Introduction to Ceramic PCBs
Ceramic PCBs, also known as ceramic printed circuit boards, are a specialized type of PCB that offers unique properties and advantages over traditional FR-4 boards. In recent years, ceramic PCBs have gained popularity due to their excellent thermal conductivity, high dielectric strength, and superior mechanical stability. As we move into 2023, the demand for ceramic PCBs is expected to grow further, driven by advancements in technology and the need for highly customizable solutions.
This comprehensive guide will delve into the world of ceramic PCBs, exploring their composition, manufacturing process, applications, and the latest trends in the industry. Whether you are an engineer, designer, or enthusiast, this article will provide you with valuable insights to help you understand and leverage the potential of ceramic PCBs in your projects.
What are Ceramic PCBs?
Ceramic PCBs are printed circuit boards that use ceramic materials, such as alumina or aluminum nitride, as the substrate instead of the commonly used FR-4 material. These ceramic substrates offer several advantages over traditional PCB materials, including:
- High thermal conductivity
- Excellent electrical insulation
- Low dielectric loss
- High mechanical strength
- Resistance to harsh environments
The unique properties of ceramic PCBs make them ideal for applications that require superior thermal management, high-frequency performance, and reliability in demanding conditions.
Advantages of Ceramic PCBs
1. Thermal Management
One of the key advantages of ceramic PCBs is their excellent thermal conductivity. Ceramic materials, such as alumina and aluminum nitride, have a much higher thermal conductivity compared to FR-4. This property allows ceramic PCBs to efficiently dissipate heat generated by electronic components, preventing overheating and ensuring stable performance.
Material | Thermal Conductivity (W/mK) |
---|---|
Alumina (Al2O3) | 20-30 |
Aluminum Nitride (AlN) | 150-180 |
FR-4 | 0.3-0.4 |
As evident from the table above, ceramic materials offer significantly higher thermal conductivity than FR-4, making them ideal for applications that generate substantial heat.
2. Electrical Insulation and Low Dielectric Loss
Ceramic PCBs provide excellent electrical insulation due to the high dielectric strength of ceramic materials. This property allows for the design of high-voltage circuits and minimizes the risk of electrical breakdown. Additionally, ceramic PCBs exhibit low dielectric loss, which is crucial for high-frequency applications. Low dielectric loss ensures minimal signal attenuation and distortion, resulting in improved signal integrity and overall performance.
3. Mechanical Strength and Durability
Ceramic materials are known for their high mechanical strength and durability. Ceramic PCBs can withstand extreme temperatures, vibrations, and shocks without compromising their structural integrity. This makes them suitable for applications in harsh environments, such as aerospace, automotive, and industrial sectors, where reliability is of utmost importance.
4. Customization and Miniaturization
Ceramic PCBs offer a high degree of customization, allowing designers to create complex and intricate circuit layouts. The excellent electrical and thermal properties of ceramic materials enable the miniaturization of electronic components and the development of high-density PCBs. This is particularly advantageous in applications where space is limited, such as in portable devices and wearable technology.
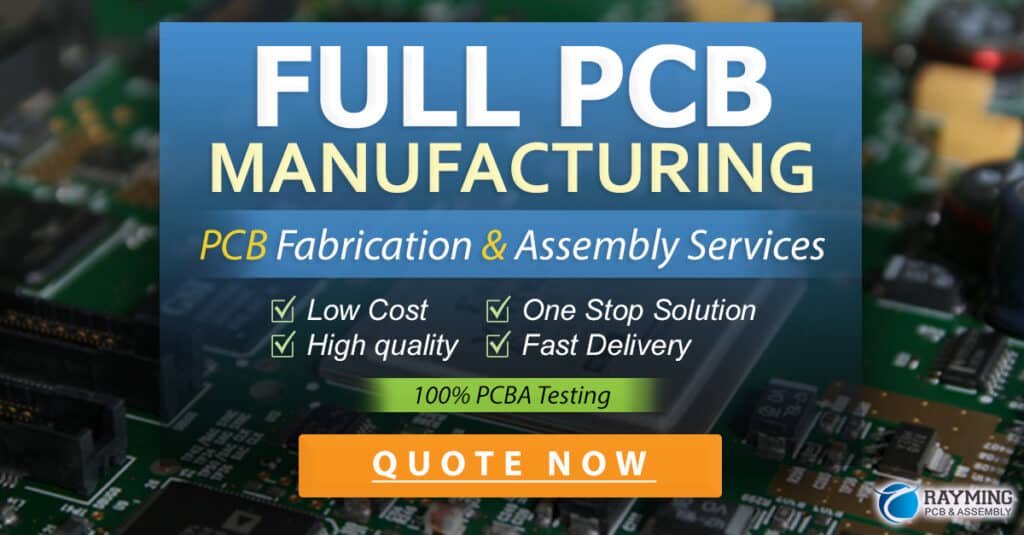
Manufacturing Process of Ceramic PCBs
The manufacturing process of ceramic PCBs differs from that of traditional FR-4 boards. Here is a brief overview of the key steps involved:
-
Substrate Preparation: The ceramic substrate, typically alumina or aluminum nitride, is prepared by mixing the ceramic powder with binders and additives. The mixture is then pressed into the desired shape and size.
-
Via Formation: Holes are drilled or punched into the ceramic substrate to create vias for electrical connections between layers.
-
Metallization: The vias and surface of the ceramic substrate are metallized using thin-film deposition techniques, such as sputtering or electroplating. This creates conductive paths for electrical signals.
-
Circuit Patterning: The desired circuit pattern is created on the metallized surface using photolithography and etching processes. This involves applying a photoresist layer, exposing it to UV light through a photomask, and developing the pattern.
