective layer applied to a PCB assembly to shield it from environmental factors such as moisture, dust, chemicals, and extreme temperatures. Common conformal coating materials include:
- Acrylic
- Silicone
- Polyurethane
- Epoxy
- Parylene
PCB adhesives used in conjunction with conformal coatings must be compatible with the chosen coating material to ensure proper adhesion and long-term protection.
Strain Relief
Strain relief is a method of reducing mechanical stress on electrical connections, such as wires or cables, where they join a PCB. Proper strain relief prevents damage to the connections caused by pulling, twisting, or bending forces. PCB adhesives can be used to provide strain relief by securely bonding wires or cables to the board, minimizing the risk of connection failure due to mechanical stress.
Types of PCB Adhesives
PCB adhesives come in various formulations, each with unique properties and advantages. The most common types of PCB adhesives are:
Epoxy Adhesives
Epoxy adhesives are widely used in electronics manufacturing due to their excellent mechanical strength, chemical resistance, and thermal stability. They consist of two components: a resin and a hardener, which are mixed prior to application. Epoxy adhesives offer several advantages:
- Strong adhesion to various substrates
- High temperature resistance
- Excellent electrical insulation
- Good gap-filling properties
However, epoxy adhesives typically have longer curing times compared to other adhesive types and may require elevated temperatures for optimal curing.
Silicone Adhesives
Silicone adhesives are known for their flexibility, high temperature resistance, and excellent electrical insulation properties. They are often used in applications where the PCB assembly is exposed to thermal cycling or extreme temperatures. Silicone adhesives offer several benefits:
- Excellent thermal stability
- Good vibration and shock resistance
- High dielectric strength
- Resistance to moisture and chemicals
Silicone adhesives are available in both one-part and two-part formulations, with varying cure mechanisms such as moisture, heat, or UV light.
Acrylic Adhesives
Acrylic adhesives are fast-curing, flexible, and offer good adhesion to a wide range of substrates. They are often used in applications where quick assembly times are required. Acrylic adhesives provide several advantages:
- Fast curing at room temperature
- Good impact and vibration resistance
- Excellent environmental resistance
- Clear and colorless appearance
Acrylic adhesives are available in both solvent-based and water-based formulations, as well as one-part and two-part systems.
Polyurethane Adhesives
Polyurethane adhesives offer a combination of strength, flexibility, and durability. They are known for their excellent adhesion to various substrates and resistance to harsh environmental conditions. Polyurethane adhesives provide several benefits:
- High tensile and shear strength
- Good flexibility and impact resistance
- Resistance to moisture, chemicals, and abrasion
- Wide temperature range
Polyurethane adhesives are available in both one-part and two-part formulations, with varying cure mechanisms such as moisture or heat.
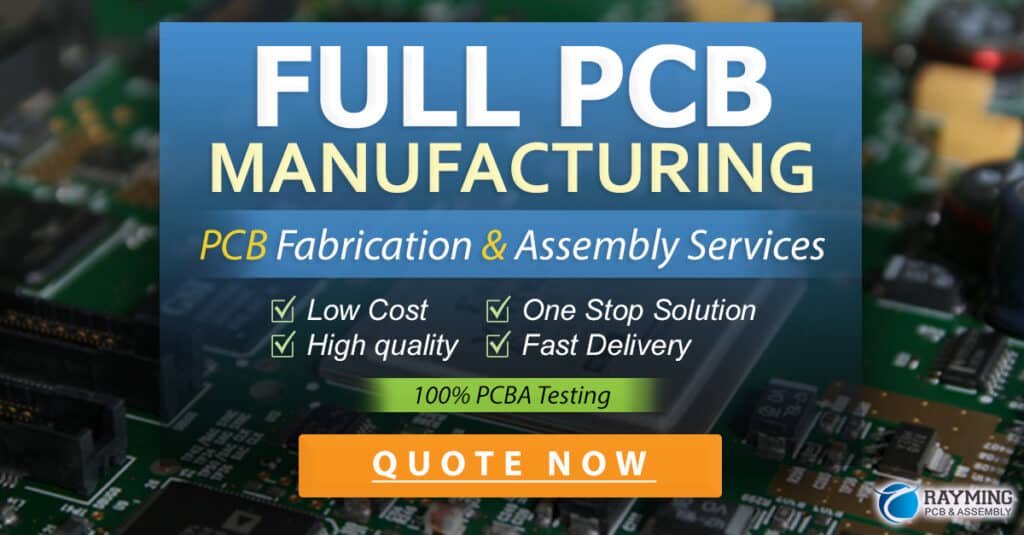
Choosing the Right PCB Adhesive
Selecting the appropriate PCB adhesive depends on several factors, including:
- Substrate materials (PCB and components)
- Environmental conditions (temperature, humidity, chemicals)
- Required mechanical properties (strength, flexibility, impact resistance)
- Electrical properties (insulation, dielectric strength)
- Processing requirements (cure time, temperature, dispensing method)
To ensure optimal performance and reliability, it is essential to work with experienced adhesive manufacturers and conduct thorough testing to validate the chosen adhesive for your specific application.
