Introduction to PCB Quality
Printed Circuit Boards (PCBs) are the backbone of modern electronics. They are used in almost every electronic device, from smartphones and computers to medical equipment and aerospace systems. The quality of a PCB is critical to the performance, reliability, and longevity of the device it powers. Poor quality PCBs can lead to device failures, safety hazards, and costly repairs or replacements.
PCB quality is determined by several factors, including the design, materials, manufacturing processes, and testing. To ensure good quality, PCBs must undergo rigorous testing and inspection at various stages of the manufacturing process. One of the most important aspects of PCB quality assurance is failure analysis.
What is PCB Failure Analysis?
PCB failure analysis is the process of examining a failed PCB to determine the root cause of the failure. It involves a series of tests and inspections to identify the specific component, connection, or design flaw that led to the failure. The goal of failure analysis is to prevent similar failures from occurring in the future by identifying and correcting the underlying issue.
There are several types of PCB failures that can occur, including:
- Short circuits
- Open circuits
- Component failures
- Solder joint failures
- Delamination
- Contamination
Each type of failure requires a different approach to analysis and correction.
Short Circuits
Short circuits occur when two or more conductors that should not be connected come into contact with each other. This can happen due to a manufacturing defect, such as a solder bridge, or due to damage to the PCB during handling or use. Short circuits can cause the device to malfunction or fail completely.
To identify a short circuit, a technician will typically use a multimeter or oscilloscope to measure the resistance between the affected conductors. If the resistance is lower than expected, it indicates a short circuit. The technician can then visually inspect the PCB to locate the specific area where the short is occurring.
Open Circuits
Open circuits occur when a connection that should be present is broken or missing. This can happen due to a manufacturing defect, such as a missing or damaged trace, or due to damage to the PCB during handling or use. Open circuits can cause the device to malfunction or fail completely.
To identify an open circuit, a technician will typically use a multimeter or oscilloscope to measure the resistance between the affected conductors. If the resistance is higher than expected or infinite, it indicates an open circuit. The technician can then visually inspect the PCB to locate the specific area where the open is occurring.
Component Failures
Component failures occur when an individual component on the PCB fails to function properly. This can happen due to a manufacturing defect, such as a faulty component or incorrect installation, or due to damage or wear during use. Component failures can cause the device to malfunction or fail completely.
To identify a component failure, a technician will typically use a variety of tools and techniques, including:
- Visual inspection
- Multimeter testing
- Oscilloscope testing
- Thermal imaging
- X-ray inspection
The specific technique used will depend on the type of component and the nature of the failure.
Solder Joint Failures
Solder joint failures occur when the connection between a component and the PCB is weak or broken. This can happen due to a manufacturing defect, such as insufficient solder or incorrect temperature, or due to damage or wear during use. Solder joint failures can cause intermittent or complete device failure.
To identify a solder joint failure, a technician will typically use visual inspection and x-ray imaging. Visual inspection can reveal cracks, voids, or other defects in the solder joint. X-ray imaging can provide a more detailed view of the internal structure of the joint and reveal defects that may not be visible on the surface.
Delamination
Delamination occurs when the layers of the PCB separate from each other. This can happen due to a manufacturing defect, such as improper lamination or contamination, or due to exposure to extreme temperatures or moisture. Delamination can cause the PCB to warp or crack, leading to device failure.
To identify delamination, a technician will typically use visual inspection and cross-sectioning. Visual inspection can reveal surface defects such as blistering or discoloration. Cross-sectioning involves cutting the PCB into thin slices and examining the internal structure under a microscope to identify areas of separation.
Contamination
Contamination occurs when foreign substances, such as dirt, dust, or chemicals, are present on the PCB. This can happen due to improper handling or storage, or due to exposure to harsh environments. Contamination can cause short circuits, corrosion, or other types of damage to the PCB.
To identify contamination, a technician will typically use visual inspection and chemical analysis. Visual inspection can reveal visible contaminants on the surface of the PCB. Chemical analysis can identify the specific type of contaminant and its potential impact on the PCB.
