Introduction to Surface Finish and ENIPIG
Surface finish is a crucial aspect of manufacturing, as it determines the quality, appearance, and functionality of a product. In the electronics industry, achieving an exceptional surface finish is particularly important for ensuring reliable electrical connections and preventing corrosion. One technique that has gained popularity in recent years is ENIPIG (Electroless Nickel Immersion Palladium Immersion Gold), which offers several advantages over traditional surface finish methods.
What is ENIPIG?
ENIPIG is a type of surface finish that involves depositing multiple layers of metal onto a substrate, typically a printed circuit board (PCB). The process begins with an electroless nickel layer, followed by a thin layer of immersion palladium, and finally, a layer of immersion gold. This combination of metals provides excellent solderability, durability, and resistance to oxidation and corrosion.
Advantages of ENIPIG
- Improved solderability
- Enhanced durability
- Increased shelf life
- Better wire bonding performance
- Compatibility with lead-free soldering processes
The ENIPIG Process
Step 1: Electroless Nickel Plating
The first step in the ENIPIG process is electroless nickel plating. This involves immersing the substrate in a solution containing nickel ions and a reducing agent. The reducing agent causes the nickel ions to deposit onto the substrate surface, forming a uniform layer of nickel. The thickness of the nickel layer typically ranges from 3 to 6 microns.
Advantages of Electroless Nickel Plating
- Uniform thickness distribution
- Excellent corrosion resistance
- Good hardness and wear resistance
- Ability to plate on non-conductive surfaces
Step 2: Immersion Palladium Plating
After the electroless nickel layer is deposited, the substrate is immersed in a solution containing palladium ions. The palladium ions replace some of the nickel atoms on the surface, forming a thin layer of palladium. The thickness of the palladium layer is typically around 0.05 to 0.15 microns.
Advantages of Immersion Palladium Plating
- Prevents nickel oxidation
- Enhances solderability
- Provides a barrier between the nickel and gold layers
- Improves wire bonding performance
Step 3: Immersion Gold Plating
The final step in the ENIPIG process is immersion gold plating. The substrate is immersed in a solution containing gold ions, which replace some of the palladium atoms on the surface. The resulting gold layer is very thin, typically around 0.05 to 0.10 microns.
Advantages of Immersion Gold Plating
- Protects the palladium layer from oxidation
- Enhances solderability
- Provides a clean, oxide-free surface for assembly
- Improves shelf life of the finished product
Comparison of ENIPIG with Other Surface Finish Techniques
ENIG (Electroless Nickel Immersion Gold)
ENIG is another popular surface finish technique that involves depositing a layer of electroless nickel followed by a layer of immersion gold. While ENIG offers good solderability and corrosion resistance, it has some limitations compared to ENIPIG.
Characteristic | ENIG | ENIPIG |
---|---|---|
Nickel thickness | 3-6 μm | 3-6 μm |
Gold thickness | 0.05-0.10 μm | 0.05-0.10 μm |
Palladium layer | No | Yes |
Solderability | Good | Excellent |
Wire bonding performance | Fair | Good |
Black pad issue | Possible | Minimized |
ENEPIG (Electroless Nickel Electroless Palladium Immersion Gold)
ENEPIG is similar to ENIPIG, but it uses an electroless palladium plating process instead of immersion palladium. While ENEPIG offers comparable performance to ENIPIG, it is more expensive and complex due to the additional electroless palladium step.
Characteristic | ENEPIG | ENIPIG |
---|---|---|
Nickel thickness | 3-6 μm | 3-6 μm |
Palladium thickness | 0.05-0.15 μm | 0.05-0.15 μm |
Gold thickness | 0.05-0.10 μm | 0.05-0.10 μm |
Palladium plating method | Electroless | Immersion |
Process complexity | High | Medium |
Cost | High | Medium |
OSP (Organic Solderability Preservative)
OSP is a surface finish technique that involves applying an organic compound to the copper surface to prevent oxidation. While OSP is cost-effective and easy to apply, it has limited shelf life and solderability compared to ENIPIG.