PCB Adhesive Application Methods
PCB adhesives can be applied using various methods, depending on the adhesive type, viscosity, and production requirements. Common application methods include:
- Manual dispensing (e.g., syringes, cartridges)
- Automated dispensing (e.g., needle dispensers, jetting systems)
- Screen printing
- Stencil printing
- Dip coating
- Brush coating
Choosing the appropriate application method ensures consistent adhesive coverage, minimal waste, and efficient processing.
Curing PCB Adhesives
After application, PCB adhesives must be cured to achieve their final mechanical, electrical, and thermal properties. The curing process varies depending on the adhesive type and formulation. Common curing methods include:
- Room temperature curing
- Heat curing (convection, infrared, or hot air)
- UV curing
- Moisture curing
The curing method and parameters (time, temperature, humidity) must be carefully controlled to ensure optimal adhesive performance and avoid potential issues such as incomplete curing, voids, or excessive shrinkage.
Frequently Asked Questions (FAQ)
1. What is the difference between a one-part and two-part PCB adhesive?
One-part PCB adhesives are pre-mixed and ready to use, typically curing through exposure to heat, moisture, or UV light. Two-part adhesives consist of a resin and a hardener that must be mixed in a specific ratio before application. Two-part adhesives often offer better mechanical properties and resistance to harsh environments but require more preparation and have shorter working times.
2. How do I select the right PCB adhesive for my application?
To select the right PCB adhesive, consider the following factors:
– Substrate materials and their compatibility with the adhesive
– Required mechanical, electrical, and thermal properties
– Environmental conditions (temperature, humidity, chemicals)
– Processing requirements (cure time, temperature, dispensing method)
– Cost and availability
Consult with adhesive manufacturers and conduct thorough testing to validate the chosen adhesive for your specific application.
3. Can PCB adhesives be reworked or removed?
Some PCB adhesives, particularly those with lower temperature resistance, can be reworked or removed using heat or solvents. However, rework and removal processes can be challenging and may damage the PCB or components. It is essential to consider the potential need for rework during the adhesive selection process and choose an adhesive that facilitates rework if necessary.
4. How do I store PCB adhesives, and what is their shelf life?
PCB adhesives should be stored in a cool, dry place, away from direct sunlight and sources of heat or moisture. The shelf life of PCB adhesives varies depending on the type and formulation but is typically between 6 months to 1 year when stored under proper conditions. Always refer to the manufacturer’s storage and handling guidelines to ensure optimal adhesive performance.
5. Are there any health and safety concerns when working with PCB adhesives?
Some PCB adhesives may contain volatile organic compounds (VOCs) or other chemicals that can be harmful if inhaled or come into contact with skin or eyes. Always review the safety data sheet (SDS) provided by the manufacturer and follow proper handling, ventilation, and personal protective equipment (PPE) guidelines to minimize health and safety risks.
Conclusion
PCB adhesives play a critical role in the assembly and reliability of modern electronic devices. Understanding the key applications and types of PCB adhesives is essential for selecting the appropriate adhesive for your specific requirements. By considering factors such as substrate compatibility, environmental conditions, and processing requirements, you can ensure optimal performance and reliability in your PCB assemblies.
As electronics continue to evolve, so will the demand for advanced PCB adhesives that can withstand increasingly challenging conditions. Staying informed about the latest developments in PCB adhesive technology and working closely with experienced manufacturers will help you stay ahead of the curve in this dynamic industry.
PCB Adhesive Type | Key Characteristics | Typical Applications |
---|---|---|
Epoxy | – Strong mechanical properties – High temperature resistance – Excellent chemical resistance |
– Surface mount technology (SMT) – Potting and encapsulation – High-reliability applications |
Silicone | – High flexibility – Excellent thermal stability – Good electrical insulation |
– Applications with thermal cycling – High-temperature environments – Vibration and shock-resistant assemblies |
Acrylic | – Fast curing at room temperature – Good impact and vibration resistance – Clear and colorless appearance |
– Quick assembly processes – Applications requiring environmental resistance – Bonding clear or translucent components |
Polyurethane | – High tensile and shear strength – Good flexibility and impact resistance – Wide temperature range |
– Applications requiring a combination of strength and flexibility – Harsh environmental conditions – Bonding dissimilar materials |
No responses yet