The Importance of PCB Failure Analysis
PCB failure analysis is essential for ensuring the quality and reliability of electronic devices. By identifying the root cause of failures, manufacturers can take steps to prevent similar issues from occurring in the future. This can include:
- Improving the design of the PCB
- Changing the materials or components used
- Modifying the manufacturing process
- Implementing additional testing and inspection procedures
Failure analysis can also help manufacturers to identify and address potential safety hazards before they cause harm to users. For example, if a PCB failure could lead to a fire or electrical shock, failure analysis can help to identify and correct the issue before it becomes a serious problem.
In addition to improving quality and safety, failure analysis can also help manufacturers to reduce costs associated with warranty claims and product recalls. By identifying and correcting issues early in the manufacturing process, manufacturers can avoid the expense of replacing or repairing defective products in the field.
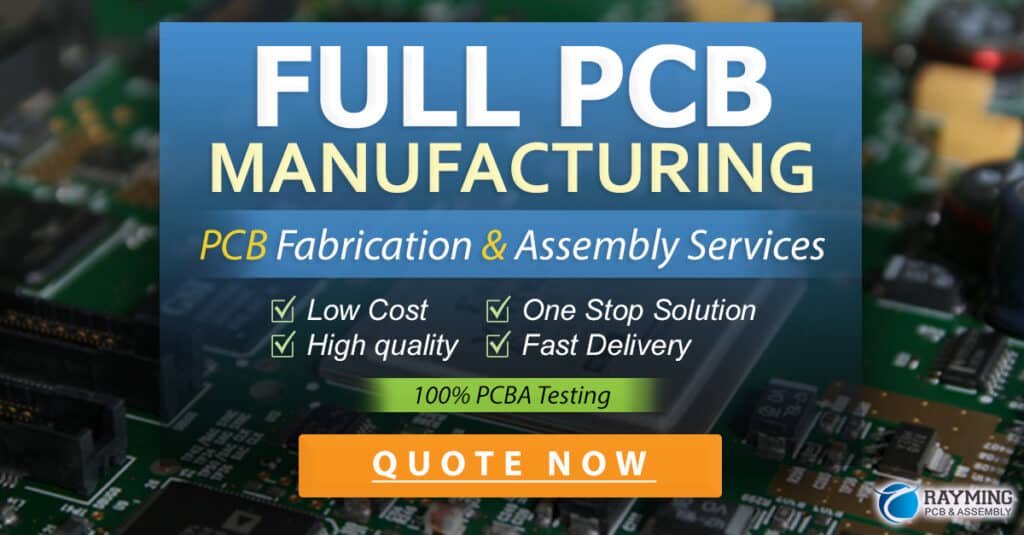
The PCB Failure Analysis Process
The PCB failure analysis process typically involves several stages, including:
-
Identification: The first step in failure analysis is to identify the specific PCB that has failed and the nature of the failure. This may involve collecting information from the customer or end-user about the symptoms of the failure and the conditions under which it occurred.
-
Visual Inspection: The next step is to visually inspect the PCB for any obvious defects or damage. This may involve using a magnifying glass, microscope, or other visual inspection tools to examine the surface of the PCB and its components.
-
Electrical Testing: After visual inspection, the technician will typically perform electrical tests to identify any short circuits, open circuits, or other electrical faults. This may involve using a multimeter, oscilloscope, or other testing equipment to measure resistance, voltage, and other electrical properties.
-
Destructive Testing: In some cases, destructive testing may be necessary to identify the root cause of the failure. This may involve cutting or cross-sectioning the PCB to examine its internal structure, or removing and testing individual components.
-
Analysis: Once all the necessary data has been collected, the technician will analyze the results to determine the root cause of the failure. This may involve comparing the data to known good samples, consulting with other experts, or using specialized software tools to identify patterns or trends.
-
Reporting: Finally, the technician will prepare a report summarizing the findings of the failure analysis and providing recommendations for corrective action. This report will typically include a detailed description of the failure, the testing methods used, and the root cause of the failure, as well as any recommended changes to the design, materials, or manufacturing process.