Characteristic | OSP | ENIPIG |
---|---|---|
Shelf life | Limited (3-6 months) | Extended (12+ months) |
Solderability | Fair | Excellent |
Corrosion resistance | Fair | Excellent |
Cost | Low | Medium |
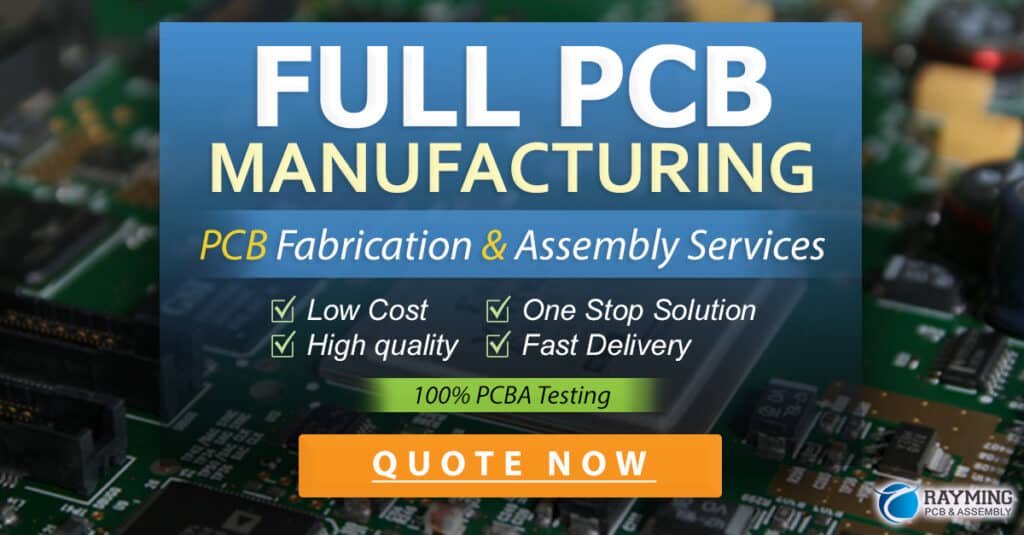
Applications of ENIPIG
ENIPIG is widely used in various industries, particularly in electronics manufacturing. Some common applications include:
- Printed Circuit Boards (PCBs)
- High-density interconnect (HDI) boards
- Rigid-flex boards
-
Multi-layer boards
-
Semiconductor Packaging
- Ball Grid Array (BGA) packages
- Quad Flat Package (QFP)
-
Chip Scale Package (CSP)
-
Automotive Electronics
- Engine control units (ECUs)
- Sensors and actuators
-
Infotainment systems
-
Medical Devices
- Implantable devices
- Diagnostic equipment
-
Wearable electronics
-
Aerospace and Defense
- Avionics systems
- Radar and communication equipment
- Satellite components
Implementing ENIPIG in Manufacturing
Equipment and Materials
To implement ENIPIG in a manufacturing process, the following equipment and materials are required:
- Plating line with tanks for electroless nickel, immersion palladium, and immersion gold
- Chemical solutions for each plating step
- Substrates (e.g., PCBs, package substrates)
- Rinse stations and drying equipment
- Quality control instruments (e.g., thickness gauges, XRF analyzers)
Process Control and Optimization
To ensure consistent and high-quality results, it is essential to control and optimize the ENIPIG process parameters. Some key factors to consider include:
- Solution composition and concentration
- Plating temperature and time
- Agitation and filtration of plating solutions
- Rinse water quality and temperature
- Drying conditions
Regular monitoring and maintenance of the plating line, as well as frequent quality checks, are necessary to maintain the desired surface finish characteristics.
Cost Considerations
Implementing ENIPIG in a manufacturing process involves several cost considerations, such as:
- Capital investment in plating equipment and infrastructure
- Operating costs, including chemicals, utilities, and labor
- Maintenance and repair costs
- Quality control and testing expenses
- Training and certification of personnel
While ENIPIG may have higher initial costs compared to simpler surface finish techniques like OSP, the long-term benefits in terms of product quality, reliability, and customer satisfaction can justify the investment.
Future Trends and Developments
As the electronics industry continues to evolve, new challenges and opportunities arise for surface finish technologies like ENIPIG. Some future trends and developments to watch include:
- Miniaturization and increased circuit density
- Adoption of advanced packaging techniques (e.g., 3D packaging, fanout wafer-level packaging)
- Growing demand for high-reliability electronics in harsh environments
- Increasing focus on sustainability and environmental regulations
- Development of new plating chemistries and processes
To stay competitive, manufacturers must continually adapt and innovate their surface finish strategies, while also ensuring compliance with industry standards and customer requirements.
FAQ
-
Q: What is the main difference between ENIPIG and ENIG?
A: The main difference between ENIPIG and ENIG is the presence of an immersion palladium layer in ENIPIG, which provides additional benefits such as improved solderability, wire bonding performance, and minimized black pad issues. -
Q: Is ENIPIG suitable for lead-free soldering processes?
A: Yes, ENIPIG is compatible with lead-free soldering processes and offers excellent solderability and reliability in lead-free applications. -
Q: How does ENIPIG compare to OSP in terms of cost and performance?
A: ENIPIG offers superior solderability, corrosion resistance, and shelf life compared to OSP, but it also comes with higher costs due to the additional plating steps and materials involved. -
Q: Can ENIPIG be used for both PCBs and semiconductor packaging?
A: Yes, ENIPIG is widely used in both PCB and semiconductor packaging applications, providing a high-quality surface finish for various package types and circuit board designs. -
Q: What are the key factors to consider when implementing ENIPIG in a manufacturing process?
A: When implementing ENIPIG, key factors to consider include equipment and material selection, process control and optimization, cost considerations, and staying updated with future trends and developments in the industry.
Conclusion
ENIPIG is an exceptional surface finish technique that offers numerous benefits for electronics manufacturing, including improved solderability, enhanced durability, and extended shelf life. By understanding the ENIPIG process, its advantages over other surface finish methods, and its wide range of applications, manufacturers can make informed decisions about implementing this technique in their production lines.
However, successfully implementing ENIPIG also requires careful consideration of equipment, materials, process control, and cost factors. As the electronics industry continues to evolve, staying informed about future trends and developments in surface finish technologies is crucial for maintaining a competitive edge and meeting customer demands.
By adopting ENIPIG and continuously optimizing its implementation, manufacturers can achieve the highest levels of product quality, reliability, and customer satisfaction, ultimately driving business success in the dynamic and challenging world of electronics manufacturing.
No responses yet