Introduction to ESD protection
Electrostatic Discharge (ESD) is a common phenomenon that can cause significant damage to electronic components and printed circuit boards (PCBs). ESD occurs when there is a sudden transfer of electric charge between two objects with different electrical potentials. In the context of electronics, ESD can happen when a charged object, such as a human body or a tool, comes into contact with a sensitive electronic component or a PCB.
ESD events can generate high voltages and currents that can instantly damage or degrade electronic components, leading to reduced performance, reliability issues, or complete failure of the device. To prevent ESD-related problems, it is essential to incorporate ESD protection measures into the design of PCBs and electronic systems.
In this beginner’s guide, we will explore the fundamentals of ESD protection circuit design for PCBs, covering topics such as ESD sources, ESD models, ESD protection devices, and best practices for designing effective ESD protection circuits.
Understanding ESD Sources and Models
ESD Sources
ESD can originate from various sources, including:
-
Human Body Model (HBM): This model represents the discharge from a charged human body to a grounded device. The HBM is the most common ESD source in electronic manufacturing and handling environments.
-
Charged Device Model (CDM): This model represents the discharge from a charged device to a grounded surface or another device. CDM events can occur during the manufacturing process or when devices are handled or transported.
-
Machine Model (MM): This model represents the discharge from a charged machine or tool to a grounded device. MM events can happen in automated manufacturing or testing environments.
ESD Models and Standards
To quantify and standardize ESD events, several ESD models and standards have been developed. These models help in designing and testing ESD protection circuits. Some of the commonly used ESD models and standards include:
-
IEC 61000-4-2: This international standard defines the test methods and levels for ESD immunity testing of electronic equipment. It covers both contact discharge and air discharge scenarios.
-
ANSI/ESDA/JEDEC JS-001: This joint standard by the American National Standards Institute (ANSI), the ESD Association (ESDA), and the JEDEC Solid State Technology Association defines the HBM test method and classification levels for ESD sensitivity of electronic components.
-
ANSI/ESDA/JEDEC JS-002: This joint standard defines the CDM test method and classification levels for ESD sensitivity of electronic components.
Understanding these ESD sources and models is crucial for designing effective ESD protection circuits that can withstand the expected ESD events in the intended application environment.
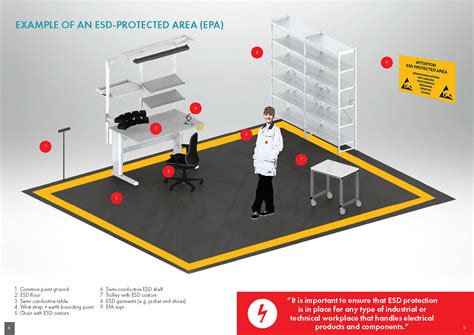
ESD Protection Devices
To protect electronic components and PCBs from ESD events, various ESD protection devices are available. These devices are designed to quickly respond to ESD events by shunting the excessive current away from the sensitive components and limiting the voltage across them. Some of the commonly used ESD protection devices include:
TVS Diodes
Transient Voltage Suppressor (TVS) diodes are specially designed diodes that have a fast response time and can handle high peak currents. When the voltage across a TVS diode exceeds its breakdown voltage, it quickly enters avalanche breakdown mode and clamps the voltage to a safe level, protecting the downstream components.
TVS diodes are available in various voltage ratings and package sizes, making them suitable for a wide range of applications. They are commonly used for protecting data lines, power supply lines, and other sensitive interfaces.
MOVs
Metal Oxide Varistors (MOVs) are voltage-dependent resistors that have a high resistance at normal operating voltages but quickly switch to a low resistance state when the voltage exceeds a certain threshold. This characteristic allows MOVs to absorb and dissipate the energy of an ESD event, protecting the connected components.
MOVs are often used in power supply lines and AC mains protection circuits due to their high energy handling capability. However, they have a slower response time compared to TVS diodes and may not be suitable for high-speed data lines.
Gas Discharge Tubes
Gas Discharge Tubes (GDTs) are two-terminal devices that contain a noble gas mixture between two electrodes. When the voltage across the GDT exceeds the breakdown voltage of the gas, it ionizes and becomes conductive, allowing the ESD current to flow through it.
GDTs have a high voltage handling capability and can withstand multiple ESD events. They are commonly used in telecommunications and power systems for overvoltage protection.
