Introduction to PCB Artwork
Printed Circuit Board (PCB) artwork is a crucial aspect of the PCB design and manufacturing process. It refers to the graphical representation of the PCB layout, including the copper traces, component footprints, and other features. Creating accurate and precise PCB artwork is essential for ensuring the proper functioning and reliability of the final product. In this article, we will explore the key design guidelines that every PCB manufacturer should be aware of to create high-quality PCB artwork.
The Importance of PCB Artwork Guidelines
Following PCB artwork guidelines is critical for several reasons:
-
Manufacturability: Adhering to design guidelines ensures that the PCB can be manufactured efficiently and with minimal issues. It helps avoid potential problems during the fabrication process, such as short circuits, open circuits, or incorrect component placement.
-
Reliability: Well-designed PCB artwork contributes to the overall reliability of the final product. By following guidelines related to trace width, spacing, and other parameters, manufacturers can minimize signal integrity issues and improve the performance of the PCB.
-
Cost-effectiveness: Proper PCB artwork design can help reduce manufacturing costs. By optimizing the layout and minimizing the number of layers required, manufacturers can save on material and production expenses.
Key Elements of PCB Artwork
Before delving into the design guidelines, let’s review the essential elements of PCB artwork:
-
Copper Traces: These are the conductive pathways that carry electrical signals between components on the PCB. Copper traces are typically made of copper and can be found on both the top and bottom layers of the board.
-
Component Footprints: Footprints are the specific patterns and layouts designed to accommodate electronic components on the PCB. They include the pads, holes, and silkscreen markings that define where each component should be placed.
-
Vias: Vias are small holes drilled through the PCB to allow electrical connections between different layers of the board. They are essential for creating multi-layer PCBs and enabling more complex routing.
-
Solder Mask: The solder mask is a protective layer applied over the copper traces to prevent accidental short circuits and protect the PCB from environmental factors. It is typically green in color but can also be found in other colors.
-
Silkscreen: The silkscreen layer contains text, logos, and other markings that provide information about the PCB, such as component designators, company logos, and assembly instructions.
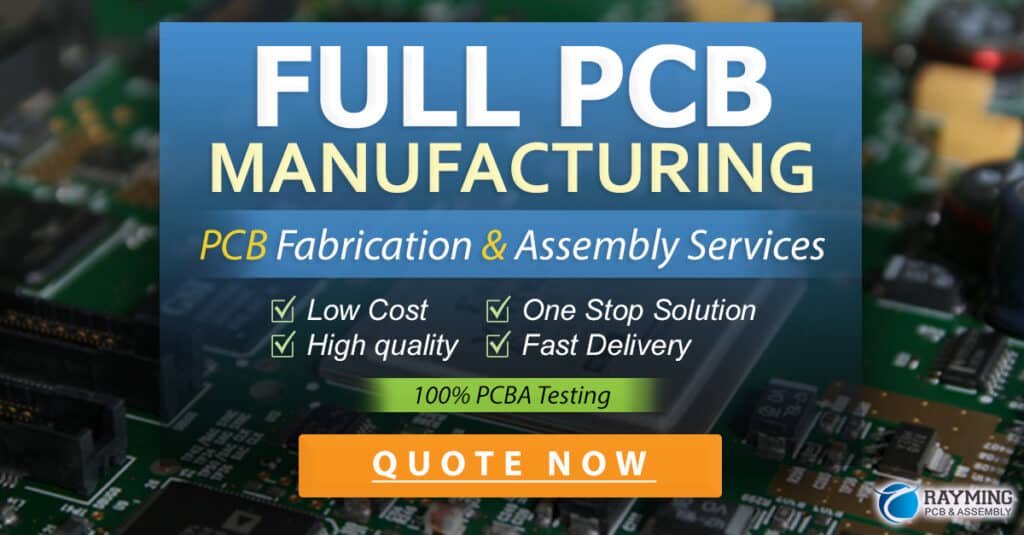
PCB Artwork Design Guidelines
Now, let’s explore the key design guidelines that PCB manufacturers should follow when creating PCB artwork.
1. Trace Width and Spacing
Trace width and spacing are critical parameters that impact the manufacturability and performance of the PCB. The trace width refers to the thickness of the copper traces, while spacing refers to the distance between adjacent traces.
Parameter | Recommended Value |
---|---|
Minimum Trace Width | 0.006 inches (0.15 mm) |
Minimum Trace Spacing | 0.006 inches (0.15 mm) |
It is essential to maintain appropriate trace width and spacing to ensure proper signal integrity and avoid manufacturing issues. Traces that are too thin or too close together can lead to signal crosstalk, electromagnetic interference (EMI), or manufacturing defects.
2. Clearance and Creepage
Clearance and creepage are two important considerations when designing PCB artwork. Clearance refers to the minimum distance between conductive features on the same layer, while creepage refers to the minimum distance between conductive features on different layers.