PCB Quality Testing Tools
There are several tools and techniques used in PCB failure analysis and quality testing, including:
Tool | Description |
---|---|
Multimeter | A device used to measure resistance, voltage, and current. Used to identify short circuits, open circuits, and other electrical faults. |
Oscilloscope | A device used to display and analyze waveforms. Used to identify issues such as signal integrity and timing problems. |
X-ray Imaging | A technique used to examine the internal structure of a PCB without destroying it. Used to identify defects such as voids, cracks, and solder joint failures. |
Thermal Imaging | A technique used to identify areas of the PCB that are generating excessive heat. Used to identify component failures and other heat-related issues. |
Microscopy | A technique used to examine the surface of the PCB and its components at high magnification. Used to identify defects such as contamination, corrosion, and solder joint failures. |
Cross-Sectioning | A destructive technique used to examine the internal structure of the PCB by cutting it into thin slices. Used to identify defects such as delamination and internal cracks. |
By using a combination of these tools and techniques, technicians can identify a wide range of PCB failures and quality issues.
The Benefits of Working with a Professional PCB Failure Analysis Service
While some manufacturers may have the capability to perform PCB failure analysis in-house, there are several benefits to working with a professional failure analysis service, including:
-
Expertise: Professional failure analysis services have teams of experienced technicians and engineers who specialize in identifying and correcting PCB failures. They have access to the latest tools and techniques and can quickly identify even the most complex issues.
-
Objectivity: In-house failure analysis teams may be biased towards certain design or manufacturing practices, which can lead to missed opportunities for improvement. Professional services provide an objective, third-party perspective that can help identify areas for improvement that may be overlooked by in-house teams.
-
Speed: Professional failure analysis services typically have dedicated labs and equipment that allow them to quickly process and analyze failed PCBs. This can help manufacturers to identify and correct issues more quickly, reducing downtime and minimizing the impact of failures on production schedules.
-
Cost: While professional failure analysis services may have higher upfront costs than in-house analysis, they can often provide more comprehensive and efficient services that ultimately save manufacturers money in the long run. By identifying and correcting issues early in the manufacturing process, professional services can help to reduce warranty claims, product recalls, and other costly issues.
Conclusion
PCB failure analysis is a critical aspect of ensuring the quality and reliability of electronic devices. By identifying the root cause of failures, manufacturers can take steps to prevent similar issues from occurring in the future, improving the overall quality and safety of their products.
Whether performed in-house or by a professional service, PCB failure analysis requires specialized tools, techniques, and expertise. By investing in failure analysis and quality testing, manufacturers can reduce costs, improve customer satisfaction, and maintain a competitive edge in today’s fast-paced electronics industry.
Frequently Asked Questions (FAQ)
-
What is the most common cause of PCB failure?
The most common cause of PCB failure is manufacturing defects, such as incorrect component placement, insufficient solder, or contamination. Other common causes include design flaws, component failures, and damage during handling or use. -
How long does PCB failure analysis typically take?
The length of time required for PCB failure analysis depends on the complexity of the issue and the testing methods required. Simple failures may be identified in a matter of hours, while more complex issues may take several days or even weeks to fully analyze. -
Can PCB failure analysis be performed on any type of PCB?
Yes, PCB failure analysis can be performed on any type of PCB, including rigid, flexible, and rigid-flex designs. However, the specific tools and techniques used may vary depending on the type of PCB and the nature of the failure. -
How much does PCB failure analysis cost?
The cost of PCB failure analysis varies depending on the complexity of the issue and the testing methods required. Simple failures may cost a few hundred dollars to analyze, while more complex issues may cost several thousand dollars. Many professional failure analysis services offer fixed-price packages or hourly rates based on the specific needs of the customer. -
Can PCB failure analysis be performed on a single failed board, or are multiple samples required?
In most cases, PCB failure analysis can be performed on a single failed board. However, if the failure is intermittent or if multiple failures have occurred, analyzing multiple samples may provide more comprehensive data and help to identify patterns or trends that may not be apparent from a single sample.
No responses yet