Introduction to Copper fills
Copper fills, also known as copper fill-ins or copper filling, is a technique used in printed circuit board (PCB) manufacturing to fill in vias and plated through holes (PTHs) with copper. This process is typically done after the initial copper plating step and before the application of the Solder Mask.
The primary purpose of copper fills is to improve the mechanical strength and reliability of the PCB by reinforcing the vias and PTHs. Additionally, copper fills can enhance the thermal and electrical properties of the board, making it more suitable for high-power and high-frequency applications.
Advantages of Copper Fills
- Increased mechanical strength
- Improved thermal conductivity
- Enhanced electrical performance
- Better reliability and durability
- Reduced risk of barrel cracking
The Copper Fill Process
The copper fill process involves several steps to ensure proper filling of the vias and PTHs. The following table outlines the general steps involved in the copper fill process:
Step | Description |
---|---|
1 | Drilling of vias and PTHs |
2 | Copper plating of the board |
3 | Cleaning and preparation of the board surface |
4 | Application of the copper fill material |
5 | Curing and drying of the copper fill material |
6 | Planarization and Surface Finishing |
Drilling of Vias and PTHs
The first step in the copper fill process is the drilling of vias and PTHs. This is typically done using a CNC drilling machine or a laser drill, depending on the size and complexity of the board. The drilled holes must be clean and free of debris to ensure proper copper plating and filling.
Copper Plating
After drilling, the board undergoes a copper plating process to create a conductive layer on the surface of the board and inside the vias and PTHs. This is typically done using an electroplating process, where the board is immersed in a copper sulfate solution and an electric current is applied to deposit the copper onto the board surface.
Cleaning and Preparation
Before applying the copper fill material, the board surface must be cleaned and prepared to ensure proper adhesion. This typically involves a desmear process to remove any residual drilling debris and a surface roughening step to improve the adhesion of the fill material.
Application of the Copper Fill Material
The copper fill material is then applied to the board surface, typically using a screen printing or stencil printing process. The fill material is a paste-like substance that contains copper particles suspended in a binding agent.
Curing and Drying
After application, the copper fill material must be cured and dried to harden and adhere properly to the board surface. This is typically done in an oven or a convection dryer, where the board is exposed to high temperatures for a specific duration.
Planarization and Surface Finishing
Finally, the board undergoes a planarization process to remove any excess copper fill material and create a smooth, level surface. This is typically done using a chemical-mechanical planarization (CMP) process or a mechanical grinding process. After planarization, the board may undergo additional surface finishing steps, such as solder mask application or surface plating, depending on the specific requirements of the application.
Mechanical Properties of Copper Fills
The mechanical properties of copper fills are a critical consideration in PCB Design and manufacturing. The following table outlines some of the key mechanical properties of copper fills:
Property | Description | Typical Values |
---|---|---|
Tensile Strength | The maximum stress that the material can withstand before breaking | 200-300 MPa |
Elongation | The maximum strain that the material can undergo before breaking | 5-15% |
Young’s Modulus | The ratio of stress to strain, indicating the stiffness of the material | 100-130 GPa |
Coefficient of Thermal Expansion (CTE) | The amount of expansion or contraction per degree of temperature change | 17-18 ppm/°C |
Hardness | The resistance of the material to indentation or scratching | 80-100 HV |
Tensile Strength
The tensile strength of copper fills is an important consideration in PCB design, as it determines the maximum stress that the board can withstand before breaking. Copper fills typically have a tensile strength of 200-300 MPa, which is higher than that of the base PCB material (typically FR-4). This increased strength helps to prevent barrel cracking and other mechanical failures in the vias and PTHs.
Elongation
Elongation refers to the maximum strain that the copper fill material can undergo before breaking. Copper fills typically have an elongation of 5-15%, which is lower than that of the base PCB material. This lower elongation can help to reduce the risk of via and PTH failures due to thermal or mechanical stress.
Young’s Modulus
Young’s modulus, also known as the elastic modulus, is a measure of the stiffness of the copper fill material. It is defined as the ratio of stress to strain and is typically expressed in gigapascals (GPa). Copper fills typically have a Young’s modulus of 100-130 GPa, which is higher than that of the base PCB material. This increased stiffness can help to improve the mechanical stability and reliability of the board.
Coefficient of Thermal Expansion (CTE)
The coefficient of thermal expansion (CTE) is a measure of how much the copper fill material expands or contracts with changes in temperature. Copper fills typically have a CTE of 17-18 ppm/°C, which is similar to that of the copper plating on the board. This matched CTE helps to reduce the risk of thermal stress and cracking in the vias and PTHs.
Hardness
The hardness of the copper fill material is a measure of its resistance to indentation or scratching. Copper fills typically have a hardness of 80-100 HV (Vickers hardness), which is higher than that of the base PCB material. This increased hardness can help to improve the wear resistance and durability of the board.
