What is PCB Practical?
PCB Practical refers to the hands-on skills and knowledge required to design, fabricate, and test printed circuit boards. It encompasses a wide range of activities, from schematic capture and board layout to component selection and soldering. A skilled PCB engineer should be proficient in using various software tools, understanding manufacturing processes, and troubleshooting issues that may arise during the development cycle.
Key Skills for PCB Practical
To become a successful PCB engineer, one must possess a combination of technical and soft skills. Some of the essential skills include:
-
Schematic Capture: The ability to create accurate and readable schematics using EDA (Electronic Design Automation) software such as Altium Designer, Eagle, or KiCad.
-
Board Layout: Proficiency in designing the physical layout of the PCB, including component placement, routing, and adherence to design rules and constraints.
-
Component Selection: Knowledge of electronic components, their specifications, and their suitability for different applications.
-
Manufacturing Processes: Understanding of various PCB manufacturing techniques, such as etching, drilling, plating, and solder mask application.
-
Soldering: Skill in hand soldering and rework, as well as familiarity with surface mount technology (SMT) and through-hole components.
-
Testing and Debugging: Ability to test and debug PCBs using oscilloscopes, multimeters, and other diagnostic tools.
-
Communication: Effective communication skills to collaborate with team members, suppliers, and clients.
PCB Design Workflow
The PCB design workflow typically involves the following stages:
-
Schematic Capture: Creating a schematic diagram that represents the electrical connections between components.
-
Board Layout: Translating the schematic into a physical layout, considering factors such as component placement, routing, and manufacturability.
-
Design Rule Check (DRC): Verifying that the board layout adheres to the design rules and constraints specified by the manufacturer.
-
Prototyping: Fabricating a prototype PCB for testing and validation.
-
Testing and Debugging: Verifying the functionality of the prototype and identifying any issues or improvements.
-
Manufacturing: Finalizing the design and sending it for mass production.
PCB Design Software
There are several popular PCB design software packages available in the market. Some of the widely used tools include:
Software | Manufacturer | Key Features |
---|---|---|
Altium Designer | Altium | Comprehensive PCB design suite |
Eagle | Autodesk | Schematic capture and board layout |
KiCad | KiCad | Open-source PCB design software |
OrCAD | Cadence | Schematic capture, simulation, and PCB layout |
PADS | Mentor | PCB design and analysis tools |
PCB Manufacturing Techniques
PCB manufacturing involves several processes that transform the design into a physical board. Some of the common manufacturing techniques include:
Etching
Etching is the process of removing unwanted copper from the PCB substrate to create the desired circuit pattern. There are two main methods of etching:
-
Subtractive Etching: In this method, a photoresist layer is applied to the copper-clad board and exposed to UV light through a photomask. The unexposed areas are then removed, and the exposed copper is etched away using a chemical solution.
-
Additive Etching: This method involves selectively depositing copper onto the substrate using techniques such as electroplating or chemical deposition.
Drilling
Drilling is the process of creating holes in the PCB for through-hole components and vias. There are two types of drilling:
-
Mechanical Drilling: This method uses a drill bit to create holes in the PCB. It is suitable for larger holes and lower quantities.
-
Laser Drilling: Laser drilling uses a high-powered laser to create precise, small-diameter holes in the PCB. It is ideal for high-density designs and microvias.
Plating
Plating is the process of depositing a thin layer of metal onto the PCB to improve conductivity, solderability, and durability. There are several types of plating:
-
Electroless Plating: This method involves depositing a thin layer of copper onto the PCB using a chemical process, without the use of an electric current.
-
Electrolytic Plating: In this method, an electric current is used to deposit a layer of copper or other metal onto the PCB.
-
Immersion Plating: This method involves dipping the PCB into a plating solution to deposit a thin layer of metal, such as gold or silver.
Solder Mask Application
Solder mask is a protective layer applied to the PCB to prevent solder from adhering to unwanted areas during the soldering process. It also provides insulation and protection against environmental factors. Solder mask is typically applied using screen printing or photoimaging techniques.
