What is Solder Paste?
Solder paste is a key material used in surface mount assembly of printed circuit boards (PCBs). It is a suspension of tiny solder particles in a flux medium. The solder particles are typically an alloy of tin, lead, and silver, though lead-free versions are increasingly common. The flux serves to clean the metal surfaces, prevent oxidation, and promote wetting and spreading of the solder.
When solder paste is heated above its melting point during reflow soldering, the solder particles melt and the flux vaporizes, allowing the solder to form strong electrical and mechanical bonds between component leads and PCB pads. Selecting the right solder paste and using proper storage and application techniques are critical for achieving high-quality, reliable solder joints in electronics assembly.
Key Properties of Solder Paste
There are several important characteristics to consider when choosing a solder paste:
Alloy Composition
The most common solder alloys for electronics assembly are tin-lead (SnPb) and lead-free tin-silver-copper (SAC). SnPb is eutectic at 63% tin and 37% lead, melting at 183°C. Due to RoHS regulations, lead-free SAC alloys like SAC305 (96.5% tin, 3% silver, 0.5% copper) are now widely used, with a melting point of 217–220°C.
Solder Alloy | Tin (Sn) | Lead (Pb) | Silver (Ag) | Copper (Cu) | Melting Point |
---|---|---|---|---|---|
Sn63/Pb37 | 63% | 37% | – | – | 183°C |
SAC305 | 96.5% | – | 3% | 0.5% | 217-220°C |
Particle Size
Solder paste is classified by the size of the solder particles, indicated by mesh size or Type designations. Smaller particles allow printing finer pitches and result in fewer solder balls. Common particle sizes range from Type 3 (25-45 μm) to Type 6 (5-15 μm).
Type | Mesh Size | Particle Size Range |
---|---|---|
Type 3 | -325/+500 | 25-45 μm |
Type 4 | -400/+635 | 20-38 μm |
Type 5 | -500/+635 | 10-25 μm |
Type 6 | -635 | 5-15 μm |
Flux Type
The flux in solder paste can be rosin-based (R), water-soluble (WS/ORH), or no-clean (NC). Rosin and water-soluble fluxes require cleaning after reflow, while no-clean fluxes leave minimal residue.
Flux Type | Cleaning Required | Residue | Activity Level |
---|---|---|---|
Rosin (R) | Yes | Moderate | Low-Moderate |
Water-soluble (WS/ORH) | Yes | High | High |
No-clean (NC) | No | Minimal | Low |
Viscosity
Solder paste viscosity determines its printability, slump resistance, and tack life. Viscosity is measured in centipoise (cP) and typically ranges from 400,000 to 1,000,000 cP. Higher viscosity pastes print better and slump less but can be harder to release from fine-pitch stencils.
Metal Load
Metal load refers to the percentage of solder particles by weight in the paste. Higher metal loads (88-90%) provide good wetting but can compromise printability. Lower metal loads (85-87%) improve printability and release from stencils. Metal-free zones in the stencil design can prevent bridging with high metal load pastes.
Solder Paste Storage and Handling
Proper storage and handling of solder paste are essential for maintaining its quality and performance:
Refrigerated Storage
Unopened solder paste should be stored at 0-10°C to maximize shelf life, typically 6-12 months. Allow refrigerated paste to warm to room temperature naturally for 4-6 hours before opening to prevent moisture condensation.
Room Temperature Storage
Opened jars or cartridges can be stored at room temperature for up to 1 month. Keep the container tightly sealed when not in use to prevent solvent evaporation and flux separation. Working life is around 4-8 hours on the stencil.
Kneading and Stirring
Before using, knead jar paste or stir cartridge paste gently to ensure even flux distribution. Avoid introducing air bubbles.
Thawing Paste
If paste has been chilled below room temperature, allow it to thaw naturally. Do not heat the paste to accelerate thawing, as this can degrade rheology and cause flux separation.
Scoop and Print
Use clean stainless steel spatulas to transfer paste from jars to stencils. Avoid using squeeze bottles, which can cause flux separation. Print promptly after scooping to minimize exposure to air.
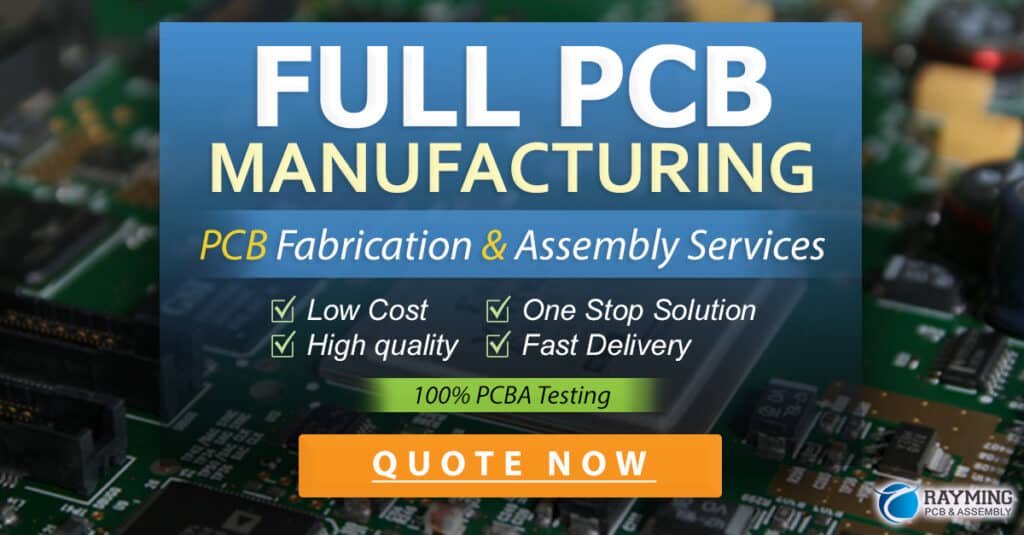
Solder Paste Application
Stencil printing is the most common method of applying solder paste to PCB pads:
Stencil Design
Stencils are typically laser-cut from stainless steel foils. Aperture sizes should be slightly larger (10-20%) than pad sizes to allow for paste shrinkage during reflow. Include aperture reductions of 25-50% in fine-pitch and high-density areas to minimize bridging. Stencil thickness ranges from 100-150 μm (4-6 mils), with thinner stencils used for finer pitches.