-
Multilayer Lamination: For multilayer ceramic PCBs, additional ceramic layers are stacked and laminated together under high pressure and temperature.
-
Sintering: The laminated ceramic PCB is sintered in a high-temperature furnace to fuse the ceramic layers and create a dense, monolithic structure.
-
Surface Finishing: The final step involves applying surface finishes, such as nickel/gold plating or solder mask, to protect the circuit and enhance solderability.
The manufacturing process of ceramic PCBs requires specialized equipment and expertise due to the unique properties of ceramic materials and the high temperatures involved in sintering.
Applications of Ceramic PCBs
Ceramic PCBs find applications in various industries and sectors where high performance, reliability, and customization are critical. Some of the key application areas include:
-
Aerospace and Defense: Ceramic PCBs are used in avionics, satellite communication systems, radar equipment, and military electronics due to their ability to withstand extreme temperatures, vibrations, and radiation.
-
Automotive: In the automotive industry, ceramic PCBs are employed in engine control units, power electronics, and sensors, where they provide reliable performance in harsh environments.
-
High-Power Electronics: Ceramic PCBs are ideal for high-power applications, such as power amplifiers, inverters, and motor drives, thanks to their excellent thermal management capabilities.
-
RF and Microwave: The low dielectric loss and high-frequency performance of ceramic PCBs make them suitable for RF and microwave applications, including telecommunications, radar systems, and wireless devices.
-
Medical Devices: Ceramic PCBs are used in medical equipment, such as implantable devices, surgical instruments, and diagnostic tools, where biocompatibility and reliability are essential.
-
LED Lighting: The high thermal conductivity of ceramic PCBs helps in the efficient dissipation of heat generated by high-power LEDs, ensuring stable performance and extended lifespan.
Latest Trends and Innovations in Ceramic PCBs
As technology advances, the ceramic PCB industry continues to evolve and innovate to meet the growing demands of various sectors. Some of the latest trends and innovations in ceramic PCBs include:
-
3D Printing: The adoption of 3D printing technology in ceramic PCB manufacturing allows for the creation of complex geometries and faster prototyping, reducing development time and costs.
-
Embedded Components: Ceramic PCBs with embedded components, such as capacitors and resistors, offer higher levels of integration and miniaturization, enabling the development of more compact and efficient electronic devices.
-
High-Frequency Materials: The development of advanced ceramic materials with even lower dielectric loss and higher thermal conductivity is driving the performance of ceramic PCBs in high-frequency applications.
-
Hybrid Ceramic-Organic PCBs: The combination of ceramic and organic materials in PCB manufacturing offers the benefits of both technologies, providing a balance between thermal management, mechanical strength, and cost-effectiveness.
-
Sustainability and Eco-Friendly Practices: The ceramic PCB industry is increasingly focusing on sustainable manufacturing practices, including the use of recyclable materials and the reduction of waste and energy consumption.
Frequently Asked Questions (FAQs)
-
Q: What is the difference between ceramic PCBs and traditional FR-4 PCBs?
A: Ceramic PCBs use ceramic materials, such as alumina or aluminum nitride, as the substrate, while FR-4 PCBs use a glass-reinforced epoxy laminate. Ceramic PCBs offer superior thermal conductivity, electrical insulation, and mechanical strength compared to FR-4 PCBs. -
Q: Are ceramic PCBs more expensive than FR-4 PCBs?
A: Yes, ceramic PCBs are generally more expensive than FR-4 PCBs due to the higher cost of ceramic materials and the specialized manufacturing processes involved. However, the enhanced performance and reliability of ceramic PCBs justify the increased cost in many applications. -
Q: Can ceramic PCBs be used for high-frequency applications?
A: Yes, ceramic PCBs are well-suited for high-frequency applications due to their low dielectric loss and excellent electrical insulation properties. They are commonly used in RF and microwave applications, where signal integrity and minimal attenuation are crucial. -
Q: Are ceramic PCBs suitable for harsh environments?
A: Yes, ceramic PCBs are designed to withstand harsh environments, including extreme temperatures, vibrations, and shocks. Their high mechanical strength and durability make them ideal for applications in aerospace, automotive, and industrial sectors. -
Q: What are the challenges in the manufacturing of ceramic PCBs?
A: The manufacturing of ceramic PCBs requires specialized equipment and expertise due to the unique properties of ceramic materials and the high temperatures involved in sintering. Challenges include ensuring uniform substrate thickness, precise via formation, and achieving reliable metallization and circuit patterning on the ceramic surface.
Conclusion
Ceramic PCBs offer a wide range of benefits and customization options, making them an attractive choice for various industries and applications. As we move into 2023, the demand for ceramic PCBs is expected to grow further, driven by advancements in technology and the increasing need for high-performance, reliable, and compact electronic solutions.
This comprehensive guide has provided an in-depth overview of ceramic PCBs, covering their composition, manufacturing process, applications, and the latest trends and innovations in the industry. By understanding the unique properties and advantages of ceramic PCBs, engineers, designers, and enthusiasts can make informed decisions when choosing the most suitable PCB technology for their projects.
As the ceramic PCB industry continues to evolve, it is essential to stay updated with the latest developments and innovations. Embracing new technologies, such as 3D printing and hybrid ceramic-organic PCBs, can open up new possibilities for product design and manufacturing. Additionally, the focus on sustainability and eco-friendly practices in the industry aligns with the growing global emphasis on environmental responsibility.
In conclusion, ceramic PCBs are a powerful tool in the world of electronics, offering unparalleled customization, performance, and reliability. By leveraging the advantages of ceramic PCBs, businesses and individuals can push the boundaries of innovation and create cutting-edge products that meet the demands of the future.
No responses yet