Polymer ESD Suppressors
Polymer ESD suppressors, also known as Polymeric Positive Temperature Coefficient (PPTC) devices, are resettable fuses that combine the functions of a fuse and a varistor. These devices have a low resistance under normal conditions but quickly switch to a high resistance state when the current exceeds a certain threshold, effectively limiting the ESD current.
Polymer ESD suppressors are often used in USB ports, audio jacks, and other low-voltage interfaces due to their compact size and resettable nature.
ESD Protection ICs
ESD protection integrated circuits (ICs) are specialized devices that integrate multiple ESD protection structures, such as diodes, transistors, and resistors, into a single package. These ICs offer a compact and easy-to-use solution for ESD protection in various applications.
ESD protection ICs are available for different interface standards, such as USB, HDMI, Ethernet, and I2C, and can provide bidirectional protection with low capacitance and fast response times.
Choosing the appropriate ESD protection device depends on factors such as the expected ESD levels, the interface type, the operating voltage and current, and the available board space. It is essential to consider the specifications and ratings of the ESD protection devices to ensure they provide adequate protection for the specific application.
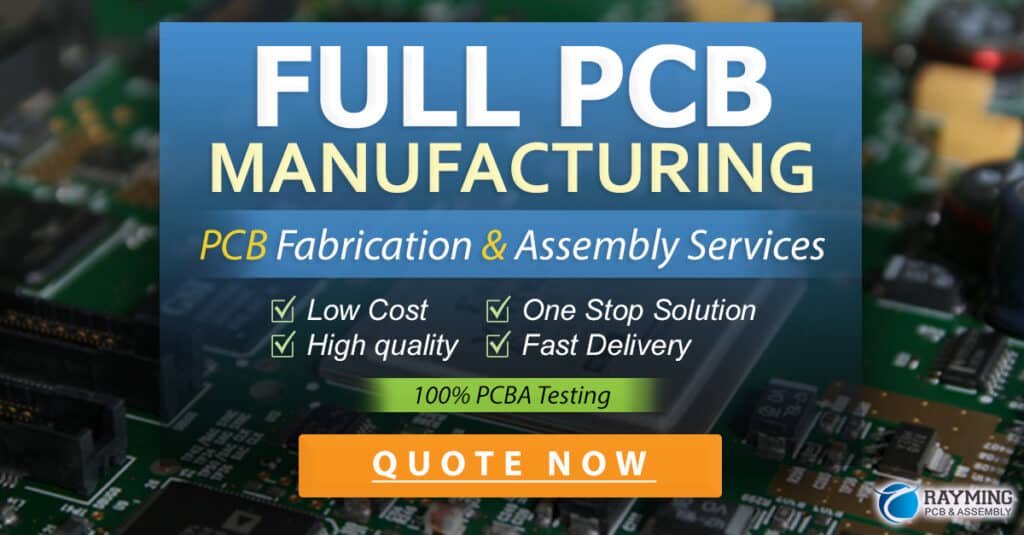
Designing ESD Protection Circuits
When designing ESD protection circuits for PCBs, several best practices should be followed to ensure effective protection and minimize the impact on signal integrity. Some key considerations include:
Placement and Routing
-
Place ESD protection devices as close as possible to the connector or the point of entry of the ESD event. This minimizes the inductance in the discharge path and improves the response time of the protection device.
-
Route the ESD discharge path away from sensitive components and signal traces to avoid coupling and interference. Use dedicated ground planes or traces for the ESD current return path.
-
Avoid creating loops or long traces in the ESD discharge path, as they can increase the inductance and degrade the protection performance.
Grounding and Shielding
-
Provide a low-impedance ground path for the ESD current to flow through. Use multiple vias to connect the ground planes on different layers and minimize the ground impedance.
-
Implement proper shielding techniques, such as using grounded metal enclosures or shielding gaskets, to prevent ESD events from directly reaching the sensitive components.
-
Use guard rings or grounded traces around sensitive components to provide a preferred path for the ESD current and divert it away from the components.
Component Selection and Rating
-
Choose ESD protection devices with appropriate voltage and current ratings based on the expected ESD levels and the interface specifications. Ensure that the devices can handle the maximum expected ESD voltage and current without damage.
-
Consider the capacitance and leakage current of the ESD protection devices, especially for high-speed interfaces. Low capacitance devices, such as silicon TVS diodes, are preferred for high-speed applications to minimize signal distortion.
-
Select ESD protection devices with fast response times to ensure quick clamping of the ESD voltage and minimize the energy transferred to the protected components.
Simulation and Testing
-
Perform simulations using ESD models and circuit simulation tools to analyze the effectiveness of the ESD protection design. Simulate different ESD scenarios and verify that the protection devices clamp the voltage to safe levels and provide adequate current handling capability.