Squeegee Blades
Metal squeegee blades (stainless steel or nickel) provide the most consistent printing results. Specify a squeegee length at least 25 mm (1 inch) longer than the stencil width. Squeegee durometer (hardness) should be around 90A for metal blades.
Printing Parameters
- Alignment: Align the stencil apertures to the PCB pads using fiducials or vision systems.
- Pressure: Squeegee pressure affects paste deposit volume. Higher pressure (0.3-0.5 kg/cm) works better for fine-pitch and is more forgiving of stencil wear. Lower pressure (0.2-0.3 kg/cm) is better for standard pitches.
- Speed: Squeegee speeds of 20-70 mm/s are typical. Slower speeds allow the paste to roll in front of the blade for more consistent prints. Faster speeds can improve cycle time but may introduce defects.
- Separation: “Snap-off” the stencil from the PCB at a controlled speed (1-5 mm/s) to allow the paste to cleanly release from the apertures.
- Understencil Cleaning: Wipe the bottom of the stencil regularly (every 5-10 prints) with a lint-free cloth and solvent to remove paste residue. Isopropyl alcohol (IPA) is commonly used.
Print Inspection
After printing, inspect the paste deposits for consistent volume and shape. 2D Automated Optical Inspection (AOI) systems can measure paste area and height. 3D Solder Paste Inspection (SPI) systems use laser triangulation or structured light to provide more detailed volume measurements. Correct any print defects before reflowing the PCB.
Solder Paste Reflow
After printing and placing components, the solder paste is reflowed in a controlled heating process:
Reflow Profile
The reflow oven heats the PCB and components according to a temperature profile, typically with 4 stages:
- Preheat: Gradually ramp from room temperature to 150-180°C at 0.5-2°C/s. This activates the flux and evaporates solvents.
- Soak: Maintain preheat temperature for 60-120s to allow components to equilibrate and flux to clean surfaces.
- Reflow: Quickly ramp to 20-40°C above solder melting point and hold for 30-90s. This allows the solder to melt, wet, and form intermetallic bonds. Peak temperature and time above liquidus (TAL) are critical.
- Cooling: Cool PCB back to room temperature at < 4°C/s to solidify joints and prevent thermal shock.
The exact profile parameters depend on the solder paste specification and the PCB/component thermal mass. Follow paste manufacturer guidelines and optimize the profile for your process.
Defect Inspection
After reflow, inspect solder joints visually or with AOI for defects such as:
- Bridging: Solder shorts between adjacent pads/pins
- Insufficient Solder: Solder joint with low volume or poor wetting
- Tombstoning: Component lifting up on one end due to uneven heating or pad sizes
- Solder Beads/Balls: Small solder spheres near joints from spattered paste
- Voiding: Holes within the solder joint from flux outgassing or moisture
- Dewetting: Solder not adhering to pad or component surfaces
X-ray inspection can detect voids or other defects not visible from the surface. Cross-sectioning and metallurgical analysis may be used to diagnose chronic defects. Rework localized defects as necessary.
Solder Paste FAQ
What is the shelf life of solder paste?
Unopened refrigerated solder paste typically has a shelf life of 6-12 months. Consult the manufacturer’s datasheet and date code for specifics.
How long can I store an opened jar of paste at room temperature?
An opened jar or cartridge of paste can be stored at room temperature for about 1 month. Keep it tightly sealed when not in use to prevent drying out or flux separation.
What is the difference between no-clean and water-soluble solder pastes?
No-clean pastes have a flux that leaves minimal inert residue after reflow, not requiring cleaning. Water-soluble pastes have a more active flux that must be removed with DI water after reflow. No-clean pastes are more common, but water-soluble may be used for high-reliability assemblies.
What solder paste particle size should I use for my PCB?
Solder paste Type 3 (25-45 μm) or Type 4 (20-38 μm) is most common for typical SMT assembly with part pitches down to 0.4 mm. Type 5 (10-25 μm) or Type 6 (5-15 μm) may be needed for fine-pitch components with leadless terminations. Smaller particles allow finer printing but can be harder to handle.
How do I choose a solder paste flux type?
Select a no-clean solder paste first when possible, as it simplifies the assembly process and is suitable for most applications. If the assembly will be conformal coated, is high-reliability, or has sensitive RF circuitry, consider a water-soluble paste. Rosin pastes are less common but may be needed for specialized military/aerospace projects.
In summary, selecting the right solder paste and implementing effective storage, printing, and reflow processes are key to successful SMT assembly. Consider the solder alloy, particle size, flux type, and viscosity required for your components and PCB design. Follow proper cold storage and room temperature handling procedures to maintain paste quality. Optimize the stencil design, printing parameters, and reflow profile to achieve consistent paste volumes and high-quality solder joints. Inspect prints and reflowed assemblies to quickly identify and correct any defects. With the appropriate solder paste material and process controls, you can ensure reliable PCB Assembly performance and yield.
No responses yet