Introduction to PCB Design
Printed Circuit Board (PCB) design is a crucial aspect of electronic product development. A well-designed PCB ensures the proper functioning, reliability, and manufacturability of the final product. This comprehensive guide aims to provide you with essential PCB design guidelines to help you create high-quality PCBs that meet your project requirements.
What is a PCB?
A PCB is a flat board made of insulating material, such as fiberglass or composite epoxy, with conductive copper traces printed on one or both sides. These traces connect various electronic components, such as resistors, capacitors, and Integrated Circuits (ICs), to form a functional electronic circuit.
Why are PCB Design Guidelines Important?
Following PCB design guidelines is essential for several reasons:
- Ensure proper functionality and reliability of the electronic device
- Minimize electromagnetic interference (EMI) and signal integrity issues
- Facilitate easy manufacturing and assembly processes
- Reduce the risk of design errors and costly revisions
- Improve the overall quality and performance of the final product
PCB Design Workflow
Step 1: Schematic Design
- Create a schematic diagram of the electronic circuit using EDA (Electronic Design Automation) software
- Ensure proper component selection and connections
- Perform simulation and analysis to verify the circuit’s functionality
Step 2: Component Placement
- Arrange components on the PCB Layout considering factors such as signal flow, power distribution, and mechanical constraints
- Minimize the distance between related components to reduce signal delays and noise
- Consider Component Orientation for optimal thermal management and ease of assembly
Step 3: Routing
- Route the connections between components using copper traces
- Follow routing guidelines for trace width, spacing, and length to ensure signal integrity and manufacturability
- Use appropriate layer stackup and via placement for efficient routing and signal isolation
Step 4: Design Rule Check (DRC)
- Perform DRC to ensure the PCB layout adheres to the manufacturing and assembly guidelines
- Check for potential issues such as short circuits, open circuits, and clearance violations
- Modify the layout as necessary to resolve any DRC errors
Step 5: Gerber File Generation
- Generate Gerber files, which are industry-standard files used for PCB Fabrication
- Include all necessary layers, such as copper, solder mask, and silkscreen
- Verify the Gerber files for accuracy and completeness before sending them to the PCB Manufacturer
PCB Layer Stackup
The PCB layer stackup refers to the arrangement of conductive and insulating layers in a PCB. A proper layer stackup is crucial for signal integrity, power distribution, and EMI control.
Common Layer Stackups
- Single-layer PCB: A single conductive layer on one side of the insulating substrate
- Double-layer PCB: Two conductive layers, one on each side of the insulating substrate
- Multi-layer PCB: Three or more conductive layers separated by insulating layers
Choosing the Right Layer Stackup
Consider the following factors when selecting the appropriate layer stackup for your PCB:
- Circuit complexity and density
- Signal speed and integrity requirements
- Power distribution and ground plane placement
- Manufacturing cost and lead time
Layer Stackup | Advantages | Disadvantages |
---|---|---|
Single-layer | Low cost, simple design | Limited routing space, poor EMI control |
Double-layer | Improved routing space, better EMI control | Higher cost than single-layer |
Multi-layer | Excellent signal integrity, EMI control, and power distribution | Higher cost and complexity |
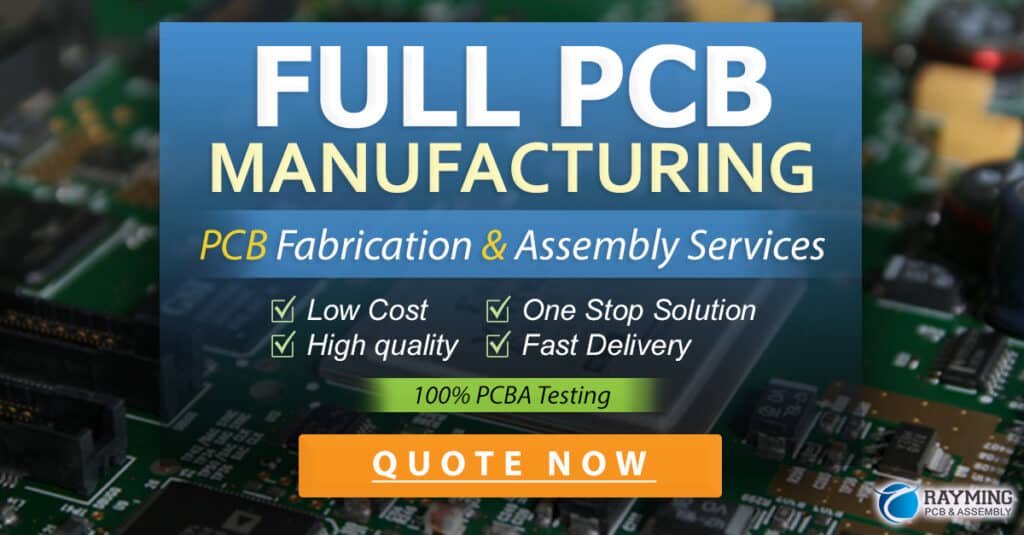
Component Placement Guidelines
Proper component placement is essential for optimal PCB performance and manufacturability. Follow these guidelines when placing components on your PCB layout:
Placement Considerations
- Signal flow: Place components in a logical sequence following the signal flow to minimize trace lengths and crossovers
- Power distribution: Position power-hungry components close to power supply pins to minimize voltage drops and noise
- Thermal management: Arrange components with high heat dissipation requirements to facilitate efficient heat transfer and cooling
- Mechanical constraints: Consider component heights, connector locations, and mounting holes when placing components
Placement Techniques
- Use a grid-based placement approach to ensure consistent spacing and alignment
- Group related components together to minimize trace lengths and improve signal integrity
- Place decoupling capacitors close to the power pins of ICs to minimize power supply noise
- Orient components for easy assembly and soldering, considering factors such as pick-and-place machines and reflow ovens
Routing Guidelines
Routing is the process of creating conductive paths (traces) between components on a PCB. Follow these guidelines to ensure proper routing and signal integrity:
Trace Width and Spacing
- Use appropriate trace widths based on the current carrying requirements and manufacturing capabilities
- Maintain adequate spacing between traces to prevent short circuits and minimize crosstalk
- Follow the PCB manufacturer’s guidelines for minimum trace width and spacing
Signal Integrity
- Route critical signals, such as high-speed and analog signals, on dedicated layers to minimize interference
- Use ground planes to provide a low-impedance return path for signals and reduce EMI
- Avoid sharp corners and use smooth curves for traces to minimize signal reflections and impedance discontinuities
Via Placement
- Place vias strategically to minimize signal path lengths and layer transitions
- Use appropriate via sizes and pad diameters based on the manufacturing capabilities and signal requirements