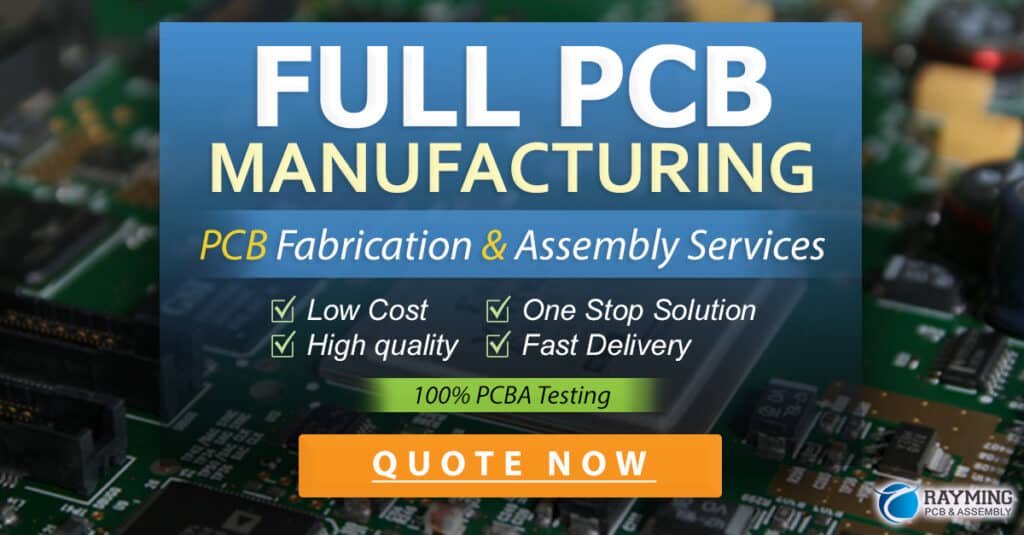
Factors Affecting the Mechanical Properties of Copper Fills
Several factors can affect the mechanical properties of copper fills, including:
- Fill material composition
- Fill process parameters
- Via and PTH geometry
- Board material and thickness
Fill Material Composition
The composition of the copper fill material can have a significant impact on its mechanical properties. The fill material typically consists of copper particles suspended in a binding agent, and the size, shape, and distribution of these particles can affect the strength, stiffness, and other properties of the fill.
Fill Process Parameters
The parameters used in the copper fill process, such as the printing pressure, curing temperature, and curing time, can also affect the mechanical properties of the fill. Proper optimization of these parameters is essential to achieve the desired fill properties and ensure reliable performance.
Via and PTH Geometry
The geometry of the vias and PTHs, including their size, shape, and aspect ratio, can also impact the mechanical properties of the copper fill. Smaller vias and higher aspect ratios can make it more challenging to achieve complete and uniform filling, which can lead to reduced mechanical strength and reliability.
Board Material and Thickness
The material and thickness of the PCB can also affect the mechanical properties of the copper fill. Thicker boards and higher-performance materials, such as polyimide or PTFE, may require different fill process parameters and material compositions to achieve the desired mechanical properties.
Testing and Qualification of Copper Fills
To ensure the reliability and performance of copper fills, various testing and qualification methods are used. These methods typically involve subjecting the filled vias and PTHs to mechanical, thermal, and environmental stresses to evaluate their durability and stability.
Some common testing methods for copper fills include:
- Cross-sectioning and microscopy
- Thermal cycling
- Mechanical shock and vibration
- Humidity and temperature cycling
- Accelerated life testing
Cross-Sectioning and Microscopy
Cross-sectioning and microscopy are used to visually inspect the quality and uniformity of the copper fill in the vias and PTHs. This involves cutting the board along the via or PTH and examining the cross-section under a microscope to check for voids, cracks, or other defects.
Thermal Cycling
Thermal cycling tests involve subjecting the board to repeated cycles of high and low temperatures to evaluate the stability and durability of the copper fill under thermal stress. This can help to identify any issues with thermal expansion mismatch or poor adhesion between the fill material and the board.
Mechanical Shock and Vibration
Mechanical shock and vibration tests are used to evaluate the resistance of the copper fill to physical stresses. These tests typically involve subjecting the board to high-acceleration impacts or vibrations and checking for any signs of cracking, delamination, or other mechanical failures.
Humidity and Temperature Cycling
Humidity and temperature cycling tests involve exposing the board to varying levels of humidity and temperature to evaluate the stability and durability of the copper fill under environmental stress. This can help to identify any issues with moisture absorption or degradation of the fill material.
Accelerated Life Testing
Accelerated life testing involves subjecting the board to elevated levels of stress, such as higher temperatures or voltages, to simulate the effects of long-term use and aging. This can help to predict the reliability and lifetime of the copper fill under real-world operating conditions.
FAQ
-
What is the purpose of copper fills in PCBs?
Copper fills are used to reinforce the mechanical strength and reliability of vias and plated through holes (PTHs) in PCBs. They also improve the thermal and electrical performance of the board. -
How are copper fills applied to PCBs?
Copper fills are typically applied using a screen printing or stencil printing process, where a paste-like material containing copper particles is deposited onto the board surface and into the vias and PTHs. -
What factors can affect the mechanical properties of copper fills?
The mechanical properties of copper fills can be affected by the fill material composition, fill process parameters, via and PTH geometry, and board material and thickness. -
How are copper fills tested and qualified?
Copper fills are typically tested and qualified using methods such as cross-sectioning and microscopy, thermal cycling, mechanical shock and vibration, humidity and temperature cycling, and accelerated life testing. -
What are the typical tensile strength and elongation values for copper fills?
Copper fills typically have a tensile strength of 200-300 MPa and an elongation of 5-15%.
Conclusion
Copper fills are a critical component in the manufacturing of high-reliability PCBs. By reinforcing the mechanical strength and improving the thermal and electrical performance of vias and PTHs, copper fills help to ensure the durability and stability of the board under various operating conditions.
The mechanical properties of copper fills, such as tensile strength, elongation, and hardness, are key considerations in PCB design and manufacturing. These properties are influenced by various factors, including the fill material composition, fill process parameters, and board geometry.
To ensure the reliability and performance of copper fills, rigorous testing and qualification methods are used, including cross-sectioning, thermal cycling, mechanical shock and vibration, and accelerated life testing. By understanding the mechanical properties and performance characteristics of copper fills, PCB designers and manufacturers can optimize their designs and processes to achieve the highest levels of quality and reliability.
No responses yet