Understanding ESD and its Impact on SMT Assembly
What is ESD?
ESD is the sudden flow of electricity between two objects with different electrical charges, caused by direct contact or induced by an electrostatic field. When an object with a static charge comes into contact with a conductive surface, the electrons rapidly transfer from one object to another, creating a high-voltage, high-current discharge.
How ESD Affects SMT Components
SMT components, such as integrated circuits (ICs), resistors, and capacitors, are particularly susceptible to ESD damage due to their small size and sensitive internal structures. ESD events can cause the following issues:
- Dielectric breakdown: High-voltage discharges can break down the insulating materials within components, leading to short circuits and permanent damage.
- Junction damage: ESD can cause localized melting or vaporization of semiconductor junctions, altering their electrical properties and potentially rendering the component non-functional.
- Latent defects: Some ESD events may not immediately destroy a component but can cause latent defects that manifest as premature failures during operation.
The Cost of ESD Damage
ESD damage can have significant financial implications for electronics manufacturers, including:
- Component replacement costs
- Rework and repair expenses
- Increased production delays
- Reduced product reliability and customer satisfaction
- Potential liability issues
ESD Prevention Strategies in SMT Assembly
To minimize the risk of ESD damage in SMT assembly processes, manufacturers should implement a comprehensive ESD prevention strategy that addresses both the facility and the personnel involved in the assembly process.
ESD-Safe Facility Design
An ESD-safe facility is crucial for preventing static buildup and discharges during SMT assembly. Key elements of an ESD-safe facility include:
- Grounded workstations: All workstations should be properly grounded to a common earth ground to prevent static buildup.
- Conductive flooring: Use conductive or dissipative flooring materials to prevent static buildup on personnel and equipment.
- Ionizers: Employ ionizing equipment to neutralize static charges in the air and on surfaces.
- Humidity control: Maintain relative humidity levels between 40% and 60% to minimize static buildup.
Personnel ESD protection
Proper training and personal protective equipment (PPE) are essential for preventing ESD events caused by personnel. Important considerations include:
- ESD-safe garments: Personnel should wear ESD-safe smocks, gloves, and footwear to prevent static buildup on their bodies.
- Grounding straps: Use grounding straps or heel grounders to ensure personnel are properly grounded when handling sensitive components.
- Training: Provide regular ESD awareness and prevention training to all personnel involved in SMT assembly processes.
ESD-Safe Material Handling
Proper handling of SMT components and materials is critical for preventing ESD damage. Best practices include:
- ESD-safe packaging: Store and transport sensitive components in ESD-safe packaging, such as conductive or dissipative bags, boxes, and trays.
- Grounded storage racks: Use grounded storage racks to prevent static buildup on stored materials.
- ESD-safe workstations: Handle sensitive components only at properly grounded and equipped ESD-safe workstations.
ESD Monitoring and Testing
Regular monitoring and testing of ESD prevention measures are necessary to ensure their effectiveness and identify potential issues before they lead to component damage. Key aspects of ESD monitoring and testing include:
- Periodic audits: Conduct regular audits of ESD prevention measures, including facility design, personnel protection, and material handling practices.
- Resistance testing: Test the resistance of grounding systems, conductive flooring, and personnel grounding equipment to ensure proper functionality.
- Static charge monitoring: Use static charge meters to monitor static levels on personnel, equipment, and materials.
- Event logging: Maintain a log of ESD events and their root causes to identify trends and implement corrective actions.
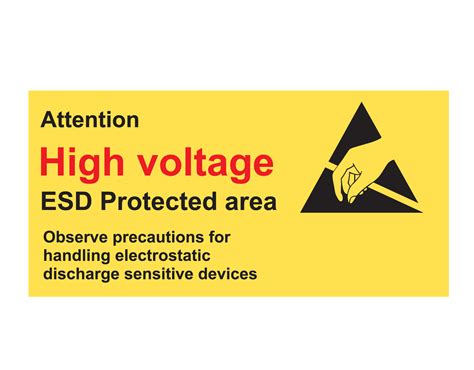
Implementing an ESD Control Program
An effective ESD control program is essential for ensuring consistent and reliable ESD prevention in SMT assembly processes. The following steps outline the process for implementing an ESD control program:
- Assess current ESD prevention measures and identify areas for improvement.
- Develop an ESD control plan that addresses facility design, personnel protection, material handling, and monitoring and testing.
- Implement the ESD control plan, including necessary facility upgrades, personnel training, and process changes.
- Establish a system for regular monitoring, testing, and auditing of ESD prevention measures.
- Continuously review and improve the ESD control program based on event logs, audit results, and industry best practices.