- Avoid placing vias in sensitive areas, such as under component pads or in high-current paths
Length Matching
- Match the lengths of related signals, such as differential pairs and clock lines, to maintain signal integrity and timing
- Use serpentine routing techniques to add controlled amounts of delay for length matching purposes
EMI and Noise Reduction Techniques
Electromagnetic Interference (EMI) and noise can adversely affect the performance and reliability of electronic devices. Implement the following techniques to minimize EMI and noise in your PCB design:
Grounding and Shielding
- Use a solid ground plane to provide a low-impedance return path for signals and reduce EMI
- Implement proper grounding techniques, such as star grounding and split ground planes, to isolate sensitive circuits
- Use shielding enclosures and conductive coatings to contain EMI and prevent external interference
Decoupling and Filtering
- Place decoupling capacitors close to the power pins of ICs to minimize power supply noise
- Use appropriate values and types of decoupling capacitors based on the frequency range and current requirements
- Implement power supply filtering techniques, such as ferrite beads and LC filters, to attenuate high-frequency noise
Layout Techniques
- Separate analog and digital circuits to minimize crosstalk and interference
- Use guard rings and ground shields to isolate sensitive signals from noise sources
- Minimize the loop area of high-current paths to reduce magnetic field coupling and EMI
PCB Manufacturing and Assembly
Consider the following factors to ensure your PCB design is compatible with manufacturing and assembly processes:
Design for Manufacturing (DFM)
- Follow the PCB manufacturer’s guidelines for minimum feature sizes, such as trace width, spacing, and hole diameters
- Use standard component footprints and package sizes to facilitate easy sourcing and assembly
- Provide adequate clearances and access for automated assembly equipment
Design for Assembly (DFA)
- Use surface mount technology (SMT) components whenever possible to simplify the assembly process
- Provide clear and legible component markings and polarity indicators on the silkscreen layer
- Include fiducial markers to assist with component placement and alignment during assembly
Panelization and Tooling
- Consider panelizing multiple PCBs on a single panel to reduce manufacturing costs and lead times
- Include tooling holes and alignment marks to facilitate accurate registration and processing during manufacturing
- Provide adequate spacing between PCBs on a panel to allow for depanelization and singulation
Frequently Asked Questions (FAQ)
1. What is the difference between a schematic and a PCB layout?
A schematic is a graphical representation of an electronic circuit, showing the components and their interconnections using standardized symbols. A PCB layout, on the other hand, is the physical representation of the circuit on a printed circuit board, where the components are placed and connected using conductive traces.
2. How do I choose the right PCB material for my project?
The choice of PCB material depends on several factors, such as the operating environment, frequency range, and cost. Common PCB materials include FR-4, which is a glass-reinforced epoxy laminate suitable for general-purpose applications, and high-frequency materials like Rogers RO4000 series for RF and microwave circuits. Consider the dielectric constant, loss tangent, and thermal properties of the material when making your selection.
3. What is the purpose of a ground plane in a PCB?
A ground plane is a large conductive layer on a PCB that serves as a low-impedance return path for signals. It helps to minimize electromagnetic interference (EMI), reduce signal noise, and provide a stable reference voltage for the circuit. Ground planes also help to distribute heat and improve the mechanical stability of the PCB.
4. How can I minimize crosstalk between adjacent signals on a PCB?
To minimize crosstalk between adjacent signals, consider the following techniques:
- Increase the spacing between the traces to reduce the coupling capacitance
- Use guard traces or ground shields between sensitive signals to isolate them from each other
- Route critical signals on different layers with ground planes in between to provide shielding
- Use differential signaling techniques, such as LVDS or CML, for high-speed signals to cancel out the electromagnetic fields
5. What are the advantages of using surface mount technology (SMT) components in PCB design?
Surface mount technology (SMT) components offer several advantages over through-hole components in PCB design:
- Smaller footprints, allowing for higher component density and more compact PCB designs
- Easier and faster automated assembly processes, reducing manufacturing costs and lead times
- Better high-frequency performance due to shorter lead lengths and reduced parasitic inductance
- Improved mechanical stability and reliability due to the absence of drilled holes in the PCB
Conclusion
PCB design is a critical aspect of electronic product development, and following best practices and guidelines is essential for creating high-quality, reliable, and manufacturable PCBs. By understanding the PCB design workflow, layer stackup considerations, component placement and routing guidelines, EMI reduction techniques, and manufacturing and assembly factors, you can optimize your PCB designs for better performance, cost-effectiveness, and overall success.
Remember to always consult with your PCB manufacturer and assembly partners to ensure your design meets their specific requirements and capabilities. Continuously update your knowledge and skills in PCB design as new technologies and techniques emerge to stay competitive in the ever-evolving world of electronics.
No responses yet