What is OSP PCB?
OSP (Organic Solderability Preservative) PCB is a type of surface finish applied to printed circuit boards (PCBs) to protect the exposed copper from oxidation and ensure good solderability. OSP is a water-based organic compound that selectively bonds to the copper surface, creating a protective layer that prevents oxidation and maintains the solderability of the PCB.
OSP PCB has gained popularity as an alternative to other surface finishes like HASL (Hot Air Solder Leveling), ENIG (Electroless Nickel Immersion Gold), and Immersion Silver. It offers several advantages, including cost-effectiveness, good shelf life, and compatibility with various soldering processes.
Advantages of OSP PCB
Cost-effectiveness
One of the primary advantages of OSP PCB is its cost-effectiveness compared to other surface finishes. The application process for OSP is relatively simple and does not require expensive materials or equipment. This makes it an attractive option for manufacturers looking to reduce production costs without compromising on quality.
Good shelf life
OSP PCB has a good shelf life, typically ranging from 6 to 12 months, depending on the storage conditions. The organic compound used in OSP forms a stable bond with the copper surface, preventing oxidation and maintaining solderability for an extended period. This is particularly beneficial for PCBs that may not be assembled immediately after manufacturing.
Compatibility with various soldering processes
OSP PCB is compatible with a wide range of soldering processes, including wave soldering, reflow soldering, and hand soldering. The organic coating does not interfere with the soldering process and allows for good wetting and joint formation. This versatility makes OSP suitable for different types of PCB assemblies and applications.
Flat surface finish
Unlike HASL, which can result in an uneven surface due to the hot air leveling process, OSP provides a flat and uniform surface finish. This is advantageous for surface-mount technology (SMT) components, as it ensures better contact and reduces the risk of component misalignment during assembly.
RoHS compliance
OSP PCB is compliant with the Restriction of Hazardous Substances (RoHS) directive, as it does not contain any hazardous materials like lead. This makes it an environmentally friendly option and ensures compliance with international regulations.
Disadvantages of OSP PCB
Limited shelf life compared to other finishes
Although OSP PCB has a good shelf life, it is still shorter compared to other surface finishes like ENIG or Immersion Silver. The organic coating may degrade over time, especially if exposed to high humidity or temperature. This can lead to reduced solderability and potential assembly issues if the PCBs are stored for extended periods.
Sensitivity to handling and contamination
OSP PCB is more sensitive to handling and contamination compared to other surface finishes. The organic coating can be easily damaged or contaminated by improper handling, fingerprints, or exposure to certain chemicals. This can result in poor solderability and assembly defects. Proper handling and storage procedures must be followed to maintain the integrity of the OSP finish.
Not suitable for multiple reflow cycles
OSP PCB is not recommended for PCB assemblies that require multiple reflow cycles, such as double-sided SMT boards or boards with complex components. The organic coating may deteriorate after the first reflow cycle, leading to reduced solderability in subsequent reflow processes. In such cases, other surface finishes like ENIG or Immersion Silver may be more suitable.
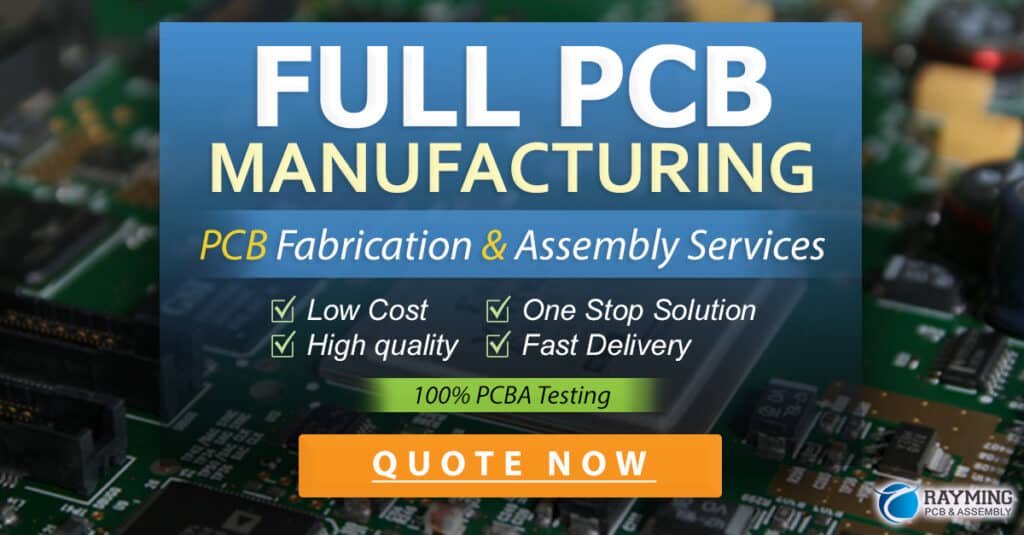
OSP PCB Application Process
The application process for OSP PCB involves several steps to ensure a uniform and stable protective layer on the copper surface. The general steps are as follows:
-
Cleaning: The PCB is thoroughly cleaned to remove any dirt, grease, or oxides from the copper surface. This is typically done using a mild alkaline cleaning solution.
