Introduction to FR PCBs
Printed Circuit Boards (PCBs) are essential components in modern electronics, providing a platform for electrical components to be mounted and interconnected. Among the various types of PCBs, FR-grade boards are widely used due to their excellent mechanical and electrical properties. FR stands for “Flame Retardant,” indicating that these PCBs are designed to be resistant to fire and high temperatures.
In this article, we will focus on FR1 PCBs and compare them with other commonly used FR-grade PCBs, namely FR2, FR3, and FR4. We will explore their differences in terms of material composition, properties, applications, and manufacturing processes.
What is an FR1 PCB?
FR1 PCBs are made from a laminate material that consists of a paper base impregnated with a phenolic resin. The phenolic resin provides the flame-retardant properties and helps to bind the paper layers together. FR1 is the oldest and most basic type of FR-grade PCB material.
Key Characteristics of FR1 PCBs
- Low cost
- Good electrical insulation
- Moderate mechanical strength
- Limited heat resistance
- Suitable for low-frequency applications
FR2 PCBs: A Step Up from FR1
FR2 PCBs are similar to FR1 in terms of their paper-phenolic composition, but they offer slightly better properties. The main difference lies in the quality of the paper used and the resin content. FR2 PCBs have a higher resin content, which results in improved mechanical strength and moisture resistance compared to FR1.
Key Characteristics of FR2 PCBs
- Moderate cost
- Better mechanical strength than FR1
- Improved moisture resistance
- Limited heat resistance
- Suitable for low to medium frequency applications
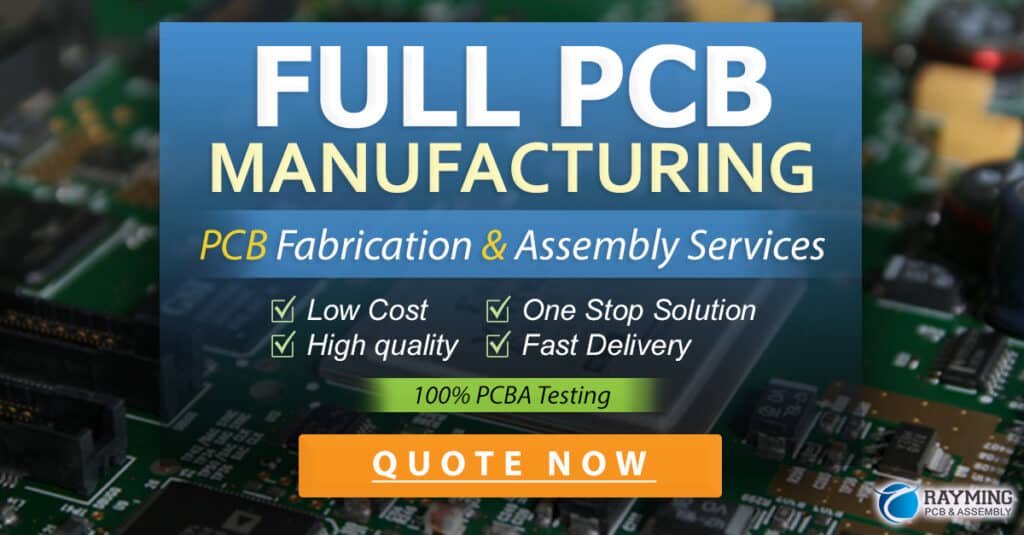
FR3 PCBs: Enhanced Mechanical Properties
FR3 PCBs are made from a combination of paper and epoxy resin, which provides superior mechanical properties compared to FR1 and FR2. The epoxy resin offers better adhesion between the layers and enhances the overall durability of the board. FR3 PCBs are known for their excellent punching and drilling characteristics.
Key Characteristics of FR3 PCBs
- Moderate to high cost
- Excellent mechanical strength
- Good electrical insulation
- Improved heat resistance compared to FR1 and FR2
- Suitable for medium-frequency applications
FR4 PCBs: The Industry Standard
FR4 PCBs are the most widely used type of FR-grade PCBs in the electronics industry. They are made from a glass-reinforced epoxy laminate material, which offers superior mechanical, thermal, and electrical properties compared to the other FR-grade PCBs.
