Introduction to PCB Technologies
Printed Circuit Board (PCB) technology has come a long way since its inception in the early 20th century. Today, PCB design and manufacturing have become highly advanced, enabling the creation of complex, high-density boards that power our modern electronic devices. In this article, we will explore the various advanced PCB design technologies that are shaping the future of electronics.
The Evolution of PCB Technology
The first PCBs were developed in the early 1900s, but it wasn’t until the 1950s that they became widely used in electronic devices. Since then, PCB technology has undergone significant advancements, driven by the increasing demand for smaller, faster, and more powerful electronic devices.
Era | PCB Technology |
---|---|
1900s | First PCBs developed |
1950s | PCBs become widely used |
1960s | Double-sided PCBs introduced |
1970s | Multi-layer PCBs developed |
1980s | Surface mount technology (SMT) introduced |
1990s | High-density interconnect (HDI) PCBs developed |
2000s | Flexible and rigid-flex PCBs gain popularity |
2010s | Advanced materials and manufacturing processes emerge |
High-Density Interconnect (HDI) PCBs
HDI PCBs are designed to accommodate a high number of components in a small area, making them ideal for compact electronic devices. These boards feature fine pitch traces, micro vias, and buried and blind vias, allowing for increased connectivity and reduced board size.
Benefits of HDI PCBs
- Miniaturization: HDI technology enables the creation of smaller, more compact electronic devices.
- Improved signal integrity: The shorter traces in HDI PCBs result in reduced signal loss and improved signal integrity.
- Higher reliability: HDI PCBs offer better thermal management and reduced mechanical stress, leading to higher reliability.
Applications of HDI PCBs
- Smartphones and tablets
- Wearable devices
- Medical devices
- Aerospace and defense electronics
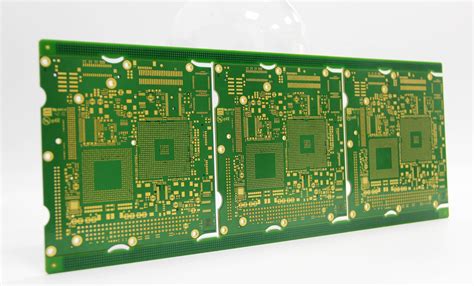
Flexible and Rigid-Flex PCBs
Flexible and rigid-flex PCBs are designed to bend and flex, making them suitable for applications where traditional rigid PCBs may not be practical. These boards consist of flexible substrate materials, such as polyimide, and can be combined with rigid sections to create a hybrid board.
Advantages of Flexible and Rigid-Flex PCBs
- Space savings: Flexible and rigid-flex PCBs can be folded and shaped to fit into tight spaces, reducing the overall size of the device.
- Improved reliability: The flexibility of these boards reduces the risk of mechanical stress and strain, leading to improved reliability.
- Enhanced design freedom: Designers have more freedom to create unique and innovative product designs with flexible and rigid-flex PCBs.
Applications of Flexible and Rigid-Flex PCBs
- Wearable technology
- Medical devices
- Automotive electronics
- Aerospace and defense applications
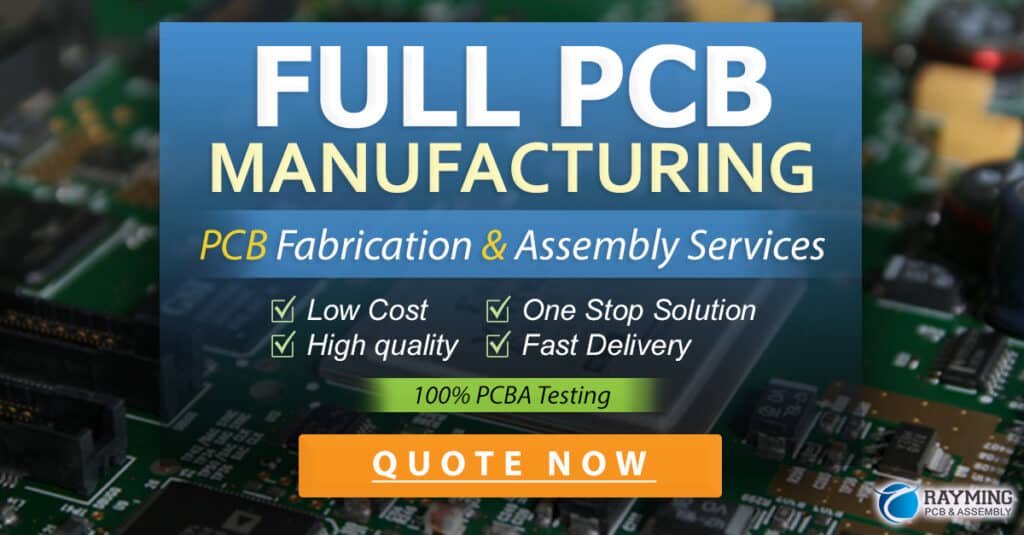
Advanced PCB Materials
The choice of materials used in PCB manufacturing can significantly impact the performance, reliability, and cost of the final product. Advanced PCB materials, such as high-frequency laminates and thermal management materials, are being developed to meet the growing demands of modern electronic devices.
