Introduction to PCB Testing
Printed Circuit Board (PCB) assembly is a complex process involving multiple steps to create the final product that will be used in electronic devices. To ensure the quality and reliability of the PCB, it is crucial to conduct thorough testing at various stages of the assembly process. Functional testing, also known as PCBA FCT (Printed Circuit Board Assembly Functional Circuit Testing), is a critical step in validating the performance and functionality of the assembLED PCB.
In this article, we will explore the importance of functional testing in PCB Assembly, the different types of tests involved, and the associated costs. We will also discuss how to optimize the testing process to achieve the best results while managing costs effectively.
Why is Functional Testing Important in PCB Assembly?
Functional testing is essential in PCB assembly for several reasons:
-
Quality Assurance: Functional testing helps identify any defects or issues in the assembled PCB, ensuring that only high-quality products are delivered to the end-user.
-
Reliability: By conducting thorough functional tests, manufacturers can ensure that the PCB will perform as intended and maintain its reliability over its expected lifecycle.
-
Cost Savings: Identifying and rectifying issues early in the assembly process through functional testing can save significant costs associated with repairs, replacements, and recalls later on.
-
Compliance: Functional testing helps ensure that the PCB meets the required industry standards and regulations, such as IPC, UL, and RoHS.
Types of Functional Tests in PCB Assembly
There are various types of functional tests that can be performed on an assembled PCB, depending on the specific requirements and complexity of the board. Some of the most common functional tests include:
In-Circuit Testing (ICT)
In-Circuit Testing is a type of functional test that involves probing the individual components on the PCB to verify their presence, orientation, and functionality. ICT is typically performed using a bed-of-nails fixture that makes contact with the test points on the PCB.
Advantages of ICT:
– Helps identify component-level faults
– Can be automated for high-volume production
– Provides good test coverage
Disadvantages of ICT:
– Requires specialized fixtures and equipment
– May not detect all types of faults (e.g., mechanical issues)
– Can be time-consuming and costly for complex boards
Flying Probe Testing
Flying Probe Testing is an alternative to ICT that uses moving probes to make contact with the test points on the PCB. This method is more flexible than ICT and does not require a dedicated fixture.
Advantages of Flying Probe Testing:
– Flexibility in testing different PCB designs
– No need for custom fixtures
– Can be used for low-volume production or prototypes
Disadvantages of Flying Probe Testing:
– Slower than ICT for high-volume production
– May not provide as comprehensive test coverage as ICT
Boundary Scan Testing
Boundary Scan Testing, also known as JTAG (Joint Test Action Group) testing, is a method that uses a special test access port (TAP) to test the interconnections between integrated circuits on the PCB. This method is particularly useful for testing complex boards with high-density components.
Advantages of Boundary Scan Testing:
– Can test hard-to-reach components and interconnections
– Helps identify shorts, opens, and other faults
– Can be combined with other functional tests for comprehensive coverage
Disadvantages of Boundary Scan Testing:
– Requires JTAG-compliant components
– May not detect all types of faults (e.g., analog issues)
– Can be complex to set up and execute
Functional Test Fixtures (FTF)
Functional Test Fixtures are custom-designed setups that simulate the real-world operating conditions of the PCB. FTFs can include various types of input/output devices, such as switches, LEDs, and connectors, to test the board’s functionality under different scenarios.
Advantages of FTFs:
– Provides a comprehensive test of the PCB’s functionality
– Can simulate real-world conditions and user interactions
– Helps identify issues that may not be detected by other testing methods
Disadvantages of FTFs:
– Requires custom design and fabrication for each PCB
– Can be expensive and time-consuming to develop
– May not be suitable for high-volume production
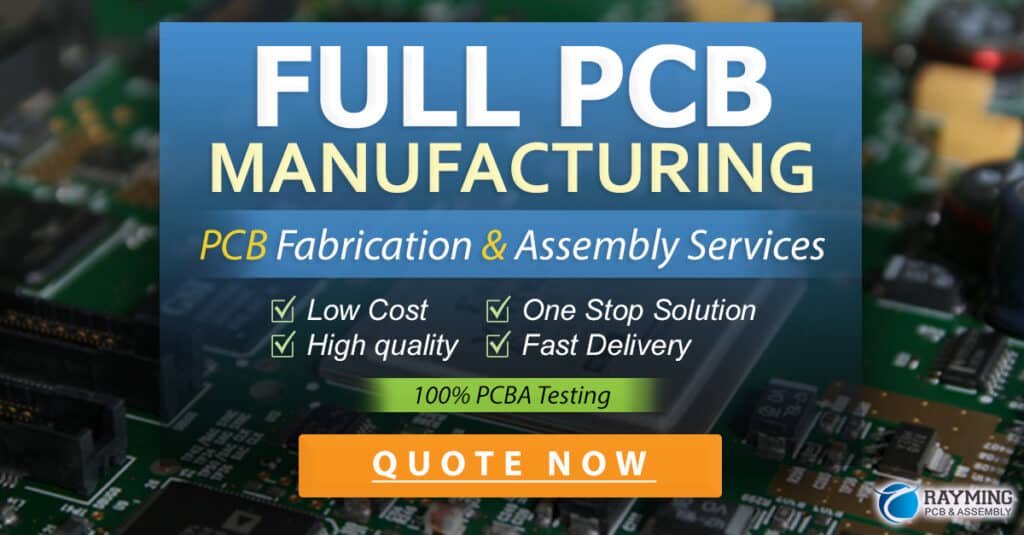
PCBA FCT Costs
The cost of functional testing in PCB assembly can vary significantly depending on factors such as the complexity of the board, the testing methods used, and the volume of production. Let’s take a closer look at some of the key cost drivers in PCBA FCT.
