What is Innerlayer Imaging in PCB Manufacturing?
Innerlayer imaging, also known as primary imaging, is a crucial step in the manufacturing process of multilayer printed circuit boards (PCBs). It involves transferring the designed circuit pattern onto the copper-clad laminates that make up the inner layers of the PCB. The accuracy and precision of innerlayer imaging directly impact the functionality and reliability of the final PCB product.
Importance of Innerlayer Imaging
Innerlayer imaging is essential for several reasons:
-
Circuit Pattern Transfer: It allows the designed circuit pattern to be accurately transferred onto the copper-clad laminates, ensuring that the PCB functions as intended.
-
Interconnectivity: Proper innerlayer imaging enables the creation of precise interconnections between different layers of the PCB through vias and plated through-holes.
-
Signal Integrity: Accurate innerlayer imaging helps maintain signal integrity by ensuring that the copper traces are properly defined and spaced, minimizing issues such as crosstalk and signal distortion.
-
Reliability: Well-executed innerlayer imaging contributes to the overall reliability of the PCB by preventing short circuits, open circuits, and other manufacturing defects.
Innerlayer Imaging Techniques
There are several techniques used for innerlayer imaging in PCB manufacturing. The choice of technique depends on factors such as the PCB Design complexity, required resolution, and production volume. Let’s explore some of the commonly used innerlayer imaging methods.
1. Photo Plotting
Photo plotting is a traditional innerlayer imaging technique that involves using a photoplotter machine to expose the circuit pattern onto a photographic film. The process is as follows:
- The PCB design files (usually in Gerber format) are loaded into the photoplotter machine.
- The machine uses a high-intensity light source and a precise optical system to expose the circuit pattern onto a photosensitive film.
- The exposed film is then developed, resulting in a clear and dark pattern representing the circuit design.
- The developed film is used as a mask for the subsequent etching process.
Photo plotting offers high resolution and accuracy, making it suitable for complex PCB designs. However, it is a relatively slow process and requires the use of photographic films, which can be costly.
2. Laser Direct Imaging (LDI)
Laser Direct Imaging (LDI) is a more advanced innerlayer imaging technique that uses a laser to directly expose the circuit pattern onto the photoresist-coated copper-clad laminate. The process eliminates the need for photographic films and offers several advantages:
-
Higher Precision: LDI systems can achieve resolutions down to 25 microns, enabling the creation of fine-pitch traces and high-density PCB designs.
-
Improved Registration: Direct imaging ensures better layer-to-layer registration accuracy, which is crucial for multilayer PCBs.
-
Faster Turnaround: LDI eliminates the need for film preparation and development, reducing the overall processing time and enabling faster production cycles.
-
Cost-Effective: By eliminating the use of photographic films, LDI reduces material costs and waste generation.
LDI systems use either UV or visible light lasers, depending on the photoresist material used. The laser beam is precisely controlled and focused onto the photoresist-coated laminate, selectively exposing the desired areas based on the PCB design data.
3. Inkjet Printing
Inkjet printing is an emerging innerlayer imaging technique that uses specialized inkjet printers to directly deposit the circuit pattern onto the copper-clad laminate. This method offers several benefits:
-
Additive Process: Unlike traditional subtractive methods that involve etching away unwanted copper, inkjet printing is an additive process, depositing the conductive ink only where needed. This reduces material waste and environmental impact.
-
Design Flexibility: Inkjet printing allows for easy modifications and customization of the circuit pattern, as the design can be directly printed onto the laminate without the need for masks or films.
-
Cost-Effective for Low Volumes: Inkjet printing is particularly suitable for low-volume production or prototyping, as it eliminates the need for expensive tooling and setup costs associated with traditional methods.
However, inkjet printing currently has limitations in terms of resolution and speed compared to photo plotting and LDI. As the technology advances, it is expected to become a more viable option for large-scale PCB production.
Innerlayer Imaging Process Flow
The innerlayer imaging process typically follows these steps:
-
Data Preparation: The PCB design files (Gerber files) are prepared and optimized for the chosen imaging technique.
-
Copper-Clad Laminate Preparation: The copper-clad laminate is cleaned and pre-treated to ensure proper adhesion of the photoresist.
-
Photoresist Application: A thin layer of photoresist is applied uniformly onto the copper surface of the laminate. This can be done through various methods, such as roller coating, curtain coating, or electrodeposition.
-
Imaging: The prepared laminate is exposed to the circuit pattern using the chosen imaging technique (photo plotting, LDI, or inkjet printing).
