Introduction to LED PCBs
Light-emitting diode (LED) printed circuit boards (PCBs) are specialized circuit boards designed to power and control LED lights. LED PCBs are used in a wide range of applications, from simple indicator lights to complex lighting systems in automotive, architectural, and industrial settings. A professional LED PCB assembly supplier plays a crucial role in providing high-quality, reliable, and cost-effective LED PCB solutions to meet the diverse needs of customers.
What are LED PCBs?
LED PCBs are circuit boards that are specifically designed to support and power LED components. These PCBs are typically made from a substrate material, such as FR-4, with conductive copper traces that connect the LED components to the power source and other electronic components. LED PCBs can be single-layered or multi-layered, depending on the complexity of the design and the number of components required.
Advantages of LED PCBs
LED PCBs offer several advantages over traditional lighting solutions:
- Energy efficiency: LEDs consume significantly less power compared to incandescent or fluorescent lights, resulting in energy savings.
- Long lifespan: LEDs have a much longer lifespan than traditional light sources, often lasting up to 50,000 hours or more.
- Durability: LEDs are solid-state devices that are resistant to shock, vibration, and extreme temperatures.
- Compact size: LED PCBs can be designed in various sizes and shapes to fit in tight spaces or conform to specific product designs.
- Environmental friendliness: LEDs do not contain hazardous materials, such as mercury, making them a more eco-friendly lighting option.
Choosing a Professional LED PCB Assembly Supplier
When selecting a professional LED PCB assembly supplier, there are several key factors to consider to ensure that you receive high-quality products and services.
Experience and Expertise
Look for a supplier with extensive experience in LED PCB assembly and a proven track record of delivering successful projects. An experienced supplier will have the knowledge and expertise to guide you through the design and manufacturing process, offering valuable insights and recommendations along the way.
Quality Control and Certifications
A professional LED PCB assembly supplier should have strict quality control measures in place to ensure that their products meet or exceed industry standards. Look for suppliers with relevant certifications, such as ISO 9001, ISO 14001, and UL, which demonstrate their commitment to quality, environmental responsibility, and safety.
Manufacturing Capabilities
Consider the supplier’s manufacturing capabilities, including their equipment, technology, and production capacity. A supplier with advanced manufacturing equipment and processes, such as surface-mount technology (SMT) and automated optical inspection (AOI), can produce high-quality LED PCBs with greater efficiency and consistency.
Design Support and Customization
A professional LED PCB assembly supplier should offer design support and customization options to help you create LED PCBs that meet your specific requirements. Look for a supplier that can provide assistance with PCB layout, component selection, and thermal management to optimize the performance and reliability of your LED PCBs.
Lead Time and Delivery
When choosing a supplier, consider their lead time and delivery options. A supplier with short lead times and reliable delivery can help you meet your project deadlines and avoid costly delays. Additionally, look for a supplier that offers flexible order quantities and can accommodate both small and large production runs.
LED PCB Design Considerations
Designing LED PCBs requires careful consideration of several factors to ensure optimal performance, reliability, and longevity.
Thermal Management
LEDs generate heat during operation, which can negatively impact their performance and lifespan if not properly managed. Effective thermal management is crucial in LED PCB design to dissipate heat away from the LEDs and maintain stable operating temperatures. This can be achieved through the use of heat sinks, thermal vias, and other cooling methods.
Current and Voltage Requirements
LEDs have specific current and voltage requirements that must be met to ensure proper operation and avoid damage. LED PCB designs must incorporate appropriate current-limiting resistors and voltage regulators to provide the correct amount of current and voltage to each LED. Additionally, the PCB layout should be designed to minimize voltage drops and ensure even current distribution across the LEDs.
Optical Considerations
The optical performance of LED PCBs is influenced by factors such as LED placement, viewing angle, and color consistency. When designing LED PCBs, consider the desired beam pattern, color temperature, and color rendering index (CRI) to achieve the intended visual effect. The PCB layout should also be optimized to minimize shadowing and ensure uniform light distribution.
Component Selection
Selecting the right components is crucial for the performance and reliability of LED PCBs. Choose high-quality LEDs from reputable manufacturers that meet the required specifications for brightness, color, and efficiency. Other components, such as resistors, capacitors, and connectors, should also be selected based on their performance, reliability, and compatibility with the LED PCB design.
PCB Material and Thickness
The choice of PCB material and thickness can impact the thermal performance, mechanical stability, and overall reliability of LED PCBs. Common PCB materials for LED applications include FR-4, aluminum-backed PCBs, and metal-core PCBs (MCPCBs). The thickness of the PCB should be selected based on the thermal and mechanical requirements of the application, as well as the manufacturing capabilities of the supplier.
