How Does an Induction Heater Circuit Work?
The working principle of an induction heater circuit is based on Faraday’s law of electromagnetic induction. When an alternating current (AC) is passed through a coil, it generates an alternating magnetic field around the coil. If a conductive material, such as a metal workpiece, is placed inside or near this magnetic field, eddy currents are induced in the material. These eddy currents flow in closed loops within the material, generating heat due to the material’s electrical resistance.
Key Components of an Induction Heater Circuit
An induction heater circuit consists of several key components:
- Power supply: Provides the alternating current to the work coil.
- Work coil: Generates the alternating magnetic field that induces eddy currents in the workpiece.
- Capacitor bank: Helps to tune the circuit to the desired frequency and improve power transfer.
- Workpiece: The conductive material that is heated by the induced eddy currents.
Factors Affecting the Heating Process
The efficiency and effectiveness of the induction heating process depend on several factors:
- Frequency of the AC current: Higher frequencies result in more localized heating, while lower frequencies penetrate deeper into the workpiece.
- Power output: Higher power output leads to faster heating rates.
- Material properties: The electrical resistivity and magnetic permeability of the workpiece material affect the induced eddy currents and the heating efficiency.
- Coil design: The shape, size, and number of turns in the work coil influence the magnetic field strength and distribution.
Designing the Work Coil for an Induction Heater Circuit
The work coil is the most critical component of an induction heater circuit, as it determines the heating pattern and efficiency. Proper design of the work coil is essential for optimal performance and application-specific requirements.
Coil Shape and Size
The shape and size of the work coil depend on the geometry of the workpiece and the desired heating pattern. Common coil shapes include:
- Solenoid coil: Cylindrical shape, suitable for heating round or tubular workpieces.
- Pancake coil: Flat spiral shape, used for heating flat surfaces or thin materials.
- Channel coil: Rectangular shape, designed for heating bar or strip-shaped workpieces.
- Custom coils: Shaped to match specific workpiece geometries for uniform heating.
The size of the coil should be optimized based on the workpiece dimensions and the required heating depth. Larger coils generate more uniform magnetic fields but have lower power density, while smaller coils provide more localized heating but may result in uneven temperature distribution.
Number of Turns and Coil Pitch
The number of turns in the work coil determines the magnetic field strength and the coil’s inductance. More turns result in a stronger magnetic field but also increase the coil’s inductance, which may require adjustments to the capacitor bank for proper tuning.
The coil pitch, or the spacing between turns, affects the magnetic field distribution and the coupling efficiency between the coil and the workpiece. A tighter pitch results in a more concentrated magnetic field, while a looser pitch provides a more uniform field distribution.
Coil Material and Cooling
The work coil is subjected to high temperatures and electromagnetic stresses during operation, so it must be made of a material with good electrical conductivity, thermal stability, and mechanical strength. Copper is the most common choice for work coils due to its excellent conductivity and ease of forming.
To prevent overheating and ensure long-term reliability, the work coil may require cooling. Cooling methods include:
- Air cooling: Forced air flow around the coil using fans or blowers.
- Water cooling: Hollow copper tubing is used to construct the coil, allowing water to flow through and remove heat.
- Ceramic insulation: High-temperature ceramic materials are used to insulate the coil and reduce heat loss.
Applications of Induction Heater Circuits
Induction heater circuits find applications in various industries, ranging from metallurgy to food processing. Some common applications include:
Heat Treatment of Metals
Induction heating is widely used for heat treatment processes such as hardening, tempering, and annealing of metals. The rapid and localized heating provided by induction allows for precise control over the heat-affected zone and minimizes distortion in the workpiece.
Welding and Brazing
Induction heating is used for preheating, post-heating, and stress-relieving during welding and brazing processes. It helps to improve joint quality, reduce residual stresses, and minimize the risk of cracking.
Melting and Casting
Induction furnaces are used for melting and casting metals, particularly in the foundry industry. The non-contact heating and the ability to control the melt temperature precisely make induction heating an attractive choice for these applications.