-
Developing: The exposed laminate is developed in a chemical solution, which removes the unexposed photoresist areas, leaving behind the desired circuit pattern.
-
Etching: The developed laminate undergoes an etching process, where the exposed copper areas are chemically removed, leaving behind the circuit pattern protected by the remaining photoresist.
-
Stripping: The remaining photoresist is stripped away using a chemical solution, revealing the final copper circuit pattern on the laminate.
-
Inspection: The imaged and etched laminate is inspected for any defects or irregularities using automated optical inspection (AOI) systems or manual visual inspection.
After the innerlayer imaging process, the laminates are ready for the subsequent steps in the multilayer PCB manufacturing process, such as layup, lamination, drilling, and plating.
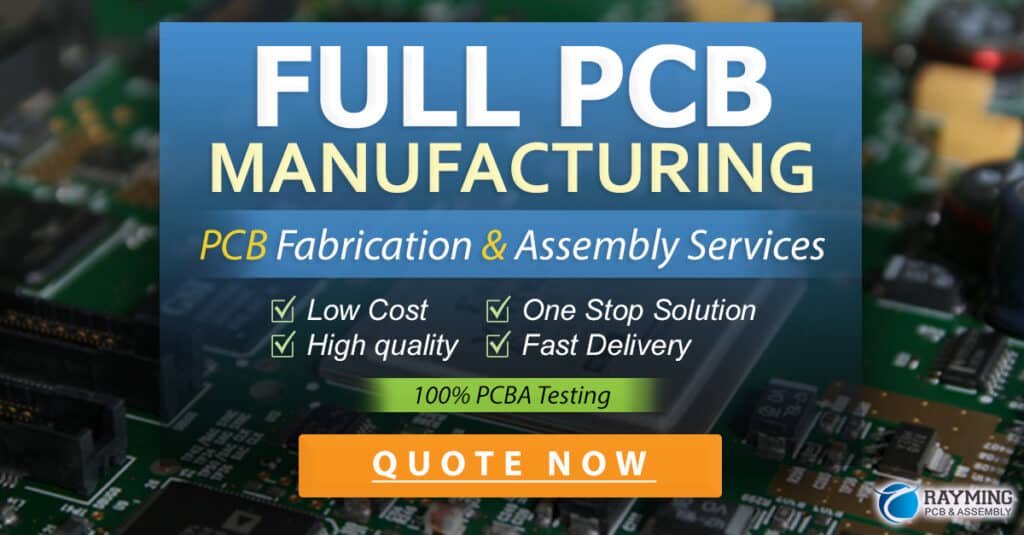
Factors Affecting Innerlayer Imaging Quality
Several factors can impact the quality of innerlayer imaging in PCB manufacturing:
-
Artwork Quality: The accuracy and completeness of the PCB design files (Gerber files) directly influence the quality of the imaged circuit pattern. Errors or inconsistencies in the artwork can lead to defects in the final PCB.
-
Photoresist Quality: The quality and consistency of the photoresist material used for imaging play a crucial role. Photoresists with good adhesion, uniform thickness, and appropriate sensitivity are essential for achieving high-quality imaging results.
-
Imaging Equipment: The performance and calibration of the imaging equipment, whether it’s a photoplotter, LDI system, or inkjet printer, affect the accuracy and resolution of the imaged circuit pattern. Regular maintenance and calibration of the equipment are necessary to ensure consistent imaging quality.
-
Exposure Parameters: The exposure time, intensity, and focus settings of the imaging equipment must be optimized based on the photoresist material and desired resolution. Overexposure or underexposure can lead to defects such as widening or narrowing of traces, respectively.
-
Developing Conditions: The concentration, temperature, and duration of the developing process can impact the quality of the imaged circuit pattern. Improper developing can result in incomplete removal of unexposed photoresist or overetching of the copper traces.
-
Environmental Factors: Factors such as temperature, humidity, and cleanliness of the manufacturing environment can affect the innerlayer imaging process. Controlled environmental conditions are necessary to ensure consistent imaging results and prevent contamination.
-
Operator Skill: The skill and experience of the operators involved in the innerlayer imaging process can influence the quality of the final product. Proper training and adherence to standard operating procedures are essential to minimize human errors and ensure consistent imaging quality.
By carefully controlling these factors and implementing strict quality control measures, PCB manufacturers can achieve high-quality innerlayer imaging and produce reliable multilayer PCBs.