Component of ESD Control Program | Key Elements |
---|---|
Facility Design | – Grounded workstations – Conductive flooring – Ionizers – Humidity control |
Personnel Protection | – ESD-safe garments – Grounding straps – Training |
Material Handling | – ESD-safe packaging – Grounded storage racks – ESD-safe workstations |
Monitoring and Testing | – Periodic audits – Resistance testing – Static charge monitoring – Event logging |
By implementing a comprehensive ESD control program that addresses all aspects of ESD prevention, SMT assembly manufacturers can significantly reduce the risk of ESD damage, improve product quality and reliability, and minimize the financial impact of ESD events.
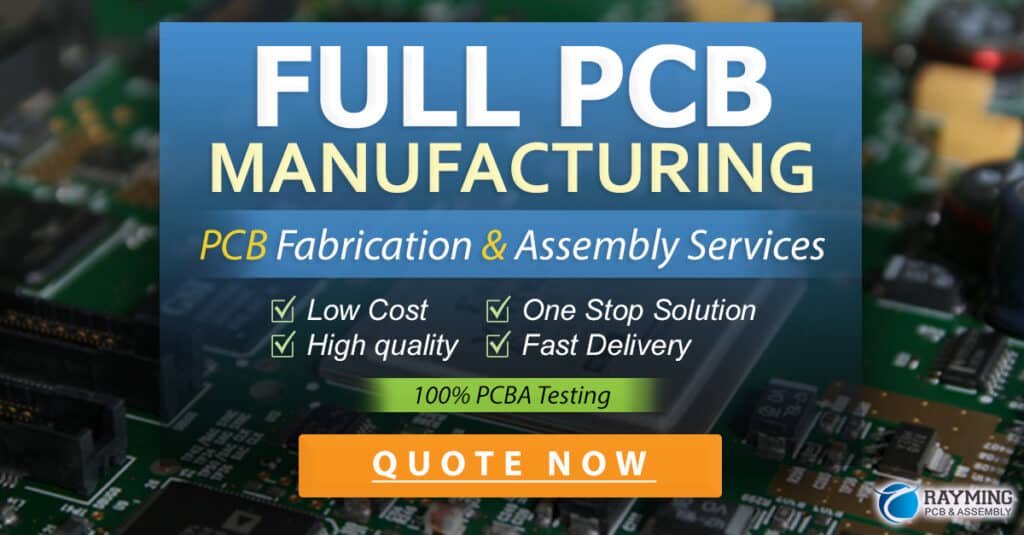
Frequently Asked Questions (FAQ)
-
Q: What is the difference between conductive and dissipative materials in ESD prevention?
A: Conductive materials have a lower electrical resistance (less than 10^4 ohms) and allow static charges to flow easily, while dissipative materials have a higher resistance (between 10^4 and 10^11 ohms) and slowly dissipate static charges without allowing rapid discharge events. -
Q: How often should ESD prevention training be conducted for personnel?
A: ESD prevention training should be conducted at least annually for all personnel involved in SMT assembly processes, with additional training provided as needed based on job role changes, process updates, or ESD event trends. -
Q: What is the recommended relative humidity level for an ESD-safe environment?
A: The recommended relative humidity level for an ESD-safe environment is between 40% and 60%. This range minimizes static buildup while maintaining a comfortable working environment for personnel. -
Q: Can ESD damage be detected visually?
A: Not always. While some ESD events may cause visible damage, such as charring or melting, many ESD events can cause latent defects that are not visible to the naked eye. Proper ESD monitoring and testing are necessary to identify potential issues. -
Q: What should be included in an ESD event log?
A: An ESD event log should include the date and time of the event, the location or workstation where the event occurred, the personnel involved, the affected components or materials, the suspected root cause, and any corrective actions taken. This information can help identify trends and guide improvements to the ESD control program.
By understanding the risks associated with ESD and implementing a comprehensive ESD control program, SMT assembly manufacturers can effectively prevent ESD damage, improve product quality and reliability, and reduce the financial impact of ESD events. Regular monitoring, testing, and continuous improvement of ESD prevention measures are essential for maintaining an ESD-safe environment and ensuring the long-term success of the SMT assembly process.
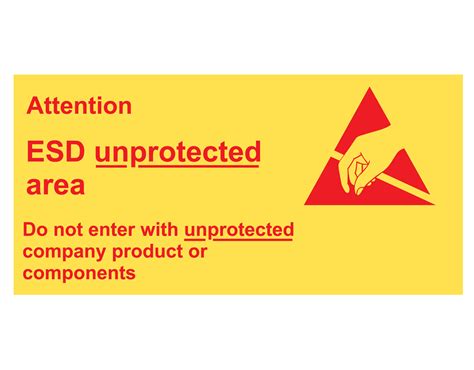
No responses yet