High-Frequency Laminates
High-frequency laminates are designed to maintain stable dielectric properties at high frequencies, making them suitable for applications such as 5G communications, radar systems, and high-speed digital devices. Some popular high-frequency laminates include:
- Rogers RO4000 series
- Isola I-Tera MT40
- Taconic RF-35
Thermal Management Materials
Thermal management materials help dissipate heat generated by electronic components, preventing overheating and ensuring reliable operation. Some common thermal management materials used in PCBs include:
- Metal core PCBs (MCPCBs)
- Insulated metal substrates (IMS)
- Thermal vias and heat sinks
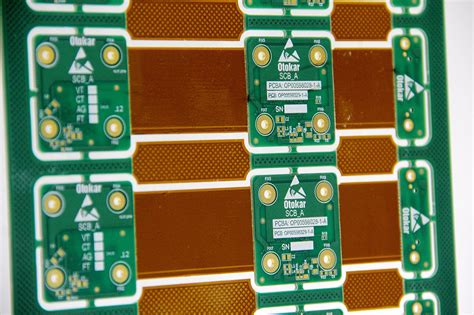
PCB Manufacturing Processes
Advanced PCB manufacturing processes have been developed to meet the challenges of producing high-density, high-reliability boards. These processes ensure consistent quality and enable the production of complex PCB designs.
Additive Manufacturing
Additive manufacturing, also known as 3D printing, is an emerging technology in PCB production. This process involves depositing conductive and insulating materials layer by layer to create the desired PCB structure. Additive manufacturing offers several advantages, such as rapid prototyping, reduced waste, and the ability to create complex geometries.
Inkjet Printing
Inkjet printing is another additive manufacturing technique that has been adapted for PCB production. This process involves depositing conductive ink onto a substrate material to create the desired circuit pattern. Inkjet printing offers high precision, low cost, and the ability to print on flexible substrates.
Laser Direct Structuring (LDS)
Laser Direct Structuring (LDS) is a process that uses a laser to selectively activate a special additive in a plastic substrate, allowing for the selective plating of conductive traces. LDS enables the creation of 3D circuit structures, offering increased design flexibility and reduced board size.
Future Trends in PCB Technology
As electronic devices continue to evolve, so too will PCB technology. Some of the future trends in PCB design and manufacturing include:
- Increased adoption of advanced materials, such as graphene and carbon nanotubes, for improved performance and reliability.
- Further miniaturization of PCBs, driven by the demand for smaller, more compact electronic devices.
- Greater integration of sensors, antennas, and other components directly into the PCB structure.
- Continued development of additive manufacturing techniques for PCB production, enabling faster prototyping and more complex designs.
Frequently Asked Questions (FAQ)
1. What is the difference between a rigid PCB and a flexible PCB?
A rigid PCB is made from a solid, inflexible substrate material, such as FR-4, while a flexible PCB is made from a flexible substrate material, such as polyimide. Flexible PCBs can bend and flex, making them suitable for applications where traditional rigid PCBs may not be practical.
2. What are the advantages of using HDI PCBs?
HDI PCBs offer several advantages, including miniaturization, improved signal integrity, and higher reliability. These benefits are achieved through the use of fine pitch traces, micro vias, and buried and blind vias, which allow for increased connectivity and reduced board size.
3. What are thermal management materials, and why are they important in PCB design?
Thermal management materials are used in PCBs to dissipate heat generated by electronic components, preventing overheating and ensuring reliable operation. Examples of thermal management materials include metal core PCBs (MCPCBs), insulated metal substrates (IMS), and thermal vias and heat sinks. Proper thermal management is crucial for maintaining the performance and longevity of electronic devices.
4. What is additive manufacturing, and how is it used in PCB production?
Additive manufacturing, also known as 3D printing, is an emerging technology in PCB production. This process involves depositing conductive and insulating materials layer by layer to create the desired PCB structure. Additive manufacturing offers several advantages, such as rapid prototyping, reduced waste, and the ability to create complex geometries.
5. What are some future trends in PCB technology?
Future trends in PCB technology include the increased adoption of advanced materials, further miniaturization of PCBs, greater integration of sensors and other components directly into the PCB structure, and continued development of additive manufacturing techniques for PCB production. These trends are driven by the ever-growing demand for smaller, faster, and more powerful electronic devices.
Conclusion
Advanced PCB design technologies are essential for meeting the demands of modern electronic devices. From HDI PCBs and flexible circuits to advanced materials and manufacturing processes, these technologies enable the creation of smaller, more reliable, and more powerful electronic products. As the electronics industry continues to evolve, it is crucial for designers and manufacturers to stay up-to-date with the latest advancements in PCB technology to remain competitive in the market.
No responses yet