What is a High-temperature PCB?
A high-temperature printed circuit board (PCB) is a specialized type of PCB designed to withstand extreme temperatures and harsh environmental conditions. These PCBs are engineered using materials and manufacturing processes that allow them to operate reliably in applications where standard PCBs would fail due to thermal stress or degradation.
High-temperature PCBs are essential for various industries, including:
- Aerospace and defense
- Automotive
- Oil and gas exploration
- Industrial equipment
- Medical devices
The key characteristics of a high-temperature PCB include:
- Thermal stability: The ability to maintain its structural integrity and electrical properties at elevated temperatures.
- Reliable performance: Consistent functionality and minimal degradation over extended periods of exposure to high temperatures.
- Durability: Resistance to thermal shock, vibration, and other mechanical stresses.
Materials Used in High-Temperature PCBs
To achieve the desired performance characteristics, high-temperature PCBs are manufactured using specialized materials that can withstand extreme conditions. Some of the most common materials used in high-temperature PCB manufacturing include:
Substrate Materials
Material | Glass Transition Temperature (Tg) | Thermal Decomposition Temperature (Td) | Dielectric Constant (Dk) | Dissipation Factor (Df) |
---|---|---|---|---|
Polyimide | 260°C – 400°C | 520°C – 620°C | 3.4 – 3.5 | 0.002 – 0.003 |
High Tg FR-4 | 170°C – 180°C | 340°C – 360°C | 4.2 – 4.5 | 0.020 – 0.025 |
Ceramic | N/A | >1000°C | 6.0 – 10.0 | 0.001 – 0.005 |
Polyimide is the most widely used substrate material for high-temperature PCBs due to its excellent thermal stability, low dielectric constant, and low dissipation factor. High Tg FR-4 is a cost-effective alternative for applications with slightly lower temperature requirements. Ceramic substrates offer the highest temperature resistance but are more expensive and have higher dielectric constants.
Conductor Materials
Material | Melting Point | Electrical Conductivity (% IACS) | Thermal Conductivity (W/mK) |
---|---|---|---|
Copper | 1085°C | 100% | 385 – 400 |
Silver | 962°C | 105% | 406 – 429 |
Gold | 1064°C | 70% | 314 – 318 |
Copper is the most common conductor material used in high-temperature PCBs due to its high electrical and thermal conductivity, as well as its relatively low cost. Silver and gold are used in specialized applications where higher conductivity or better corrosion resistance is required.
Solder Mask and Silkscreen Inks
High-temperature solder mask and silkscreen inks are formulated to withstand elevated temperatures without degradation or discoloration. These inks are typically based on polyimide, epoxy, or acrylic resins and are designed to maintain their adhesion and mechanical properties at high temperatures.
Manufacturing Processes for High-Temperature PCBs
The manufacturing process for high-temperature PCBs is similar to that of standard PCBs, with some additional considerations and modifications to ensure the final product can withstand extreme conditions.
-
Design and Layout: The PCB design must take into account the thermal expansion characteristics of the materials used, as well as the expected operating temperature range. Proper component placement, trace widths, and spacing are critical to minimizing thermal stress and ensuring reliable performance.
-
Material Selection: The appropriate substrate, conductor, and solder mask materials are chosen based on the specific application requirements and the expected operating temperature range.
-
Lamination: The selected substrate material is laminated with copper foil using high-temperature adhesives or bonding agents. The lamination process is carried out under controlled temperature and pressure conditions to ensure a strong bond between the layers.
-
Drilling: Holes are drilled through the laminated board to accommodate through-hole components and vias. High-temperature PCBs may require specialized drilling techniques or equipment to minimize thermal stress and ensure clean, accurate holes.
-
Plating: The drilled holes are plated with copper to establish electrical connections between layers. High-temperature PCBs may require special plating processes or additives to improve the adhesion and thermal stability of the plated copper.
-
Etching: The unwanted copper is etched away, leaving the desired circuit pattern on the board. High-temperature PCBs may require modified etching processes or chemistry to ensure clean, well-defined traces.
-
Solder Mask and Silkscreen: High-temperature solder mask and silkscreen inks are applied to the board to protect the circuitry and provide component identification markings.
-
Surface Finish: A protective surface finish, such as ENIG (Electroless Nickel Immersion Gold) or HASL (Hot Air Solder Leveling), is applied to the exposed copper surfaces to prevent oxidation and improve solderability.
-
Inspection and Testing: The completed high-temperature PCB undergoes thorough visual inspection and electrical testing to ensure it meets the required quality standards and performance specifications.
