Proper PCB Design for BGA Packages
PCB design is the first critical step that lays the foundation for the entire BGA assembly process. A well-designed PCB can greatly improve the yield and reliability of BGA solder joints. Here are some important design guidelines to follow:
Use the Correct BGA Land Pattern
The land pattern is the arrangement of copper pads on the PCB that matches the solder balls on the BGA component. It’s crucial to use the land pattern recommended by the BGA manufacturer to ensure proper solderability and reliability.
The key parameters of a BGA land pattern include:
- Pad size
- Pad shape (circular, square, or rounded square)
- Pad pitch (distance between the centers of adjacent pads)
- Solder mask opening
- Solder paste stencil aperture design
Refer to the manufacturer’s datasheet and application notes for the specific requirements of your BGA package. In general, the pad size should be about 80% of the ball size, and the solder mask opening should be slightly larger than the pad to allow enough space for solder wetting.
Optimize Escape Routing
Escape routing refers to the fanout of traces from the dense BGA pads to other layers of the PCB. It’s a challenging task due to the limited space between pads. Proper escape routing is important to minimize signal integrity issues and manufacturing defects.
Some best practices for BGA escape routing include:
- Use a staggered pad pattern instead of a full grid to create more space between pads
- Route traces diagonally between pads to maximize the available space
- Use microvias (small drilled holes) to route traces to inner layers
- Follow the manufacturer’s recommendations for trace width and spacing
- Perform signal integrity simulation to validate the routing design
Provide Adequate PCB Support
BGA packages are sensitive to PCB Warpage and flexing, which can cause open solder joints or solder bridges. Therefore, it’s important to provide sufficient mechanical support for the BGA component during and after the assembly process.
Some ways to enhance PCB support include:
- Use a thicker PCB substrate (e.g. 1.6 mm or more) to reduce flexing
- Add copper planes and/or stiffeners to the PCB
- Place the BGA package close to mounting holes or board edges for better support
- Avoid placing large components or connectors near the BGA that could cause uneven pressure during reflow
- Use support pins if necessary to prevent the PCB from sagging during handling
Stencil Printing for BGA Assembly
Stencil printing is the process of applying solder paste to the PCB pads through a laser-cut stencil. It’s a critical step that directly affects the volume, shape, and position of solder deposits, which in turn impact the quality of BGA solder joints.
Choose the Right Stencil Thickness
The stencil thickness determines the amount of solder paste deposited on the pads. A thicker stencil will result in a higher solder volume, while a thinner stencil will give a lower volume. The optimal stencil thickness depends on the size and pitch of the BGA package, as well as the PCB Surface Finish.
Here are some general guidelines for selecting the stencil thickness:
BGA Pitch | Stencil Thickness |
---|---|
1.0 mm | 150-200 μm |
0.8 mm | 125-150 μm |
0.5 mm | 100-125 μm |
For finer pitch BGAs (0.4 mm or less), even thinner stencils (80-100 μm) may be needed to avoid solder bridging. It’s recommended to consult with your stencil supplier or assembly partner to determine the best thickness for your specific application.
Optimize Stencil Aperture Design
The stencil aperture is the opening in the stencil that allows solder paste to be deposited onto the PCB pad. The size and shape of the aperture directly affect the print quality and solder joint reliability.
For BGA pads, the aperture design should follow these guidelines:
- The aperture size should be 80-90% of the pad size to allow some clearance for solder wetting
- The aperture shape should match the pad shape (circular or square)
- The aperture wall should have a 5-degree taper to facilitate paste release
- The area ratio (aperture area divided by aperture wall area) should be greater than 0.66 to avoid paste clogging
It’s also important to consider the aperture reduction for small and fine-pitch BGA pads to reduce the risk of solder bridging. A common practice is to reduce the aperture size by 10-20% compared to larger pads.
Control Printing Parameters
In addition to stencil design, the printing process parameters also play a key role in achieving consistent and reliable solder paste deposits. The key parameters to control include:
- Printing speed: A slower speed allows more time for the solder paste to roll and fill the apertures, but too slow may cause smearing. A typical speed range is 20-50 mm/sec.
- Printing pressure: A higher pressure helps to ensure good paste release and aperture filling, but too high may cause scooping or damage to the stencil. A typical pressure range is 0.2-0.4 kg/cm².
- Separation speed: A faster separation speed minimizes the time for the paste to stick to the aperture walls, but too fast may cause slumping or tailing. A typical speed range is 1-5 mm/sec.
It’s important to optimize and monitor these parameters regularly to maintain a stable printing process. The use of SPI (Solder Paste Inspection) systems can provide valuable feedback on the print quality and help to detect any issues early.
BGA Component Placement
After stencil printing, the next step is to place the BGA component onto the PCB. Accurate placement is crucial to ensure proper alignment between the BGA balls and PCB pads, and to avoid defects such as opens, shorts, or misregistration.
Use a High-Precision Pick-and-Place Machine
BGA placement requires a high level of accuracy and repeatability that can only be achieved by using a modern pick-and-place machine with vision alignment capability. The machine should have a placement accuracy of ±50 μm or better, and a repeatability of ±10 μm or better.
