Introduction to Wire Harnesses
A wire harness, also known as a cable harness or wiring assembly, is a collection of wires, cables, and connectors that are bundled together to transmit electrical power or signals in various applications. These harnesses are essential components in numerous industries, including automotive, aerospace, medical devices, telecommunications, and consumer electronics.
Wire harnesses are designed to simplify and organize complex electrical systems by combining multiple wires into a single, compact unit. This not only reduces the risk of errors during installation but also improves the overall efficiency and reliability of the system.
Benefits of Using Wire Harnesses
- Simplified installation process
- Reduced wiring errors
- Improved system reliability
- Enhanced electrical performance
- Space-saving design
- Cost-effective solution
The Role of Custom Wire Harness Manufacturers
Custom wire harness manufacturers play a crucial role in designing, engineering, and producing tailored wiring solutions for specific applications. These manufacturers work closely with their clients to understand their unique requirements and develop harnesses that meet or exceed industry standards.
Services Offered by Custom Wire Harness Manufacturers
- Design and engineering
- Prototyping and testing
- Materials selection
- Production and assembly
- Quality control and inspection
- Packaging and shipping
Wire Harness Design and Engineering
The design and engineering process is a critical aspect of custom wire harness manufacturing. This process involves several stages, including:
- Requirements gathering and analysis
- Schematic and wiring diagram creation
- Materials selection
- Prototyping and testing
- Design optimization and finalization
Factors to Consider in Wire Harness Design
- Electrical requirements (voltage, current, and signal types)
- Environmental conditions (temperature, humidity, and vibration)
- Space constraints and routing
- Regulatory compliance and industry standards
- Manufacturability and assembly considerations
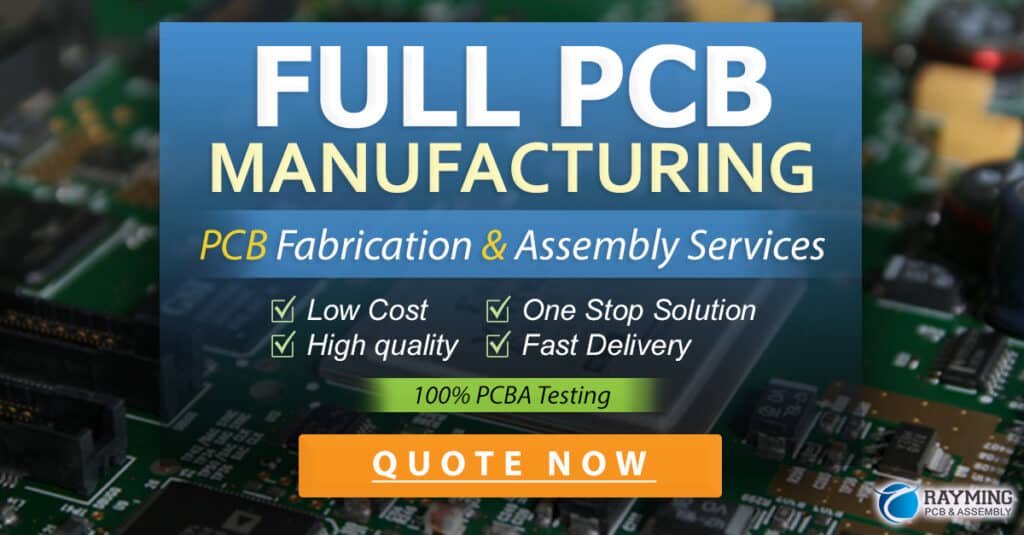
Materials Used in Wire Harness Manufacturing
Custom wire harness manufacturers use a wide range of materials to ensure optimal performance, reliability, and durability of their products. Some of the key materials include:
Wires and Cables
Material | Characteristics | Applications |
---|---|---|
Copper | High conductivity, ductility, and resistance to corrosion | General-purpose wiring |
Aluminum | Lightweight, cost-effective, and good conductivity | Automotive and aerospace |
Silver-plated copper | Enhanced conductivity and corrosion resistance | High-frequency and RF applications |
Insulation and Jacketing Materials
Material | Characteristics | Applications |
---|---|---|
PVC (Polyvinyl Chloride) | Flexibility, durability, and resistance to abrasion and chemicals | General-purpose wiring |
Teflon (PTFE) | High-temperature resistance, low friction, and excellent dielectric properties | Aerospace and medical devices |
Silicone rubber | High-temperature resistance, flexibility, and biocompatibility | Automotive and medical devices |
Connectors and Terminals
Type | Characteristics | Applications |
---|---|---|
Crimp connectors | Secure, reliable, and easy to install | General-purpose wiring |
Solder connectors | Permanent and low-resistance connections | High-reliability applications |
IDC (Insulation Displacement Connectors) | Quick and easy installation without stripping insulation | Mass-production and high-density wiring |
Wire Harness Assembly Process
The wire harness assembly process involves several steps to ensure consistent quality and reliability. These steps include:
- Cutting and stripping wires to the required lengths
- Crimping or soldering terminals and connectors
- Bundling and taping wires together
- Applying labels and identification markers
- Testing and inspection
- Packaging and shipping
Automation in Wire Harness Assembly
Many custom wire harness manufacturers employ automated solutions to streamline the assembly process and improve efficiency. Some examples of automation include:
- Wire cutting and stripping machines
- Crimping and termination machines
- Ultrasonic welding for splicing wires
- Automated testing and inspection systems
Quality Control and Testing
Quality control and testing are essential aspects of custom wire harness manufacturing to ensure the final product meets the required specifications and performance standards. Some common quality control and testing methods include:
- Visual inspection for defects and proper assembly
- Continuity and resistance testing
- Insulation resistance testing
- Dielectric strength testing
- Functional and performance testing
Importance of Quality Control and Testing
Implementing strict quality control and testing procedures helps:
- Identify and rectify defects early in the manufacturing process
- Ensure consistent product quality and reliability
- Minimize the risk of field failures and product recalls
- Maintain customer satisfaction and brand reputation
Industry Standards and Certifications
Custom wire harness manufacturers must adhere to various industry standards and certifications to ensure their products meet the required safety, quality, and performance criteria. Some key standards and certifications include:
- UL (Underwriters Laboratories)
- IPC/WHMA-A-620 (Requirements and Acceptance for Cable and Wire Harness Assemblies)
- ISO 9001 (Quality Management System)
- IATF 16949 (Automotive Quality Management System)
- AS9100 (Aerospace Quality Management System)
Benefits of Adhering to Industry Standards
- Ensures consistent product quality and reliability
- Facilitates compatibility and interoperability between different components and systems