Key Characteristics of FR4 PCBs
- High cost compared to FR1, FR2, and FR3
- Excellent mechanical strength and durability
- High glass transition temperature (Tg)
- Good electrical insulation and dielectric properties
- Suitable for high-frequency applications
Comparison Table: FR1 vs. FR2 vs. FR3 vs. FR4 PCBs
Property | FR1 | FR2 | FR3 | FR4 |
---|---|---|---|---|
Base Material | Paper | Paper | Paper | Glass |
Resin | Phenolic | Phenolic | Epoxy | Epoxy |
Cost | Low | Moderate | Moderate to High | High |
Mechanical Strength | Moderate | Better than FR1 | Excellent | Excellent |
Heat Resistance | Limited | Limited | Improved | High |
Moisture Resistance | Limited | Improved | Good | Excellent |
Electrical Insulation | Good | Good | Good | Excellent |
Frequency Range | Low | Low to Medium | Medium | High |
Typical Applications | Low-cost consumer electronics | Automotive, industrial controls | Telecommunications, aerospace | High-performance electronics, military |
Manufacturing Process of FR PCBs
The manufacturing process of FR PCBs involves several steps, including:
-
Material Selection: Choosing the appropriate FR-grade laminate material based on the desired properties and application requirements.
-
Lamination: Stacking and pressing the layers of the laminate material together using heat and pressure to form a solid board.
-
Drilling: Creating holes in the board for mounting components and vias using CNC drilling machines.
-
Plating: Applying a conductive layer (usually copper) to the drilled holes and surface of the board to establish electrical connections.
-
Etching: Removing unwanted copper from the board surface to create the desired circuit pattern using photolithography and chemical etching processes.
-
Solder Mask Application: Applying a protective layer over the copper traces to prevent short circuits and improve the board’s appearance.
-
Silkscreen Printing: Adding text, symbols, and component identifiers to the board surface using silkscreen printing techniques.
-
Surface Finishing: Applying a final finish (e.g., HASL, ENIG, OSP) to the exposed copper areas to prevent oxidation and enhance solderability.
-
Inspection and Testing: Conducting visual and electrical inspections to ensure the quality and functionality of the manufactured PCBs.
Advantages and Disadvantages of FR1 PCBs
Advantages
- Cost-effective solution for low-end applications
- Easy to manufacture and process
- Suitable for prototyping and small-scale production
Disadvantages
- Limited mechanical strength and durability
- Poor heat resistance and thermal stability
- Not suitable for high-frequency or high-performance applications
- Susceptible to moisture absorption and warping
Applications of FR1 PCBs
FR1 PCBs are commonly used in low-cost consumer electronics and applications where high performance is not a critical requirement. Some examples include:
- Simple Single-Sided PCBs for toys and novelty items
- Low-power electronic devices such as remote controls and calculators
- Disposable or short-lifespan products
- Educational and hobby projects
Frequently Asked Questions (FAQ)
-
Q: Can FR1 PCBs be used for multilayer designs?
A: While it is technically possible to create multilayer FR1 PCBs, it is not common practice due to the material’s limited heat resistance and mechanical strength. Multilayer designs are typically reserved for higher-grade materials like FR4. -
Q: Are FR1 PCBs suitable for high-temperature applications?
A: No, FR1 PCBs have poor heat resistance and are not recommended for applications that involve exposure to high temperatures. For such applications, FR4 or other specialized High-Temperature PCB materials are more appropriate. -
Q: How do FR1 PCBs compare to FR4 in terms of cost?
A: FR1 PCBs are significantly cheaper than FR4 PCBs due to their simpler material composition and manufacturing process. However, the cost savings come at the expense of reduced performance and durability. -
Q: Can FR1 PCBs be used for high-frequency applications?
A: No, FR1 PCBs are not suitable for high-frequency applications due to their limited electrical properties and higher dielectric losses. For high-frequency applications, FR4 or other specialized PCB materials with better dielectric properties are recommended. -
Q: Are there any environmental concerns associated with FR1 PCBs?
A: FR1 PCBs contain phenolic resin, which can release harmful substances during manufacturing and disposal. Proper safety measures and environmental regulations should be followed when handling and disposing of FR1 PCBs to minimize potential risks.
Conclusion
FR1 PCBs, although the most basic and least expensive among the FR-grade PCBs, still have their place in the electronics industry. They are suitable for low-cost, low-performance applications where mechanical strength and thermal stability are not critical factors. However, for more demanding applications, higher-grade materials like FR2, FR3, and FR4 offer better performance and reliability.
When selecting the appropriate FR-grade PCB for a specific application, designers and engineers must consider factors such as cost, performance requirements, operating environment, and manufacturing considerations. By understanding the differences between FR1, FR2, FR3, and FR4 PCBs, informed decisions can be made to ensure the optimal balance between cost and performance.
As technology continues to advance, new materials and manufacturing processes may emerge, offering even better alternatives to the traditional FR-grade PCBs. However, for now, FR1 PCBs remain a viable option for low-end electronics, while FR4 PCBs dominate the high-performance segment of the market.
No responses yet