-
Conduct ESD testing on the assembled PCBs using standardized ESD test methods, such as IEC 61000-4-2 or ANSI/ESDA/JEDEC JS-001, to validate the ESD protection performance. Perform both contact discharge and air discharge tests at different voltage levels and polarities.
-
Monitor the functionality and performance of the protected components during and after the ESD tests to ensure that they are not affected by the ESD events.
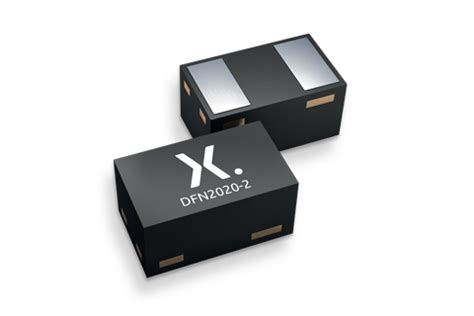
Common ESD Protection Circuit Topologies
There are several common ESD protection circuit topologies that can be used depending on the interface type and the specific application requirements. Some of these topologies include:
Shunt Protection
In a shunt protection topology, the ESD protection device is connected in parallel with the protected component or interface. When an ESD event occurs, the protection device clamps the voltage and shunts the ESD current away from the sensitive components.
Shunt protection is commonly used for power supply lines, data lines, and other interfaces where the normal operating voltage is within the clamping voltage range of the protection device.
Series Protection
In a series protection topology, the ESD protection device is connected in series with the protected component or interface. The protection device acts as a high-impedance barrier during normal operation and switches to a low-impedance state during an ESD event, diverting the current away from the sensitive components.
Series protection is often used for high-speed data lines or interfaces where the capacitance of the protection device needs to be minimized to avoid signal distortion.
Matrix Protection
Matrix protection involves using a combination of shunt and series protection devices arranged in a matrix configuration. This topology provides protection against ESD events between any two pins of a multi-pin interface, such as a connector or a cable.
Matrix protection is commonly used in applications with high pin count interfaces, such as USB, HDMI, or Ethernet, where ESD events can occur between any combination of pins.
π (Pi) Filter Protection
A π filter protection topology combines shunt protection devices with series impedance elements, such as ferrites or resistors, to form a low-pass filter. This topology helps to attenuate high-frequency ESD transients while allowing the desired signal to pass through with minimal distortion.
π filter protection is often used in applications where both ESD protection and electromagnetic interference (EMI) suppression are required, such as in automotive or industrial environments.
PCB Layout Considerations for ESD Protection
Proper PCB layout is crucial for effective ESD protection. Here are some key considerations and best practices for ESD protection in PCB layout:
-
Place ESD protection devices close to the connectors or entry points of the PCB to minimize the inductance in the discharge path. This improves the response time and effectiveness of the protection devices.
-
Provide a low-impedance ground path for the ESD current to flow through. Use dedicated ground planes or wide ground traces to minimize the ground impedance.
-
Avoid routing sensitive signal traces near the ESD protection devices or the discharge path to prevent coupling and interference. Maintain sufficient spacing between the ESD protection devices and the sensitive components.
-
Use multiple vias to connect the ground planes on different layers of the PCB. This helps to minimize the ground impedance and provides a low-inductance path for the ESD current.
-
Implement guard rings or grounded traces around sensitive components to provide a preferred path for the ESD current and divert it away from the components.
-
Consider the use of shielding techniques, such as grounded metal enclosures or shielding gaskets, to prevent direct ESD events from reaching the sensitive components.
-
Follow good PCB design practices, such as minimizing trace lengths, avoiding sharp bends or angles, and using appropriate trace widths and spacing, to minimize the inductance and impedance in the ESD protection circuits.
-
Perform thorough ESD testing on the assembled PCBs to validate the effectiveness of the ESD protection design and identify any potential weaknesses or areas for improvement.
ESD Protection Testing and Verification
Testing and verifying the ESD protection design is essential to ensure that the PCB and its components can withstand the expected ESD events in the intended application environment. Here are some common ESD testing methods and considerations:
-
IEC 61000-4-2 Testing: This is a widely used international standard for ESD immunity testing of electronic equipment. It defines the test methods, voltage levels, and discharge waveforms for both contact discharge and air discharge scenarios.
-
Human Body Model (HBM) Testing: HBM testing simulates the discharge from a charged human body to a grounded device. It is commonly used for testing the ESD sensitivity of individual components and ICs.
