What is Wave Soldering?
Wave soldering is a method of soldering electronic components to a PCB using a molten solder wave. The process involves the following steps:
- PCB preparation: The PCB is designed with through-hole components and solder pads on the bottom side.
- Flux application: A thin layer of flux is applied to the bottom of the PCB to improve solder wettability and prevent oxidation.
- Preheating: The PCB is preheated to activate the flux and minimize thermal shock to the components during soldering.
- Wave soldering: The PCB is passed over a wave of molten solder, which wicks up through the holes and creates electrical connections between the components and the PCB.
- Cooling and cleaning: The soldered PCB is cooled and cleaned to remove any excess flux or solder residue.
Wave soldering is particularly suitable for through-hole components and can handle high-volume production runs efficiently.
What is Reflow Soldering?
Reflow soldering is a process that involves applying solder paste to specific areas of a PCB and then heating the entire board in a controlled manner to melt the solder and create electrical connections. The process consists of the following steps:
- PCB preparation: The PCB is designed with surface mount components and solder pads on the top side.
- Solder paste application: Solder paste, a mixture of tiny solder particles and flux, is applied to the solder pads using a stencil or syringe.
- Component placement: Surface mount components are placed onto the solder paste using pick-and-place machines or by hand.
- Reflow: The PCB is passed through a reflow oven, which heats the board in a controlled manner, causing the solder paste to melt and form electrical connections between the components and the PCB.
- Cooling and inspection: The soldered PCB is cooled and inspected for any defects or issues.
Reflow soldering is the preferred method for surface mount components and is well-suited for high-density PCB designs.
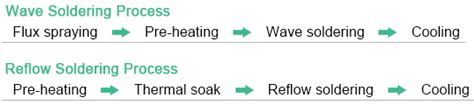
Key Differences Between Wave Soldering and Reflow Soldering
Component Types
One of the primary differences between wave soldering and reflow soldering is the type of components they can handle:
Soldering Method | Suitable Component Types |
---|---|
Wave Soldering | Through-hole components |
Reflow Soldering | Surface mount components |
Wave soldering is designed for through-hole components, which have long leads that are inserted into holes drilled in the PCB. The molten solder wave fills these holes, creating a strong mechanical and electrical connection.
Reflow soldering, on the other hand, is used for surface mount components, which have small leads or terminations that are soldered directly onto the surface of the PCB. The solder paste applied to the pads melts during the reflow process, forming the electrical connection.
Process Flow
The process flow for wave soldering and reflow soldering differs significantly:
Process Step | Wave Soldering | Reflow Soldering |
---|---|---|
PCB Preparation | Through-hole components, solder pads on the bottom side | Surface mount components, solder pads on the top side |
Flux Application | Thin layer of flux applied to the bottom of the PCB | Solder paste (containing flux) applied to solder pads |
Preheating | PCB preheated to activate flux and minimize thermal shock | Not required as a separate step |
Soldering | PCB passed over a wave of molten solder | PCB passed through a reflow oven to melt solder paste |
Component Placement | Components inserted into holes before soldering | Components placed onto solder paste before reflow |
Cooling and Cleaning | Soldered PCB cooled and cleaned to remove excess flux or solder | Soldered PCB cooled and inspected for defects |
The process flow for wave soldering involves applying flux, preheating the PCB, and passing it over a wave of molten solder. Components are inserted into the holes before the soldering process begins.
In contrast, the reflow soldering process starts with applying solder paste to the pads, followed by placing the surface mount components onto the paste. The PCB then passes through a reflow oven, which melts the solder paste to form the electrical connections.
