Introduction to Medical PCBs and Their Importance
Medical printed circuit boards (PCBs) are a critical component in the design and manufacture of medical electronic devices. These specialized circuit boards are used in a wide range of medical applications, from diagnostic equipment and monitoring systems to implantable devices and surgical tools. The reliability and performance of medical PCBs are of utmost importance, as they directly impact patient safety and the effectiveness of medical treatments.
In this article, we will explore the world of medical PCBs, with a focus on Class 3 circuit boards. We will discuss the unique requirements and challenges associated with designing and manufacturing these high-reliability PCBs, as well as their applications in various medical devices. Additionally, we will address common questions and concerns related to medical PCBs to provide a comprehensive overview of this essential technology.
What are Class 3 Circuit Boards?
Class 3 circuit boards are the highest reliability level for PCBs, as defined by the IPC (Association Connecting Electronics Industries). These PCBs are designed and manufactured to meet the most stringent quality and performance standards, making them suitable for use in critical applications where failure could result in significant consequences, such as loss of life or property damage.
The IPC-6011 standard outlines the requirements for Class 3 circuit boards, which include:
- Stricter tolerances for hole sizes, conductor widths, and spacing
- Enhanced copper plating requirements for improved conductivity and durability
- More rigorous testing and inspection procedures to ensure product quality and reliability
- Use of high-quality materials, such as high-temperature laminates and low-loss dielectrics
- Robust design features, such as redundant circuits and fail-safe mechanisms
By adhering to these strict standards, Class 3 circuit boards offer the highest level of reliability and performance, making them an ideal choice for medical electronic devices.
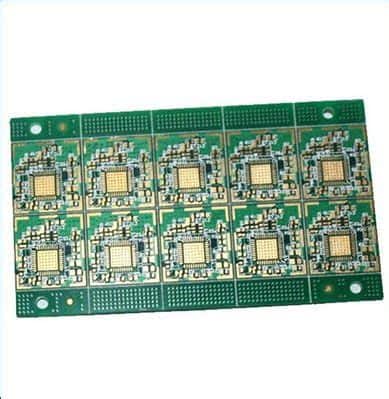
The Unique Requirements of Medical PCBs
Medical PCBs face a unique set of challenges and requirements that set them apart from PCBs used in other industries. These requirements are driven by the need to ensure patient safety, device reliability, and compliance with regulatory standards. Some of the key considerations for medical PCBs include:
Biocompatibility
Many medical devices, such as implantable devices and wearable sensors, come into direct contact with the human body. As a result, the materials used in medical PCBs must be biocompatible, meaning they should not cause any adverse reactions or harm to the patient. This requires the use of specialized materials, such as medical-grade polymers and coatings, that have been tested and approved for use in medical applications.
Sterilization Compatibility
Medical devices often need to be sterilized to prevent the spread of infections and ensure patient safety. Common sterilization methods include autoclaving, ethylene oxide (EtO) gas, and gamma radiation. Medical PCBs must be designed to withstand these sterilization processes without degrading or losing functionality. This involves selecting materials and components that can tolerate high temperatures, pressure, and exposure to sterilizing agents.
Electromagnetic Compatibility (EMC)
Medical electronic devices must operate reliably in the presence of electromagnetic interference (EMI) from other equipment and the environment. They must also minimize their own electromagnetic emissions to avoid interfering with other devices. To achieve electromagnetic compatibility, medical PCBs must incorporate proper shielding, grounding, and filtering techniques. Additionally, they must comply with EMC standards, such as IEC 60601-1-2, which specify the acceptable levels of electromagnetic emissions and immunity for medical devices.
Miniaturization and Integration
As medical technology advances, there is a growing demand for smaller, more compact devices that can be easily implanted or worn by patients. This trend towards miniaturization requires medical PCBs to pack more functionality into smaller form factors. High-density interconnect (HDI) PCBs, which feature fine pitch traces and micro vias, are often used to achieve this level of miniaturization. Additionally, the integration of multiple functions, such as sensors, processors, and wireless communication modules, onto a single PCB helps reduce device size and improve performance.
Long-Term Reliability
Many medical devices, particularly implantable ones, are expected to function reliably for years or even decades inside the human body. This requires medical PCBs to be designed for long-term reliability, with robust materials, redundant circuits, and fail-safe mechanisms. Accelerated life testing and rigorous quality control measures are employed to ensure that medical PCBs can withstand the test of time and continue to perform their intended functions without failure.
