Overview of the PCB Fabrication Process
The PCB fabrication process can be broken down into several key stages:
- Design and Preparation
- Printing the Circuit Pattern
- Etching
- Drilling
- Plating and Finishing
- Solder Mask Application
- Silkscreen
- Surface Finish
- Electrical Testing
- Cutting and Packaging
We’ll explore each of these steps in detail. But first, let’s review what a PCB is and the materials it’s made from.
What is a PCB?
A printed circuit board (PCB) is the foundation of nearly every electronic device. It’s a flat board made of insulating materials like fiberglass, with conductive copper traces printed on the surface in a specific pattern. The copper forms circuits that connect various electronic components like resistors, capacitors, and integrated circuit (IC) chips that are soldered onto the board.
PCBs provide mechanical support and electrical connections for the components. They can be single-sided (copper on one side), double-sided (copper on both sides), or multi-layer (alternating layers of insulation and copper). The insulating substrate is typically FR-4, a glass-reinforced epoxy laminate. The copper foil is electrodeposited or rolled-annealed to the desired thickness.
Step 1: Design and Preparation
PCB fabrication starts with the circuit design. An electrical engineer captures the schematic in EDA (electronic design automation) software. The schematic is a diagram showing how components connect. It’s then laid out to create a board file with the physical location of components and copper traces.
The Gerber format is the standard for PCB design files. It consists of the following “layers”:
- Copper layers (traces)
- Solder mask (protective coating)
- Silkscreen (text/labels)
- Drill file (hole locations/sizes)
- Board outline
The fabrication house takes these Gerber files and uses them to make film photoplots and drill files for the next steps in the process. They inspect the files to ensure all layers are aligned and no design rules (e.g. minimum trace width) are violated.
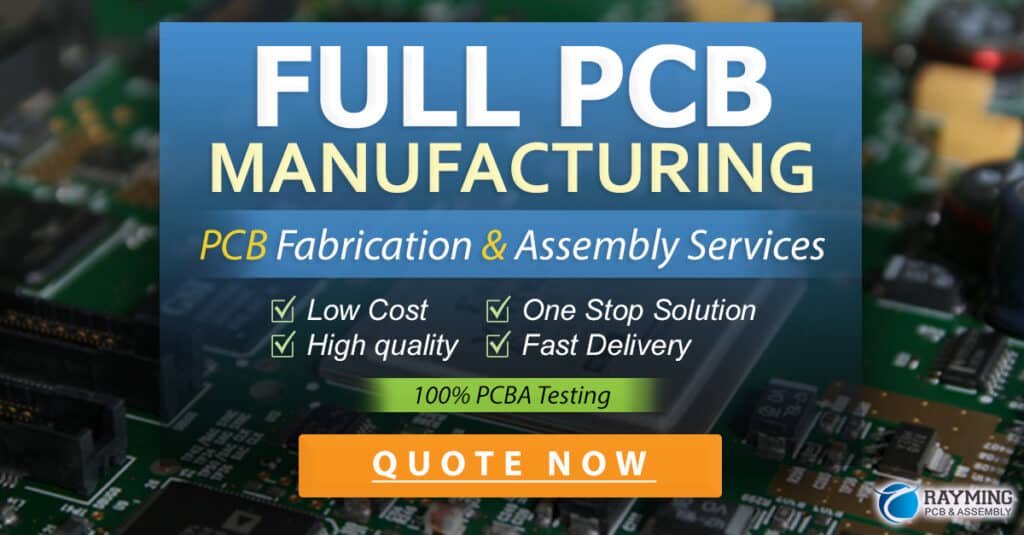
Step 2: Printing the Circuit Pattern
With the design files ready, it’s time to print the circuit pattern onto the copper-clad laminate. There are two main imaging methods:
Photoengraving
Photoengraving uses a photomask and UV light to transfer the circuit image to the copper. Here’s how it works:
-
The copper-clad panel is coated with a layer of photoresist, a light-sensitive polymer.
-
A photomask (film or glass with opaque circuit pattern) is placed over the photoresist.
-
The panel is exposed to intense UV light. Where light passes through, it hardens the resist. Areas under the opaque parts of the mask remain soluble.
-
The panel is “developed” by spraying it with an alkaline solution. This removes the unexposed resist, leaving the circuit pattern.
Direct Imaging
Direct imaging is an increasingly popular alternative to photoengraving. Instead of using physical photomasks, the circuit pattern is printed directly onto the photoresist using a laser or inkjet printer. This allows quick turnaround for prototypes and avoids issues with mask alignment.
Step 3: Etching
After the resist is developed, the next step is to etch away the unwanted copper, leaving only the circuit traces. The most common etchant is acidified cupric chloride. Other etchants include:
- Ammoniacal
- Alkaline
- Cupric chloride (non-acidified)
The laminate is sprayed with or immersed in the etchant, which dissolves copper not protected by hardened resist. Factors affecting etch quality include:
- Etchant temperature
- Concentration
- Agitation
- Etch time
After etching, the remaining photoresist is stripped with a solvent, leaving the bare copper traces. An oxide treatment is sometimes applied to the copper to preserve solderability.
