What is SMT PCB Assembly?
SMT PCB Assembly is a method of assembling electronic circuits in which the components are mounted directly onto the surface of a PCB. This is in contrast to through-hole technology (THT), where the components are inserted into holes drilled in the PCB and soldered to pads on the opposite side.
SMT PCB assembly offers several advantages over THT, including:
- Smaller component sizes
- Higher component density
- Faster assembly speeds
- Lower production costs
- Improved reliability
Advantages of SMT PCB Assembly
-
Smaller Component Sizes: SMDs are much smaller than their through-hole counterparts, allowing for more compact PCB designs. This is particularly important in today’s electronics industry, where devices are becoming increasingly miniaturized.
-
Higher Component Density: With SMDs, it is possible to place more components on a single PCB, resulting in higher component density. This allows for more complex circuits to be built in a smaller footprint.
-
Faster Assembly Speeds: SMT PCB assembly is a highly automated process, with pick-and-place machines capable of placing thousands of components per hour. This results in faster assembly speeds compared to manual THT assembly.
-
Lower Production Costs: The automation of SMT PCB assembly reduces labor costs and minimizes human error. Additionally, the smaller size of SMDs means that less PCB material is required, further reducing production costs.
-
Improved Reliability: SMDs have shorter lead lengths and are less susceptible to mechanical stress than through-hole components. This results in improved reliability and reduced failure rates.
The SMT PCB Assembly Process
The SMT PCB assembly process consists of several key steps, each of which must be carefully controlled to ensure high-quality results.
1. Solder Paste Application
The first step in SMT PCB assembly is the application of solder paste to the PCB. Solder paste is a mixture of tiny solder spheres suspended in a flux medium. The paste is applied to the PCB using a stencil printing process, where a stencil with openings corresponding to the component pads is placed over the PCB. The solder paste is then spread over the stencil using a squeegee, depositing it onto the pads.
2. Component Placement
Once the solder paste has been applied, the next step is to place the SMDs onto the PCB. This is typically done using a pick-and-place machine, which uses a vacuum nozzle to pick up the components from a reel or tray and place them onto the PCB with high precision.
3. Reflow Soldering
After the components have been placed, the PCB is sent through a reflow oven. The reflow oven heats the PCB to a temperature high enough to melt the solder paste, typically around 220-250°C. As the solder melts, it forms a strong mechanical and electrical bond between the component leads and the PCB pads.
4. Inspection and Testing
Once the reflow soldering process is complete, the PCB undergoes a series of inspections and tests to ensure that all components are properly soldered and functioning correctly. This may include visual inspection, automated optical inspection (AOI), X-ray inspection, and functional testing.
Best Practices for SMT PCB Assembly
To achieve high-quality results in SMT PCB assembly, it is important to follow best practices at each stage of the process.
PCB Design
- Use a grid-based layout to ensure consistent component spacing
- Follow the manufacturer’s recommendations for pad sizes and shapes
- Provide adequate clearance between components to avoid short circuits
- Use thermal relief pads for components that generate significant heat
Solder Paste Application
- Use a high-quality solder paste with the appropriate particle size and flux type
- Ensure that the stencil is properly aligned with the PCB
- Control the printing process parameters, such as squeegee pressure and speed
- Regularly inspect and clean the stencil to prevent clogging
Component Placement
- Use a pick-and-place machine with high accuracy and repeatability
- Ensure that the component feeders are properly loaded and aligned