Plastic Injection Molding
Induction heating is used for preheating plastic pellets before injection molding, ensuring a consistent melt temperature and reducing cycle times. It is also used for mold heating to improve surface finish and reduce warpage in the molded parts.
Food Processing
Induction heating is used in various food processing applications, such as cooking, pasteurization, and sterilization. The rapid and uniform heating provided by induction improves product quality and reduces processing times compared to traditional heating methods.
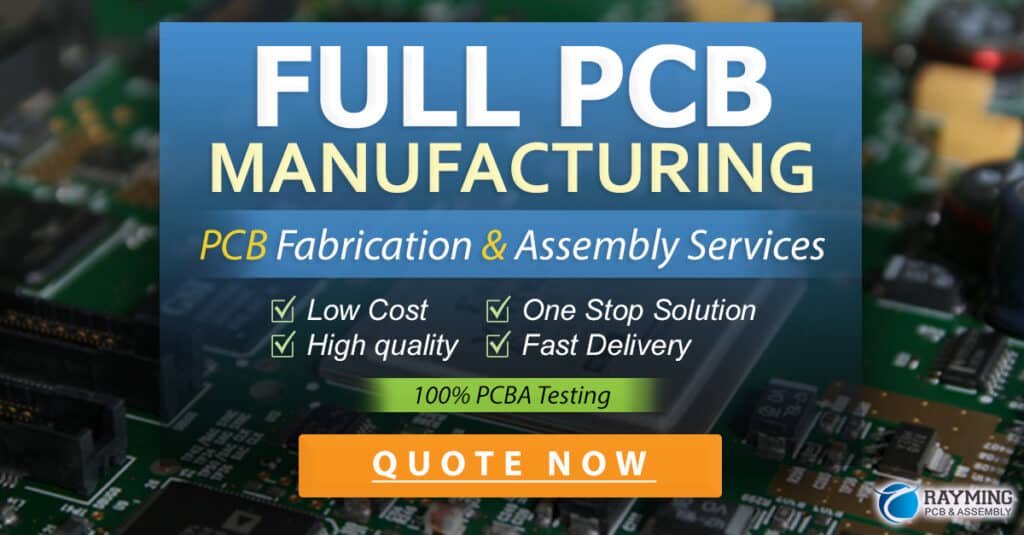
Frequently Asked Questions (FAQ)
-
Q: What is the advantage of induction heating over other heating methods?
A: Induction heating offers several advantages, including rapid heating, precise temperature control, localized heating, and non-contact heating. It is more energy-efficient and has a lower environmental impact compared to fossil fuel-based heating methods. -
Q: Can induction heating be used for non-conductive materials?
A: Induction heating works best with conductive materials, such as metals. However, it can be used for heating non-conductive materials indirectly by using a conductive susceptor or by incorporating conductive particles into the non-conductive material. -
Q: How does the frequency of the AC current affect the induction heating process?
A: The frequency of the AC current determines the depth of penetration and the heating pattern. Higher frequencies (10-400 kHz) result in more localized heating and are suitable for surface treatments, while lower frequencies (50 Hz-10 kHz) penetrate deeper into the workpiece and are used for through-heating applications. -
Q: What factors should be considered when selecting the work coil material?
A: The work coil material should have high electrical conductivity, good thermal stability, and adequate mechanical strength. Copper is the most common choice due to its excellent conductivity and ease of forming. Other factors to consider include the operating temperature, the required heating pattern, and the compatibility with the workpiece material. -
Q: How can the efficiency of an induction heater circuit be improved?
A: The efficiency of an induction heater circuit can be improved by optimizing the work coil design, selecting the appropriate frequency and power output, and ensuring proper coupling between the coil and the workpiece. Using high-quality capacitors and minimizing losses in the power supply and other components can also enhance overall efficiency.
Conclusion
Induction heater circuits are powerful tools for generating heat in conductive materials, offering numerous advantages over traditional heating methods. By understanding the working principle and the key design considerations for the work coil, engineers can develop efficient and application-specific induction heating solutions. With its wide range of applications, from heat treatment of metals to food processing, induction heating continues to play a crucial role in various industries, driving innovation and improving process efficiency.
No responses yet