Introduction to Inventory Management and BOM
Inventory management is a crucial aspect of any manufacturing business, especially when it comes to managing Bill of Materials (BOM) inventory. A BOM is a comprehensive list of all the raw materials, components, and subassemblies required to manufacture a finished product. Effective BOM inventory management ensures that production runs smoothly, minimizes downtime, and helps control costs.
In this article, we will explore the key concepts of BOM inventory management, best practices, and strategies to optimize your inventory for efficient production runs.
The Importance of BOM Inventory Management
Ensuring Smooth Production Runs
One of the primary goals of BOM inventory management is to ensure that production runs smoothly without interruptions due to material shortages. By maintaining accurate inventory levels and forecasting demand, manufacturers can avoid stockouts and keep production lines running at optimal capacity.
Reducing Inventory Carrying Costs
Efficient BOM inventory management helps reduce inventory carrying costs by minimizing excess stock and preventing obsolescence. By analyzing historical data and demand patterns, manufacturers can determine the optimal inventory levels for each component, reducing the need for excess safety stock.
Improving Cash Flow
Effective BOM inventory management can improve cash flow by reducing the amount of working capital tied up in inventory. By implementing just-in-time (JIT) inventory practices and establishing strong supplier relationships, manufacturers can minimize inventory holding costs and free up cash for other business needs.
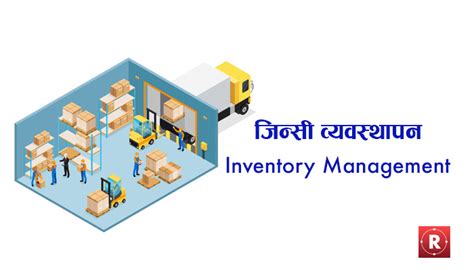
Key Components of BOM Inventory Management
Accurate Inventory Tracking
Accurate inventory tracking is the foundation of effective BOM inventory management. Manufacturers must implement systems and processes to monitor inventory levels, track material movements, and maintain accurate records of stock on hand.
Inventory Tracking Method | Description |
---|---|
Barcode Scanning | Scanning barcodes on materials and components to track movements and update inventory records in real-time. |
RFID Technology | Using radio-frequency identification (RFID) tags to automatically track inventory movements and levels. |
Inventory Management Software | Implementing specialized software to manage inventory data, generate reports, and provide real-time visibility into stock levels. |
Demand Forecasting
Accurate demand forecasting is essential for Optimizing BOM inventory levels. By analyzing historical sales data, market trends, and customer demand patterns, manufacturers can predict future material requirements and adjust inventory levels accordingly.
Demand Forecasting Technique | Description |
---|---|
Time Series Analysis | Using historical data to identify patterns and trends in demand over time. |
Regression Analysis | Analyzing the relationship between demand and various factors such as price, promotions, and economic conditions. |
Collaborative Forecasting | Working with customers and suppliers to share information and develop more accurate demand forecasts. |
Supplier Relationship Management
Strong supplier relationships are crucial for ensuring a reliable supply of materials and components. Manufacturers should work closely with suppliers to establish clear communication channels, negotiate favorable terms, and develop contingency plans for potential supply chain disruptions.
Supplier Relationship Management Strategy | Description |
---|---|
Supplier Scorecards | Evaluating supplier performance based on key metrics such as quality, delivery, and cost. |
Supplier Collaboration | Working with suppliers to develop joint forecasts, share information, and identify opportunities for improvement. |
Supplier Diversification | Maintaining a diverse supplier base to mitigate the risk of supply chain disruptions and ensure a steady supply of materials. |
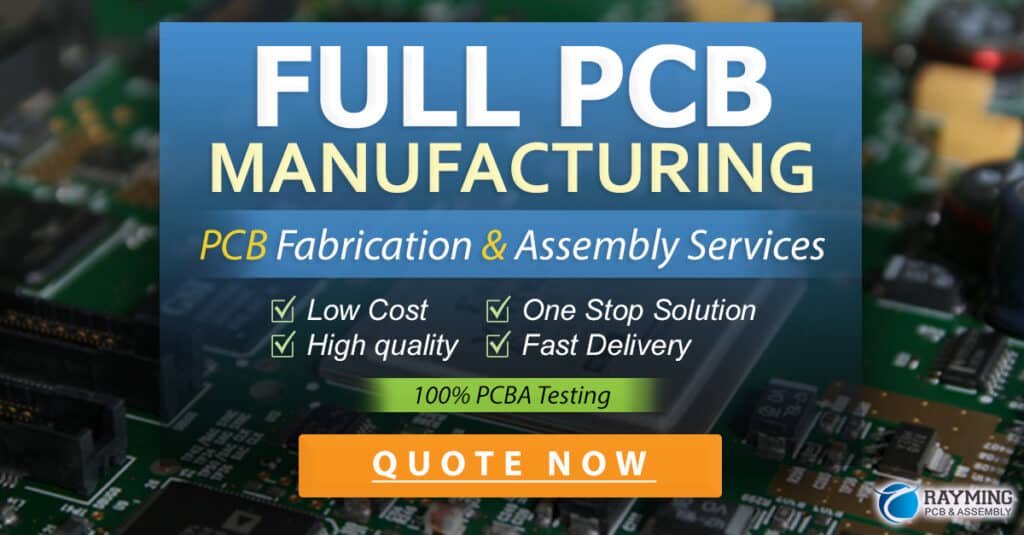
Implementing BOM Inventory Management Best Practices
ABC Analysis
ABC analysis is a method of categorizing inventory based on its value and importance. By classifying items as A (high value, low quantity), B (medium value, medium quantity), or C (low value, high quantity), manufacturers can prioritize inventory management efforts and focus on the most critical items.
