Introduction
Designing PCBs can be a complex and challenging process, especially when it comes to creating accurate and reliable footprints. Footprints, also known as land patterns or component outlines, are the physical representations of electronic components on a PCB. They define the copper pads, holes, and other features required to properly mount and connect components to the board.
However, creating footprints is not always straightforward, and even experienced designers can make mistakes that lead to manufacturing issues, assembly problems, or even complete project failures. In this article, we will explore some of the most common and diabolical footprint mistakes and provide practical tips on how to avoid them.
The Importance of Accurate Footprints
Before diving into the specific mistakes and solutions, it’s essential to understand why accurate footprints are so crucial in PCB design. Here are a few key reasons:
-
Manufacturing Compatibility: Accurate footprints ensure that components can be properly mounted and soldered onto the PCB during the manufacturing process. Incorrect footprints can lead to component misalignment, poor soldering, or even the inability to assemble the board altogether.
-
Electrical Connectivity: Footprints define the electrical connections between components and the PCB. Inaccurate footprints can result in open circuits, short circuits, or signal integrity issues, compromising the functionality and reliability of the entire system.
-
Design Reusability: Well-designed footprints can be reused across multiple projects, saving time and effort in future designs. Inconsistent or inaccurate footprints, on the other hand, may require modifications or redesigns for each new project, leading to inefficiencies and potential errors.
-
Collaboration and Communication: Accurate footprints facilitate clear communication between PCB designers, component manufacturers, and assembly teams. Using standardized and well-documented footprints reduces the chances of misinterpretation and ensures that everyone involved in the project is on the same page.
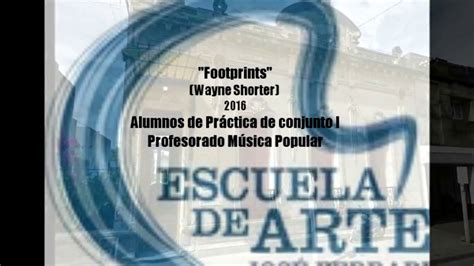
Common Footprint Mistakes
Now that we understand the importance of accurate footprints, let’s explore some of the most common mistakes that designers make and how to avoid them.
1. Incorrect Pad Size and Shape
One of the most fundamental footprint mistakes is using incorrect pad sizes or shapes. Pads that are too small can lead to poor soldering and weak mechanical connections, while oversized pads can cause short circuits or violate clearance requirements. Additionally, using the wrong pad shape (e.g., round instead of rectangular) can make it difficult to properly align and solder components.
To avoid this mistake:
- Always refer to the component manufacturer’s datasheet or application notes for recommended pad sizes and shapes.
- Consider the manufacturing capabilities and limitations of your PCB fabrication and assembly partners.
- Use IPC standards (e.g., IPC-7351) as a guideline for pad sizing and spacing.
2. Incorrect Hole Size and Placement
Another common mistake is using incorrect hole sizes or placing holes in the wrong locations. This is particularly critical for through-hole components, where the leads must pass through the holes and be soldered on the opposite side of the board. Incorrect hole sizes can make it impossible to insert the component or cause it to sit at an angle, while misplaced holes can lead to alignment issues and mechanical stress.
To avoid this mistake:
- Double-check the hole sizes specified in the component datasheet and compare them to your footprint dimensions.
- Use plated through-holes (PTHs) for through-hole components to ensure a reliable electrical and mechanical connection.
- Pay attention to the hole-to-pad ratio and ensure that there is sufficient annular ring around the hole for proper soldering.
3. Silkscreen Overlapping Pads
Silkscreen is the white text and graphics printed on the PCB surface to provide component labels, assembly instructions, and other important information. However, a common mistake is allowing the silkscreen to overlap with the component pads, which can cause assembly issues and make it difficult to read the labels.
To avoid this mistake:
- Maintain a minimum clearance between the silkscreen and the pads, typically around 0.1-0.2mm.
- Use a contrasting color for the silkscreen to improve readability, especially against the solder mask.
- Consider using abbreviations or smaller font sizes for component labels in tight spaces.
4. Incorrect Courtyard Definition
The courtyard is an invisible boundary around a component footprint that defines the minimum clearance required for assembly and manufacturing. Incorrectly defining the courtyard can lead to component overlap, insufficient space for pick-and-place machines, or difficulty in rework and repair.
To avoid this mistake:
- Follow IPC-7351 guidelines for courtyard definition, which provide recommended clearances based on component size and type.
- Consider the manufacturing tolerances and assembly processes when defining the courtyard, such as the size of the pick-and-place nozzle and the accuracy of the placement machine.
- Use your PCB design software’s design rule checks (DRCs) to ensure that courtyards do not overlap and meet the minimum clearance requirements.
5. Inconsistent or Missing 3D Models
With the increasing use of 3D PCB design and mechanical integration, having accurate 3D models of components is becoming more important than ever. Inconsistent or missing 3D models can lead to mechanical interference, clearance issues, or inaccurate visualizations of the final product.
To avoid this mistake:
- Use standardized and validated 3D models from component manufacturers or reputable libraries.
- Ensure that the 3D models are properly aligned with the footprint and have the correct dimensions and orientation.
- Regularly update your 3D model library to keep up with component changes and new releases.
