What is a Wire Harness?
A wire harness, also known as a cable harness or wiring assembly, is a systematic and organized bundle of wires, cables, and connectors that transmit electrical power or signals in various applications, such as automobiles, aircraft, appliances, and industrial machinery. The primary purpose of a wire harness is to simplify the installation process, minimize wiring errors, and ensure efficient and reliable transmission of electrical signals and power throughout the system.
Components of a Wire Harness
A typical wire harness consists of the following components:
- Wires and cables
- Connectors and terminals
- Protective coverings (e.g., sleeves, conduits, or tapes)
- Fasteners and mounting hardware
Wires and Cables
Wires and cables are the primary components of a wire harness. They are selected based on factors such as current carrying capacity, voltage rating, insulation properties, and environmental conditions (e.g., temperature, humidity, and chemical exposure). Common types of wires and cables used in wire harnesses include:
- Copper wires
- Aluminum wires
- Coaxial cables
- Twisted pair cables
- Fiber optic cables
Connectors and Terminals
Connectors and terminals are used to establish electrical connections between wires, cables, and other components within the wire harness. They ensure secure and reliable connections and allow for easy installation, maintenance, and replacement of components. Some common types of connectors and terminals include:
- Crimp terminals
- Soldered terminals
- Insulation displacement connectors (IDCs)
- Circular connectors
- Rectangular connectors
- D-sub connectors
Protective Coverings
Protective coverings are used to shield the wires and cables from environmental factors, such as abrasion, moisture, and extreme temperatures. They also help to organize and bundle the wires for a cleaner and more manageable installation. Common types of protective coverings include:
- PVC sleeves
- Nylon braided sleeves
- Heat shrink tubing
- Corrugated conduits
- Vinyl tapes
Fasteners and Mounting Hardware
Fasteners and mounting hardware are used to secure the wire harness to the designated locations within the application, ensuring a stable and vibration-resistant installation. Examples of fasteners and mounting hardware include:
- Cable ties
- Adhesive mounts
- Clamps
- Brackets
- Grommets
Wire Harness Assembly Process
The wire harness assembly process typically involves the following steps:
- Design and Engineering
- Prototyping and Testing
- Production Planning
- Wire Cutting and Stripping
- Connector and Terminal Crimping
- Wire Routing and Bundling
- Quality Control and Testing
- Packaging and Shipping
Design and Engineering
The design and engineering phase involves creating a detailed schematic or blueprint of the wire harness based on the specific requirements of the application. This includes selecting the appropriate wires, cables, connectors, and protective coverings, as well as determining the optimal routing and layout of the harness.
Prototyping and Testing
Once the design is finalized, a prototype of the wire harness is created for testing and validation. This allows for any necessary modifications or improvements to be made before moving into full-scale production.
Production Planning
Production planning involves determining the most efficient and cost-effective method for manufacturing the wire harness. This includes deciding on the assembly line layout, equipment requirements, and workforce allocation.
Wire Cutting and Stripping
The first step in the actual assembly process is cutting the wires and cables to the required lengths and stripping the insulation from the ends to expose the conductors for termination.
Connector and Terminal Crimping
The exposed conductors are then inserted into the appropriate connectors or terminals and securely crimped using specialized tooling to ensure a reliable electrical connection.
Wire Routing and Bundling
The terminated wires and cables are routed and bundled according to the designed layout, using protective coverings and fasteners to organize and secure the harness.
Quality Control and Testing
Throughout the assembly process, quality control measures are implemented to ensure that the wire harness meets the required specifications and standards. This includes visual inspections, continuity testing, and functional testing to verify the integrity and performance of the harness.
Packaging and Shipping
Once the wire harness has passed all quality control checks, it is carefully packaged to prevent damage during transportation and shipped to the customer or end-user.
Applications of Wire Harnesses
Wire harnesses are used in a wide range of industries and applications, including:
- Automotive
- Aerospace
- Medical Devices
- Industrial Machinery
- Consumer Electronics
- Telecommunications
- Military and Defense
Automotive
In the automotive industry, wire harnesses are used to distribute electrical power and signals throughout the vehicle, connecting various components such as the engine, sensors, lights, and infotainment systems. Some common automotive wire harnesses include:
- Engine wiring harness
- Body wiring harness
- Chassis wiring harness
- Instrument panel wiring harness
Aerospace
Wire harnesses are critical components in aircraft, as they ensure the reliable transmission of electrical power and signals for navigation, communication, and control systems. They must be designed to withstand the harsh environmental conditions encountered in aerospace applications, such as extreme temperatures, vibration, and altitude.
Medical Devices
Medical devices, such as patient monitors, imaging equipment, and surgical instruments, rely on wire harnesses to transmit electrical signals and power between various components. These harnesses must be designed to meet strict safety and reliability standards to ensure patient safety and device performance.