ABC Category | Description | Inventory Management Strategy |
---|---|---|
A Items | High value, low quantity | Tight control, frequent monitoring, and precise forecasting |
B Items | Medium value, medium quantity | Moderate control, regular monitoring, and reasonable forecasting |
C Items | Low value, high quantity | Loose control, periodic monitoring, and simple forecasting |
Safety Stock Calculation
Safety stock is an additional quantity of inventory held to protect against uncertainties in demand and supply. To calculate appropriate safety stock levels, manufacturers should consider factors such as lead time, demand variability, and service level targets.
Safety Stock Formula:
Safety Stock = Z * σ * √(LT)
Where:
– Z = Safety factor (based on desired service level)
– σ = Standard deviation of demand
– LT = Lead time
Inventory Optimization Techniques
Inventory optimization involves finding the right balance between inventory levels, service levels, and costs. Some common inventory optimization techniques include:
Technique | Description |
---|---|
Economic Order Quantity (EOQ) | Determining the optimal order quantity that minimizes total inventory costs, including ordering and holding costs. |
Reorder Point (ROP) | Setting the inventory level at which a new order should be placed to maintain adequate stock levels. |
Lot Sizing | Determining the most economical production or purchase quantity to minimize setup costs and inventory holding costs. |
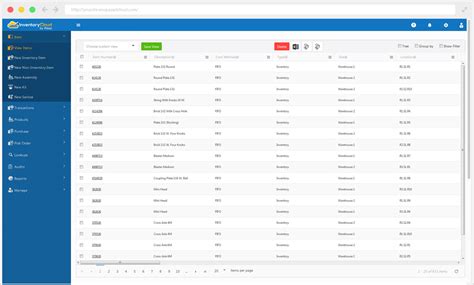
Continuous Improvement in BOM Inventory Management
Measuring and Monitoring Inventory Performance
To continuously improve BOM inventory management, manufacturers must establish key performance indicators (KPIs) and regularly monitor inventory performance. Some common inventory management KPIs include:
KPI | Description |
---|---|
Inventory Turnover Ratio | Measures how quickly inventory is sold and replaced, indicating the efficiency of inventory management. |
Stock Accuracy | Measures the percentage of inventory records that match actual physical stock levels. |
Stock-Out Frequency | Measures the number of times a stockout occurs within a given period, indicating the effectiveness of inventory planning. |
Conducting Regular Inventory Audits
Regular inventory audits help ensure the accuracy of inventory records and identify areas for improvement. Manufacturers should conduct physical counts, reconcile discrepancies, and investigate the root causes of any errors or inconsistencies.
Continuous Improvement Methodologies
Implementing continuous improvement methodologies, such as Lean Manufacturing and Six Sigma, can help manufacturers streamline inventory management processes, reduce waste, and improve overall efficiency.
Methodology | Description |
---|---|
Lean Manufacturing | Focuses on eliminating waste, reducing inventory, and improving flow through techniques like just-in-time (JIT) inventory and kanban systems. |
Six Sigma | Emphasizes data-driven decision making and process improvement through the DMAIC (Define, Measure, Analyze, Improve, Control) framework. |
Frequently Asked Questions (FAQ)
-
What is the difference between BOM and inventory management?
A: A BOM (Bill of Materials) is a list of all the components and materials required to manufacture a finished product, while inventory management refers to the processes and strategies used to control and optimize inventory levels, including BOM components. -
How often should I update my BOM inventory records?
A: BOM inventory records should be updated in real-time or as close to real-time as possible to ensure accurate inventory tracking and decision-making. The frequency of updates may depend on the complexity of your manufacturing process and the systems you have in place. -
What is the best way to manage inventory for products with a short shelf life?
A: For products with a short shelf life, it’s essential to implement first-in, first-out (FIFO) inventory management practices, closely monitor expiration dates, and maintain accurate demand forecasts to minimize waste and ensure optimal inventory turnover. -
How can I improve collaboration with suppliers for better BOM inventory management?
A: To improve collaboration with suppliers, consider implementing supplier scorecards, establishing regular communication channels, and sharing demand forecasts and production plans. Collaborative planning, forecasting, and replenishment (CPFR) initiatives can also help align supply chain activities and improve overall performance. -
What role does technology play in BOM inventory management?
A: Technology plays a crucial role in BOM inventory management by enabling real-time inventory tracking, automating data collection and analysis, and providing tools for demand forecasting and inventory optimization. Inventory management software, enterprise resource planning (ERP) systems, and industrial IoT solutions can all contribute to more efficient and effective BOM inventory management.
Conclusion
Effective BOM inventory management is essential for ensuring smooth production runs, controlling costs, and improving overall manufacturing performance. By implementing best practices such as accurate inventory tracking, demand forecasting, and supplier relationship management, manufacturers can optimize their inventory levels and minimize the risk of stockouts or excess stock.
Continuous improvement methodologies, regular performance monitoring, and the adoption of advanced technologies can further enhance BOM inventory management processes and contribute to long-term success in today’s competitive manufacturing landscape.
No responses yet