Step 4: Drilling
With the outer layers etched, holes are drilled through the board for two purposes:
- Vias – conductive holes that electrically connect different layers
- Component holes – for leads of through-hole parts
Drilling is done on computer-controlled machines with carbide drill bits. For large volumes, multiple boards are stacked up and drilled together to save time. The holes are then deburred to remove any rough edges.
Step 5: Plating and Finishing
If the board has more than two layers, the inner layers are laminated together with insulating prepreg sheets in between. Holes are then plated with electroless copper to make the barrel conductive. Additional copper is electroplated to the desired thickness (1-2 mils).
Step 6: Solder Mask Application
The solder mask is a polymer coating that covers the outer copper layers of the PCB, except for pads and holes where components will be soldered. It serves several purposes:
- Protects copper from oxidation and corrosion
- Prevents solder bridges between closely-spaced traces
- Insulates against short circuits
- Helps solder adhere to exposed pads
- Provides color-coding (typically green, but other colors are available)
Solder mask is applied by silkscreening a liquid photo-imageable ink, aligning a phototool, exposing it to UV light to harden, and developing it to remove unexposed areas. Alternatively, it can be laminated on as a dry film and photoimaged.
Step 7: Silkscreen
The silkscreen is the layer of text and graphics typically printed in white ink on the component side of the PCB. It labels component part numbers, polarity, test points, and other important information for assembly and troubleshooting. Like solder mask, silkscreen ink is applied through a phototool and screen.
Step 8: Surface Finish
The final metal coating applied to the PCB’s exposed copper is called the surface finish. Its main purposes are to:
- Protect bare copper circuitry
- Enhance solderability of component pads
- Prevent oxidation during storage
Common surface finishes include:
Finish | Composition | Pros | Cons |
---|---|---|---|
HASL (Hot Air Solder Leveling) | Tin-lead | Excellent solderability, low cost | Not RoHS compliant, uneven surface |
ENIG (Electroless Nickel Immersion Gold) | Nickel (1-2µm), gold (0.05-0.1µm) | Flat surface, gold wire-bondable | Higher cost, prone to “black pad” issue |
OSP (Organic Solderability Preservatives) | Thin organic film | Low-cost, easy to apply | Short shelf life compared to others |
After the surface finish is applied, the PCB fabrication process is nearly complete.
Step 9: Electrical Testing
To ensure PCB Quality and catch any fabrication defects, electrical testing is performed before shipping the finished boards. Two common tests are:
Flying Probe Test
A flying probe tester has two or more moving test pins that “fly” to different test points on the PCB, making continuity and isolation measurements between nets. It tests both bare boards and populated boards, and is ideal for prototypes or small volumes.
Bed of Nails Test
For large volumes, a bed of nails test fixture is faster and more cost-effective than flying probe. Spring-loaded pogo pins make contact with test pads on the PCB. The fixture is specific to the board design and requires more setup, but many boards can be tested in parallel.
Step 10: Cutting and Packaging
Finally, individual boards are routed out of the panel using a CNC machine or punched out with a die. They are visually inspected for obvious defects, packaged to prevent damage, and shipped to the customer.
Frequently Asked Questions
What is the typical turnaround time for PCB fabrication?
Depending on the complexity, a simple 2-layer board can be fabricated in 1-2 days, while a 4-6 layer board takes 3-5 days. Larger/thicker boards with 8+ layers may take 2 weeks or more. Rush services are available for a premium.
What factors affect the cost of PCB fabrication?
The main cost drivers are:
- Number of layers
- Board size
- Smallest trace/space
- Number of holes
- Surface finish
Generally, two layer boards are the most economical. Specifying wider trace/space (>8 mil), fewer holes, and standard surface finish (HASL) will minimize cost.
What are some common PCB fabrication defects?
Some fabrication issues to watch for include:
- Acid traps (inability to fully etch narrow channels)
- Voids/pinholes in copper traces
- Over/under-etching
- Misregistration between layers
- Damaged/missing solder mask or silkscreen
- Drill misalignment or breakout
Following design rules and working with a reputable fabrication house helps avoid these issues. Always inspect boards thoroughly before assembly.
What file formats do I need to provide for PCB fabrication?
The industry standard is Gerber RS-274X. At minimum you should provide the following Gerber files:
- GTL – Top copper
- GBL – Bottom copper
- GTS – Top soldermask
- GBS – Bottom soldermask
- GTO – Top silkscreen
- GBO – Bottom silkscreen
- TXT – Drill file
Additionally, an NC drill file, fabrication drawing, and PCB stackup are helpful.
How do I choose a PCB fabrication vendor?
Consider the following when selecting a fab house:
- Capabilities (layer count, materials, min feature size, etc.)
- Certifications (ISO-9001, UL, RoHS)
- Lead times
- Pricing
- Quality/yield
- Support and communication
Look for a vendor who specializes in your type of product, whether that’s quick-turn prototypes or high-volume production. Get quotes and feedback from multiple vendors before committing.
Conclusion
We’ve covered the PCB fabrication process from design through shipping and everything in between. While it may seem daunting at first, having a grasp of the steps and terminology will help you navigate the process with confidence.
Remember that communication is key – work closely with your fabrication vendor and don’t hesitate to ask questions. By understanding their capabilities and design rules, you can ensure a smooth, successful manufacturing experience.
No responses yet