Introduction to Electroless Cu Plating
Electroless copper (Cu) deposition is a chemical process that allows for the coating of Cu onto various substrate materials without the use of an external electrical current. This makes it different from traditional electroplating methods which require an electric current to reduce metal ions in an electrolyte solution and deposit them onto a conductive substrate that serves as the cathode.
The key advantages of electroless Cu deposition include:
– Ability to uniformly coat complex shapes and cavities
– No need for a conductive substrate material
– Excellent adhesion to properly prepared substrates
– High purity, ductile, and conductive Cu deposits
– Relatively simple and cost-effective setup
These benefits make electroless Cu widely used in electronics manufacturing for printed circuit boards (PCBs), EMI shielding, and decorative coatings. It also has applications in automotive, aerospace, medical, and other industries.
Chemical Reactions in Electroless Copper Plating
The basic chemical reaction in electroless Cu deposition involves the autocatalytic reduction of copper(II) ions to metallic copper on a catalytIC Substrate surface:
Cu^2+ + 2 HCHO + 4 OH^- -> Cu^0 + 2 HCOO^- + 2 H2O + H2
In this reaction, formaldehyde (HCHO) serves as the reducing agent, providing the electrons needed to reduce Cu^2+ to Cu metal. The reaction consumes hydroxide ions (OH^-) and generates formate (HCOO^-), water, and hydrogen gas as byproducts.
For the reaction to proceed, the substrate surface must have catalytic properties to initiate the reduction of Cu^2+ ions. This is usually achieved through a series of pretreatment steps to clean, etch, and activate the surface with Pd catalysts. The deposited Cu layer itself is catalytic, allowing the reaction to continue autocatalytically.
Key components in a typical electroless Cu plating bath include:
– Copper source (e.g. copper sulfate)
– Reducing agent (e.g. formaldehyde)
– Complexing agent (e.g. EDTA, tartrate)
– pH regulator (e.g. sodium hydroxide)
– Stabilizers (e.g. cyanide, thiourea)
The complexing agent helps prevent precipitation of copper hydroxide at alkaline pH and buffers the Cu^2+ ion concentration. Stabilizers are added in small amounts to prevent spontaneous decomposition of the plating bath. Careful control of bath composition, pH, and temperature is critical for optimal plating results.
Substrate Preparation for Electroless Cu
Proper substrate preparation is essential for achieving good adhesion and uniformity of the electroless Cu deposit. The general procedure involves:
-
Cleaning: Removes grease, oils, and contaminants from the substrate surface using alkaline cleaners or organic solvents.
-
Etching: Roughens the surface to improve mechanical interlocking with the Cu deposit. Common etchants include strong acids or oxidizing agents depending on the substrate.
-
Activation: Deposits catalytic Pd particles on the surface to initiate electroless Cu deposition. Typical activators are acidic solutions containing Pd and Sn chloride.
-
Acceleration: Removes excess Sn from the Pd-Sn colloidal particles, leaving behind exposed Pd sites for Cu deposition. Dilute acids like hydrochloric or sulfuric acid are commonly used.
The specific chemicals and process parameters used for substrate preparation depend on the type of material being plated. Some common substrates for electroless Cu include:
Substrate | Cleaning | Etching | Activation |
---|---|---|---|
ABS plastic | Alkaline cleaner | Chromic acid | Pd-Sn activator |
Polyimide | Alkaline cleaner | Permanganate | Pd-Sn activator |
Epoxy | Plasma cleaning | Sulfuric/chromic acid | Pd-Sn activator |
Aluminum | Alkaline cleaner | NaOH etch | Zincate + Pd-Sn |
Steel/Kovar | Alkaline cleaner | HCl pickle | Pd-Sn activator |
For non-conductive substrates like plastics, a brief etching step is often performed after activation to roughen the surface and improve adhesion. Over-etching should be avoided as it can lead to poor deposit quality.