Test Equipment and Fixtures
One of the most significant costs in functional testing is the investment in test equipment and fixtures. Depending on the testing methods used, this can include:
- In-Circuit Test (ICT) machines and fixtures
- Flying Probe testers
- Boundary Scan (JTAG) equipment
- Functional Test Fixtures (FTFs)
The cost of this equipment can range from tens of thousands to hundreds of thousands of dollars, depending on the features and capabilities required. In addition to the initial investment, there are ongoing costs associated with maintenance, calibration, and upgrades.
Test Program Development
Another significant cost driver in PCBA FCT is the development of test programs. For each PCB design, a custom test program must be created to define the test sequence, parameters, and pass/fail criteria. This process can be time-consuming and requires skilled engineers with expertise in the specific testing methods and equipment used.
The cost of test program development can vary depending on the complexity of the PCB and the testing requirements. In some cases, it may be possible to adapt existing test programs for similar designs, which can help reduce development costs.
Labor Costs
Labor costs are another important factor in PCBA FCT, as testing requires skilled technicians to set up, operate, and maintain the test equipment. The number of technicians required and the time needed for testing will depend on the complexity of the PCB, the testing methods used, and the volume of production.
In some cases, it may be more cost-effective to outsource functional testing to a specialized provider, particularly for low-volume production or complex boards that require expensive equipment and expertise.
Cost Optimization Strategies
To manage PCBA FCT costs effectively, manufacturers can employ several strategies:
-
Design for Testability (DFT): By incorporating testability features into the PCB design, such as test points and JTAG interfaces, manufacturers can simplify the testing process and reduce the time and cost of testing.
-
Standardization: Using standardized test equipment and processes across different PCB designs can help reduce the cost of test program development and technician training.
-
Automated Testing: Investing in automated test equipment, such as robotic handlers and conveyors, can help reduce labor costs and increase testing throughput.
-
Outsourcing: For low-volume production or complex boards, outsourcing functional testing to a specialized provider can be more cost-effective than investing in in-house equipment and expertise.
FAQ
1. What is the difference between functional testing and structural testing?
Functional testing focuses on verifying that the PCB performs as intended under real-world operating conditions, while structural testing (such as ICT and Flying Probe Testing) focuses on verifying the presence, orientation, and functionality of individual components on the board.
2. Is functional testing required for all PCBs?
The extent of functional testing required will depend on the specific application and industry standards. In general, functional testing is recommended for PCBs used in critical applications, such as medical devices, aerospace, and automotive systems, where reliability and safety are paramount.
3. How much does functional testing cost?
The cost of functional testing can vary widely depending on factors such as the complexity of the PCB, the testing methods used, and the volume of production. In general, functional testing can account for 5-20% of the total manufacturing cost of a PCB.
4. Can functional testing be automated?
Yes, many aspects of functional testing can be automated using robotic handlers, conveyors, and software-driven test sequences. Automation can help reduce labor costs and increase testing throughput, particularly for high-volume production.
5. What are the benefits of outsourcing functional testing?
Outsourcing functional testing to a specialized provider can offer several benefits, including access to advanced equipment and expertise, reduced capital investment, and increased flexibility in testing capacity. This can be particularly cost-effective for low-volume production or complex boards that require expensive equipment and specialized knowledge.
Conclusion
Functional testing is a critical step in the PCB assembly process, helping ensure the quality, reliability, and performance of the final product. By understanding the different types of functional tests available and the associated costs, manufacturers can make informed decisions about the best testing strategies for their specific needs.
To optimize PCBA FCT costs, manufacturers should consider factors such as design for testability, standardization, automation, and outsourcing. By taking a strategic approach to functional testing, manufacturers can balance the need for thorough testing with the goal of managing costs effectively.
As the complexity of PCBs continues to increase and the demands for quality and reliability grow, functional testing will remain an essential part of the manufacturing process. By staying up-to-date with the latest testing technologies and best practices, manufacturers can ensure that their products meet the highest standards while controlling costs and maximizing profitability.
No responses yet