Equipment and Setup
The equipment and setup required for wave soldering and reflow soldering also differ:
Soldering Method | Key Equipment |
---|---|
Wave Soldering | – Wave soldering machine with molten solder bath |
– Fluxing system | |
– Preheating unit | |
– Conveyor system | |
Reflow Soldering | – Solder paste printer or dispenser |
– Pick-and-place machine (for high-volume production) | |
– Reflow oven with controlled heating zones | |
– Conveyor system |
Wave soldering requires a specialized machine that maintains a molten solder bath and a pump to create the solder wave. A fluxing system, preheating unit, and conveyor system are also necessary for the wave soldering process.
Reflow soldering, in contrast, relies on a solder paste printer or dispenser to apply the solder paste accurately. For high-volume production, a pick-and-place machine is used to place the components onto the PCB. The reflow oven, with its controlled heating zones, is the key piece of equipment for melting the solder paste and forming the connections.
Suitability for Different PCB Designs
The choice between wave soldering and reflow soldering often depends on the specific PCB design and its requirements:
PCB Design Aspect | Wave Soldering | Reflow Soldering |
---|---|---|
Component Density | Suitable for low to medium density PCBs | Ideal for high-density PCBs with closely spaced components |
Mixed Components | Can accommodate a mix of through-hole and surface mount components | Limited ability to handle through-hole components |
PCB Size | Can handle larger PCBs | Better suited for smaller PCBs |
Fine-Pitch Components | Not suitable for fine-pitch surface mount components | Can handle fine-pitch surface mount components |
Wave soldering is generally used for PCBs with low to medium component density and can accommodate a mix of through-hole and surface mount components. It is also suitable for larger PCBs.
Reflow soldering, on the other hand, is ideal for high-density PCBs with closely spaced surface mount components. It can handle fine-pitch components but has limited ability to accommodate through-hole components. Reflow soldering is better suited for smaller PCBs.
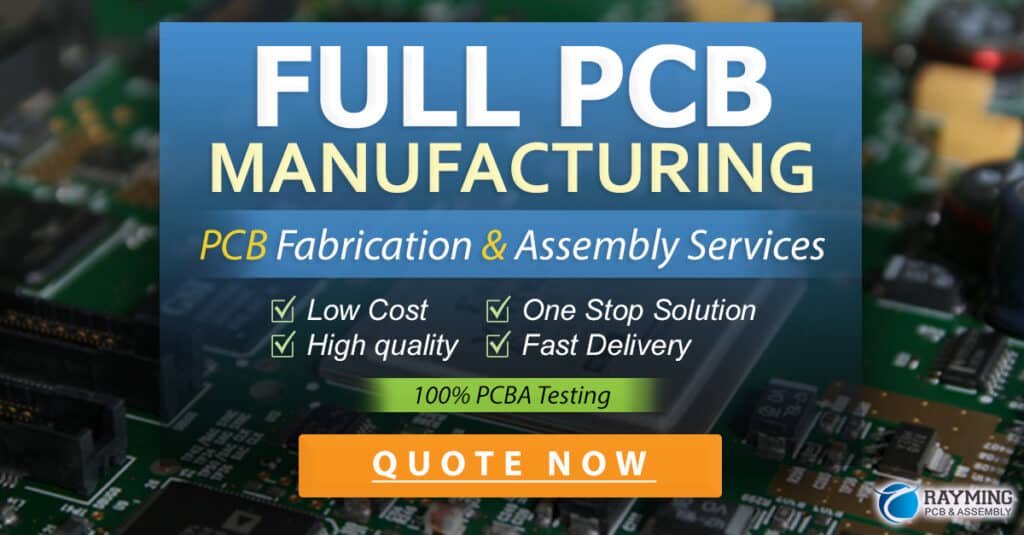
Advantages and Disadvantages of Wave Soldering and Reflow Soldering
Both wave soldering and reflow soldering have their own set of advantages and disadvantages, which should be considered when choosing the appropriate method for a specific project.
