Introduction to Copper in PCB Manufacturing
Copper is an essential material in the production of printed circuit boards (PCBs). It plays a crucial role in the functioning and performance of electronic devices. In PCB manufacturing, copper is used to create the conductive pathways that allow electrical signals to travel between components on the board. The quality, thickness, and patterning of the copper layers directly impact the reliability, signal integrity, and overall performance of the final PCB.
In this article, we will delve into the various aspects of copper in PCB manufacturing, including its properties, the different types of copper used, the PCB fabrication process, and the challenges and considerations associated with copper in PCB design and production.
Properties of Copper in PCB Manufacturing
Copper is the preferred material for PCB manufacturing due to its unique combination of properties that make it well-suited for electronic applications. Some of the key properties of copper that make it ideal for PCB production include:
-
High Electrical Conductivity: Copper is an excellent conductor of electricity, allowing for efficient and reliable transmission of electrical signals through the PCB traces.
-
Thermal Conductivity: Copper has good thermal conductivity, which helps dissipate heat generated by components on the PCB, preventing overheating and ensuring stable operation.
-
Durability: Copper is a relatively strong and durable material, able to withstand the stresses and strains encountered during PCB fabrication and assembly processes.
-
Corrosion Resistance: When properly treated and protected, copper exhibits good resistance to corrosion, ensuring the long-term reliability of the PCB.
-
Etch-ability: Copper can be easily etched using chemical or mechanical processes, allowing for the creation of intricate and precise circuit patterns on the PCB.
Comparison of Copper with Other Conductive Materials
While copper is the most commonly used material for PCB manufacturing, there are other conductive materials that can be used in specific applications. The following table compares the properties of copper with some alternative materials:
Material | Electrical Conductivity (S/m) | Thermal Conductivity (W/mK) | Durability | Cost |
---|---|---|---|---|
Copper | 5.96 × 10^7 | 401 | High | Low |
Silver | 6.30 × 10^7 | 429 | High | High |
Gold | 4.10 × 10^7 | 318 | High | High |
Aluminum | 3.50 × 10^7 | 237 | Moderate | Low |
As seen in the table, copper offers an excellent balance of high electrical and thermal conductivity, durability, and cost-effectiveness compared to other materials. This makes copper the preferred choice for most PCB manufacturing applications.
Types of Copper Used in PCB Manufacturing
There are several types of copper used in PCB manufacturing, each with specific characteristics and applications. The most common types include:
Electrodeposited Copper (ED Copper)
ED copper is the most widely used type of copper in PCB production. It is created by electroplating a thin layer of copper onto a dielectric substrate. ED copper offers good adhesion, uniformity, and etch-ability, making it suitable for creating fine-pitch traces and complex circuit patterns.
Rolled Annealed Copper (RA Copper)
RA copper is produced by rolling copper foils under high pressure and temperature, followed by an annealing process to improve its mechanical properties. RA copper exhibits higher ductility and better thermal stability compared to ED copper, making it ideal for applications that require greater flexibility or exposure to higher temperatures.
High-Temperature Elongation (HTE) Copper
HTE copper is a special grade of RA copper that is optimized for high-temperature applications. It maintains its mechanical properties and structural integrity at elevated temperatures, making it suitable for PCBs used in automotive, aerospace, and industrial environments.
Reverse Treated Copper (RTF)
RTF copper undergoes a special surface treatment process that enhances its adhesion to the dielectric substrate and improves its resistance to delamination. This type of copper is commonly used in high-reliability PCBs for aerospace, defense, and medical applications.
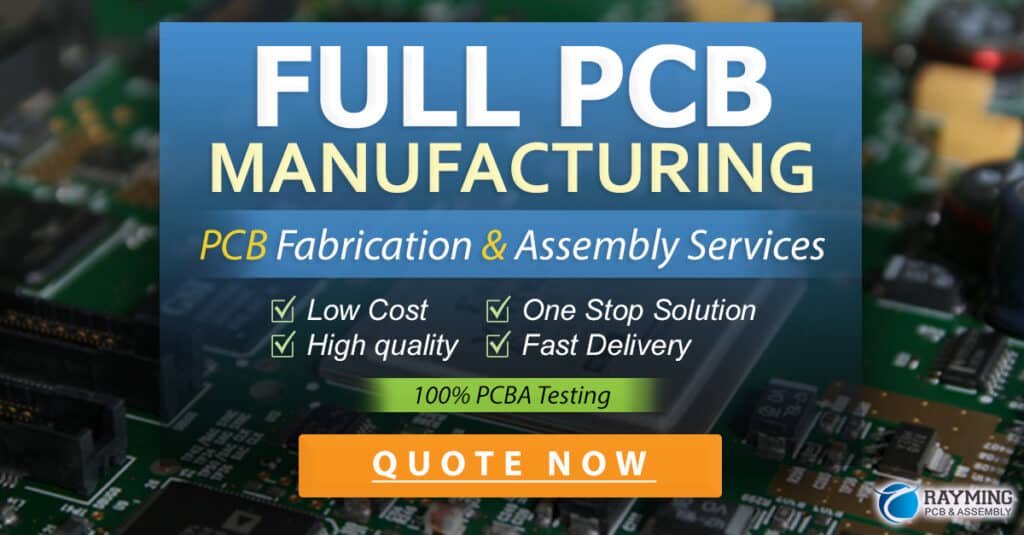
PCB Fabrication Process with Copper
The PCB fabrication process involves several steps that utilize copper to create the conductive layers and circuit patterns on the board. The main stages of PCB fabrication with copper include:
-
Substrate Preparation: The dielectric substrate, typically FR-4, is cleaned and prepared for copper deposition.