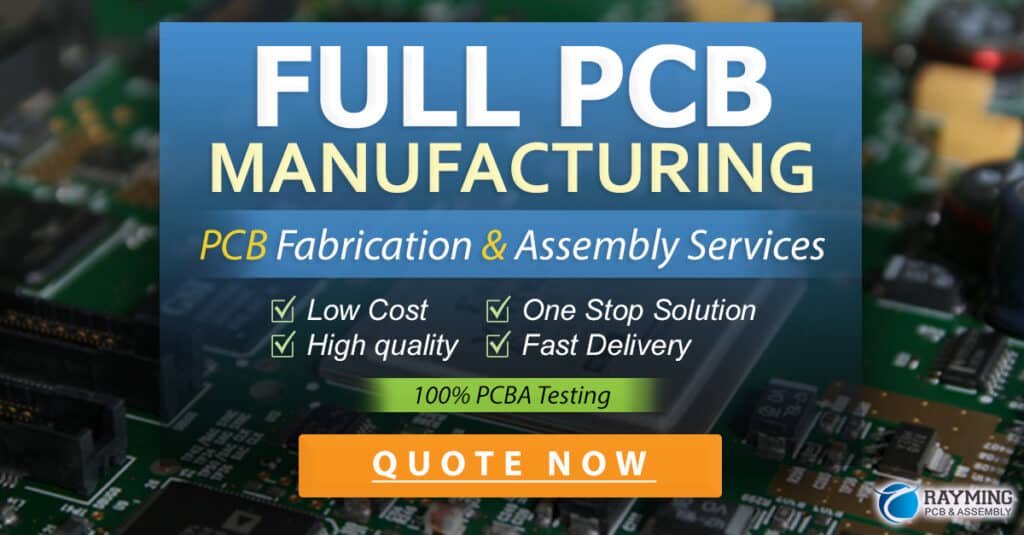
Best Practices for Creating Accurate Footprints
In addition to avoiding common mistakes, there are several best practices that designers can follow to ensure accurate and reliable footprints:
-
Use Trusted Component Libraries: Whenever possible, use footprints from trusted component libraries provided by your PCB design software, component manufacturers, or industry standards organizations. These libraries are typically well-maintained, thoroughly tested, and compliant with relevant standards.
-
Verify Footprint Dimensions: Always cross-reference the footprint dimensions with the component datasheet or application notes. Pay special attention to critical dimensions such as pad size, pitch, and hole diameter, and ensure that they match the manufacturer’s specifications.
-
Follow Industry Standards: Adhere to industry standards such as IPC-7351 for land pattern geometries, IPC-2221 for general PCB design guidelines, and IPC-SM-782 for surface mount design and land pattern standards. These standards provide proven guidelines and best practices for creating accurate and reliable footprints.
-
Use Parametric Footprint Design: Parametric footprint design allows you to create footprints that automatically adjust based on key parameters such as component dimensions, pad sizes, and clearances. This approach can save time and reduce errors, especially when working with families of components that share similar characteristics.
-
Perform Design Rule Checks: Regularly run design rule checks (DRCs) on your footprints to ensure that they meet the specified clearance, spacing, and size requirements. Most PCB design software includes built-in DRC tools that can help catch common footprint errors and inconsistencies.
-
Document and Share Footprints: Create a clear and concise documentation system for your footprints, including naming conventions, layer assignments, and any special requirements or notes. Share these footprints with your team members and stakeholders to ensure consistency and facilitate collaboration.
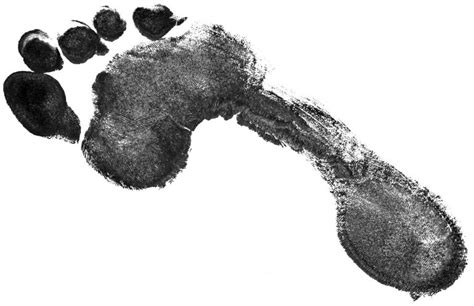
Footprint Mistakes FAQs
-
Q: What are the consequences of using incorrect pad sizes in a footprint?
A: Incorrect pad sizes can lead to poor soldering, weak mechanical connections, short circuits, or clearance violations, depending on whether the pads are too small or too large. -
Q: How can I ensure that my footprints are compatible with the manufacturing process?
A: To ensure manufacturing compatibility, always refer to the component manufacturer’s datasheet for recommended pad sizes and shapes, consider the capabilities and limitations of your PCB fabrication and assembly partners, and follow industry standards such as IPC-7351. -
Q: What is the importance of the courtyard in a component footprint?
A: The courtyard defines the minimum clearance required around a component for assembly and manufacturing. Incorrectly defining the courtyard can lead to component overlap, insufficient space for pick-and-place machines, or difficulty in rework and repair. -
Q: How can I avoid silkscreen overlapping with component pads?
A: To avoid silkscreen overlapping with pads, maintain a minimum clearance between the silkscreen and the pads (typically 0.1-0.2mm), use a contrasting color for the silkscreen, and consider using abbreviations or smaller font sizes for component labels in tight spaces. -
Q: What are the benefits of using parametric footprint design?
A: Parametric footprint design allows you to create footprints that automatically adjust based on key parameters such as component dimensions, pad sizes, and clearances. This approach can save time, reduce errors, and facilitate the creation of footprints for families of components with similar characteristics.
Conclusion
Creating accurate and reliable footprints is a critical aspect of PCB design that directly impacts the manufacturability, functionality, and reliability of the final product. By understanding and avoiding common footprint mistakes, such as incorrect pad sizes, hole placement, silkscreen overlaps, courtyard definitions, and inconsistent 3D models, designers can significantly reduce the risk of costly errors and delays.
Furthermore, by following best practices such as using trusted component libraries, verifying footprint dimensions, adhering to industry standards, employing parametric design techniques, performing regular design rule checks, and maintaining clear documentation, designers can streamline the footprint creation process and ensure consistent, high-quality results.
As PCB designs continue to increase in complexity and density, the importance of accurate footprints will only continue to grow. By staying informed about the latest techniques, tools, and standards, and by continuously refining their skills and processes, PCB designers can create footprints that not only meet the demands of today’s projects but also lay the foundation for future innovations in electronic design.
No responses yet