Advantages of Wave Soldering
- Efficient for high-volume production of through-hole components
- Can accommodate a mix of through-hole and surface mount components
- Suitable for larger PCBs
- Provides strong mechanical connections for through-hole components
Disadvantages of Wave Soldering
- Not suitable for fine-pitch surface mount components
- Requires more manual handling and setup
- Higher risk of thermal shock to components
- Potential for solder bridges and icicles
Advantages of Reflow Soldering
- Ideal for high-density PCBs with surface mount components
- Can handle fine-pitch components
- Highly automated process, reducing manual labor
- More precise and consistent solder joints
- Lower risk of thermal shock to components
Disadvantages of Reflow Soldering
- Limited ability to handle through-hole components
- Requires precise control of solder paste application and reflow profile
- Higher setup costs for equipment and stencils
- Not suitable for larger PCBs
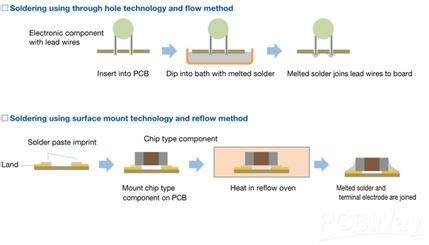
Frequently Asked Questions (FAQ)
-
Can wave soldering and reflow soldering be used together on the same PCB?
Yes, it is possible to use both wave soldering and reflow soldering on the same PCB, especially when the board contains a mix of through-hole and surface mount components. In such cases, the surface mount components are typically reflow soldered first, followed by a wave soldering process for the through-hole components. -
How do I choose between wave soldering and reflow soldering for my project?
The choice between wave soldering and reflow soldering depends on several factors, including the types of components used (through-hole or surface mount), the density of the components on the PCB, the size of the PCB, and the production volume. Consider the advantages and disadvantages of each method and consult with experienced PCB assembly professionals to determine the best approach for your specific project. -
What is selective soldering, and how does it differ from wave soldering?
Selective soldering is a specialized form of wave soldering that targets specific areas of a PCB, rather than exposing the entire board to a molten solder wave. This method is useful when a PCB contains a mix of through-hole and surface mount components, or when certain components are sensitive to the high temperatures of the wave soldering process. Selective soldering machines use mini-waves or solder pots to apply solder only to the desired areas, minimizing the risk of damage to sensitive components. -
Are there any environmental concerns associated with wave soldering and reflow soldering?
Both wave soldering and reflow soldering processes have environmental considerations. Lead-based solder, which was widely used in the past, has been largely phased out due to health and environmental concerns. Today, lead-free solder alloys are used in most soldering processes. However, the fluxes used in both wave soldering and reflow soldering can produce fumes and require proper ventilation and handling. Additionally, the energy consumption of the equipment used in these processes should be taken into account when evaluating the environmental impact of PCB assembly. -
How can I ensure the quality of solder joints in wave soldering and reflow soldering?
Ensuring the quality of solder joints in both wave soldering and reflow soldering requires careful control of various parameters. For wave soldering, the key factors include the solder wave height, the preheat temperature, the conveyor speed, and the flux application. In reflow soldering, the solder paste application, component placement accuracy, and the reflow temperature profile are critical. Implementing proper process controls, regular maintenance of equipment, and thorough inspection of soldered PCBs can help maintain high-quality solder joints in both methods.
Conclusion
Wave soldering and reflow soldering are two essential methods used in the PCB assembly process, each with its own unique characteristics, advantages, and disadvantages. Understanding the differences between these two soldering techniques is crucial for making informed decisions when designing and manufacturing electronic devices.
Wave soldering is particularly suitable for through-hole components and can handle a mix of component types, while reflow soldering is ideal for high-density PCBs with surface mount components. The choice between these methods depends on various factors, such as the PCB design, component types, and production volume.
By familiarizing yourself with the key distinctions between wave soldering and reflow soldering, you can optimize your PCB assembly process, ensure the quality of solder joints, and create reliable electronic products. As technology continues to advance, staying informed about the latest developments in soldering techniques will help you stay competitive in the ever-evolving electronics manufacturing industry.
No responses yet