- Enhances customer confidence and trust in the manufacturer
- Helps manufacturers stay competitive in the global market
Applications of Custom Wire Harnesses
Custom wire harnesses find applications in a wide range of industries, each with its unique requirements and challenges. Some of the key industries and applications include:
Automotive Industry
- Engine wiring harnesses
- Body and chassis wiring harnesses
- Infotainment and navigation systems
- Advanced driver assistance systems (ADAS)
Aerospace Industry
- Avionics systems
- In-flight entertainment systems
- Cabin management systems
- Electrical power distribution systems
Medical Devices
- Diagnostic and monitoring equipment
- Surgical instruments
- Imaging systems
- Patient monitoring devices
Telecommunications
- Fiber optic cable assemblies
- Coaxial cable assemblies
- Data center wiring solutions
- 5G infrastructure
Industrial Automation
- Control panels and cabinets
- Robotics and machine wiring
- Sensors and actuators
- Power distribution systems
Choosing the Right Custom Wire Harness Manufacturer
Selecting the right custom wire harness manufacturer is crucial for the success of your project. Consider the following factors when making your decision:
- Experience and expertise in your industry
- Design and engineering capabilities
- Manufacturing capacity and lead times
- Quality control and testing processes
- Certifications and compliance with industry standards
- Customer support and communication
Questions to Ask a Potential Manufacturer
- What is your experience in manufacturing wire harnesses for my specific industry and application?
- Can you provide references or case studies of similar projects you have completed?
- What design and engineering services do you offer?
- How do you ensure the quality and reliability of your products?
- What is your typical lead time for a project like mine?
Future Trends in Wire Harness Manufacturing
As technology continues to advance, custom wire harness manufacturers must adapt to new trends and challenges in the industry. Some of the key trends shaping the future of wire harness manufacturing include:
- Miniaturization and high-density wiring solutions
- Increased use of lightweight materials, such as aluminum and fiber optics
- Adoption of Industry 4.0 technologies, such as IoT, AI, and machine learning
- Growing demand for electric and hybrid vehicles in the automotive industry
- Expansion of 5G networks and infrastructure in the telecommunications industry
Challenges and Opportunities
These trends present both challenges and opportunities for custom wire harness manufacturers. Some of the key challenges include:
- Adapting to rapidly changing technologies and customer requirements
- Ensuring compatibility and interoperability between different components and systems
- Managing supply chain disruptions and material shortages
- Maintaining cost competitiveness while investing in new technologies and processes
However, these challenges also present opportunities for manufacturers to:
- Develop innovative solutions and differentiate themselves in the market
- Expand into new industries and applications
- Forge strategic partnerships with suppliers, customers, and technology providers
- Improve operational efficiency and productivity through automation and digitalization
Conclusion
Custom wire harness manufacturers play a vital role in the development and production of electrical systems across various industries. By providing tailored wiring solutions that meet specific requirements and standards, these manufacturers help their clients improve system performance, reliability, and efficiency.
As technology continues to evolve, custom wire harness manufacturers must remain agile and adaptable to stay competitive in the global market. By investing in advanced manufacturing processes, quality control, and customer support, these manufacturers can position themselves as trusted partners for their clients and contribute to the advancement of their respective industries.
Frequently Asked Questions (FAQ)
-
What is the difference between a wire harness and a cable assembly?
A wire harness is a collection of wires, cables, and connectors that are bundled together to transmit electrical power or signals, while a cable assembly typically refers to a single cable with connectors on one or both ends. -
How long does it take to design and manufacture a custom wire harness?
The lead time for designing and manufacturing a custom wire harness varies depending on the complexity of the project, the materials required, and the manufacturer’s capacity. Typically, it can range from a few weeks to several months. -
Can custom wire harnesses be designed for harsh environments?
Yes, custom wire harnesses can be designed to withstand harsh environments, such as extreme temperatures, humidity, vibration, and chemical exposure. Manufacturers use specialized materials, insulation, and jacketing to ensure the harness can perform reliably in these conditions. -
What are the most common wire and cable materials used in custom wire harnesses?
The most common wire and cable materials used in custom wire harnesses are copper, aluminum, and silver-plated copper. The choice of material depends on factors such as conductivity, weight, cost, and the specific application requirements. -
How can I ensure that my custom wire harness meets the required industry standards and certifications?
To ensure your custom wire harness meets the required industry standards and certifications, work with a reputable manufacturer that has experience in your industry and a proven track record of compliance. Discuss your specific requirements and ask for documentation of their certifications and quality control processes.
No responses yet