-
Microetching: A microetching process is performed to remove any remaining oxides and provide a clean and activated copper surface for OSP application. This step enhances the bonding between the copper and the organic compound.
-
OSP application: The OSP solution is applied to the PCB surface either by immersion or spraying. The PCB is then dried using hot air to evaporate any excess moisture.
-
Curing: The PCB undergoes a curing process to promote the formation of a stable and uniform OSP layer. This is typically done by exposing the PCB to elevated temperatures for a specific duration.
-
Inspection: The OSP-coated PCB is inspected for surface coverage, uniformity, and any defects. This is done using visual inspection or specialized equipment like a solderability tester.
OSP PCB Storage and Handling
To maintain the quality and solderability of OSP PCBs, proper storage and handling procedures must be followed. Some key considerations include:
-
Storage conditions: OSP PCBs should be stored in a cool, dry environment with a relative humidity of less than 60% and a temperature below 30°C. Exposure to high humidity or temperature can degrade the OSP coating over time.
-
Packaging: OSP PCBs should be packaged in moisture barrier bags (MBB) with desiccants to protect them from moisture and contamination during storage and transportation.
-
Handling: Proper handling procedures should be followed to avoid damaging or contaminating the OSP surface. This includes using clean gloves, avoiding direct contact with the surface, and minimizing exposure to airborne contaminants.
-
Shelf life monitoring: The shelf life of OSP PCBs should be monitored, and the boards should be used within the recommended timeframe to ensure optimal solderability. Expired boards may require additional testing or re-finishing before assembly.
Comparison with Other PCB Surface Finishes
Surface Finish | Pros | Cons |
---|---|---|
OSP | – Cost-effective – Good solderability – Flat surface finish – RoHS compliant |
– Limited shelf life – Sensitive to handling and contamination – Not suitable for multiple reflow cycles |
HASL | – Excellent solderability – Long shelf life – Suitable for multiple reflow cycles |
– Uneven surface finish – Contains lead (non-RoHS compliant) – Higher cost compared to OSP |
ENIG | – Excellent solderability – Long shelf life – Suitable for multiple reflow cycles – RoHS compliant |
– Higher cost compared to OSP – Risk of “black pad” defect – Requires strict process control |
Immersion Silver | – Good solderability – Flat surface finish – RoHS compliant |
– Higher cost compared to OSP – Limited shelf life compared to ENIG – Can tarnish over time |
FAQ
-
Q: What is the typical shelf life of OSP PCBs?
A: The typical shelf life of OSP PCBs ranges from 6 to 12 months, depending on the storage conditions and the specific OSP formulation used. -
Q: Can OSP PCBs be reworked or repaired?
A: Yes, OSP PCBs can be reworked or repaired using standard soldering techniques. However, the OSP coating may be damaged during the rework process, and the repaired area may require additional protection. -
Q: Is OSP suitable for High-Frequency PCB applications?
A: Yes, OSP is suitable for high-frequency PCB Applications due to its flat and uniform surface finish, which minimizes signal loss and distortion. -
Q: How does OSP compare to ENIG in terms of cost?
A: OSP is generally more cost-effective than ENIG, as the application process is simpler and does not require expensive materials like gold. -
Q: Can OSP be used for PCBs with fine-pitch components?
A: Yes, OSP can be used for PCBs with fine-pitch components, as the flat surface finish allows for precise component placement and good solderability.
In conclusion, OSP PCB is an effective and cost-efficient surface finish option for a wide range of PCB applications. Its good solderability, flat surface finish, and compatibility with various soldering processes make it a popular choice among manufacturers. However, its limited shelf life and sensitivity to handling and contamination should be considered when deciding on the most suitable surface finish for a specific project. By understanding the advantages, disadvantages, and proper handling procedures for OSP PCBs, manufacturers can ensure high-quality and reliable PCB assemblies.
No responses yet