Some other key features to look for in a BGA placement machine include:
- Multiple cameras for fiducial recognition and component alignment
- Programmable placement force and speed
- Automatic nozzle changing for different component sizes
- Heated head for handling moisture-sensitive components
- Statistical process control (SPC) for monitoring and optimizing the placement process
Perform Vision Alignment
Vision alignment is the process of using cameras to align the BGA component with the PCB fiducials and pads. It’s a critical step to compensate for any print offset or component shift, and to ensure accurate placement.
There are two main types of vision alignment methods:
- Fiducial alignment: The machine locates the PCB fiducials (reference marks) and the component fiducials, and calculates the offset and rotation between them. It then adjusts the placement position accordingly.
- Pattern recognition: The machine compares the actual component image with a reference image, and adjusts the placement position to achieve the best match.
For fine-pitch BGAs, the pattern recognition method is preferred as it provides better accuracy. It’s important to teach the machine the correct reference image and to set appropriate tolerance limits for the alignment.
Control Placement Parameters
Similar to printing, the placement process parameters also need to be optimized and controlled to ensure consistent and reliable results. The key parameters include:
- Placement force: A higher force helps to ensure good contact between the BGA balls and solder paste, but too high may cause component or PCB damage. A typical force range is 1-5 N.
- Placement speed: A slower speed allows more time for the component to settle and align, but too slow may impact the throughput. A typical speed range is 10-50 mm/sec.
- Dwell time: A longer dwell time (the time the component is held in place before release) helps to stabilize the component position, but too long may cause paste slumping. A typical dwell time range is 0.1-0.5 sec.
It’s important to monitor these parameters and the placement quality regularly, and to make adjustments as needed. The use of AOI (Automated Optical Inspection) systems can help to detect any placement errors or defects before reflow.
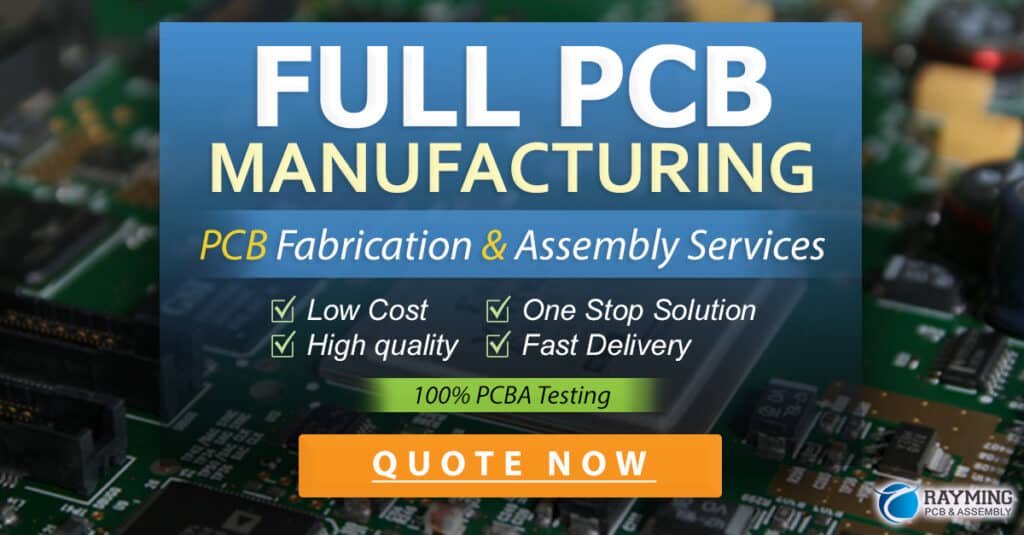
Reflow Soldering for BGA Assembly
Reflow soldering is the final and most critical step in the BGA assembly process. It involves heating the PCB Assembly to melt the solder paste and form permanent solder joints between the BGA balls and PCB pads. Proper reflow is essential to achieve strong, reliable, and defect-free BGA solder joints.
Select the Right Reflow Profile
The reflow profile is the time-temperature curve that the PCB assembly follows during the reflow process. It consists of several zones, including preheat, soak, reflow, and cooling. The optimal reflow profile depends on the solder paste composition, the BGA package type, and the PCB design.
Here are some general guidelines for selecting the reflow profile:
- The preheat rate should be 1-3°C/sec to gradually warm up the assembly and activate the solder flux
- The soak zone should be 150-180°C for 60-120 sec to allow the flux to fully activate and the solder paste to dry out
- The reflow peak temperature should be 20-40°C above the solder melting point (217°C for SAC305) for 30-90 sec to ensure complete melting and wetting
- The cooling rate should be 2-6°C/sec to allow the solder to solidify and form strong joints
It’s important to follow the solder paste and component manufacturer’s recommendations for the specific reflow profile parameters. Running a profile simulation or characterization on actual assemblies is also helpful to validate and optimize the profile.
Minimize PCB Warpage and Thermal Stress
During reflow, the PCB and components undergo thermal expansion and contraction, which can cause warpage and stress on the BGA solder joints. Excessive warpage can lead to open joints, solder bridging, or even component cracking.
