Introduction to Hybrid PCBs
Hybrid printed circuit boards (PCBs) are a combination of different materials and technologies used to create a single, integrated circuit board. These PCBs are designed to take advantage of the unique properties of each material, resulting in a board that is optimized for specific applications. Hybrid PCBs are commonly used in high-performance electronics, such as aerospace, military, and medical devices, where reliability, durability, and functionality are critical.
What are Hybrid PCBs?
Hybrid PCBs are circuit boards that incorporate multiple materials, such as ceramic, metal, and polymer, to create a single, integrated board. These materials are chosen based on their specific properties, such as thermal conductivity, electrical insulation, and mechanical strength. By combining these materials, designers can create PCBs that are tailored to meet the specific requirements of an application.
Advantages of Hybrid PCBs
Hybrid PCBs offer several advantages over traditional single-material PCBs:
- Improved thermal management: By incorporating materials with high thermal conductivity, such as ceramics or metals, hybrid PCBs can dissipate heat more effectively, reducing the risk of thermal damage to components.
- Enhanced electrical performance: Hybrid PCBs can use materials with specific dielectric properties to improve signal integrity and reduce electromagnetic interference (EMI).
- Increased mechanical strength: The combination of materials in a hybrid PCB can provide greater mechanical strength and durability, making them suitable for harsh environments.
- Miniaturization: Hybrid PCBs can integrate multiple functions into a single board, reducing the overall size and weight of the electronic device.
Types of Materials Used in Hybrid PCBs
Ceramics
Ceramics are widely used in hybrid PCBs due to their excellent thermal and electrical properties. Some common ceramic materials include:
- Alumina (Al2O3): Alumina is a popular choice for hybrid PCBs due to its high thermal conductivity, good electrical insulation, and mechanical strength. It is often used as a substrate material for high-power applications.
- Aluminum Nitride (AlN): AlN has a higher thermal conductivity than alumina and is used in applications that require even better heat dissipation, such as high-power LEDs and power electronics.
- Beryllium Oxide (BeO): BeO has the highest thermal conductivity among ceramic materials but is less commonly used due to its toxicity and high cost.
Metals
Metals are used in hybrid PCBs for their excellent electrical and thermal conductivity. Some common metals include:
- Copper: Copper is the most widely used metal in PCBs due to its high electrical conductivity and relatively low cost. It is often used for signal traces and heat spreaders.
- Aluminum: Aluminum is lighter than copper and has good thermal conductivity, making it suitable for applications where weight is a concern, such as aerospace electronics.
- Invar: Invar is a nickel-iron alloy with a very low coefficient of thermal expansion (CTE), making it useful for applications where dimensional stability is critical, such as in high-precision optics and instrumentation.
Polymers
Polymers are used in hybrid PCBs for their low dielectric constant, flexibility, and low cost. Some common polymers include:
- Polyimide (PI): PI is a high-temperature polymer with excellent electrical insulation properties and mechanical strength. It is often used as a flexible substrate material in hybrid PCBs.
- Liquid Crystal Polymer (LCP): LCP has a low dielectric constant and low moisture absorption, making it suitable for high-frequency applications, such as 5G telecommunications.
- Epoxy: Epoxy is a low-cost polymer used as a bonding agent and encapsulant in hybrid PCBs.
Manufacturing Processes for Hybrid PCBs
Thick Film Technology
Thick film technology involves screen printing conductive and resistive pastes onto a ceramic substrate and firing them at high temperatures (typically 850°C) to form a robust, conductive pattern. This process is commonly used for creating resistors, capacitors, and conductors on hybrid PCBs.
Low-Temperature Co-fired Ceramics (LTCC)
LTCC is a multi-layer ceramic technology that uses multiple layers of ceramic tapes with embedded conductors, resistors, and other passive components. These layers are laminated together and fired at lower temperatures (typically 850-900°C) than traditional ceramics, allowing for the integration of more delicate components, such as capacitors and inductors.
High-Temperature Co-fired Ceramics (HTCC)
HTCC is similar to LTCC but uses ceramic materials that require higher firing temperatures (typically 1600-1800°C). This process is used for applications that require higher thermal stability and mechanical strength, such as in aerospace and military electronics.
