Understanding the Importance of PCB Component Selection
PCB component selection is a critical aspect of the PCB design process. The components you choose will directly impact the performance, reliability, and cost of your PCB. Poor component selection can lead to issues such as signal integrity problems, thermal management challenges, and even complete board failure. On the other hand, carefully selecting the right components can optimize your PCB’s functionality, improve its lifespan, and reduce overall costs.
Key Factors to Consider When Selecting PCB Components
When selecting PCB components, there are several key factors to consider:
- Functionality: The component must fulfill the specific function required by your circuit design.
- Reliability: The component should have a proven track record of reliability and durability.
- Cost: The component should fit within your budget without compromising on quality.
- Availability: The component should be readily available from reliable suppliers to avoid delays in production.
- Compatibility: The component must be compatible with other components on the PCB and the manufacturing process.
Tip 1: Understand Your PCB’s Requirements
Before diving into component selection, it’s essential to have a clear understanding of your PCB’s requirements. This includes factors such as the intended application, operating environment, power requirements, and signal integrity needs. Having a well-defined set of requirements will help you narrow down your component choices and ensure that you select components that are suitable for your specific PCB design.
Defining Your PCB’s Specifications
To define your PCB’s specifications, consider the following aspects:
- Application: What is the purpose of your PCB? Is it for a consumer electronic device, an industrial control system, or a medical device?
- Operating Environment: Will your PCB be exposed to extreme temperatures, humidity, vibrations, or other harsh conditions?
- Power Requirements: What are the voltage and current requirements for your PCB? Will it require high power handling capabilities?
- Signal Integrity: What are the signal frequencies and data rates your PCB needs to support? Are there any specific signal integrity considerations?
By clearly defining your PCB’s specifications, you’ll have a solid foundation for selecting the right components.
Tip 2: Consider the Component’s Packaging
PCB components come in various packaging options, such as through-hole, surface mount (SMT), and ball grid array (BGA). The choice of packaging will depend on factors such as the available space on your PCB, the manufacturing process, and the component’s performance requirements.
Through-Hole vs. Surface Mount Components
Through-hole components have long leads that are inserted into holes drilled in the PCB and soldered on the opposite side. They are generally larger and easier to handle than surface mount components. Through-hole components are suitable for applications that require high power handling or mechanical stability.
Surface mount components, on the other hand, are smaller and are mounted directly onto the surface of the PCB. They offer several advantages over through-hole components, including:
- Reduced PCB size and weight
- Improved high-frequency performance
- Faster assembly process
- Lower manufacturing costs
Ball Grid Array (BGA) Packaging
BGA components have a grid of solder balls on their underside that are used to attach the component to the PCB. BGA packaging offers a high density of interconnects in a small footprint, making it suitable for complex, high-performance applications. However, BGA components can be more challenging to work with due to their small size and the need for precise alignment during the soldering process.
Packaging Type | Advantages | Disadvantages |
---|---|---|
Through-Hole | – High power handling – Mechanical stability – Easier to handle |
– Larger size – Higher manufacturing costs – Limited high-frequency performance |
Surface Mount | – Reduced PCB size and weight – Improved high-frequency performance – Faster assembly process – Lower manufacturing costs |
– Smaller size can be challenging to handle – Requires precise placement and soldering |
Ball Grid Array | – High density of interconnects – Small footprint – Suitable for complex, high-performance applications |
– Challenging to work with due to small size – Requires precise alignment during soldering |
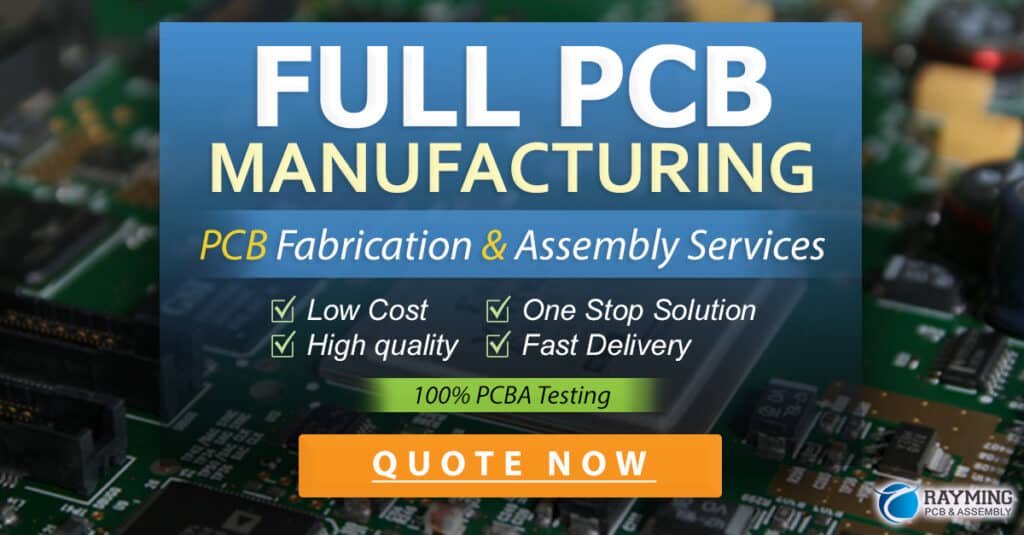
Tip 3: Evaluate the Component’s Electrical Characteristics
When selecting PCB components, it’s crucial to evaluate their electrical characteristics to ensure they meet your circuit’s requirements. This includes factors such as voltage and current ratings, power dissipation, and tolerance.