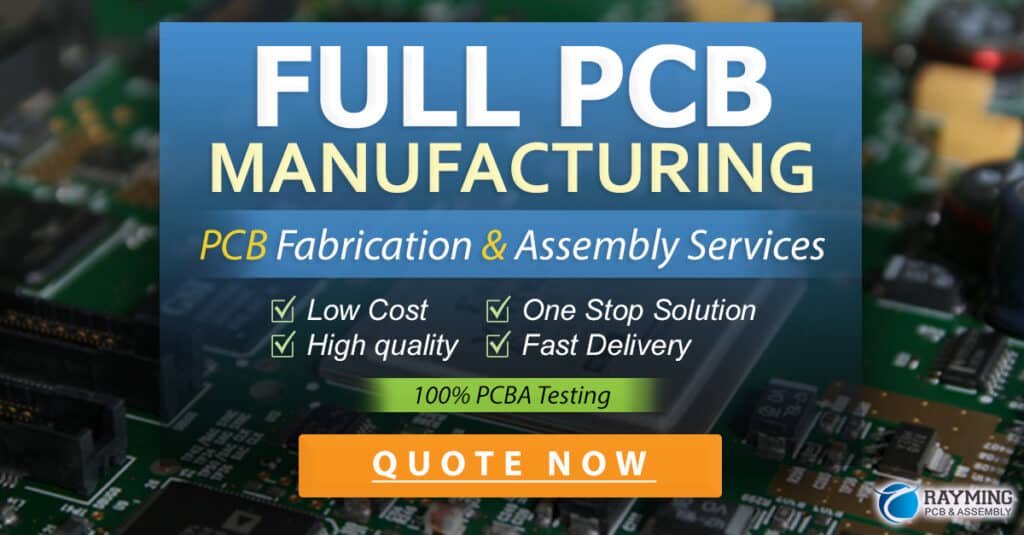
Applications of High-Temperature PCBs
High-temperature PCBs are used in a wide range of industries and applications where reliable performance under extreme conditions is critical. Some of the most common applications include:
Aerospace and Defense
- Jet engine control systems
- Missile guidance systems
- Satellite communications equipment
- Radar and sonar systems
Automotive
- Engine control units (ECUs)
- Exhaust gas sensors
- Brake systems
- Hybrid and electric vehicle power electronics
Oil and Gas Exploration
- Downhole drilling equipment
- Wellhead control systems
- Pipeline monitoring sensors
Industrial Equipment
- Power generation and distribution systems
- HVAC control systems
- Chemical processing equipment
- Welding and soldering machines
Medical Devices
- Sterilization equipment
- Surgical instruments
- Implantable devices
- Diagnostic imaging systems
Challenges and Considerations in High-Temperature PCB Design and Manufacturing
Designing and manufacturing high-temperature PCBs presents several unique challenges and considerations:
-
Material Compatibility: Ensuring that all materials used in the PCB, including the substrate, conductors, and components, are compatible and can withstand the expected operating temperature range.
-
Thermal Expansion: Accounting for the different thermal expansion rates of the materials used in the PCB and designing the layout to minimize thermal stress and warpage.
-
Component Selection: Choosing components that are rated for the expected operating temperature range and have compatible packaging and mounting options.
-
Manufacturing Process Control: Maintaining strict control over the manufacturing process parameters, such as lamination temperature and pressure, plating chemistry, and etching conditions, to ensure consistent quality and performance.
-
Testing and Qualification: Developing appropriate testing and qualification procedures to validate the performance and reliability of the high-temperature PCB under the expected operating conditions.
Frequently Asked Questions (FAQ)
-
What is the difference between a high-temperature PCB and a standard PCB?
A high-temperature PCB is designed to withstand extreme temperatures and harsh environmental conditions, while a standard PCB is intended for use in more moderate temperature ranges. High-temperature PCBs use specialized materials and manufacturing processes to ensure reliable performance at elevated temperatures. -
What are the most common substrate materials used in high-temperature PCBs?
The most common substrate materials used in high-temperature PCBs are polyimide, high Tg FR-4, and ceramic. Polyimide offers the best combination of thermal stability, low dielectric constant, and low dissipation factor, making it the preferred choice for most high-temperature applications. -
Can standard components be used on high-temperature PCBs?
In most cases, standard components cannot be used on high-temperature PCBs, as they are not designed to withstand the extreme temperatures and thermal stresses encountered in these applications. High-temperature PCBs require components that are specifically rated for the expected operating temperature range and have compatible packaging and mounting options. -
How do you ensure reliable solder joints on high-temperature PCBs?
To ensure reliable solder joints on high-temperature PCBs, it is essential to use high-temperature solder alloys, such as lead-free alloys with higher melting points, and to follow proper soldering techniques and temperature profiles. Additionally, using a compatible surface finish, such as ENIG or HASL, can improve the solderability and reliability of the solder joints. -
What are the key considerations when designing a high-temperature PCB layout?
When designing a high-temperature PCB layout, it is crucial to consider the thermal expansion characteristics of the materials used and to minimize thermal stress and warpage by using appropriate component placement, trace widths, and spacing. Additionally, designers must ensure that all materials, including the substrate, conductors, and components, are compatible and can withstand the expected operating temperature range.
In conclusion, high-temperature PCBs are essential for applications that require reliable performance under extreme conditions. By using specialized materials, manufacturing processes, and design techniques, high-temperature PCBs can withstand elevated temperatures and harsh environments, enabling the development of advanced technologies in aerospace, automotive, oil and gas, industrial equipment, and medical devices. As the demand for high-performance electronics in challenging environments continues to grow, the importance of high-temperature PCBs will only increase, driving further innovation in materials, manufacturing, and design.
No responses yet