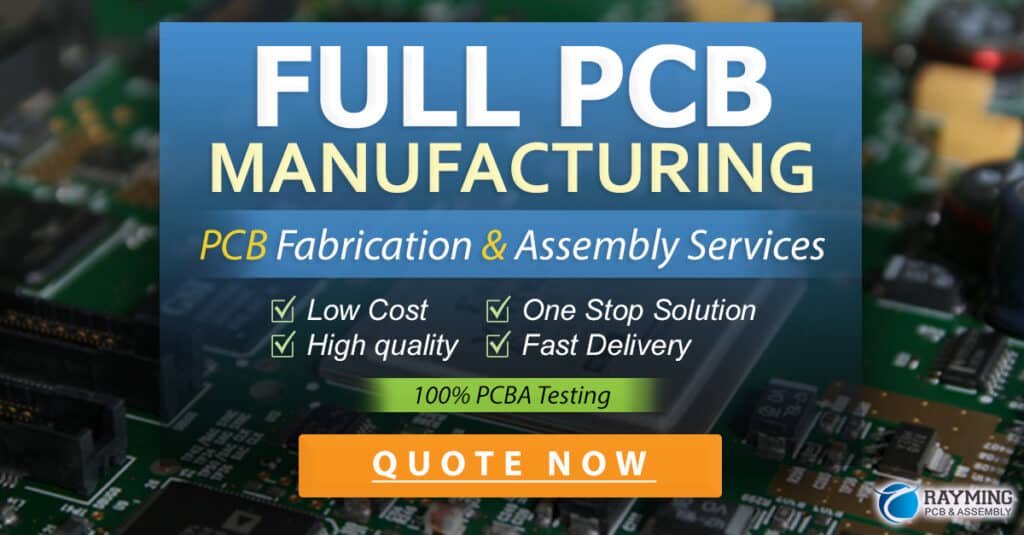
Testing and Debugging PCBs
Testing and debugging are critical steps in the PCB Development process. They help identify and resolve issues before the board goes into mass production. Some of the common testing and debugging techniques include:
-
Visual Inspection: Visually examining the PCB for any obvious defects, such as incorrect component placement, solder bridges, or damaged traces.
-
Continuity Testing: Using a multimeter to verify that the electrical connections between components are intact and there are no short circuits or open circuits.
-
Functional Testing: Powering up the PCB and verifying that it performs the intended functions correctly.
-
In-Circuit Testing (ICT): Using an automated test system to verify the functionality of individual components and circuits on the PCB.
-
Boundary Scan Testing: Utilizing JTAG (Joint Test Action Group) interface to test the interconnections between components on the PCB.
-
Thermal Imaging: Using an infrared camera to identify areas of the PCB that are generating excessive heat, which may indicate a design or component issue.
FAQ
-
What is the difference between a schematic and a PCB layout?
A schematic is a graphical representation of the electrical connections between components, while a PCB layout is the physical arrangement of those components on the board. -
What is the purpose of a via in a PCB?
A via is a conductive hole that allows electrical signals to pass from one layer of the PCB to another. Vias are used to create interconnections between different layers of the board. -
What is the role of a solder mask in PCB manufacturing?
A solder mask is a protective layer applied to the PCB that prevents solder from adhering to unwanted areas during the soldering process. It also provides insulation and protection against environmental factors. -
What is the difference between surface mount technology (SMT) and through-hole technology?
SMT components are mounted directly onto the surface of the PCB, while through-hole components have leads that are inserted into holes drilled in the board. SMT allows for smaller component sizes and higher component density compared to through-hole technology. -
What is the purpose of a design rule check (DRC) in PCB design?
A DRC is a software-based check that verifies whether the PCB layout adheres to the design rules and constraints specified by the manufacturer. It helps identify potential issues, such as insufficient clearances or trace widths, before the board goes into production.
Conclusion
PCB engineering is a vital skill in the electronics industry, and practical knowledge is essential for success in this field. A skilled PCB engineer should be proficient in schematic capture, board layout, component selection, manufacturing processes, soldering, testing, and debugging. By understanding the PCB design workflow, manufacturing techniques, and testing methods, engineers can create reliable and efficient circuit boards that power modern electronic devices.
No responses yet