-
Charged Device Model (CDM) Testing: CDM testing simulates the discharge from a charged device to a grounded surface or another device. It is relevant for automated manufacturing and handling processes where devices can become charged.
-
System-Level ESD Testing: In addition to component-level testing, it is important to perform system-level ESD testing on the complete PCB or product. This involves applying ESD events to the external interfaces, such as connectors or buttons, and verifying the functionality and immunity of the system.
-
ESD Gun Testing: ESD guns are used to generate controlled ESD events with specified voltage levels and polarities. They are commonly used for system-level testing and can be configured for contact discharge or air discharge scenarios.
-
Failure Analysis: In case of ESD-related failures during testing, it is important to perform failure analysis to identify the root cause and weak points in the ESD protection design. This may involve visual inspection, electrical testing, or microscopic analysis of the damaged components.
-
Design Iterations: Based on the results of ESD testing and failure analysis, the ESD protection design may need to be modified or optimized. This could involve changing the protection device selection, modifying the PCB layout, or implementing additional protection measures.
-
Documentation and Reporting: Proper documentation of the ESD protection design, test procedures, and test results is essential for future reference and compliance purposes. It helps to ensure that the ESD protection measures are effectively implemented and maintained throughout the product lifecycle.
Frequently Asked Questions (FAQ)
- What is ESD, and why is ESD protection important in PCB design?
-
ESD (Electrostatic Discharge) is a sudden transfer of electric charge between two objects with different electrical potentials. ESD events can generate high voltages and currents that can damage or degrade electronic components and PCBs. ESD protection is important in PCB design to prevent ESD-related failures, improve reliability, and ensure the long-term performance of electronic devices.
-
What are the common sources of ESD in electronic systems?
-
The common sources of ESD in electronic systems include:
- Human body discharge (HBM): ESD events caused by charged human bodies touching electronic devices.
- Charged device model (CDM): ESD events caused by charged devices discharging to grounded surfaces or other devices.
- Machine model (MM): ESD events caused by charged machines or tools discharging to grounded devices.
-
What are the different types of ESD protection devices used in PCB design?
-
The common types of ESD protection devices used in PCB design include:
- TVS (Transient Voltage Suppressor) diodes: Fast-acting diodes that clamp the voltage to a safe level during ESD events.
- MOVs (Metal Oxide Varistors): Voltage-dependent resistors that absorb and dissipate the energy of ESD events.
- Gas Discharge Tubes (GDTs): Two-terminal devices that ionize a gas mixture to provide high-voltage ESD protection.
- Polymer ESD suppressors: Resettable fuses that limit the ESD current by switching to a high-resistance state.
- ESD protection ICs: Integrated circuits that combine multiple ESD protection structures into a single package.
-
What are the best practices for placing and routing ESD protection devices on a PCB?
-
The best practices for placing and routing ESD protection devices on a PCB include:
- Placing the protection devices close to the entry points or connectors to minimize the inductance in the discharge path.
- Routing the ESD discharge path away from sensitive components and signal traces to avoid coupling and interference.
- Providing a low-impedance ground path for the ESD current using dedicated ground planes or traces.
- Avoiding loops or long traces in the ESD discharge path to minimize inductance and improve protection performance.
-
How can ESD testing be performed to validate the effectiveness of ESD protection design in a PCB?
- ESD testing can be performed using standardized test methods, such as IEC 61000-4-2 or ANSI/ESDA/JEDEC JS-001, which define the test voltage levels, discharge waveforms, and test procedures. ESD guns are commonly used to generate controlled ESD events for system-level testing. Component-level testing, such as HBM or CDM testing, can also be performed to evaluate the ESD sensitivity of individual components. Failure analysis and design iterations based on the test results help to optimize the ESD protection design and ensure its effectiveness.
Conclusion
ESD protection is a critical aspect of PCB design to ensure the reliability and long-term performance of electronic devices. By understanding the sources and models of ESD, selecting appropriate ESD protection devices, and following best practices for PCB layout and design, engineers can effectively mitigate the risks associated with ESD events.
Designing effective ESD protection circuits involves considering factors such as the expected ESD levels, interface types, operating voltages, and available board space. Proper placement and routing of protection devices, grounding and shielding techniques, and component selection based on ratings and specifications are essential for optimal ESD protection performance.
ESD testing and verification are crucial steps in validating the effectiveness of the ESD protection design. Standardized test methods, such as IEC 61000-4-2 or HBM/CDM testing, help to evaluate the E
No responses yet