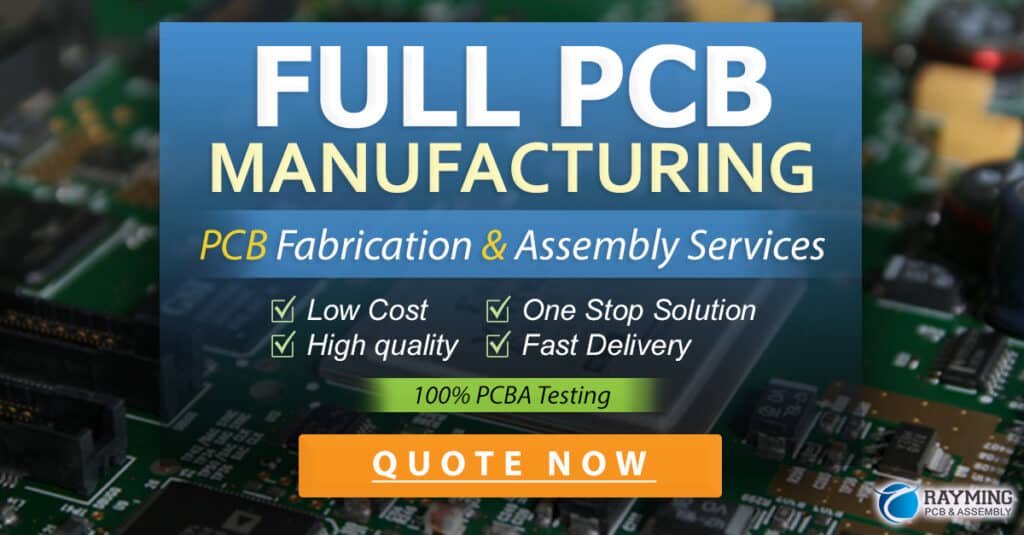
Electroless Copper Bath Formulations
Many different electroless Cu bath formulations have been developed to cater to specific substrate materials, plating requirements, and operating conditions. However, most baths can be classified into one of three types based on the reducing agent used:
- Formaldehyde-reduced baths
- Glyoxylic acid-reduced baths
- Hypophosphite-reduced baths
Formaldehyde is the most commonly used reducing agent due to its low cost, good stability, and fast plating rates. A typical formaldehyde-based electroless Cu bath composition is:
Component | Concentration |
---|---|
Copper sulfate | 0.03-0.08 M |
Sodium hydroxide | 0.05-0.2 M |
EDTA | 0.03-0.1 M |
Formaldehyde (37%) | 0.05-0.25 M |
Potassium cyanide | 1-5 ppm |
Thiourea | 1-3 ppm |
The bath is typically operated at a pH of 11.5-13.0 and temperature of 40-60°C. Plating rates of 2-5 μm/hr can be achieved with good stability and deposit properties.
Glyoxylic acid is a milder reducing agent compared to formaldehyde, providing slower plating rates but improved bath stability and deposit ductility. Glyoxylic acid baths typically use tartrate as the complexing agent and operate at pH 11-12 and 30-50°C.
Hypophosphite is the least common reducing agent for electroless Cu due to its very slow plating rate and incorporation of phosphorus in the deposit. However, it can be useful for plating on certain sensitive substrates like aluminum. Hypophosphite baths use citrate as the complexing agent and operate at pH 8-10 and 60-90°C.
In addition to these main components, various additives such as stabilizers, brighteners, and wetting agents may be used to improve the performance and properties of the electroless Cu bath. The specific formulation should be optimized based on the application requirements and substrate material.
Deposit Properties and Characterization
The properties of electroless Cu deposits can vary significantly depending on the bath composition, operating conditions, and substrate material. Some key characteristics of electroless Cu include:
- Purity: Typically >99% Cu, with low levels of co-deposited impurities like C, O, H.
- Resistivity: 1.7-2.0 μΩ·cm, compared to 1.68 μΩ·cm for pure Cu.
