Introduction: SpaceX and the Importance of PCB Technology
SpaceX, founded by visionary entrepreneur Elon Musk, has revolutionized the aerospace industry with its groundbreaking achievements in rocket technology and space exploration. From successfully landing reusable rockets to launching astronauts to the International Space Station, SpaceX has pushed the boundaries of what’s possible. But behind these incredible feats lies a critical component that often goes unnoticed: the humble printed circuit board (PCB).
PCBs are the backbone of modern electronics, and their evolution has played a crucial role in enabling SpaceX to achieve its ambitious goals. In this article, we’ll explore how advancements in PCB design and manufacturing have supported SpaceX’s visions and paved the way for a new era of space exploration.
The Role of PCBs in Aerospace Applications
Printed circuit boards are essential in aerospace applications, where reliability, durability, and performance are paramount. In the harsh conditions of space, PCBs must withstand extreme temperatures, vibrations, and radiation while maintaining optimal functionality. SpaceX’s rockets and spacecraft rely on a complex network of PCBs to control various systems, including:
- Propulsion
- Navigation
- Communication
- Life support
- Payload management
The failure of a single PCB can have catastrophic consequences, making it crucial for SpaceX to leverage the latest advancements in PCB technology to ensure the success of their missions.
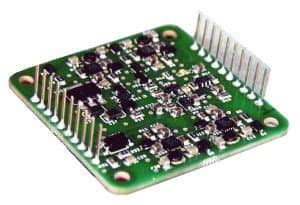
The Evolution of PCB Design and Manufacturing
Over the years, PCB design and manufacturing have undergone significant transformations, enabling the creation of more sophisticated and reliable boards. Some of the key milestones in PCB evolution include:
Era | Advancements |
---|---|
1950s | – Introduction of through-hole technology – Manual design and fabrication processes |
1960s-1970s | – Development of surface-mount technology (SMT) – Adoption of computer-aided design (CAD) tools |
1980s-1990s | – Multilayer PCBs become commonplace – Automated assembly processes gain traction |
2000s-Present | – High-density interconnect (HDI) PCBs emerge – Advanced materials and manufacturing techniques |
These advancements have allowed for the creation of smaller, lighter, and more complex PCBs, which are essential for SpaceX’s rockets and spacecraft, where space and weight are at a premium.
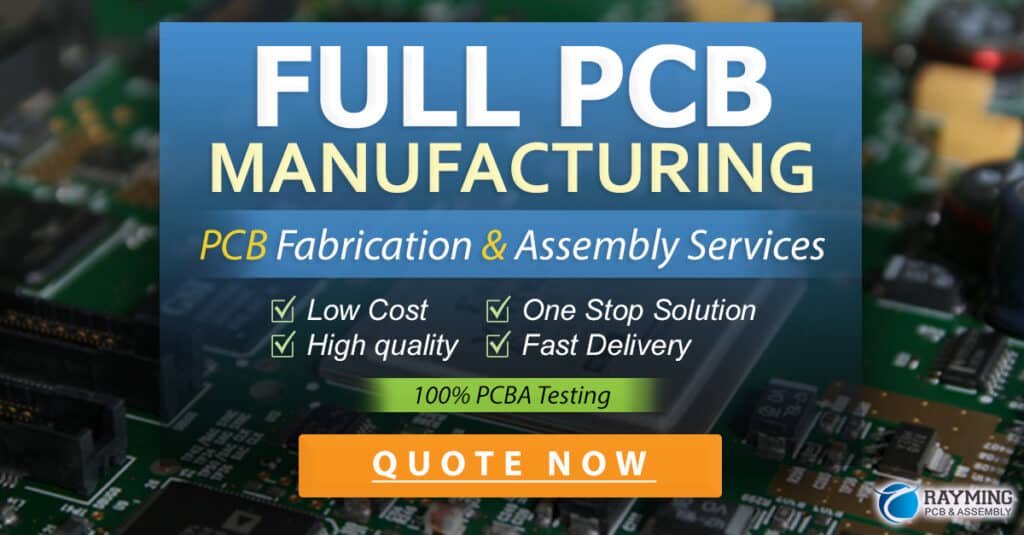
SpaceX’s PCB Design Challenges and Solutions
Designing PCBs for SpaceX’s applications presents unique challenges that require innovative solutions. Some of the key challenges and how SpaceX has addressed them include:
Vibration and Shock Resistance
During launch and flight, SpaceX’s rockets and spacecraft experience intense vibrations and shock loads. To ensure PCBs can withstand these conditions, SpaceX employs several techniques:
- Using high-quality, aerospace-grade materials
- Implementing robust mechanical supports and dampening mechanisms
- Conducting rigorous testing and simulation to validate PCB performance
Thermal Management
The extreme temperature fluctuations in space can cause PCBs to expand and contract, leading to potential failures. SpaceX addresses this challenge by:
- Selecting materials with low coefficients of thermal expansion (CTE)
- Incorporating thermal management features, such as heat sinks and thermal vias
- Designing PCBs with adequate spacing and ventilation to dissipate heat
Radiation Hardening
Space is a harsh radiation environment that can damage electronic components, including PCBs. To mitigate this risk, SpaceX employs radiation-hardening techniques, such as:
- Using radiation-tolerant components and materials
- Implementing redundancy and error-correction mechanisms
- Shielding sensitive components with protective layers
By addressing these challenges head-on, SpaceX ensures that its PCBs can perform reliably in the demanding conditions of space.
