What are Rogers PCB Materials Used For?
Rogers Corporation produces a wide range of high-performance printed circuit board (PCB) materials engineered for demanding applications. Rogers’ PCB Laminates offer superior electrical properties, thermal management, and mechanical stability for use in:
- High-frequency RF/microwave circuits
- Antenna and radar systems
- 5G wireless infrastructure
- Aerospace and defense electronics
- Automotive radar and sensors
- High-power industrial controls
- Medical equipment
Rogers’ innovative PCB materials enable the design of compact, reliable electronic systems that can withstand harsh environmental conditions. The unique properties of Rogers’ laminates make them ideal for applications requiring:
- Low dielectric loss for high signal integrity
- Consistent electrical performance over temperature
- Controlled impedance for impedance matching
- Excellent thermal conductivity for heat dissipation
- Dimensional stability for fine-line circuitry
- UL 94 V-0 flame retardancy
Popular Rogers PCB Material Product Lines
RO3000 Series Laminates
RO3000 series high-frequency circuit materials are ceramic-filled PTFE composites designed for commercial RF/microwave applications. They offer:
- Dielectric constants from 3.0 to 6.15
- Dissipation factors as low as 0.0009
- Consistent properties up to 77 GHz
Material | Dielectric Constant | Dissipation Factor @ 10 GHz |
---|---|---|
RO3003 | 3.00 | 0.0010 |
RO3006 | 6.15 | 0.0020 |
RO3010 | 10.2 | 0.0023 |
RO4000 Series Laminates
RO4000 series hydrocarbon ceramic laminates provide a cost-effective FR-4 alternative for high-volume wireless electronics production. Benefits include:
- Dielectric constants from 2.55 to 6.15
- Low Z-axis CTE for reliable plated through holes
- CAF resistant with lead-free assembly
Material | Dielectric Constant | Dissipation Factor @ 2.5 GHz |
---|---|---|
RO4003C | 3.38 | 0.0027 |
RO4350B | 3.48 | 0.0037 |
RO4360G2 | 6.15 | 0.0038 |
RT/duroid Laminates
RT/duroid® microwave laminates are PTFE-based composites reinforced with glass microfibers for military and space applications. Key properties:
- Extremely low dissipation factors (0.001-0.002)
- Excellent dielectric constant tolerance (<0.02)
- Resistant to out-gassing in vacuum
Material | Dielectric Constant | Dissipation Factor @ 10 GHz |
---|---|---|
RT/duroid 5870 | 2.33 | 0.0012 |
RT/duroid 5880 | 2.20 | 0.0009 |
RT/duroid 6002 | 2.94 | 0.0012 |
High-Frequency PCB Design Considerations
Designing PCBs for RF/microwave frequencies requires careful material selection and layout techniques to maintain signal integrity. Key considerations include:
Moisture Absorption
PTFE-based laminates like RO3000 and RT/duroid have very low moisture absorption compared to FR-4, minimizing the change in dielectric constant that can detune circuits.
Coefficient of Thermal Expansion (CTE)
Mismatches in the X-Y and Z-axis CTE of the dielectric and copper cladding can cause warping or interfacial failures during assembly. RO4000 laminates have a low Z-axis expansion for reliable plated through holes.
Thermal Management
High-power circuits generate significant heat that must be dissipated to avoid performance degradation. RT/duroid 6035HTC combines low loss with a high thermal conductivity of 1.44 W/m·K for effective cooling.
Controlled Impedance
Maintaining a constant impedance is critical for impedance matching and minimizing signal reflections. Rogers’ laminates have a tight dielectric constant control for consistent impedance across the board.
Insertion Loss
Insertion loss increases with frequency due to dielectric loss and conductor effects. Using low-loss materials like RO3000 and RT/duroid minimizes insertion loss for longer transmission distances.