- Tensile strength: 300-500 MPa, depending on heat treatment.
- Elongation: 10-20% as deposited, can be improved by annealing.
- Hardness: 150-200 HV, higher than electroplated Cu.
- Density: 8.7-8.9 g/cm³, close to bulk Cu (8.96 g/cm³).
- Thermal stability: Stable up to 350°C without oxidation.
Electroless Cu deposits are generally more pure, harder, and more resistant to oxidation compared to electroplated Cu. However, they may have higher tensile stress and lower ductility in the as-deposited state.
Various analytical techniques can be used to characterize electroless Cu deposits for quality control and understanding structure-property relationships. Some commonly used methods include:
- Cross-section microscopy (SEM/TEM) to examine deposit thickness, morphology, and interface.
- X-ray diffraction (XRD) to determine grain size, orientation, and crystal structure.
- X-ray fluorescence (XRF) or atomic absorption spectroscopy (AAS) for chemical composition analysis.
- Four-point probe or van der Pauw method to measure electrical resistivity.
- Nanoindentation or microhardness testing to evaluate mechanical properties.
- Adhesion testing (e.g. tape test, pull test) to assess interfacial bonding strength.
By correlating the deposit properties with the plating parameters, the electroless Cu process can be optimized to meet specific application requirements. For example, annealing at 150-200°C can be used to reduce tensile stress and improve ductility of the deposit for better formability.
Applications of Electroless Copper
Electroless Cu has found widespread use in various industries due to its unique capabilities and benefits over other metallization methods. Some major application areas include:
Electronics
- Printed circuit boards (PCBs): Electroless Cu is used for through-hole plating, trace formation, and Solder Masking in PCB manufacturing.
- Semiconductor packaging: Redistribution layers, under bump metallization, and EMI shielding on ICs and substrates.
- Flexible electronics: Stretchable and bendable Cu traces on polymer substrates for wearables, sensors, and displays.
Automotive
- Decorative coatings: Electroless Cu/Ni/Cr plating on plastic parts like door handles, trim, and emblems.
- Wear resistant coatings: Cu-PTFE composite coatings on engine components for improved lubricity and wear resistance.
- EMI shielding: Cu coatings on plastic housings and enclosures for electronic control units and sensors.
Aerospace & Defense
- Electromagnetic interference (EMI) shielding on aircraft composites and electronic boxes.
- Lightweight wiring and cable shielding for weight reduction.
- Anti-corrosion coatings on steel and aluminum components.
Medical
- Antimicrobial Cu coatings on high-touch surfaces like bed rails, door knobs, and medical equipment.
- Biocompatible Cu coatings on implantable devices and sensors.
- Shielding of MRI and other medical imaging rooms.
Industrial
- Corrosion protection of steel, cast iron, and magnesium parts.
- Wear resistant and anti-galling coatings on bearing surfaces.
- Chemical resistant coatings on valves, fittings, and fasteners.
As the demand for miniaturization, functionality, and performance continues to grow across industries, electroless Cu will play an increasingly important role in enabling new applications and design possibilities.
Troubleshooting Common Issues
While electroless Cu is a relatively robust and forgiving process, various issues can arise during plating that impact the quality and performance of the deposit. Some common problems and their potential causes and solutions are:
Problem | Possible Causes | Solutions |
---|---|---|
Blistering/Peeling | – Improper pretreatment – Contamination – High stress |
– Optimize cleaning/etching – Use higher purity chemicals – Reduce plating rate |
Pitting | – Surface defects – Particulate matter – Low stabilizer |
– Improve substrate polish – Filter plating solution – Increase stabilizer dosage |
Dull/dark deposit | – Organic contamination – Low formaldehyde – High thickness |
– Replace or carbon treat bath – Adjust formaldehyde concentration – Reduce plating time |
Slow plating | – Low temperature – Low pH – Aged bath |
– Increase bath temperature – Add NaOH to raise pH – Replace or replenish bath |
Rough/nodular deposit | – High plating rate – Insufficient agitation – Low stabilizer |
– Lower temperature or pH – Increase stirring or work movement – Increase stabilizer concentration |
Other issues like poor adhesion, high stress, or bath decomposition can also occur and may require more extensive troubleshooting. It is important to regularly monitor the bath composition, pH, and temperature, as well as the quality of the deposited Cu to identify and correct any problems early on.