- Optimize the placement sequence to minimize the risk of component shifting
- Verify the placement accuracy using vision systems or manual inspection
Reflow Soldering
- Use a reflow oven with accurate temperature control and a well-designed heating profile
- Monitor the oven temperature and conveyor speed to ensure consistent results
- Use nitrogen atmosphere to reduce oxidation and improve solder joint quality
- Regularly calibrate and maintain the reflow oven to ensure optimal performance
Inspection and Testing
- Implement a comprehensive inspection and testing plan
- Use automated optical inspection (AOI) to detect solder defects and component placement errors
- Perform X-ray inspection to detect hidden defects, such as voids or insufficient solder
- Conduct functional testing to verify that the assembled PCB meets the required specifications
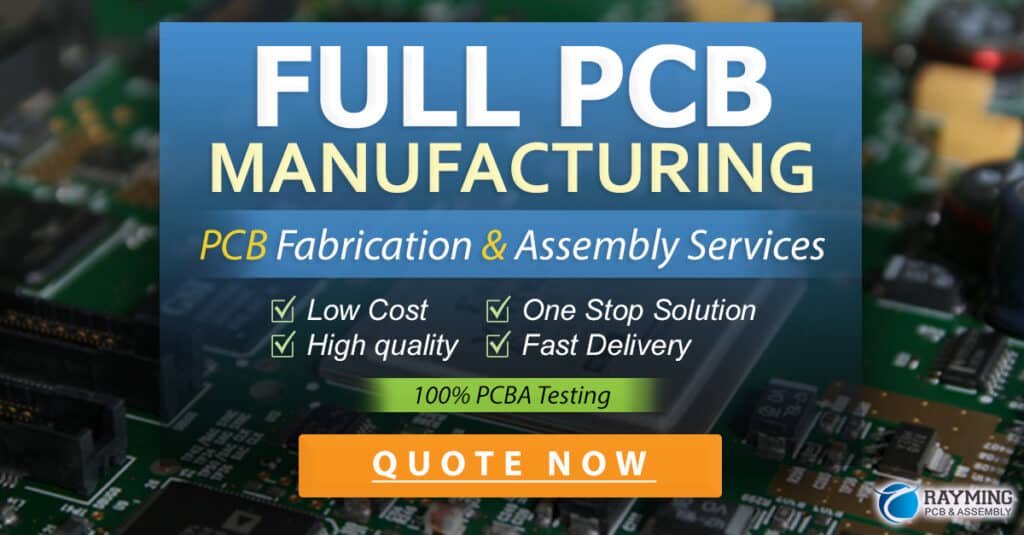
Conclusion
SMT PCB assembly is a complex process that requires careful control and attention to detail at every stage. By following best practices in PCB design, solder paste application, component placement, reflow soldering, and inspection and testing, it is possible to achieve high-quality, reliable PCB assemblies that meet the demands of today’s electronics industry.
Frequently Asked Questions (FAQ)
1. What is the difference between SMT and THT PCB assembly?
SMT (surface-mount technology) PCB assembly involves placing components directly onto the surface of the PCB, while THT (through-hole technology) PCB assembly involves inserting component leads through holes in the PCB and soldering them to pads on the opposite side.
2. What are the advantages of SMT PCB assembly over THT?
SMT PCB assembly offers several advantages over THT, including smaller component sizes, higher component density, faster assembly speeds, lower production costs, and improved reliability.
3. What is solder paste, and how is it applied in SMT PCB assembly?
Solder paste is a mixture of tiny solder spheres suspended in a flux medium. It is applied to the PCB using a stencil printing process, where a stencil with openings corresponding to the component pads is placed over the PCB, and the paste is spread over the stencil using a squeegee.
4. What is a reflow oven, and what is its role in SMT PCB assembly?
A reflow oven is a specialized oven used in SMT PCB assembly to melt the solder paste and form a strong mechanical and electrical bond between the component leads and the PCB pads. The oven heats the PCB to a temperature high enough to melt the solder paste, typically around 220-250°C.
5. What kinds of inspections and tests are performed after SMT PCB assembly?
After SMT PCB assembly, the PCB undergoes a series of inspections and tests to ensure that all components are properly soldered and functioning correctly. This may include visual inspection, automated optical inspection (AOI), X-ray inspection, and functional testing.
Stage | Best Practices |
---|---|
PCB Design | – Use a grid-based layout – Follow manufacturer’s recommendations for pad sizes and shapes – Provide adequate clearance between components – Use thermal relief pads for heat-generating components |
Solder Paste Application | – Use high-quality solder paste with appropriate particle size and flux type – Ensure proper stencil alignment – Control printing process parameters – Regularly inspect and clean the stencil |
Component Placement | – Use a high-accuracy pick-and-place machine – Ensure proper component feeder loading and alignment – Optimize placement sequence – Verify placement accuracy |
Reflow Soldering | – Use a reflow oven with accurate temperature control and well-designed heating profile – Monitor oven temperature and conveyor speed – Use nitrogen atmosphere to reduce oxidation – Regularly calibrate and maintain the reflow oven |
Inspection and Testing | – Implement a comprehensive inspection and testing plan – Use automated optical inspection (AOI) – Perform X-ray inspection – Conduct functional testing |
No responses yet