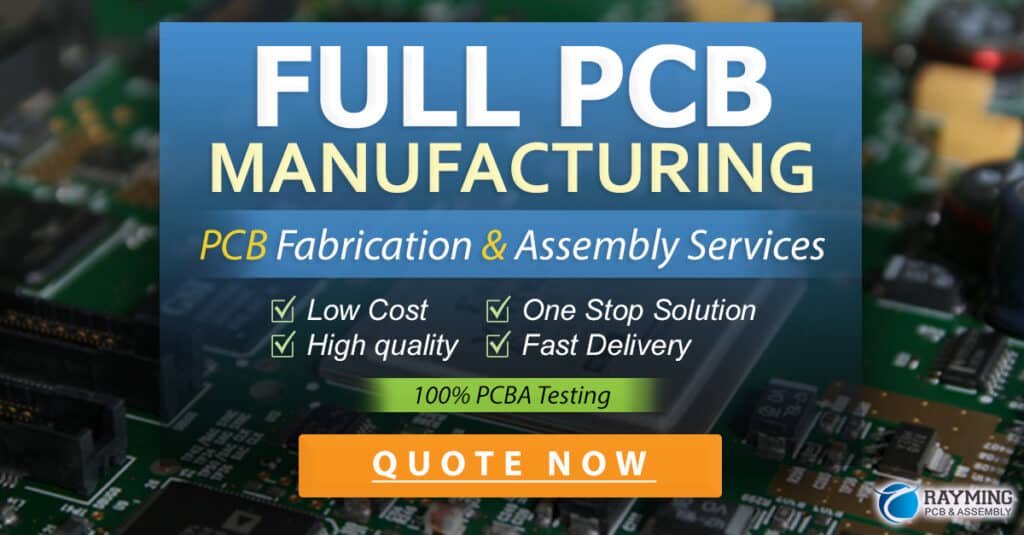
LED PCB Manufacturing Process
The manufacturing process for LED PCBs involves several key steps to ensure high-quality and reliable products.
PCB Fabrication
The first step in LED PCB manufacturing is the fabrication of the bare PCB. This involves creating the conductive copper traces on the substrate material using a photolithographic process. The PCB is then drilled, plated, and finished with a protective solder mask and silkscreen layer.
SMT Assembly
Surface-mount technology (SMT) is the most common method for assembling LED PCBs. In this process, a solder paste is applied to the PCB pads, and the LED components are placed onto the board using an automated pick-and-place machine. The PCB is then sent through a reflow oven, which melts the solder paste and creates a permanent electrical and mechanical connection between the components and the PCB.
Through-Hole Assembly
In some cases, LED PCBs may require through-hole assembly for certain components, such as connectors or larger LED packages. In this process, the component leads are inserted through holes in the PCB and soldered in place using a wave soldering machine or manual soldering techniques.
Inspection and Testing
After assembly, LED PCBs undergo rigorous inspection and testing to ensure quality and functionality. This may include automated optical inspection (AOI) to check for component placement and solder joint quality, as well as functional testing to verify the electrical and optical performance of the LEDs. Other tests, such as thermal cycling and vibration testing, may also be performed to assess the reliability and durability of the LED PCBs.
Packaging and Shipping
Once the LED PCBs have passed inspection and testing, they are packaged for shipping. The packaging should be designed to protect the PCBs from damage during transit and may include anti-static bags, foam inserts, and sturdy outer boxes. The supplier should also provide appropriate documentation, such as packing slips and certificates of conformance, to ensure traceability and compliance with customer requirements.
Applications of LED PCBs
LED PCBs are used in a wide range of applications across various industries, including:
- Automotive lighting: LED PCBs are used in headlights, taillights, interior lighting, and instrument panel illumination in vehicles.
- Architectural lighting: LED PCBs are used in indoor and outdoor lighting fixtures, such as downlights, spotlights, and linear lighting, for commercial and residential buildings.
- Signage and displays: LED PCBs are used in digital signage, billboards, and information displays for advertising and wayfinding.
- Industrial lighting: LED PCBs are used in high-bay lighting, machine vision lighting, and hazardous location lighting for industrial facilities and warehouses.
- Medical devices: LED PCBs are used in medical illumination devices, such as surgical lights, endoscopes, and dental lights.
- Consumer electronics: LED PCBs are used in devices such as smartphones, tablets, laptops, and televisions for backlighting and indicator lights.
Frequently Asked Questions (FAQ)
1. What is the minimum order quantity (MOQ) for LED PCBs?
The minimum order quantity for LED PCBs varies depending on the supplier and the specific product. Some suppliers may offer low MOQs for standard LED PCB designs, while others may require higher MOQs for custom designs or large production runs. It is best to discuss your specific requirements with the supplier to determine their MOQ policies.
2. How long does it take to manufacture LED PCBs?
The lead time for manufacturing LED PCBs depends on several factors, including the complexity of the design, the quantity ordered, and the supplier’s production schedule. Typical lead times can range from a few days to several weeks. Rush production options may be available for urgent projects, but these may come with additional costs.
3. Can LED PCBs be customized to fit my specific application?
Yes, a professional LED PCB assembly supplier should be able to offer customization options to meet your specific application requirements. This may include custom PCB layouts, component selection, and thermal management solutions. The supplier’s design support team can work with you to create an LED PCB that meets your unique needs.
4. How can I ensure the quality and reliability of the LED PCBs?
To ensure the quality and reliability of your LED PCBs, choose a supplier with a proven track record of delivering high-quality products and services. Look for suppliers with relevant certifications, such as ISO 9001 and UL, and ask about their quality control processes and testing procedures. Additionally, provide clear and detailed product specifications and requirements to the supplier to minimize the risk of quality issues.
5. What support services can I expect from an LED PCB assembly supplier?
A professional LED PCB assembly supplier should offer a range of support services to help you throughout the design, manufacturing, and post-production phases. These services may include design support, prototyping, testing, and debugging assistance, as well as technical documentation and after-sales support. Look for a supplier that is responsive, communicative, and willing to work closely with you to ensure the success of your project.
Conclusion
Choosing a professional LED PCB assembly supplier is crucial for ensuring the success of your LED lighting projects. By considering factors such as experience, quality control, manufacturing capabilities, and design support, you can select a supplier that can meet your specific requirements and deliver high-quality LED PCBs. Additionally, understanding the key design considerations, manufacturing processes, and applications of LED PCBs can help you make informed decisions and optimize the performance and reliability of your products. With the right supplier and a thorough understanding of LED PCB technology, you can bring your LED lighting visions to life and stay ahead in the competitive lighting industry.
No responses yet