Industrial Machinery
Industrial machinery, such as manufacturing equipment, robotics, and automation systems, uses wire harnesses to interconnect various components and subsystems. These harnesses must be durable and resistant to the harsh environmental conditions found in industrial settings, such as exposure to chemicals, extreme temperatures, and vibration.
Consumer Electronics
Wire harnesses are used in a wide range of consumer electronics, including smartphones, laptops, televisions, and home appliances. These harnesses must be designed for high-volume production and cost-effectiveness while still meeting the required performance and reliability standards.
Telecommunications
In the telecommunications industry, wire harnesses are used to interconnect various components within network infrastructure, such as routers, switches, and servers. These harnesses must be designed to handle high-speed data transmission and ensure signal integrity over long distances.
Military and Defense
Wire harnesses used in military and defense applications must be designed to withstand extreme environmental conditions and meet stringent reliability and performance requirements. These harnesses are used in a wide range of equipment, including vehicles, aircraft, communication systems, and weapon systems.
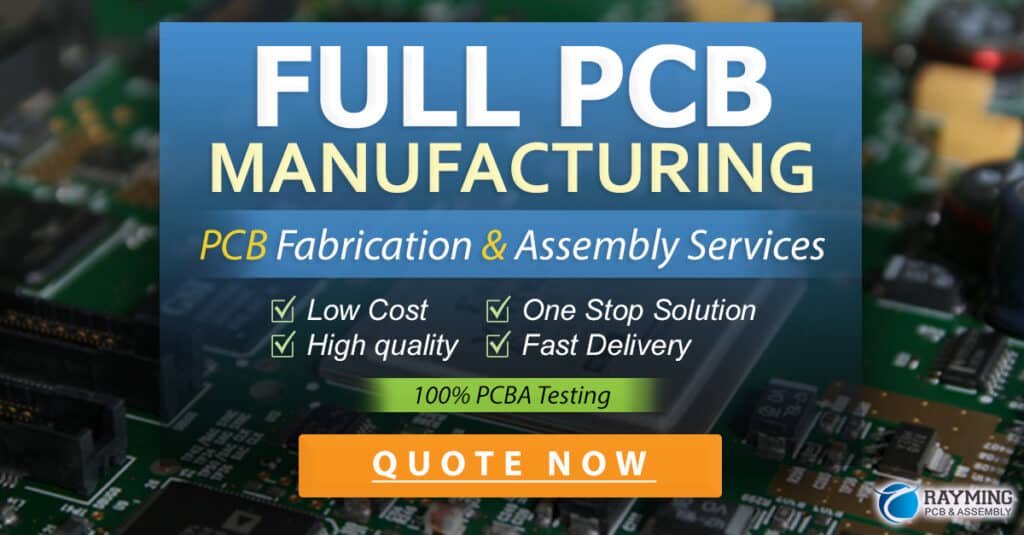
Benefits of Wire Harnesses
Using wire harnesses offers several benefits over traditional point-to-point wiring, including:
- Simplified Installation
- Reduced Wiring Errors
- Improved Reliability
- Enhanced Maintainability
- Space and Weight Savings
Simplified Installation
Wire harnesses are pre-assembled and tested before installation, which simplifies the installation process and reduces the time and labor required to interconnect various components within a system.
Reduced Wiring Errors
By using pre-assembled wire harnesses, the risk of wiring errors during installation is significantly reduced, as the harnesses are designed and tested to ensure the correct connections are made.
Improved Reliability
Wire harnesses are designed and manufactured to meet specific performance and reliability standards, ensuring that the electrical connections remain secure and stable over the life of the product.
Enhanced Maintainability
Wire harnesses are designed with maintainability in mind, allowing for easy replacement of individual components or sections of the harness without the need to rewire the entire system.
Space and Weight Savings
By bundling and organizing wires and cables into a compact harness, manufacturers can optimize space utilization and reduce the overall weight of the product, which is particularly important in applications such as automotive and aerospace.
Challenges in Wire Harness Assembly
Despite the many benefits of using wire harnesses, there are also several challenges that manufacturers must address during the assembly process, including:
- Complexity of Design
- Material Selection
- Quality Control
- Cost Optimization
- Regulatory Compliance
Complexity of Design
As products become more sophisticated and technologically advanced, the complexity of wire harness designs also increases. This requires manufacturers to invest in advanced design tools and skilled personnel to create and manage these complex designs.
Material Selection
Selecting the appropriate materials for wire harnesses is crucial to ensure the required performance, reliability, and durability. Manufacturers must consider factors such as environmental conditions, electrical requirements, and cost when selecting materials.