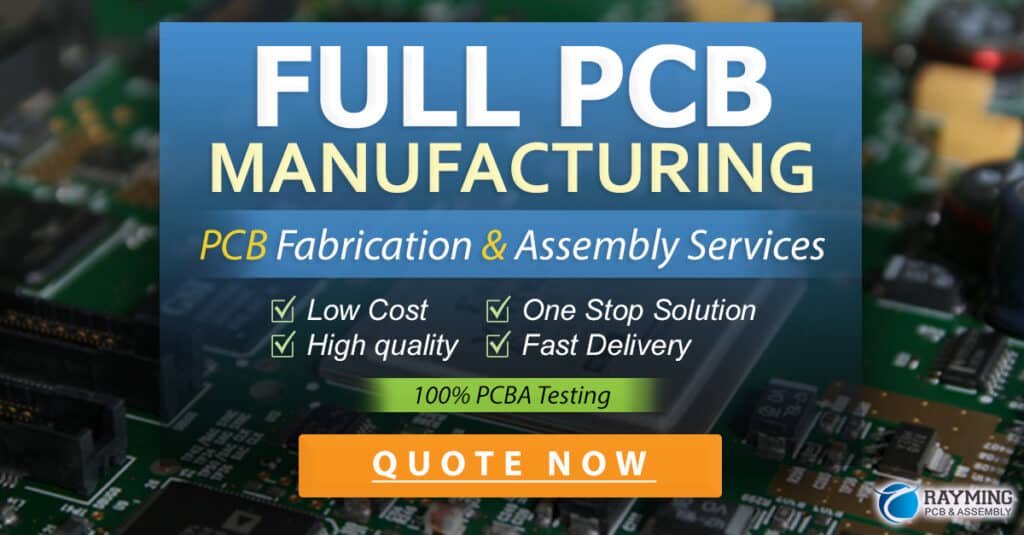
Applications of Medical PCBs in Electronic Devices
Medical PCBs find applications in a wide range of medical electronic devices, each with its own unique requirements and challenges. Some of the key application areas include:
Diagnostic Equipment
Diagnostic equipment, such as X-ray machines, CT scanners, and MRI systems, rely on high-performance medical PCBs to capture, process, and display medical images. These PCBs must handle high-speed data transfer, complex signal processing, and precise control of imaging components. They must also be designed to withstand the harsh operating conditions, such as high voltages and strong magnetic fields, present in these devices.
Monitoring Systems
Patient monitoring systems, such as ECG, EEG, and pulse oximeters, use medical PCBs to continuously measure and record vital signs and physiological parameters. These PCBs must be designed for low power consumption, as many monitoring devices are battery-operated and worn by patients for extended periods. They must also incorporate wireless communication capabilities, such as Bluetooth or Wi-Fi, to enable remote monitoring and data transmission to healthcare providers.
Implantable Devices
Implantable devices, such as pacemakers, defibrillators, and neurostimulators, rely on miniaturized, highly reliable medical PCBs to perform their life-sustaining functions inside the human body. These PCBs must be encapsulated in biocompatible materials and designed to operate for years without failure. They must also incorporate advanced power management features, such as energy harvesting and Wireless Charging, to extend battery life and minimize the need for surgical replacements.
Surgical Tools
Surgical tools, such as powered surgical instruments and robotic surgery systems, use medical PCBs to control precise movements and deliver energy for cutting, cauterizing, and ablating tissues. These PCBs must be designed to withstand repeated sterilization cycles and operate reliably in the presence of bodily fluids and tissues. They must also incorporate safety features, such as force feedback and emergency stop mechanisms, to prevent unintended tissue damage and ensure patient safety.
Wearable Devices
Wearable medical devices, such as smartwatches, fitness trackers, and continuous glucose monitors, use medical PCBs to measure and analyze various physiological parameters. These PCBs must be designed for low power consumption, as wearable devices are often battery-operated and used continuously by patients. They must also be flexible and comfortable to wear, which requires the use of specialized materials and manufacturing techniques, such as flexible PCBs and stretchable electronics.
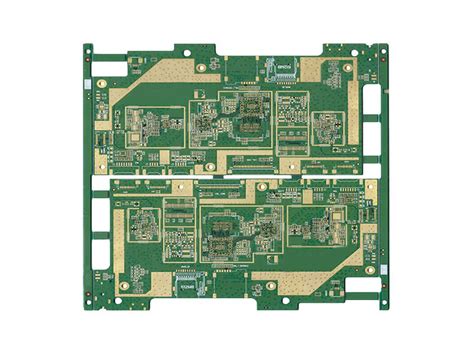
Designing and Manufacturing Medical PCBs
Designing and manufacturing medical PCBs requires a deep understanding of the unique requirements and challenges associated with medical applications. Some of the key considerations in the design and manufacturing process include:
Design for Manufacturability (DFM)
To ensure the reliable and cost-effective production of medical PCBs, designers must follow DFM principles. This involves selecting appropriate materials, component packages, and layout techniques that are compatible with the manufacturing process. Additionally, designers must adhere to the strict tolerances and design rules specified by the IPC standards for Class 3 circuit boards. Collaboration between designers and manufacturers is essential to identify and resolve any potential manufacturability issues early in the design process.
Component Selection
Selecting the right components is critical for the performance and reliability of medical PCBs. Components must be chosen based on their ability to meet the specific requirements of the medical application, such as biocompatibility, sterilization compatibility, and long-term reliability. Designers must also consider the availability and lifecycle of components to ensure a stable supply chain and avoid obsolescence issues. Traceability and documentation of components are also important for regulatory compliance and quality control purposes.