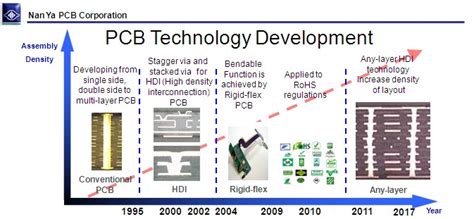
Advanced PCB Technologies Used by SpaceX
SpaceX leverages cutting-edge PCB technologies to push the boundaries of what’s possible in space exploration. Some of the advanced techniques and materials used by SpaceX include:
High-Density Interconnect (HDI) PCBs
HDI PCBs allow for the creation of highly complex and compact designs, which are essential for SpaceX’s rockets and spacecraft. By using fine-pitch components, microvias, and buried/blind vias, SpaceX can pack more functionality into smaller PCBs, reducing weight and saving space.
Flexible and Rigid-Flex PCBs
Flexible and rigid-flex PCBs offer several advantages for aerospace applications, including:
- Improved vibration and shock resistance
- Reduced weight and space requirements
- Enhanced signal integrity and reliability
SpaceX uses these types of PCBs in areas where flexibility and durability are critical, such as in deployable solar arrays and communication antennas.
Advanced Materials
SpaceX employs a range of advanced materials in its PCBs to ensure optimal performance and reliability. Some of these materials include:
- Polyimide: A high-temperature, low-CTE material that offers excellent thermal stability and mechanical strength.
- Ceramic: Used in high-frequency and high-power applications due to its excellent electrical and thermal properties.
- Metal core: Provides superior thermal management and mechanical stability for power-intensive applications.
By leveraging these advanced technologies and materials, SpaceX can create PCBs that are well-suited for the rigors of space exploration.
The Future of PCB Design in Space Exploration
As SpaceX continues to push the boundaries of space exploration, the role of PCB design will only become more critical. Future advancements in PCB technology are expected to enable even more ambitious missions, such as:
Interplanetary Travel
PCBs will play a crucial role in the development of spacecraft capable of carrying humans to Mars and beyond. These long-duration missions will require highly reliable and robust PCBs that can withstand the challenges of deep space travel.
Space Habitats
As humanity establishes a permanent presence in space, PCBs will be essential in the construction and operation of space habitats. These self-sustaining environments will rely on advanced PCBs to control life support systems, power generation, and communication networks.
In-Space Manufacturing
The ability to manufacture and repair PCBs in space will be a game-changer for long-duration missions and space habitats. In-space manufacturing technologies, such as 3D printing and robotic assembly, will enable the creation of custom PCBs on-demand, reducing the need for costly and time-consuming resupply missions.
As PCB technology continues to evolve, SpaceX and other space exploration companies will be well-positioned to take advantage of these advancements and push the boundaries of what’s possible in the final frontier.
Frequently Asked Questions (FAQ)
-
Q: Why are PCBs so important for SpaceX’s rockets and spacecraft?
A: PCBs are the backbone of modern electronics and are essential for controlling various systems in SpaceX’s rockets and spacecraft, including propulsion, navigation, communication, life support, and payload management. The reliability and performance of these PCBs are critical to the success of SpaceX’s missions. -
Q: What are some of the key challenges in designing PCBs for aerospace applications?
A: Designing PCBs for aerospace applications presents unique challenges, such as vibration and shock resistance, thermal management, and radiation hardening. SpaceX addresses these challenges by using high-quality materials, implementing robust mechanical supports, and employing advanced design techniques like HDI and flexible PCBs. -
Q: How have advancements in PCB technology supported SpaceX’s achievements?
A: Advancements in PCB technology, such as surface-mount technology, multilayer boards, and automated assembly processes, have allowed for the creation of smaller, lighter, and more complex PCBs. These advancements have been crucial in enabling SpaceX to develop the sophisticated electronics needed for its rockets and spacecraft. -
Q: What role will PCB design play in the future of space exploration?
A: As space exploration continues to advance, PCB design will play an increasingly critical role in enabling ambitious missions like interplanetary travel, space habitats, and in-space manufacturing. Future advancements in PCB technology are expected to support the development of highly reliable and robust electronics capable of withstanding the challenges of deep space travel. -
Q: How does SpaceX ensure the reliability of its PCBs in the harsh conditions of space?
A: SpaceX employs several techniques to ensure the reliability of its PCBs in space, including using aerospace-grade materials, implementing redundancy and error-correction mechanisms, and conducting rigorous testing and simulation to validate PCB performance. Additionally, SpaceX leverages advanced technologies like HDI, flexible PCBs, and specialized materials to create boards that can withstand the extreme conditions of space.
Conclusion
The evolution of PCB design has been a critical factor in allowing SpaceX to achieve its ambitious visions for space exploration. From the introduction of through-hole technology in the 1950s to the advanced techniques and materials used today, PCB technology has continuously adapted to meet the unique challenges of aerospace applications.
SpaceX has leveraged these advancements to create highly reliable and performant PCBs that form the backbone of its rockets and spacecraft. By employing innovative solutions to challenges like vibration, thermal management, and radiation hardening, SpaceX has pushed the boundaries of what’s possible in space exploration.
As we look to the future, it’s clear that PCB design will continue to play a crucial role in enabling the next generation of space missions. From interplanetary travel to space habitats and in-space manufacturing, the success of these ambitious endeavors will depend on the development of ever more sophisticated and reliable PCBs.
SpaceX, with its commitment to innovation and its track record of success, is well-positioned to lead the way in this exciting new era of space exploration. And as PCB technology continues to evolve, we can expect to see even more incredible achievements from SpaceX and other pioneers in the aerospace industry.
No responses yet