Voltage and Current Ratings
Every component has specified voltage and current ratings that indicate the maximum values it can handle without damage. It’s essential to choose components with ratings that exceed your circuit’s requirements to ensure reliable operation and prevent component failure.
Power Dissipation
Power dissipation refers to the amount of power a component can safely dissipate as heat. When selecting components, consider the power dissipation requirements of your circuit and choose components with adequate power handling capabilities. Insufficient power dissipation can lead to overheating and component failure.
Tolerance
Tolerance indicates the acceptable range of variation in a component’s nominal value. For example, a resistor with a tolerance of 5% can have a resistance value that varies by up to 5% from its nominal value. When selecting components, consider the tolerance requirements of your circuit and choose components with appropriate tolerances to ensure accurate and reliable performance.
Tip 4: Consider the Component’s Environmental Factors
The environment in which your PCB will operate can have a significant impact on component selection. Factors such as temperature, humidity, and vibration can affect the performance and reliability of your components.
Temperature Range
PCB components are rated for specific temperature ranges, indicating the minimum and maximum temperatures at which they can operate reliably. When selecting components, consider the expected temperature range of your PCB’s operating environment and choose components with suitable temperature ratings.
Humidity and Moisture Resistance
Humidity and moisture can cause corrosion, electrical leakage, and other issues in PCB components. If your PCB will be exposed to high humidity or moisture, choose components with appropriate moisture resistance ratings, such as those with conformal coatings or sealed packaging.
Vibration and Shock Resistance
Vibration and shock can cause mechanical stress on PCB components, leading to damage or failure. If your PCB will be subject to vibration or shock, select components with robust mechanical construction and rated for the expected levels of vibration and shock.
Environmental Factor | Consideration |
---|---|
Temperature Range | Choose components with suitable temperature ratings for your PCB’s operating environment |
Humidity and Moisture | Select components with appropriate moisture resistance ratings if exposed to high humidity or moisture |
Vibration and Shock | Opt for components with robust mechanical construction and rated for expected vibration and shock levels |
Tip 5: Examine the Component’s Quality and Reliability
The quality and reliability of your PCB components are critical for ensuring the long-term performance and durability of your PCB. When selecting components, consider factors such as the manufacturer’s reputation, quality certifications, and reliability data.
Manufacturer Reputation
Choose components from reputable manufacturers with a proven track record of producing high-quality and reliable products. Look for manufacturers with a strong presence in the industry and positive customer feedback.
Quality Certifications
Look for components that have undergone rigorous quality testing and have received relevant certifications, such as ISO 9001, IATF 16949, or MIL-STD-883. These certifications indicate that the manufacturer adheres to strict quality standards and processes.
Reliability Data
Examine the reliability data provided by the manufacturer, such as mean time between failures (MTBF), failure in time (FIT) rates, and accelerated life testing results. This data can give you valuable insights into the expected reliability and lifespan of the component.
Tip 6: Consider the Component’s Availability and Lead Time
When selecting PCB components, it’s essential to consider their availability and lead time to ensure timely and uninterrupted production.