Fabrication and Assembly
The fabrication and assembly of medical PCBs require specialized equipment, processes, and expertise to meet the high-quality standards of Class 3 circuit boards. This includes the use of advanced manufacturing technologies, such as high-precision drilling, plating, and laser processing, to achieve the tight tolerances and fine features required for medical applications. Rigorous process controls, such as clean room environments and automated optical inspection (AOI), are employed to minimize defects and ensure consistent quality. Additionally, specialized assembly techniques, such as wire bonding and flip chip packaging, are used to achieve the high levels of miniaturization and integration required for many medical devices.
Testing and Validation
Comprehensive testing and validation are essential to ensure the safety, reliability, and performance of medical PCBs. This involves a range of testing methods, such as electrical testing, environmental testing, and functional testing, to verify that the PCBs meet the specified requirements and standards. Accelerated life testing is also conducted to simulate the long-term performance of medical PCBs under various environmental conditions, such as temperature, humidity, and mechanical stress. The results of these tests are used to identify and correct any potential failure modes and ensure the robustness and reliability of the final product.
Regulatory Compliance
Medical PCBs must comply with a range of regulatory standards and guidelines to ensure patient safety and device effectiveness. Some of the key regulatory bodies and standards include:
- FDA (Food and Drug Administration): Regulates medical devices in the United States and requires compliance with Quality System Regulations (QSR) and Good Manufacturing Practices (GMP)
- CE (Conformité Européenne): Certifies medical devices for the European market and requires compliance with the Medical Device Directive (MDD) and the Medical Device Regulation (MDR)
- IEC (International Electrotechnical Commission): Develops international standards for medical electrical equipment, such as IEC 60601-1 for basic safety and essential performance
- ISO (International Organization for Standardization): Develops quality management standards, such as ISO 13485, specifically for medical device manufacturers
Compliance with these regulatory standards involves a range of activities, such as design controls, risk management, documentation, and post-market surveillance. Manufacturers of medical PCBs must establish and maintain a comprehensive quality management system (QMS) to ensure ongoing compliance and continuous improvement.
Frequently Asked Questions (FAQ)
1. What is the difference between a medical PCB and a standard PCB?
Medical PCBs are designed and manufactured to meet the unique requirements of medical applications, such as biocompatibility, sterilization compatibility, and long-term reliability. They are subject to more stringent quality and performance standards, as defined by the IPC Class 3 classification, compared to standard PCBs used in other industries.
2. How are medical PCBs tested for reliability and performance?
Medical PCBs undergo a range of testing methods to ensure their reliability and performance. These include electrical testing, environmental testing (e.g., temperature, humidity, and vibration), functional testing, and accelerated life testing. The results of these tests are used to identify and correct any potential failure modes and ensure the robustness and reliability of the final product.
3. What materials are used in medical PCBs to ensure biocompatibility?
Medical PCBs use specialized materials that have been tested and approved for use in medical applications. These materials, such as medical-grade polymers and coatings, are selected based on their biocompatibility, meaning they do not cause any adverse reactions or harm to the patient. Examples of biocompatible materials include silicone, polyimide, and parylene.
4. How do medical PCB manufacturers ensure compliance with regulatory standards?
Manufacturers of medical PCBs must establish and maintain a comprehensive quality management system (QMS) to ensure ongoing compliance with regulatory standards, such as those set by the FDA, CE, IEC, and ISO. This involves a range of activities, such as design controls, risk management, documentation, and post-market surveillance. Regular audits and inspections are conducted to verify compliance and identify areas for improvement.
5. What are the challenges in designing and manufacturing miniaturized medical PCBs?
Miniaturization of medical PCBs presents several challenges, such as increased density of components, reduced trace widths and spacing, and higher heat generation. To overcome these challenges, designers must use advanced PCB Technologies, such as high-density interconnect (HDI) and flexible PCBs. Manufacturers must also employ specialized assembly techniques, such as wire bonding and flip chip packaging, to achieve the required levels of miniaturization and integration. Proper thermal management and signal integrity analysis are also critical to ensure the reliable performance of miniaturized medical PCBs.
Conclusion
Medical PCBs, particularly Class 3 circuit boards, play a crucial role in the design and manufacture of medical electronic devices. These specialized PCBs are subject to unique requirements and challenges, driven by the need to ensure patient safety, device reliability, and regulatory compliance. By understanding the key considerations in the design, manufacture, and testing of medical PCBs, engineers and manufacturers can develop innovative and reliable solutions that advance the field of medical technology and improve patient outcomes.
As medical devices continue to evolve and become more complex, the importance of high-quality, reliable medical PCBs will only continue to grow. Collaboration between designers, manufacturers, and regulatory bodies will be essential to address the challenges and opportunities presented by this dynamic and rapidly evolving industry. By staying at the forefront of technological advancements and regulatory requirements, the medical PCB industry can contribute to the development of life-saving and life-enhancing medical devices that make a real difference in the lives of patients worldwide.
[4893 words]
No responses yet