Challenges and Future Trends in Innerlayer Imaging
As PCB designs become more complex and miniaturized, innerlayer imaging faces several challenges and opportunities for improvement:
-
Higher Resolution: With the increasing demand for high-density interconnect (HDI) PCBs, innerlayer imaging techniques must be capable of achieving finer resolutions and smaller feature sizes. Advanced LDI systems and inkjet printing technologies are being developed to meet these requirements.
-
Improved Registration: Maintaining accurate layer-to-layer registration is crucial for the reliability and functionality of multilayer PCBs. Advancements in imaging equipment and process control are necessary to achieve tighter registration tolerances.
-
Faster Imaging Speeds: As production volumes and time-to-market pressures increase, innerlayer imaging processes need to be optimized for faster throughput without compromising quality. Continuous improvements in imaging equipment and automation are essential to meet these demands.
-
Environmental Sustainability: There is a growing emphasis on environmentally friendly PCB manufacturing processes. Innerlayer imaging techniques that reduce waste, minimize the use of hazardous chemicals, and promote energy efficiency are gaining attention. Inkjet printing, with its additive nature, offers potential benefits in this regard.
-
Integration with Industry 4.0: The integration of innerlayer imaging processes with Industry 4.0 technologies, such as the Internet of Things (IoT), big data analytics, and machine learning, can enable real-time process monitoring, predictive maintenance, and adaptive process control. This can lead to improved quality, efficiency, and cost-effectiveness in PCB manufacturing.
As the PCB industry continues to evolve, innerlayer imaging techniques will need to keep pace with the changing requirements and technological advancements. Continuous research and development efforts are essential to overcome challenges and drive innovation in this critical aspect of multilayer PCB manufacturing.
Frequently Asked Questions (FAQ)
-
What is the purpose of innerlayer imaging in multilayer PCB manufacturing?
Innerlayer imaging is the process of transferring the designed circuit pattern onto the copper-clad laminates that form the inner layers of a multilayer PCB. It is crucial for ensuring the accurate reproduction of the circuit pattern, enabling proper interconnectivity between layers, and maintaining signal integrity. -
What are the common techniques used for innerlayer imaging?
The common techniques used for innerlayer imaging include: - Photo Plotting: Exposing the circuit pattern onto a photographic film using a photoplotter machine.
- Laser Direct Imaging (LDI): Directly exposing the circuit pattern onto the photoresist-coated copper-clad laminate using a laser.
-
Inkjet Printing: Directly depositing the circuit pattern onto the copper-clad laminate using specialized inkjet printers.
-
What are the advantages of Laser Direct Imaging (LDI) over traditional photo plotting?
LDI offers several advantages over photo plotting: - Higher precision and resolution, enabling the creation of fine-pitch traces and high-density PCB designs.
- Improved layer-to-layer registration accuracy.
- Faster turnaround time by eliminating the need for film preparation and development.
-
Cost-effectiveness by reducing material costs and waste generation.
-
What factors can affect the quality of innerlayer imaging in PCB manufacturing?
Several factors can impact the quality of innerlayer imaging, including: - Artwork quality and accuracy of the PCB design files.
- Quality and consistency of the photoresist material used.
- Performance and calibration of the imaging equipment.
- Exposure parameters, such as time, intensity, and focus settings.
- Developing conditions, including concentration, temperature, and duration.
- Environmental factors, such as temperature, humidity, and cleanliness.
-
Operator skill and adherence to standard operating procedures.
-
What are some of the future trends and challenges in innerlayer imaging for multilayer PCBs?
As PCB designs become more complex and miniaturized, innerlayer imaging faces challenges and opportunities for improvement: - Achieving higher resolutions and smaller feature sizes to support high-density interconnect (HDI) PCBs.
- Improving layer-to-layer registration accuracy for enhanced reliability.
- Increasing imaging speeds to meet faster production demands.
- Adopting environmentally sustainable imaging techniques and processes.
- Integrating innerlayer imaging with Industry 4.0 technologies for real-time monitoring, predictive maintenance, and adaptive process control.
Innerlayer Imaging Technique | Advantages | Disadvantages |
---|---|---|
Photo Plotting | – High resolution and accuracy – Suitable for complex designs |
– Slow process – Requires photographic films – Costly |
Laser Direct Imaging (LDI) | – Higher precision (up to 25 microns) – Improved registration – Faster turnaround – Cost-effective |
– Higher initial equipment cost |
Inkjet Printing | – Additive process (reduces waste) – Design flexibility – Cost-effective for low volumes |
– Limited resolution and speed compared to other methods |
No responses yet