Introduction to Electrostatic Spraying Technology in PCB Manufacturing
Electrostatic spraying technology has emerged as a game-changer in the manufacturing of printed circuit boards (PCBs), particularly in the production of thick-copper PCBs. This innovative approach offers numerous advantages over traditional methods, enhancing the efficiency, precision, and quality of the PCB fabrication process.
What is Electrostatic Spraying Technology?
Electrostatic spraying technology is a method of applying a coating or material onto a surface using an electrically charged spray. In the context of PCB manufacturing, this technology is used to deposit copper onto the PCB substrate, creating the conductive traces and pads that form the foundation of the circuit board.
The process involves atomizing the copper material into fine droplets and applying an electrical charge to them. The charged droplets are then attracted to the oppositely charged PCB substrate, resulting in a uniform and controlled deposition of the copper layer.
Advantages of Electrostatic Spraying Technology in Thick-Copper PCB Manufacturing
Thick-copper PCBs, which feature copper layers thicker than the standard 1-2 oz. (35-70 μm), offer several benefits, such as improved current carrying capacity, enhanced thermal management, and better mechanical stability. However, manufacturing thick-copper PCBs using conventional methods can be challenging due to the increased thickness of the copper layer.
Electrostatic spraying technology addresses these challenges by providing the following advantages:
-
Uniform Copper Distribution: Electrostatic spraying ensures a consistent and even distribution of copper across the PCB surface, minimizing variations in thickness and improving the overall quality of the circuit board.
-
Precise Thickness Control: The technology allows for precise control over the thickness of the copper layer, enabling the production of PCBs with specific copper thicknesses to meet the requirements of various applications.
-
Improved Adhesion: The electrostatic attraction between the charged copper droplets and the PCB substrate enhances the adhesion of the copper layer, resulting in better bonding and reduced risk of delamination.
-
Increased Efficiency: Electrostatic spraying technology offers a faster and more efficient means of depositing copper compared to traditional methods, reducing production time and increasing throughput.
-
Cost-Effectiveness: By optimizing the copper deposition process and reducing material waste, electrostatic spraying technology contributes to cost savings in the manufacturing of thick-copper PCBs.
The Electrostatic Spraying Process in Thick-Copper PCB Manufacturing
The electrostatic spraying process in thick-copper PCB manufacturing involves several key steps, as outlined below:
1. Substrate Preparation
The PCB substrate, typically made of FR-4 or other suitable materials, is cleaned and prepared for the copper deposition process. This step ensures that the surface is free from contaminants and provides a suitable base for the copper layer.
2. Masking and Patterning
The desired circuit pattern is created on the PCB substrate using photolithography or other patterning techniques. This step involves applying a photoresist layer, exposing it to light through a patterned mask, and developing the resist to reveal the areas where copper will be deposited.
3. Electrostatic Spraying of Copper
The prepared PCB substrate is placed in the electrostatic spraying chamber, where the copper material is atomized and electrically charged. The charged copper droplets are attracted to the exposed areas of the substrate, forming a uniform and controlled layer of copper.
The thickness of the copper layer can be precisely controlled by adjusting the spraying parameters, such as the voltage, flow rate, and duration of the spraying process. This allows for the production of thick-copper PCBs with specific copper thicknesses, typically ranging from 3-10 oz. (105-350 μm) or more.
4. Curing and Sintering
After the copper layer is deposited, the PCB undergoes a curing and sintering process to strengthen the bond between the copper and the substrate. This step involves exposing the PCB to elevated temperatures, typically in a controlled atmosphere, to promote the diffusion and cohesion of the copper particles.
5. Etching and Finishing
Once the copper layer is cured and sintered, the remaining photoresist is removed, and the PCB undergoes an etching process to remove the unwanted copper areas, leaving behind the desired circuit pattern. The PCB may then undergo additional finishing processes, such as surface treatment, solder mask application, and silkscreen printing, depending on the specific requirements of the application.
Applications of Thick-Copper PCBs Manufactured Using Electrostatic Spraying Technology
Thick-copper PCBs manufactured using electrostatic spraying technology find applications in various industries and domains, where high current carrying capacity, improved thermal management, and mechanical stability are critical. Some of the key applications include:
1. Power Electronics
Thick-copper PCBs are widely used in power electronics applications, such as power converters, inverters, and motor drives. The increased copper thickness allows for higher current carrying capacity, reducing the risk of thermal damage and improving the overall efficiency of the system.
2. Automotive Electronics
The automotive industry increasingly relies on thick-copper PCBs for applications such as electric vehicle charging systems, battery management systems, and high-power automotive electronics. The enhanced thermal management and mechanical stability offered by thick-copper PCBs are crucial in these demanding environments.
3. Industrial Control Systems
Industrial control systems, such as programmable logic controllers (PLCs), Motor Controllers, and power distribution units, often require thick-copper PCBs to handle high currents and ensure reliable operation in harsh industrial environments.
4. Aerospace and Defense
Thick-copper PCBs are used in aerospace and defense applications, where high reliability, thermal management, and mechanical durability are paramount. These PCBs are found in avionics systems, radar equipment, and satellite communication devices.
5. High-Power LED Lighting
The high-power LED lighting industry benefits from thick-copper PCBs, as they provide the necessary thermal dissipation and current carrying capacity to support high-brightness LED arrays. The improved thermal management helps to prolong the lifespan of the LEDs and maintain optimal light output.