Quality Control
Ensuring consistent quality throughout the wire harness assembly process is a significant challenge, as even minor defects or variations can impact the performance and reliability of the final product. Manufacturers must implement strict quality control measures and testing procedures to identify and address any issues.
Cost Optimization
Wire harness manufacturing can be a cost-intensive process, particularly for complex designs or high-volume production. Manufacturers must continuously seek ways to optimize costs through process improvements, automation, and supply chain management.
Regulatory Compliance
Wire harnesses must comply with various industry standards and regulations, such as those related to safety, electromagnetic compatibility (EMC), and environmental protection. Manufacturers must stay up-to-date with the latest regulatory requirements and ensure that their products meet these standards.
Future Trends in Wire Harness Assembly
As technology continues to advance, the wire harness industry is also evolving to meet the changing needs of manufacturers and end-users. Some of the key trends shaping the future of wire harness assembly include:
- Automation and Robotics
- Miniaturization
- Wireless Technology
- Sustainable Manufacturing
- Industry 4.0
Automation and Robotics
Manufacturers are increasingly adopting automation and robotics technologies to improve the efficiency, accuracy, and consistency of wire harness assembly processes. This includes the use of automated wire cutting and stripping machines, robotic crimping and termination systems, and intelligent conveyor systems for material handling.
Miniaturization
As products become smaller and more compact, wire harnesses must also be miniaturized to fit within these reduced spaces. This requires the development of advanced materials, such as ultra-thin insulation and high-density connectors, as well as innovative design and manufacturing techniques.
Wireless Technology
The growing adoption of wireless technology is also impacting the wire harness industry, as some traditional wired connections are being replaced by wireless solutions. However, wire harnesses will continue to play a critical role in many applications, particularly those requiring high power transmission or data security.
Sustainable Manufacturing
Sustainability is becoming an increasingly important consideration in wire harness manufacturing, with a focus on reducing waste, minimizing environmental impact, and using eco-friendly materials. Manufacturers are exploring the use of recycled materials, biodegradable plastics, and energy-efficient production processes to meet these sustainability goals.
Industry 4.0
Industry 4.0, or the fourth industrial revolution, is transforming the manufacturing landscape through the integration of advanced technologies such as the Internet of Things (IoT), artificial intelligence (AI), and big data analytics. In the context of wire harness assembly, this means the development of smart factories with connected, data-driven production systems that enable real-time monitoring, predictive maintenance, and continuous optimization.
FAQ
- What is the difference between a wire harness and a cable assembly?
While wire harnesses and cable assemblies serve similar purposes, a wire harness typically refers to a more complex bundle of wires and cables that interconnect various components within a system. In contrast, a cable assembly is usually a simpler configuration, often consisting of a single cable with connectors at each end.
- How are wire harnesses designed?
Wire harnesses are designed using specialized software tools, such as electrical computer-aided design (ECAD) systems, that allow engineers to create detailed schematics and 3D models of the harness. The design process involves selecting the appropriate wires, cables, and connectors, determining the optimal routing and layout, and ensuring compliance with relevant standards and regulations.
- What materials are commonly used in wire harnesses?
Wire harnesses use a variety of materials, including copper or aluminum conductors for wires and cables, plastic or rubber insulation, and various types of connectors and terminals made from metals such as brass, copper, or aluminum. The specific materials used depend on the application requirements, such as electrical properties, environmental conditions, and cost considerations.
- How are wire harnesses tested for quality and performance?
Wire harnesses undergo rigorous testing throughout the assembly process to ensure quality and performance. This includes visual inspections, continuity testing to verify electrical connections, and functional testing to validate the harness’s performance under various operating conditions. Some common testing methods include high-voltage testing, insulation resistance testing, and environmental stress screening.
- What are some of the challenges in wire harness manufacturing, and how can they be addressed?
Some of the key challenges in wire harness manufacturing include managing complex designs, ensuring consistent quality, optimizing costs, and complying with regulatory requirements. These challenges can be addressed through the adoption of advanced technologies, such as automation and robotics, the implementation of strict quality control measures, and the continuous improvement of processes and materials. Additionally, close collaboration between manufacturers, suppliers, and customers is essential to ensure that wire harnesses meet the required specifications and performance standards.
In conclusion, wire harnesses play a critical role in the functioning of various electrical and electronic systems across a wide range of industries. By simplifying installation, reducing wiring errors, and improving reliability and maintainability, wire harnesses offer significant benefits over traditional point-to-point wiring. As technology continues to advance, the wire harness industry must adapt to meet the changing needs of manufacturers and end-users, embracing trends such as automation, miniaturization, wireless technology, sustainable manufacturing, and Industry 4.0. Despite the challenges faced in wire harness assembly, the industry is well-positioned to support the growing demand for reliable, efficient, and cost-effective electrical interconnect solutions in the years to come.
No responses yet