Availability
Choose components that are readily available from multiple reliable suppliers. This reduces the risk of supply chain disruptions and ensures that you can source the components when needed.
Lead Time
Consider the lead time required to obtain the components. Some components may have longer lead times due to high demand or limited production. Plan your component selection and ordering process accordingly to avoid delays in your PCB manufacturing timeline.
Tip 7: Evaluate the Component’s Cost and Value
Cost is an important factor in PCB component selection, but it should be balanced with the component’s value and overall impact on your PCB’s performance and reliability.
Cost vs. Quality
While it may be tempting to choose the lowest-cost components, it’s crucial to consider the potential trade-offs in quality and reliability. In some cases, investing in higher-quality components can lead to better performance, longer lifespan, and reduced overall costs in the long run.
Total Cost of Ownership
When evaluating component costs, consider the total cost of ownership (TCO), which includes factors such as initial purchase price, assembly costs, and potential costs associated with component failure or replacement. A component with a higher initial cost but better reliability and longer lifespan may have a lower TCO compared to a cheaper but less reliable alternative.
Tip 8: Review the Component’s Datasheet and Specifications
Before selecting a component, thoroughly review its datasheet and specifications to ensure it meets your PCB’s requirements.
Key Specifications to Review
When reviewing a component’s datasheet, pay attention to the following key specifications:
- Electrical Characteristics: Voltage and current ratings, power dissipation, and tolerance.
- Mechanical Characteristics: Dimensions, packaging type, and pin configuration.
- Environmental Ratings: Temperature range, humidity resistance, and vibration/shock resistance.
- Performance Graphs: Graphs showing the component’s performance under various conditions, such as frequency response or temperature dependence.
Application Notes and Reference Designs
In addition to the datasheet, look for application notes and reference designs provided by the manufacturer. These resources can offer valuable insights into the component’s usage, best practices, and example circuits that can help you optimize your PCB design.
Tip 9: Consider the Component’s Compatibility and Interoperability
Ensure that the components you select are compatible with each other and with your PCB’s manufacturing process.
Compatibility with Other Components
Verify that the selected components are compatible with the other components on your PCB. This includes factors such as voltage levels, signal interfaces, and pin configurations. Incompatible components can lead to signal integrity issues, performance degradation, or even damage to the components.
Compatibility with Manufacturing Process
Consider the compatibility of the components with your PCB manufacturing process. Some components may require specific assembly techniques, such as reflow soldering or wave soldering, which should be compatible with your PCB Assembly process. Additionally, ensure that the component’s packaging and footprint are suitable for your PCB layout and assembly equipment.
Tip 10: Evaluate the Component’s Thermal Characteristics
Thermal management is a critical aspect of PCB design, and component selection plays a significant role in ensuring proper heat dissipation and preventing thermal issues.
Power Dissipation and Thermal Resistance
When selecting components, consider their power dissipation and thermal resistance. Power dissipation indicates the amount of power the component can safely dissipate as heat, while thermal resistance measures the component’s ability to transfer heat from its junction to the surrounding environment. Choose components with appropriate power dissipation and thermal resistance ratings to ensure effective heat dissipation.
Thermal Management Techniques
In addition to selecting components with suitable thermal characteristics, consider implementing thermal management techniques in your PCB design. This can include:
- Using thermal vias to transfer heat from the component to the PCB’s ground plane.
- Incorporating heat sinks or heat spreaders to enhance heat dissipation.
- Providing adequate airflow or cooling solutions to remove heat from the PCB.
By selecting components with appropriate thermal characteristics and implementing effective thermal management techniques, you can ensure the reliable operation of your PCB and prevent heat-related failures.
Tip 11: Consider the Component’s Electromagnetic Compatibility (EMC)
Electromagnetic compatibility (EMC) is the ability of electronic components and systems to operate without causing or being affected by electromagnetic interference (EMI).
EMI Susceptibility and Emissions
When selecting components, consider their EMI susceptibility and emissions. EMI susceptibility refers to a component’s ability to withstand external electromagnetic interference without performance degradation. EMI emissions, on the other hand, refer to the electromagnetic interference generated by the component itself.
EMC Compliance and Regulations
Ensure that the selected components comply with relevant EMC regulations and standards, such as FCC Part 15, EN 55022, or IEC 61000. These regulations specify limits for EMI emissions and immunity requirements to ensure that electronic devices can operate without causing or being affected by electromagnetic interference.
