Introduction to Multilayer PCB
A multilayer PCB, also known as a multilayer printed circuit board, is a complex and advanced type of circuit board that consists of multiple layers of conductive copper foil laminated together with insulating material. These layers are interconnected through plated holes called vias, which allow electrical signals to pass between the different layers. Multilayer PCBs are used in a wide range of electronic devices, from smartphones and laptops to medical equipment and aerospace systems.
Advantages of Multilayer PCB
-
Increased circuit density: Multilayer PCBs allow for more complex circuits to be designed in a smaller space, as the multiple layers provide more room for routing traces and placing components.
-
Improved signal integrity: By using dedicated layers for power and ground planes, multilayer PCBs can minimize electromagnetic interference (EMI) and reduce signal noise, resulting in better signal integrity.
-
Enhanced reliability: The compact and robust structure of multilayer PCBs makes them more resistant to vibrations, shocks, and thermal stresses, thereby improving the overall reliability of the electronic device.
-
Reduced weight and size: With the ability to accommodate more components in a smaller area, multilayer PCBs contribute to the miniaturization of electronic devices, making them lighter and more compact.
Layers in a Multilayer PCB
A typical multilayer PCB consists of several types of layers, each serving a specific purpose. The most common layers found in a multilayer PCB include:
1. Signal Layers
Signal layers are used for routing the electrical signals between components on the PCB. These layers typically have thin traces and are located on the outer layers of the board for easy access. The number of signal layers in a multilayer PCB depends on the complexity of the circuit design.
2. Power and Ground Planes
Power and ground planes are dedicated layers that provide a low-impedance path for distributing power and ground signals throughout the PCB. These planes help to reduce EMI and maintain signal integrity by minimizing the loop area between the power source and the ground return path.
3. Dielectric Layers
Dielectric layers, also known as insulating layers, are used to separate and isolate the conductive layers in a multilayer PCB. These layers are typically made of materials such as FR-4, which is a glass-reinforced epoxy laminate. The thickness and properties of the dielectric layers play a crucial role in determining the electrical characteristics of the PCB, such as impedance and capacitance.
Designing a Multilayer PCB
Designing a multilayer PCB involves several key considerations to ensure optimal performance and manufacturability. Some of the essential factors to consider when designing a multilayer PCB include:
1. Layer Stackup
The layer stackup refers to the arrangement and order of the various layers in a multilayer PCB. A well-designed layer stackup takes into account factors such as signal integrity, impedance control, and manufacturing constraints. A typical layer stackup for a 6-layer PCB might look like this:
Layer | Type |
---|---|
1 | Signal Layer |
2 | Ground Plane |
3 | Signal Layer |
4 | Signal Layer |
5 | Power Plane |
6 | Signal Layer |
2. Via Types and Placement
Vias are the plated holes that interconnect the different layers in a multilayer PCB. There are several types of vias, each with its own advantages and limitations:
- Through-hole vias: These vias pass through all layers of the PCB and are typically used for components with through-hole pins.
- Blind vias: These vias connect an outer layer to an inner layer, but do not pass through the entire board.
- Buried vias: These vias connect two or more inner layers without reaching the outer layers.
When placing vias on a multilayer PCB, it is essential to consider factors such as via size, via-to-via spacing, and via-to-trace spacing to ensure proper manufacturing and signal integrity.
3. Impedance Control
Impedance control is a critical aspect of multilayer PCB design, particularly for high-speed and high-frequency circuits. Controlled impedance is achieved by carefully selecting the dielectric material, trace width, and trace spacing to maintain a consistent characteristic impedance throughout the signal path. Common controlled impedance values include 50Ω for single-ended traces and 100Ω for differential pairs.
4. EMI Reduction Techniques
Electromagnetic interference (EMI) can be a significant issue in multilayer PCBs, especially as circuit complexity and operating frequencies increase. Some techniques for reducing EMI in multilayer PCBs include:
- Using dedicated power and ground planes to minimize loop areas
- Implementing proper grounding and shielding techniques
- Applying filters and suppressors to noise-sensitive signals
- Optimizing component placement and routing to minimize crosstalk
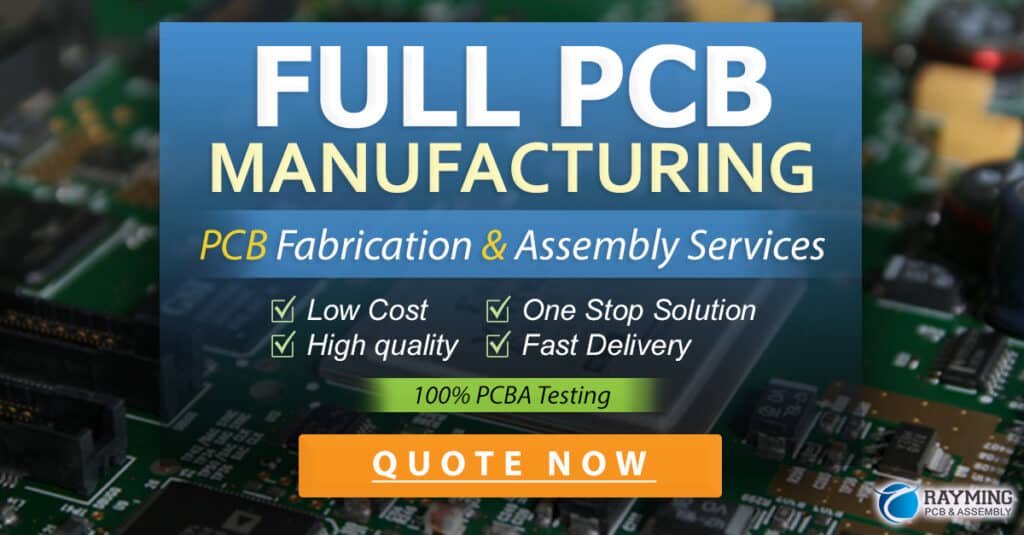
Manufacturing Multilayer PCBs
The manufacturing process for multilayer PCBs is more complex and involves several additional steps compared to single-layer or double-layer PCBs. The basic steps in manufacturing a multilayer PCB include:
-
Inner layer fabrication: The individual inner layers are etched and patterned according to the circuit design.