Parameter | Recommended Value |
---|---|
Minimum Clearance | 0.010 inches (0.25 mm) |
Minimum Creepage | 0.020 inches (0.50 mm) |
Maintaining adequate clearance and creepage distances is crucial for preventing electrical shorts and ensuring the reliability of the PCB. The specific values may vary depending on the voltage and environmental conditions of the application.
3. Drill Sizes and Pad Dimensions
When designing PCB artwork, it is important to consider the drill sizes and pad dimensions for through-hole components and vias.
Parameter | Recommended Value |
---|---|
Minimum Drill Size | 0.020 inches (0.50 mm) |
Minimum Pad Size | 0.040 inches (1.00 mm) |
Using appropriate drill sizes and pad dimensions helps ensure proper component placement and reliable solder connections. It is also important to consider the tolerances and capabilities of the PCB manufacturing process when selecting these values.
4. Solder Mask and Silkscreen
The solder mask and silkscreen layers play important roles in the PCB artwork design.
Parameter | Recommended Value |
---|---|
Minimum Solder Mask Opening | 0.002 inches (0.05 mm) larger than pad size |
Minimum Silkscreen Line Width | 0.006 inches (0.15 mm) |
Minimum Silkscreen Text Size | 0.040 inches (1.00 mm) |
Ensuring proper solder mask openings helps prevent solder bridging and improves the reliability of the solder connections. The silkscreen layer should be legible and provide clear information about component placement and orientation.
5. Component Placement and Orientation
When placing components on the PCB artwork, consider the following guidelines:
- Place components in a logical and organized manner, grouping related components together.
- Orient components in a consistent direction to facilitate assembly and troubleshooting.
- Provide sufficient spacing between components to allow for proper soldering and inspection.
- Consider the mechanical constraints and thermal requirements of components when determining their placement.
6. Routing and Signal Integrity
Proper routing and signal integrity are essential for ensuring the reliable operation of the PCB.
- Route traces as short and direct as possible to minimize signal reflections and delays.
- Avoid sharp corners and use 45-degree angles or curved traces for smoother signal flow.
- Use appropriate trace widths and spacing based on the signal frequency and current requirements.
- Implement proper grounding and shielding techniques to minimize EMI and crosstalk.
7. Documentation and Labeling
Clear documentation and labeling are crucial for facilitating PCB assembly and troubleshooting.
- Provide comprehensive documentation, including schematic diagrams, bill of materials (BOM), and assembly instructions.
- Use clear and concise labels on the silkscreen layer to identify components, test points, and other important features.
- Include version numbers and revision history to track changes and ensure consistency.
Frequently Asked Questions (FAQ)
-
What is the purpose of PCB artwork?
PCB artwork is the graphical representation of the PCB layout, including copper traces, component footprints, and other features. It serves as a blueprint for the PCB manufacturing process and ensures the proper placement and connectivity of components on the board. -
Why is it important to follow PCB artwork guidelines?
Following PCB artwork guidelines is crucial for several reasons: - It ensures the manufacturability of the PCB by avoiding potential issues during fabrication.
- It contributes to the reliability of the final product by minimizing signal integrity issues and improving performance.
-
It helps reduce manufacturing costs by optimizing the layout and minimizing the number of layers required.
-
What are the key elements of PCB artwork?
The key elements of PCB artwork include: - Copper traces: Conductive pathways that carry electrical signals between components.
- Component footprints: Specific patterns and layouts designed to accommodate electronic components.
- Vias: Small holes drilled through the PCB to allow electrical connections between different layers.
- Solder mask: Protective layer applied over the copper traces to prevent short circuits and protect the PCB.
-
Silkscreen: Text, logos, and other markings that provide information about the PCB.
-
What are the recommended values for trace width and spacing?
The recommended minimum values for trace width and spacing are: - Minimum trace width: 0.006 inches (0.15 mm)
-
Minimum trace spacing: 0.006 inches (0.15 mm)
These values ensure proper signal integrity and help avoid manufacturing issues. -
How can proper PCB artwork design contribute to cost-effectiveness?
Proper PCB artwork design can contribute to cost-effectiveness in several ways: - Optimizing the layout and minimizing the number of layers required can reduce material and production costs.
- Following design guidelines ensures manufacturability, reducing the likelihood of defects and rework.
- Efficient component placement and routing can minimize the overall board size, saving on material costs.
Conclusion
PCB artwork is a critical aspect of the PCB design and manufacturing process. By following the design guidelines outlined in this article, PCB manufacturers can create high-quality PCB artwork that ensures manufacturability, reliability, and cost-effectiveness. Key considerations include trace width and spacing, clearance and creepage, drill sizes and pad dimensions, solder mask and silkscreen, component placement and orientation, routing and signal integrity, and documentation and labeling. By adhering to these guidelines, manufacturers can produce PCBs that meet the highest standards of quality and performance.
No responses yet