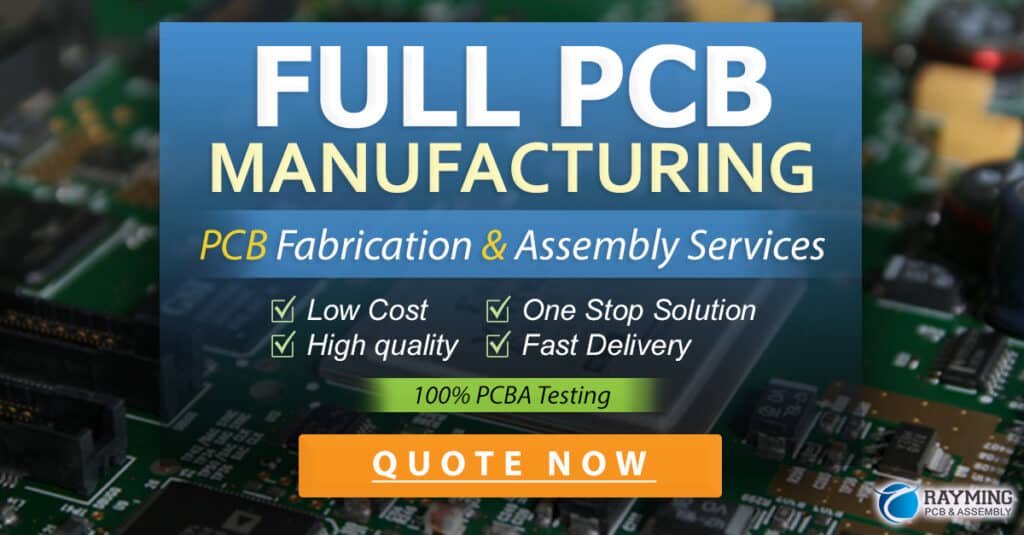
Challenges in Hybrid PCB Design and Manufacturing
Material Compatibility
One of the main challenges in hybrid PCB design is ensuring the compatibility of the various materials used. Each material has its own thermal, electrical, and mechanical properties, which must be carefully considered when designing the board. Mismatches in these properties can lead to reliability issues, such as delamination, warping, or cracking.
Thermal Management
Hybrid PCBs often incorporate high-power components that generate significant amounts of heat. Effective thermal management is crucial to ensure the reliability and longevity of the board. Designers must carefully select materials with appropriate thermal conductivity and design efficient heat dissipation paths to prevent thermal damage to components.
Manufacturability
Hybrid PCBs can be more complex to manufacture than traditional single-material PCBs due to the various materials and processes involved. Designers must work closely with manufacturers to ensure that the board can be produced reliably and cost-effectively. Factors such as material availability, process compatibility, and manufacturing tolerances must be considered during the design phase.
Cost
Hybrid PCBs can be more expensive than traditional PCBs due to the specialized materials and manufacturing processes required. Designers must balance performance requirements with cost considerations to ensure that the board is economically viable for the intended application.
Testing and Quality Control
Ensuring the quality and reliability of hybrid PCBs can be challenging due to the complex interactions between the various materials and components. Thorough testing and quality control measures must be implemented throughout the manufacturing process to identify and address any potential issues.
Applications of Hybrid PCBs
Hybrid PCBs are used in a wide range of high-performance applications, including:
- Aerospace and defense electronics
- Medical devices and implants
- Automotive electronics
- Industrial controls and instrumentation
- Telecommunications and networking equipment
- Power electronics and renewable energy systems
These applications often require a combination of high reliability, durability, and functionality, which can be achieved through the use of hybrid PCB technology.
Future Trends in Hybrid PCB Technology
As electronic devices continue to become more complex and demanding, hybrid PCB technology is expected to evolve to meet these challenges. Some potential future trends include:
- Increased use of 3D printing for rapid prototyping and small-scale production of hybrid PCBs.
- Development of new materials with improved thermal, electrical, and mechanical properties.
- Integration of active components, such as semiconductors, into hybrid PCBs for greater functionality and miniaturization.
- Adoption of advanced manufacturing processes, such as laser sintering and inkjet printing, for more precise and efficient production of hybrid PCBs.
- Expansion of hybrid PCB technology into new application areas, such as wearable electronics and Internet of Things (IoT) devices.
FAQs
-
Q: What is the difference between a hybrid PCB and a traditional PCB?
A: A hybrid PCB combines multiple materials, such as ceramics, metals, and polymers, to create a single, integrated board, while a traditional PCB typically uses a single material, such as FR-4, for the substrate. -
Q: What are the main advantages of using a hybrid PCB?
A: Hybrid PCBs offer improved thermal management, enhanced electrical performance, increased mechanical strength, and the ability to miniaturize electronic devices by integrating multiple functions into a single board. -
Q: What are some common applications for hybrid PCBs?
A: Hybrid PCBs are commonly used in aerospace and defense electronics, medical devices and implants, automotive electronics, industrial controls and instrumentation, telecommunications and networking equipment, and power electronics and renewable energy systems. -
Q: What are the main challenges in designing and manufacturing hybrid PCBs?
A: The main challenges include ensuring material compatibility, effective thermal management, manufacturability, cost considerations, and thorough testing and quality control measures. -
Q: What are some potential future trends in hybrid PCB technology?
A: Future trends may include increased use of 3D printing, development of new materials, integration of active components, adoption of advanced manufacturing processes, and expansion into new application areas, such as wearable electronics and IoT devices.
Conclusion
Hybrid PCBs offer a powerful solution for high-performance electronics that require a combination of reliability, durability, and functionality. By incorporating multiple materials with specific properties, designers can create PCBs that are optimized for specific applications, such as aerospace, military, and medical devices. However, the design and manufacturing of hybrid PCBs also present unique challenges, such as material compatibility, thermal management, and cost considerations. As electronic devices continue to evolve, hybrid PCB technology is expected to advance to meet the growing demands for high-performance, miniaturized, and reliable electronic systems.
No responses yet