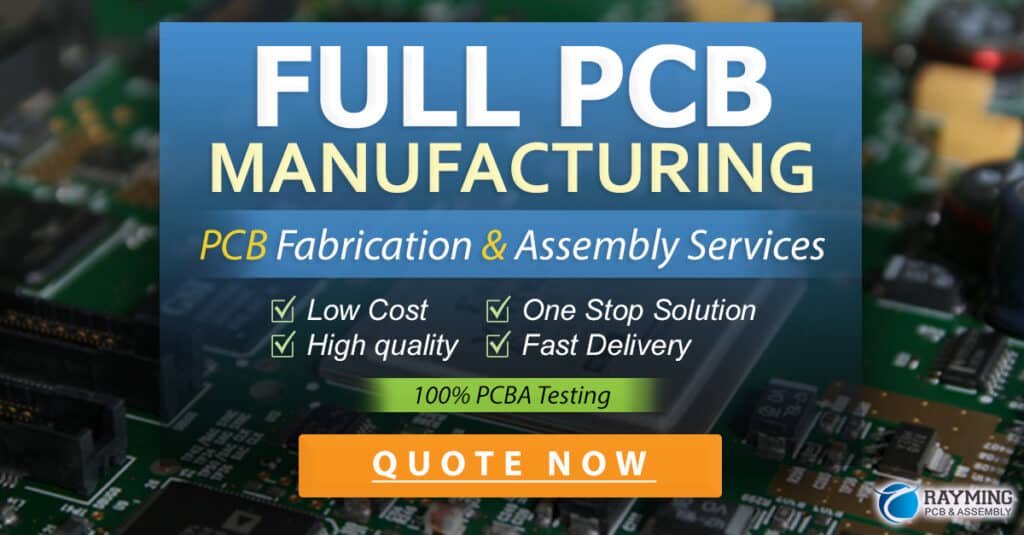
Challenges and Future Developments in Electrostatic Spraying Technology for Thick-Copper PCBs
While electrostatic spraying technology offers significant advantages in the manufacturing of thick-copper PCBs, there are still challenges and opportunities for future developments in this field.
Challenges
-
Equipment Cost: The initial investment in electrostatic spraying equipment can be substantial, which may be a barrier for some PCB manufacturers.
-
Process Optimization: Achieving optimal spraying parameters and ensuring consistent results requires careful process control and monitoring, which may involve a learning curve for manufacturers adopting this technology.
-
Material Compatibility: The compatibility of different copper materials and substrates with the electrostatic spraying process needs to be carefully evaluated to ensure the desired performance and reliability of the finished PCBs.
Future Developments
-
Hybrid Spraying Techniques: Combining electrostatic spraying with other deposition methods, such as electroplating or electroless plating, may offer further enhancements in terms of copper thickness, adhesion, and process efficiency.
-
Advanced Materials: The development of new copper alloys or composite materials specifically tailored for electrostatic spraying could improve the mechanical, thermal, and electrical properties of thick-copper PCBs.
-
Inline Process Integration: Integrating electrostatic spraying technology into inline PCB manufacturing processes, such as roll-to-roll fabrication, could increase production throughput and reduce overall manufacturing costs.
-
Simulation and Modeling: Advances in simulation and modeling tools for electrostatic spraying processes could help optimize the design and manufacturing of thick-copper PCBs, reducing trial-and-error and improving overall product quality.
Frequently Asked Questions (FAQ)
-
What is the typical thickness range for thick-copper PCBs manufactured using electrostatic spraying technology?
Thick-copper PCBs manufactured using electrostatic spraying technology typically have copper thicknesses ranging from 3-10 oz. (105-350 μm) or more, depending on the specific requirements of the application. -
Can electrostatic spraying technology be used with other PCB Substrates besides FR-4?
Yes, electrostatic spraying technology can be used with various PCB substrates, including ceramic, metal-core, and high-frequency materials. However, the compatibility of the substrate with the spraying process should be carefully evaluated to ensure optimal results. -
How does electrostatic spraying technology compare to traditional electroplating methods for thick-copper PCBs?
Electrostatic spraying technology offers several advantages over traditional electroplating methods, such as more uniform copper distribution, precise thickness control, improved adhesion, and increased efficiency. However, electroplating may still be preferred in certain applications or for very high copper thicknesses. -
Are there any environmental concerns associated with electrostatic spraying technology in PCB manufacturing?
Electrostatic spraying technology itself is relatively environmentally friendly, as it minimizes material waste and can be operated with eco-friendly copper materials. However, proper handling and disposal of any waste materials generated during the process should be ensured to minimize environmental impact. -
What are the key factors to consider when selecting an electrostatic spraying system for thick-copper PCB manufacturing?
When selecting an electrostatic spraying system for thick-copper PCB manufacturing, key factors to consider include the desired copper thickness range, substrate compatibility, production throughput requirements, process control and monitoring capabilities, and integration with existing manufacturing processes. It is also essential to evaluate the equipment cost, maintenance requirements, and vendor support to ensure a successful implementation.
Conclusion
Electrostatic spraying technology has revolutionized the manufacturing of thick-copper PCBs, offering numerous advantages over traditional methods. By providing uniform copper distribution, precise thickness control, improved adhesion, and increased efficiency, this technology enables the production of high-quality thick-copper PCBs for a wide range of applications, including power electronics, automotive, industrial control systems, aerospace, and high-power LED lighting.
As the demand for thick-copper PCBs continues to grow, driven by the increasing complexity and power requirements of modern electronic systems, electrostatic spraying technology is poised to play a crucial role in meeting these challenges. With ongoing research and development in this field, we can expect further advancements in hybrid spraying techniques, advanced materials, inline process integration, and simulation tools, which will shape the future of thick-copper PCB manufacturing.
By embracing electrostatic spraying technology, PCB manufacturers can enhance their capabilities, improve product quality, and stay competitive in the ever-evolving electronics industry. As this technology continues to mature and evolve, it will undoubtedly contribute to the development of more advanced, reliable, and efficient electronic systems across various sectors.
No responses yet