-
Copper Deposition: A thin layer of copper is deposited onto the substrate using electroplating or lamination techniques.
-
Patterning: The desired circuit pattern is transferred onto the copper layer using photolithography and etching processes.
-
Multilayer Lamination: For Multilayer PCBs, additional layers of copper and dielectric material are laminated together under high pressure and temperature.
-
Drilling: Holes are drilled through the PCB to accommodate components and create interconnections between layers.
-
Plating: The drilled holes are plated with copper to establish electrical connections between layers.
-
Surface Finish: A protective surface finish, such as HASL, ENIG, or OSP, is applied to the exposed copper areas to prevent oxidation and enhance solderability.
Throughout the fabrication process, proper control and management of the copper layers are crucial to ensure the quality, reliability, and performance of the final PCB.
Challenges and Considerations in Copper PCB Manufacturing
While copper is an excellent material for PCB manufacturing, there are several challenges and considerations that must be addressed to ensure optimal performance and reliability:
Copper Thickness and Trace Width
The thickness of the copper layers and the width of the traces on the PCB have a significant impact on signal integrity, current-carrying capacity, and manufacturing feasibility. Thicker copper layers can handle higher currents and provide better heat dissipation, but they also increase the cost and complexity of the manufacturing process. Narrower traces allow for higher component density and more compact designs, but they are more susceptible to signal loss and crosstalk.
PCB designers must carefully balance copper thickness and trace width based on the specific requirements of the application, taking into account factors such as signal frequency, power consumption, and manufacturing capabilities.
Copper Surface Roughness
The surface roughness of the copper layers can affect the adhesion of the dielectric material, the uniformity of the etching process, and the signal integrity of the PCB. Rough copper surfaces can lead to issues such as delamination, signal reflection, and increased insertion loss.
To mitigate these issues, PCB manufacturers employ various surface treatment techniques, such as chemical microetching or mechanical polishing, to control the surface roughness of the copper layers and ensure optimal performance.
Copper Losses and Signal Integrity
As signal frequencies increase, the impact of copper losses on signal integrity becomes more significant. Copper losses, including skin effect and dielectric losses, can lead to signal attenuation, distortion, and increased insertion loss, particularly at high frequencies.
To minimize copper losses and maintain signal integrity, PCB designers must consider factors such as trace geometry, dielectric material selection, and the use of impedance control techniques. Advanced manufacturing processes, such as high-density interconnect (HDI) and embedded trace technologies, can also help mitigate copper losses and improve signal performance.
Thermal Management
The thermal conductivity of copper plays a crucial role in the thermal management of PCBs. As electronic components generate heat during operation, the copper layers must effectively dissipate this heat to prevent overheating and ensure reliable performance.
PCB designers must consider the placement of high-heat-generating components, the use of thermal vias and heat sinks, and the selection of appropriate copper thicknesses to optimize thermal management. In some cases, advanced cooling techniques, such as liquid cooling or phase-change materials, may be necessary to address extreme thermal challenges.
Frequently Asked Questions (FAQ)
-
What is the typical thickness of copper used in PCB manufacturing?
The typical thickness of copper used in PCB manufacturing ranges from 0.5 oz (17.5 μm) to 4 oz (140 μm), with 1 oz (35 μm) being the most common. The choice of copper thickness depends on the specific requirements of the application, such as current-carrying capacity, signal integrity, and manufacturing constraints. -
Can copper be recycled from PCBs?
Yes, copper can be recycled from PCBs through various recycling processes. PCB Recycling involves the separation of different materials, including copper, from the board. The recovered copper can then be purified and reused in new PCB manufacturing or other applications, reducing environmental impact and conserving resources. -
What is the difference between single-sided and double-sided copper PCBs?
Single-sided copper PCBs have a copper layer on only one side of the dielectric substrate, while double-sided copper PCBs have copper layers on both sides. Double-sided PCBs offer more design flexibility, higher component density, and better signal routing compared to single-sided PCBs. However, they are also more complex and expensive to manufacture. -
How does copper thickness affect the current-carrying capacity of PCB traces?
The current-carrying capacity of PCB traces is directly proportional to the cross-sectional area of the copper trace. Thicker copper layers allow for higher current-carrying capacity, as they provide a larger cross-sectional area for the current to flow through. PCB designers must consider the required current-carrying capacity when selecting the appropriate copper thickness for their design. -
What are the advantages of using high-temperature elongation (HTE) copper in PCBs?
HTE copper offers several advantages for PCBs exposed to high-temperature environments. It maintains its mechanical properties and structural integrity at elevated temperatures, reducing the risk of thermal stress-induced failures. HTE copper also exhibits better thermal stability and resistance to thermal cycling, making it suitable for applications in automotive, aerospace, and industrial sectors where temperature fluctuations are common.
Conclusion
Copper plays a vital role in PCB manufacturing, serving as the primary conductive material for creating the intricate network of traces and interconnections that enable the functioning of electronic devices. The properties of copper, including its high electrical and thermal conductivity, durability, and etch-ability, make it an ideal choice for PCB production.
However, the use of copper in PCB manufacturing also presents various challenges and considerations, such as copper thickness and trace width optimization, surface roughness control, signal integrity management, and thermal management. PCB designers and manufacturers must carefully address these factors to ensure the optimal performance, reliability, and manufacturability of the final product.
As electronic devices continue to advance in complexity and performance, the importance of copper in PCB manufacturing will only continue to grow. By understanding the properties, types, and challenges associated with copper in PCB production, designers and manufacturers can make informed decisions and develop innovative solutions to meet the ever-increasing demands of the electronics industry.
No responses yet