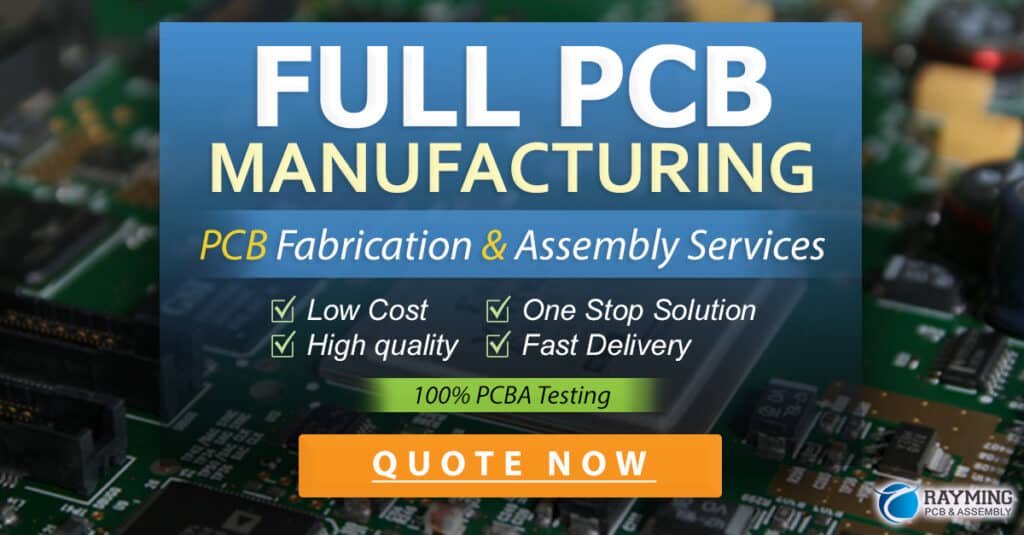
Fabrication Guidelines for Rogers PCBs
Fabricating PCBs with Rogers’ materials requires specialized processes and equipment compared to standard FR-4. Some key guidelines:
- Use recommended drill parameters and entry/exit materials to avoid delamination or burrs
- Pretreat the PTFE surface with sodium etch prior to solder mask application
- Select compatible adhesives and soldermasks rated for high temperatures
- Follow the press cycle recommendations for optimal flow and cure of the resin system
- Use a plasma or chemical treatment to prepare the PTFE surface for assembly
Working closely with a PCB fabricator experienced in processing Rogers’ materials is essential to ensure a successful manufacturing outcome.
Industry Applications for Rogers PCBs
Wireless Infrastructure
5G wireless networks rely on phased array antennas and massive MIMO systems operating in the 24-40 GHz mmWave bands. Rogers’ low-loss laminates enable the design of high-gain, multi-layer antenna boards with beam steering capabilities.
Automotive Radar
Advanced driver assistance systems (ADAS) use 77 GHz radar for collision avoidance and autonomous driving functions. RO3003 laminates offer a stable dielectric constant of 3.0 and low loss for compact, high-resolution radar modules.
Aerospace & Defense
Military radar and electronic warfare systems require PCB materials that can withstand extreme temperatures, shocks, and vibrations. RT/duroid laminates provide exceptional electrical and mechanical stability for mission-critical aerospace applications.
Medical Electronics
MRI and X-ray imaging systems operate at high voltages and frequencies, demanding low-loss PCB materials with high voltage breakdown strength. RO4000 series laminates meet the cost, performance, and reliability requirements for medical equipment.
Frequently Asked Questions (FAQ)
1. How do I select the right Rogers PCB material for my application?
Choosing the optimal Rogers PCB material depends on your specific application requirements, such as:
- Operating frequency and bandwidth
- Dielectric constant and loss tangent
- Thermal conductivity and stability
- Mechanical strength and stiffness
- Cost and availability
Consult the Rogers product selection guide or contact their technical support team for assistance in material selection.
2. Can I use standard FR-4 fabrication processes for Rogers PCBs?
While some Rogers PCB materials may be compatible with conventional FR-4 fabrication processes, others require specialized techniques, such as:
- Laser or plasma drilling for small vias
- Sodium etch pretreatment for PTFE laminates
- High-temperature press cycles for hydrocarbon ceramics
- Plasma treatment for improved copper adhesion
It is recommended to work with a PCB fabricator experienced in handling Rogers materials to ensure the best results.
3. What are the lead times and minimum order quantities for Rogers PCBs?
Lead times and minimum order quantities (MOQs) for Rogers PCBs vary depending on the material type, thickness, and copper cladding specified. Some standard materials and configurations are available from distributors with short lead times and low MOQs. Custom laminates may require longer lead times and higher MOQs due to the special manufacturing processes involved. Check with your PCB supplier for current availability and pricing.
4. How do I manage the thermal expansion mismatch between Rogers laminates and copper?
Rogers PCB materials have different coefficients of thermal expansion (CTE) compared to copper, which can cause warping or delamination during thermal cycling. To minimize CTE mismatches:
- Use a symmetrical stack-up with balanced copper weights
- Specify a low-CTE laminate like RO4360G2 for the core
- Avoid large copper pours or use a thermal relief pattern
- Employ a rigid bonding or prepreg layer between the laminate and copper
Careful material selection and stack-up design can help manage thermal expansion issues in Rogers PCBs.
5. What are the key challenges in assembling Rogers PCBs?
Assembling Rogers PCBs presents some unique challenges compared to standard FR-4, such as:
- Poor solder mask adhesion to PTFE surfaces
- Higher reflow temperatures required for lead-free assembly
- Reduced thermal conductivity of PTFE affecting heat transfer
- Potential moisture absorption and outgassing in vacuum
To overcome these challenges:
- Use a compatible, high-temperature solder mask
- Specify a HASL or ENIG surface finish for better solderability
- Employ a metal core or thermal vias for enhanced heat dissipation
- Bake the PCB prior to assembly to remove absorbed moisture
Proper assembly process control and material handling can ensure reliable and high-yield manufacturing of Rogers PCB assemblies.
No responses yet