To minimize PCB warpage and thermal stress:
- Use a thermally balanced PCB design with symmetric copper distribution
- Minimize the temperature gradient across the PCB by using multiple heating zones and/or selective heating
- Use a low-stress solder mask material and avoid thick masks around the BGA area
- Control the reflow peak temperature and time to avoid overheating the assembly
- Use a slow cooling rate to allow the PCB and components to relax and equalize
The use of a convection reflow oven with good temperature uniformity and control is also important to ensure consistent and reliable reflow results.
Implement Process Controls and Monitoring
Like any other process, reflow soldering requires proper controls and monitoring to maintain quality and prevent defects. Some key process control measures include:
- Regularly verify and calibrate the reflow oven temperature profiles using thermocouples or profilers
- Monitor the oven performance using SPC tools and control charts
- Implement a moisture control program for handling moisture-sensitive components
- Use nitrogen or inert atmosphere if needed to reduce oxidation and improve wetting
- Perform visual inspection and x-ray inspection on a sample basis to check for any defects or anomalies
- Conduct periodic cross-sectioning and/or solder joint reliability testing to validate the process
By implementing these process controls and monitoring, you can ensure a stable and capable reflow soldering process for BGA assembly.
FAQs
1. What are the most common defects in BGA assembly?
The most common defects in BGA assembly include:
- Open solder joints: Where there is no electrical connection between the BGA ball and PCB pad
- Solder bridging: Where solder melts and connects adjacent balls or pads, causing a short
- Head-in-pillow (HIP): Where the BGA ball doesn’t collapse completely onto the PCB pad, resulting in a weak or open joint
- Misalignment: Where the BGA component is not placed accurately on the pads, causing opens or shorts
- Solder voids: Where there are gaps or holes inside the solder joint, reducing the strength and reliability
2. How can I troubleshoot BGA assembly issues?
To troubleshoot BGA assembly issues, you can follow these steps:
- Visually inspect the assembly for any obvious defects or anomalies using a microscope or camera
- Use x-ray inspection to check for hidden defects such as voids, HIP, or misalignment
- Review the process data and control charts to identify any trends or outliers
- Perform failure analysis on defective assemblies, such as cross-sectioning or dye-and-pry testing
- Review the PCB design, stencil design, and component specs for any potential issues or non-conformances
- Verify the reflow profile and oven performance using thermocouples or profilers
- Consult with your suppliers, assembly partners, or industry experts for guidance and support
3. What is the best solder paste for BGA assembly?
The best solder paste for BGA assembly depends on various factors, such as the BGA package type, pitch, PCB surface finish, and reflow profile. In general, a solder paste with the following characteristics is preferred:
- Fine particle size (Type 4 or Type 5) to minimize solder balling and bridging
- Good printability and paste release to ensure consistent and accurate deposits
- Wide reflow process window to accommodate different profiles and oven types
- Low voiding tendency to minimize solder joint voids
- Good wetting and spreading properties to ensure complete and reliable solder joints
Some popular solder paste choices for BGA assembly include SAC305 (96.5Sn/3.0Ag/0.5Cu), Innolot (91.8Sn/4.0Ag/1.5Cu/1.4Sb/1.0Bi), and SN100C (99.3Sn/0.7Cu+Ni).
4. How do I select the right BGA package for my application?
To select the right BGA package for your application, you need to consider the following factors:
- I/O count and pitch: Choose a BGA package that provides enough I/Os for your design, while considering the PCB Fabrication and assembly capability for the pitch
- Thermal performance: Select a BGA package with good thermal dissipation properties, such as a heat slug or exposed pad, if your application has high power requirements
- Electrical performance: Consider the signal integrity and power delivery requirements of your application, and choose a BGA package with suitable layer stack-up and power/ground planes
- Size and weight: Choose a BGA package that fits within your application’s size and weight constraints, while providing enough clearance for assembly and testing
- Cost and availability: Consider the cost and lead time of the BGA package, as well as the compatibility with your assembly and test processes
It’s recommended to consult with your BGA supplier or design partner to select the best package option for your specific application.
5. What is the future outlook for BGA assembly?
The future outlook for BGA assembly is positive, driven by the increasing demand for miniaturization, high functionality, and high performance in electronic products. Some key trends and developments in BGA assembly include:
- Finer pitch and smaller form factor BGAs, such as 0.3mm pitch and 0.4mm ball diameter, to enable higher I/O density and smaller PCB sizes
- Advanced package technologies, such as fan-out wafer-level packaging (FOWLP) and 2.5D/3D integration, to provide more design flexibility and heterogeneous integration
- Improved assembly processes and equipment, such as high-precision printers and placement machines, to handle the challenges of finer pitch and smaller packages
- Increased use of simulation and modeling tools to optimize PCB design, stencil design, and reflow profiles for BGA assembly
- Growing adoption of advanced materials, such as low-temperature solders and high-performance substrates, to improve the reliability and performance of BGA solder joints
As the electronics industry continues to evolve and innovate, BGA assembly will remain a critical technology for enabling the next generation of products and applications.
No responses yet