Proper maintenance of the electroless Cu bath, including filtration, carbon treatment, and chemical replenishment, can help prevent many common issues and extend the bath life. Having a well-characterized process and established quality control procedures is crucial for consistent and reliable electroless Cu plating.
Frequently Asked Questions (FAQ)
What is the typical thickness of electroless Cu deposits?
Electroless Cu can be plated to a wide range of thicknesses, from a few hundred nanometers to several microns or even tens of microns in some cases. The achievable thickness depends on the specific bath formulation, plating rate, and substrate geometry. For PCB Applications, a minimum Cu thickness of 20-25 μm is often required for reliable electrical and mechanical performance.
How does electroless Cu compare to electroplated Cu in terms of properties and performance?
Electroless Cu generally has higher purity, hardness, and resistivity compared to electroplated Cu. It also tends to have better adhesion and thermal stability due to the chemical bonding with the substrate. However, electroplated Cu can be deposited at much higher rates and thicknesses, and can have better ductility and lower stress in some cases. The choice between electroless and electroplated Cu depends on the specific application requirements and substrate constraints.
Can electroless Cu be plated on non-conductive substrates like plastics and ceramics?
Yes, one of the key advantages of electroless Cu is its ability to metallize non-conductive substrates without the need for an external electrical current. This is achieved through proper surface preparation steps like etching and activation that render the substrate catalytic for Cu deposition. Electroless Cu is widely used for plating on plastics, composites, and glass for applications like EMI shielding and decorative coatings.
What are the environmental and safety concerns associated with electroless Cu plating?
Electroless Cu baths typically contain hazardous chemicals like formaldehyde, cyanide, and strong alkaline solutions that pose health and safety risks. Proper ventilation, personal protective equipment, and waste treatment are essential for safe handling and disposal of these chemicals. Efforts have been made to develop more environmentally friendly electroless Cu baths using alternative reducing agents and stabilizers, but they often suffer from lower plating rates and stability compared to traditional formaldehyde-based baths.
How does the cost of electroless Cu compare to other metallization methods?
The cost of electroless Cu depends on various factors like the bath chemistry, substrate material, and production scale. In general, electroless Cu is more expensive than electroplating due to the higher cost of chemicals and slower plating rates. However, it can be more cost-effective than other methods like sputtering or evaporation for certain applications, especially for complex-shaped parts or non-conductive substrates. A thorough cost analysis considering the specific process requirements and production volume is necessary to determine the most economical metallization method for a given application.
Conclusion
Electroless copper deposition is a versatile and powerful technique for metallizing a wide range of substrates, from plastics and composites to metals and ceramics. Its unique ability to provide uniform, conformal, and adherent Cu coatings without an external power supply has made it indispensable in various industries, particularly in electronics manufacturing.
As with any chemical process, electroless Cu requires careful control of the bath composition, operating parameters, and substrate preparation to achieve the desired deposit properties and performance. Ongoing research and development in areas like environmentally friendly chemistries, high-speed plating, and nanomaterial incorporation will continue to expand the capabilities and applications of electroless Cu.
By understanding the fundamentals of the electroless Cu process and its key variables, engineers and technicians can optimize and troubleshoot their plating operations to achieve consistent, high-quality results. With its growing importance in advanced technologies like 5G, IoT, and electric vehicles, electroless Cu will undoubtedly play a critical role in shaping the future of manufacturing and innovation.
No responses yet