-
Lamination: The inner layers are aligned and laminated together with the dielectric material under high temperature and pressure.
-
Drilling: Holes are drilled through the laminated board for vias and component mounting.
-
Plating: The drilled holes are plated with copper to create electrical connections between the layers.
-
Outer layer fabrication: The outer layers are etched and patterned, and any additional surface finishes are applied.
-
Solder mask and silkscreen: A solder mask is applied to protect the exposed copper traces, and a silkscreen layer is added for component labeling and identification.
-
Electrical testing: The completed multilayer PCB undergoes electrical testing to ensure proper functionality and adherence to specifications.
Applications of Multilayer PCB
Multilayer PCBs find applications in a wide range of industries and electronic devices, such as:
- Consumer electronics: Smartphones, tablets, laptops, and gaming consoles
- Telecommunications: Routers, switches, and base stations
- Automotive: Engine control units, infotainment systems, and advanced driver assistance systems (ADAS)
- Medical devices: Diagnostic equipment, imaging systems, and wearable monitors
- Aerospace and defense: Avionics, radar systems, and satellite communication devices
- Industrial automation: Programmable logic controllers (PLCs), human-machine interfaces (HMIs), and robotics
Frequently Asked Questions (FAQ)
1. What is the maximum number of layers that can be used in a multilayer PCB?
There is no hard limit to the number of layers in a multilayer PCB, but practical considerations such as manufacturing complexity, cost, and reliability typically limit the number of layers to around 50. Most commercial multilayer PCBs have between 4 and 12 layers.
2. How does the number of layers affect the cost of a multilayer PCB?
The cost of a multilayer PCB generally increases with the number of layers, as each additional layer requires more materials, processing steps, and manufacturing time. However, the cost per unit area may decrease with higher layer counts due to the increased circuit density and smaller overall board size.
3. What are the benefits of using blind and buried vias in a multilayer PCB?
Blind and buried vias offer several advantages over through-hole vias in multilayer PCB design:
- They allow for more efficient use of board space, as they do not occupy all layers of the PCB.
- They can improve signal integrity by reducing the via stub length and minimizing signal reflections.
- They enable more flexible routing options and can help to reduce the overall layer count of the PCB.
4. How does the choice of dielectric material affect the performance of a multilayer PCB?
The dielectric material used in a multilayer PCB can significantly impact its electrical and mechanical properties. Some key factors to consider when selecting a dielectric material include:
- Dielectric constant (Dk): A lower Dk value results in faster signal propagation and lower capacitance, which is desirable for high-speed circuits.
- Dissipation factor (Df): A lower Df value indicates lower signal loss and is preferred for high-frequency applications.
- Thermal stability: The dielectric material should maintain its properties over the expected operating temperature range of the PCB.
- Mechanical strength: The dielectric should provide sufficient mechanical support and dimensional stability to the PCB Structure.
5. What are some common design challenges encountered when working with multilayer PCBs?
Some of the common design challenges associated with multilayer PCBs include:
- Ensuring proper layer stackup and impedance control for optimal signal integrity
- Managing EMI and crosstalk through appropriate layout techniques and component placement
- Minimizing the impact of via stubs and signal reflections on high-speed signals
- Accounting for manufacturing constraints and tolerances in the design process
- Balancing the trade-offs between circuit density, manufacturing complexity, and cost
Conclusion
Multilayer PCBs are an essential component in modern electronic devices, offering increased circuit density, improved signal integrity, and enhanced reliability. By understanding the different layers, design considerations, and manufacturing processes involved in multilayer PCBs, engineers can create more efficient and high-performance electronic systems. As technology continues to advance, the demand for multilayer PCBs with higher layer counts and more complex designs is expected to grow, driving innovation in materials, manufacturing techniques, and design tools.
No responses yet