EMC Design Considerations
When designing your PCB, consider implementing EMC design best practices to minimize EMI issues. This can include:
- Proper grounding and shielding techniques
- Minimizing loop areas and current paths
- Using filters and suppressors to reduce EMI emissions
- Physically separating sensitive components from potential EMI sources
By selecting components with good EMC characteristics and implementing EMC design best practices, you can ensure that your PCB operates reliably in the presence of electromagnetic interference.
Tip 12: Evaluate the Component’s Lifecycle and Obsolescence Risk
The lifecycle and obsolescence risk of components can have a significant impact on the long-term viability and maintainability of your PCB.
Component Lifecycle Stages
Components go through various lifecycle stages, from introduction to obsolescence. When selecting components, consider their current lifecycle stage and expected longevity. Choosing components that are in the early stages of their lifecycle can help ensure long-term availability and support.
Obsolescence Risk Management
Obsolescence risk refers to the possibility of a component becoming unavailable or unsupported by the manufacturer. To manage obsolescence risk:
- Choose components from manufacturers with a strong track record of long-term support and availability.
- Consider using components with multiple sourcing options to reduce the impact of a single supplier’s obsolescence.
- Develop an obsolescence management plan that includes regular monitoring of component availability and proactive identification of potential replacement options.
By evaluating the lifecycle and obsolescence risk of components, you can ensure the long-term sustainability and maintainability of your PCB design.
Tip 13: Collaborate with Suppliers and Manufacturers
Collaboration with component suppliers and PCB manufacturers can provide valuable insights and support throughout the component selection process.
Leveraging Supplier Expertise
Component suppliers often have in-depth knowledge of their products and can provide valuable technical support and recommendations. Engage with suppliers early in the design process to discuss your requirements, get product recommendations, and access technical resources such as datasheets, application notes, and reference designs.
Manufacturing Process Considerations
Collaborate with your PCB manufacturer to ensure that your selected components are compatible with their manufacturing processes and capabilities. Discuss factors such as component placement, soldering requirements, and any specific handling or assembly considerations. This collaboration can help optimize your PCB design for manufacturability and reduce the risk of assembly issues.
Tip 14: Stay Updated with Industry Trends and Advancements
The electronics industry is constantly evolving, with new components, technologies, and design practices emerging regularly. To make informed component selection decisions, it’s essential to stay updated with the latest industry trends and advancements.
Attend Industry Events and Conferences
Attend industry events and conferences to learn about the latest component offerings, design techniques, and best practices. These events provide opportunities to network with industry experts, attend technical sessions, and explore new technologies and solutions.
Engage with Online Communities and Resources
Participate in online forums, discussion groups, and social media communities related to PCB design and component selection. These platforms allow you to connect with other professionals, ask questions, and share knowledge and experiences. Additionally, regularly review industry publications, blogs, and manufacturer resources to stay informed about new products, design trends, and application insights.
By staying updated with industry trends and advancements, you can make more informed and forward-looking component selection decisions that benefit your PCB designs.
Frequently Asked Questions (FAQ)
- What are the key factors to consider when selecting PCB components?
-
When selecting PCB components, consider factors such as functionality, reliability, cost, availability, compatibility, electrical characteristics, environmental factors, quality, and packaging.
-
How do I ensure compatibility between different components on my PCB?
-
To ensure compatibility between components, review their datasheets and specifications, paying attention to factors such as voltage levels, signal interfaces, and pin configurations. Verify that the components can work together seamlessly and are compatible with your PCB’s manufacturing process.
-
What are the differences between through-hole and surface mount components?
-
Through-hole components have long leads that are inserted into holes drilled in the PCB and soldered on the opposite side. They are larger and easier to handle but have limited high-frequency performance. Surface mount components are smaller, mounted directly onto the PCB surface, and offer advantages such as reduced size, improved high-frequency performance, and faster assembly.
-
How do I manage obsolescence risk when selecting components?
-
To manage obsolescence risk, choose components from manufacturers with a strong track record of long-term support and availability. Consider using components with multiple sourcing options and develop an obsolescence management plan that includes regular monitoring of component availability and proactive identification of potential replacement options.
-
Why is collaboration with suppliers and manufacturers important in component selection?
- Collaboration with component suppliers and PCB manufacturers provides valuable insights and support
No responses yet